Immaginate un processo di produzione che unisca l'intricata libertà di progettazione dello stampaggio a iniezione della plastica con l'impareggiabile forza e durata del metallo. Questa è la magia di Tecnologia MIMUn cambiamento di rotta nel mondo della lavorazione dei metalli.
Questo articolo si addentra nell'affascinante mondo della tecnologia MIM, esplorandone le complessità, le applicazioni, i vantaggi e le considerazioni. Allacciate le cinture e preparatevi a scoprire una tecnologia che sta superando i confini del possibile nella produzione dei metalli.
Il processo MIM
Il MIM opera secondo un principio ingannevolmente semplice. Ecco una sintesi delle fasi coinvolte:
- Polvere di potenza: Il viaggio inizia con un metallo finemente polverizzato, simile a una polvere metallica. Questa polvere può essere composta da vari metalli, tra cui acciaio, acciaio inossidabile, titanio e persino leghe esotiche.
- Incollaggio del legante: Immaginate di mescolare la polvere di metallo con uno speciale agente legante, come una colla che tiene tutto insieme. Questo miscuglio, noto come feedstock, diventa il materiale modellabile per la fase successiva.
- Intuizione dell'iniezione: La materia prima viene quindi iniettata ad alta pressione in una cavità dello stampo progettata con precisione. È come spremere il pongo in uno stampo per biscotti, ma con un macchinario molto più sofisticato.
- In forma: Una volta iniettato, il materiale di partenza prende la forma della cavità dello stampo, formando un componente di forma quasi netta. La forma near-net si riferisce a un componente che richiede una post-lavorazione minima per raggiungere le dimensioni finali.
- Raccoglitore addio: La fase successiva prevede la rimozione del legante attraverso un processo di deceraggio termico. Questo processo può prevedere tecniche come l'estrazione con solvente o la degradazione termica, che essenzialmente vaporizzano il legante e lasciano lo scheletro metallico.
- Impennata di forza: La fase finale è un processo di sinterizzazione ad alta temperatura. In questo caso, le particelle di metallo si scaldano e si addensano, fondendosi insieme e densificando il componente. Ciò aumenta notevolmente la resistenza e l'integrità strutturale del pezzo.
Pensate al MIM come a un sofisticato origami metallico, che piega meticolosamente la polvere metallica in forme intricate con una forza impressionante.
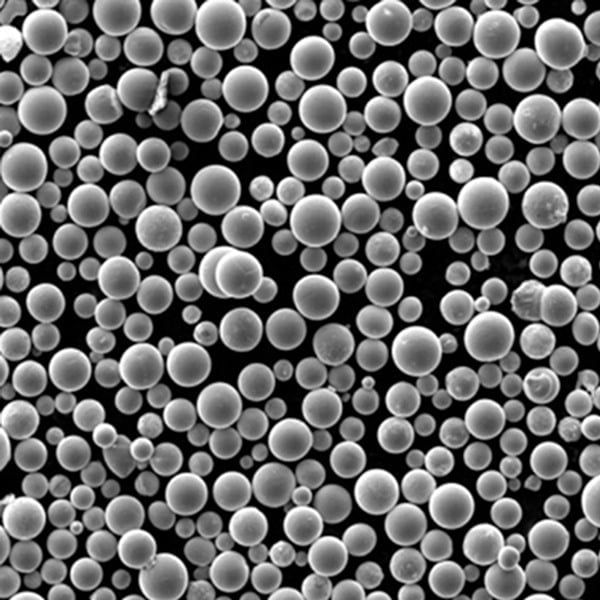
I vantaggi di Tecnologia MIM
La tecnologia MIM vanta un'interessante serie di vantaggi che la rendono una scelta privilegiata per diverse applicazioni produttive. Approfondiamo alcuni vantaggi chiave:
- Versatilità del design: A differenza dei metodi tradizionali di lavorazione dei metalli, come la fusione o la lavorazione, il MIM offre un'eccezionale libertà di progettazione. Geometrie complesse, dettagli intricati e pareti sottili: il MIM gestisce tutto con facilità. Immaginate di realizzare ingranaggi con denti minuscoli o strumenti medici intricati con caratteristiche delicate: il MIM lo rende possibile.
- Alto volume, alta precisione: Il MIM si distingue per i volumi di produzione elevati. La capacità di creare forme quasi nette riduce al minimo la necessità di un'estesa post-elaborazione, con conseguenti cicli di produzione più rapidi e risparmi sui costi. Inoltre, il MIM garantisce un'eccezionale precisione dimensionale, fondamentale per i componenti che richiedono tolleranze precise.
- Materiale Marvel: Il MIM offre la flessibilità di lavorare con un'ampia gamma di polveri metalliche. Questo apre le porte alla realizzazione di componenti in acciai ad alta resistenza, leghe resistenti alla corrosione o persino materiali leggeri come il titanio.
- Considerazioni sui costi: Sebbene i costi iniziali per il MIM possano essere più elevati, le capacità di produzione in grandi volumi e la minima post-elaborazione si traducono in un significativo risparmio di costi nel lungo periodo. Ciò rende il MIM un'opzione interessante per la produzione di massa di parti metalliche complesse.
- Non sprecare, non volere: Il MIM è un processo relativamente ecologico rispetto ai metodi tradizionali. L'approccio a forma quasi netta riduce al minimo lo spreco di materiale e il processo di deceraggio controllato consente in alcuni casi il recupero e il riutilizzo dei leganti.
La tecnologia MIM è un campione a tutto tondo, che offre flessibilità di progettazione, produzione ad alta precisione, versatilità dei materiali e convenienza economica, il tutto riducendo al minimo l'impatto ambientale.
Le applicazioni di Tecnologia MIM
La tecnologia MIM trova applicazione in una vasta gamma di settori, dall'intricato mondo dei dispositivi medici al colossale regno dei componenti automobilistici. Ecco alcuni esempi di rilievo:
- Meraviglie mediche: Il MIM svolge un ruolo cruciale nella realizzazione di impianti medici complessi come protesi articolari, protesi dentarie e strumenti chirurgici. La capacità di creare forme complesse con materiali biocompatibili rende il MIM ideale per queste applicazioni impegnative.
- Vantaggio automobilistico: L'industria automobilistica sfrutta il MIM per la produzione di vari componenti come ingranaggi, pignoni e parti del sistema di alimentazione. Le capacità di produzione in grandi volumi e la capacità di creare forme quasi nette con tolleranze ristrette rendono il MIM perfetto per il frenetico mondo automobilistico.
- Sinfonia dell'elettronica di consumo: Dai minuscoli componenti dei telefoni cellulari alle parti intricate degli oggetti da indossare, il MIM contribuisce alla miniaturizzazione e alla funzionalità dell'elettronica di consumo. La sua capacità di produrre forme complesse con elevata precisione si adatta perfettamente al mondo sempre più ristretto dei gadget.
- Ascendenza aerospaziale: L'industria aerospaziale richiede componenti leggeri ma robusti. Il MIM è all'altezza della sfida e consente di creare pezzi complessi da leghe ad alta resistenza e basso peso come il titanio. Questo si traduce in un risparmio di carburante e in un miglioramento delle prestazioni di aerei e veicoli spaziali.
- Finezza nelle armi da fuoco: Il MIM svolge un ruolo importante nell'industria delle armi da fuoco per la realizzazione di componenti intricati come grilletti, martelli e sicure. La sua capacità di produrre forme quasi nette con un'elevata precisione e un'eccezionale resistenza lo rende adatto a queste applicazioni impegnative.
Oltre a questi esempi di spicco, la tecnologia MIM ha il potenziale per rivoluzionare diversi altri settori. Man mano che la tecnologia matura e i costi diventano più competitivi, possiamo aspettarci di vedere le applicazioni MIM espandersi in campi quali:
- Infrastruttura energetica: Produzione di componenti complessi per pompe, valvole e altre parti critiche dei sistemi di generazione e distribuzione dell'energia.
- Telecomunicazioni: Creazione di componenti miniaturizzati e di alta precisione per complesse apparecchiature di telecomunicazione.
- Articoli sportivi: Realizza componenti leggeri e resistenti per biciclette, mazze da golf e altre attrezzature sportive.
Le possibilità offerte dalla tecnologia MIM sono davvero vaste e il suo impatto su vari settori industriali è destinato a crescere nei prossimi anni.
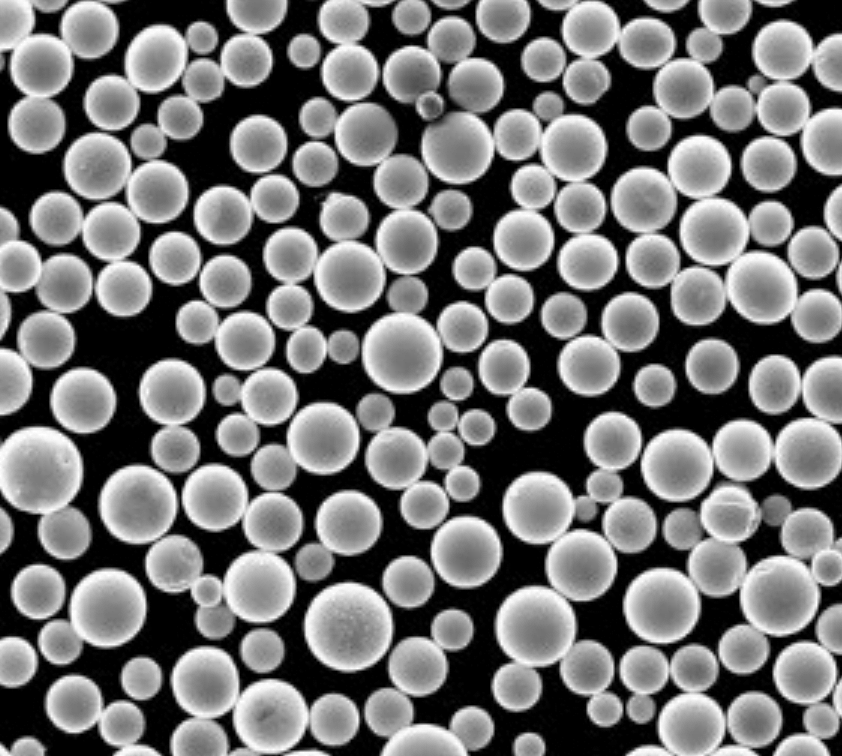
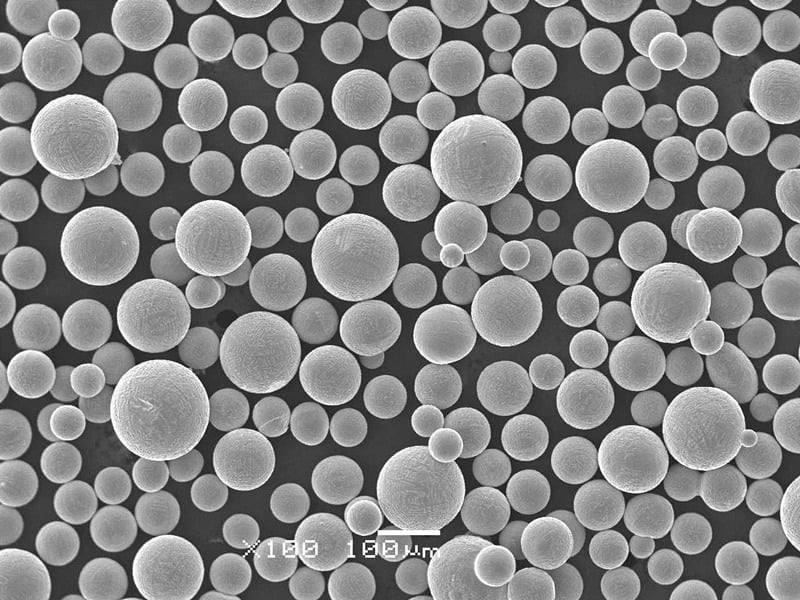
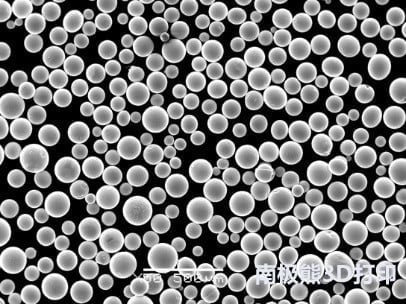
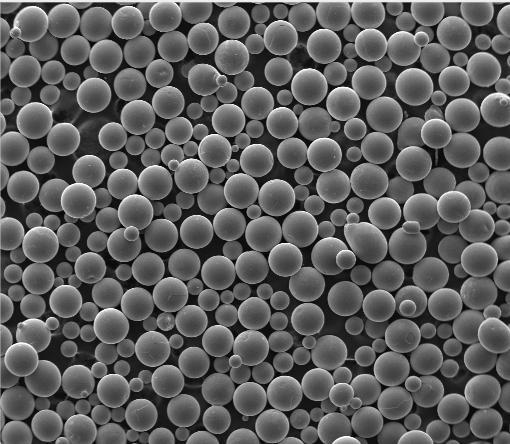
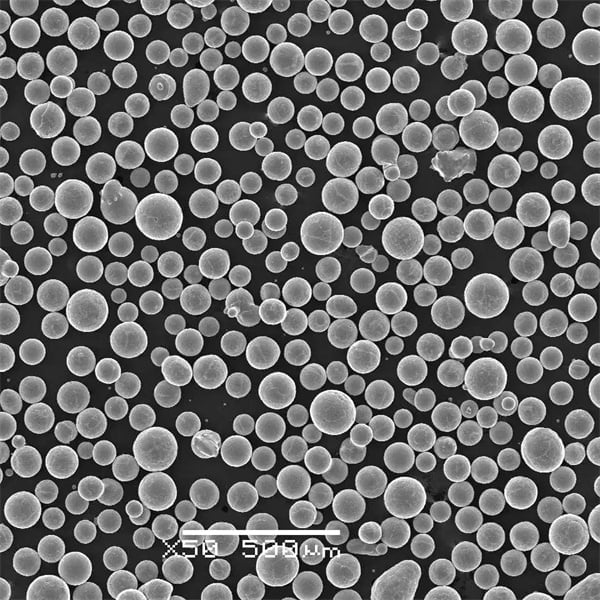
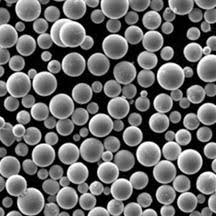
Le caratteristiche della tecnologia di atomizzazione
Dopo aver esplorato la magia del MIM, approfondiamo un aspetto cruciale: la tecnologia di atomizzazione. Questo processo è responsabile della creazione delle polveri metalliche sottili che costituiscono la base del MIM. Ecco una panoramica delle due principali tecniche di atomizzazione:
- Atomizzazione del gas: Immaginate che il metallo fuso venga spinto attraverso un ugello ad alta pressione, rompendolo in minuscole goccioline che si solidificano a mezz'aria come polvere di metallo. Questa è l'essenza dell'atomizzazione a gas. È una tecnica versatile, adatta a un'ampia gamma di metalli e leghe.
- Atomizzazione dell'acqua: Questo metodo utilizza un getto d'acqua ad alta velocità per frammentare il metallo fuso in particelle fini. L'atomizzazione ad acqua è particolarmente adatta alla produzione di polveri metalliche sferiche e viene spesso utilizzata per materiali specifici come l'acciaio inossidabile.
La scelta della tecnica di atomizzazione dipende da diversi fattori, tra cui le caratteristiche della polvere desiderate, il tipo di metallo da lavorare e le considerazioni sui costi.
Ecco una tabella che riassume le caratteristiche principali di ciascuna tecnica di atomizzazione:
Caratteristica | Atomizzazione a gas | Atomizzazione dell'acqua |
---|---|---|
Processo | Metallo fuso forzato attraverso un ugello ad alta pressione | Metallo fuso frammentato da un getto d'acqua ad alta velocità |
Morfologia della polvere | Forme generalmente irregolari | Tipicamente più sferico |
Idoneità al metallo | Ampia gamma di metalli e leghe | Adatto soprattutto per materiali specifici come l'acciaio inossidabile |
Costi | Costo generalmente più elevato | Costo inferiore rispetto all'atomizzazione a gas |
È importante notare che questa tabella fornisce un confronto generale e che le capacità possono essere in parte sovrapposte a seconda della tecnologia e dei parametri di processo specifici.
Considerazioni e limiti di Tecnologia MIM
Sebbene il MIM offra una serie di vantaggi interessanti, è essenziale comprenderne i limiti e le considerazioni prima di tuffarsi a capofitto. Ecco alcuni punti chiave da tenere a mente:
- Vincoli di dimensione dei pezzi: Il MIM è più adatto alla produzione di componenti di dimensioni relativamente piccole o medie. Le limitazioni derivano da fattori quali le capacità di riempimento dello stampo e il potenziale di cricche interne durante le fasi di sbavatura e sinterizzazione.
- Finitura superficiale: Sebbene il MIM possa produrre buone finiture superficiali, potrebbe non essere l'ideale per le applicazioni che richiedono una levigatezza eccezionale. In questi casi potrebbero essere necessarie ulteriori fasi di post-elaborazione, come la lucidatura o la lavorazione.
- Selezione del materiale: Non tutti i metalli sono facilmente compatibili con il MIM. Fattori come il punto di fusione e il comportamento di sinterizzazione giocano un ruolo fondamentale. I metalli refrattari con punti di fusione estremamente elevati potrebbero non essere adatti al MIM a causa delle limitazioni delle temperature di lavorazione.
- Progettazione per MIM: Per sfruttare appieno i vantaggi del MIM, è fondamentale progettare componenti specifici per il processo. Ciò comporta la considerazione di fattori quali lo spessore delle pareti, gli angoli di sformo e le potenziali sollecitazioni interne durante la lavorazione.
Comprendendo queste considerazioni e limitazioni, i produttori possono decidere con cognizione di causa se il MIM è adatto alla loro specifica applicazione.
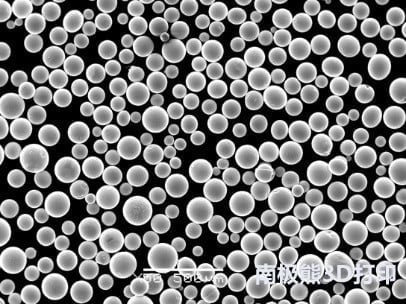
FAQ
Ecco una sezione che affronta alcune domande frequenti su Tecnologia MIM, presentati in un formato tabellare chiaro e conciso:
Domanda | Risposta |
---|---|
Quali sono i vantaggi della tecnologia MIM? | Flessibilità di progettazione, produzione di grandi volumi, versatilità dei materiali, economicità e scarti minimi. |
Quali sono le applicazioni della tecnologia MIM? | Dispositivi medici, componenti automobilistici, elettronica di consumo, parti aerospaziali, componenti per armi da fuoco e altro ancora. |
Quali sono i diversi tipi di tecniche di atomizzazione utilizzate nel MIM? | Atomizzazione di gas e atomizzazione di acqua. |
Quali sono i limiti della tecnologia MIM? | Vincoli dimensionali, limitazioni della finitura superficiale, considerazioni sulla selezione dei materiali e la necessità di progettare secondo i principi MIM. |
Il MIM è un processo ecologico? | Il MIM è relativamente ecologico rispetto ai metodi tradizionali di lavorazione dei metalli, grazie allo scarto minimo di materiale e al potenziale di riutilizzo del legante. |
Quali sono le prospettive future della tecnologia MIM? | Si prevede che la tecnologia MIM vedrà una crescita e un'adozione continue in vari settori industriali grazie ai suoi vantaggi e ai continui progressi. |
Come si colloca il MIM rispetto ad altri processi di lavorazione dei metalli, come la lavorazione o la fusione? | Il MIM offre una maggiore libertà di progettazione e forme quasi nette rispetto alla lavorazione. Mentre la colata può produrre forme complesse, il MIM vanta spesso una maggiore precisione e migliori proprietà dei materiali. |
Quali sono le sfide associate alla tecnologia MIM? | Sviluppo di metodi economicamente vantaggiosi per la lavorazione di una gamma più ampia di metalli e leghe e ulteriori progressi nelle tecniche di deceraggio per ridurre al minimo il potenziale di difetti. |
Informazioni su 3DP mETAL
Categoria di prodotto
CONTATTACI
Hai domande? Scrivici un messaggio ora! Dopo aver ricevuto il tuo messaggio, informeremo sull'elaborazione della tua richiesta a tutto il team.