3D printing, often hailed as the next industrial revolution, has introduced innovative methods to produce complex geometries with precision and efficiency. Among the myriad materials available for 3D printing, Inconel stands out as a high-performance alloy ideal for demanding applications. In this extensive guide, we’ll delve deep into the world of 3D printing with Inconel, exploring its properties, specific metal powder models, applications, and much more. Let’s get started!
概要 3D Printing Inconel
Inconel is a family of nickel-chromium-based superalloys known for their exceptional strength, heat resistance, and corrosion resistance. These properties make Inconel an excellent choice for 3D printing, especially in industries such as aerospace, automotive, and energy. 3D printing, or additive manufacturing, allows for the creation of complex shapes that are difficult or impossible to achieve with traditional manufacturing methods, thus enhancing the capabilities of Inconel.
Key Characteristics of Inconel for 3D Printing
- 高温耐性: Inconel retains its strength and oxidation resistance at high temperatures, making it ideal for high-heat environments.
- 耐蝕性: Excellent resistance to oxidation and corrosion in various environments, including acidic and marine settings.
- 機械的強度: Superior tensile and yield strength, ensuring durability and performance under stress.
- 汎用性: Suitable for producing intricate geometries and complex parts due to its good weldability and workability in powder form.
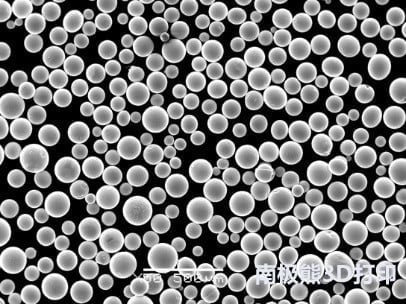
Types of Inconel for 3D Printing
There are several specific Inconel powder models used in 3D printing, each tailored to meet different requirements. Here’s a closer look at some of the most common Inconel powders:
Inconel Powder Model | 作曲 | プロパティ | アプリケーション |
---|---|---|---|
インコネル 625 | ニッケル、クロム、モリブデン、ニオブ | High tensile strength, excellent corrosion and oxidation resistance | 航空宇宙、海洋、化学処理 |
インコネル718 | Nickel, Chromium, Iron, Niobium, Molybdenum, Titanium, Aluminum | High yield strength, excellent fatigue and creep resistance | ジェットエンジン、ガスタービン、宇宙船 |
Inconel 713 | Nickel, Chromium, Molybdenum, Niobium, Aluminum, Titanium | 高温強度、耐酸化性 | Turbine blades, aerospace components |
Inconel 738 | Nickel, Chromium, Cobalt, Titanium, Aluminum | Excellent high-temperature mechanical properties | Gas turbine components |
Inconel 600 | ニッケル、クロム、鉄 | Good oxidation resistance at higher temperatures, high strength | Heat treatment equipment, chemical industry |
Inconel HX | Nickel, Chromium, Molybdenum, Iron | Good oxidation resistance, high-temperature strength | Industrial furnaces, gas turbine engines |
Inconel 617 | ニッケル、クロム、コバルト、モリブデン | 高温強度、耐酸化性 | Gas turbines, petrochemical plants |
Inconel X-750 | Nickel, Chromium, Iron, Titanium, Aluminum | 高強度、耐食性 | Aerospace, nuclear reactors |
Inconel 706 | Nickel, Chromium, Iron, Molybdenum, Niobium, Titanium, Aluminum | High mechanical strength, good weldability | Gas turbines, steam turbines |
Inconel MA754 | Nickel, Chromium, Iron, Yttrium | Exceptional strength, high oxidation resistance | Aerospace, high-temperature industrial applications |
応用例 3D Printing Inconel
The unique properties of Inconel make it a valuable material across various industries. Here’s how different sectors leverage 3D printing with Inconel:
航空宇宙産業
Inconel’s high strength-to-weight ratio and excellent thermal properties make it ideal for jet engine components, turbine blades, and exhaust systems. The ability to print complex geometries reduces weight and improves fuel efficiency.
自動車部門
Inconel is used to manufacture turbocharger components, exhaust systems, and other high-performance engine parts. Its heat resistance ensures durability under extreme operating conditions.
エネルギーと発電
Inconel’s resistance to heat and corrosion is crucial for components in gas turbines, nuclear reactors, and chemical processing plants. 3D printing allows for the production of intricate parts that enhance efficiency and performance.
海洋アプリケーション
The corrosion resistance of Inconel makes it perfect for marine environments, where components are exposed to harsh, salty conditions. It’s used in shipbuilding, offshore oil rigs, and other maritime structures.
医療分野
Inconel’s biocompatibility and strength are utilized in the production of medical implants and surgical instruments. 3D printing facilitates custom-made implants that fit patients perfectly, improving recovery times and outcomes.
Advantages and Disadvantages of 3D Printing Inconel
While Inconel offers numerous benefits, it also comes with some challenges. Here’s a balanced view:
利点
- 強度と耐久性: Inconel’s mechanical properties ensure longevity and reliability.
- 熱安定性: Excellent performance at high temperatures makes it ideal for demanding environments.
- 耐蝕性: Long-lasting resistance to oxidation and corrosive environments extends the lifespan of components.
- 複雑な幾何学: 3D printing allows for the creation of intricate and lightweight structures that are not possible with traditional methods.
欠点
- 利用料: Inconel is expensive, both in raw material form and in terms of 3D printing processes.
- Processing Difficulty: The high strength and toughness of Inconel make it challenging to machine and print, requiring specialized equipment and expertise.
- Thermal Stress: Managing thermal stresses during printing is crucial to prevent warping and defects in the final product.
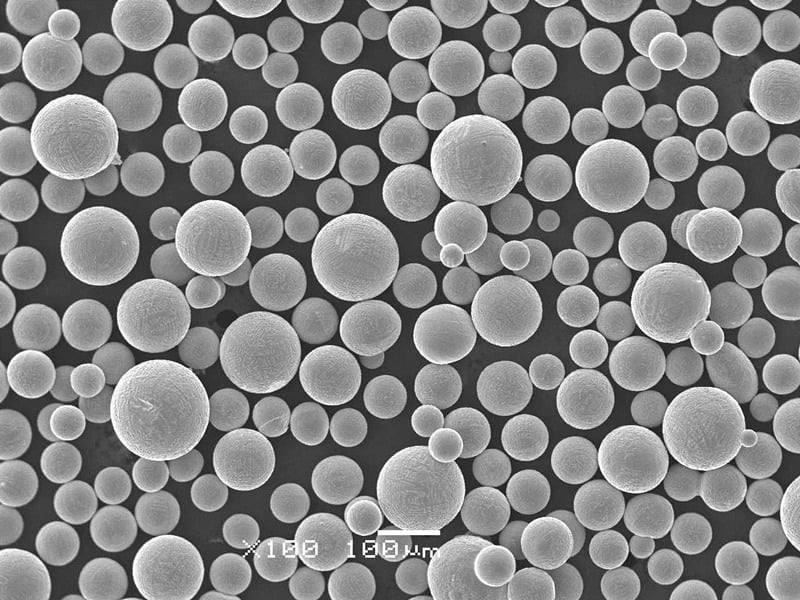
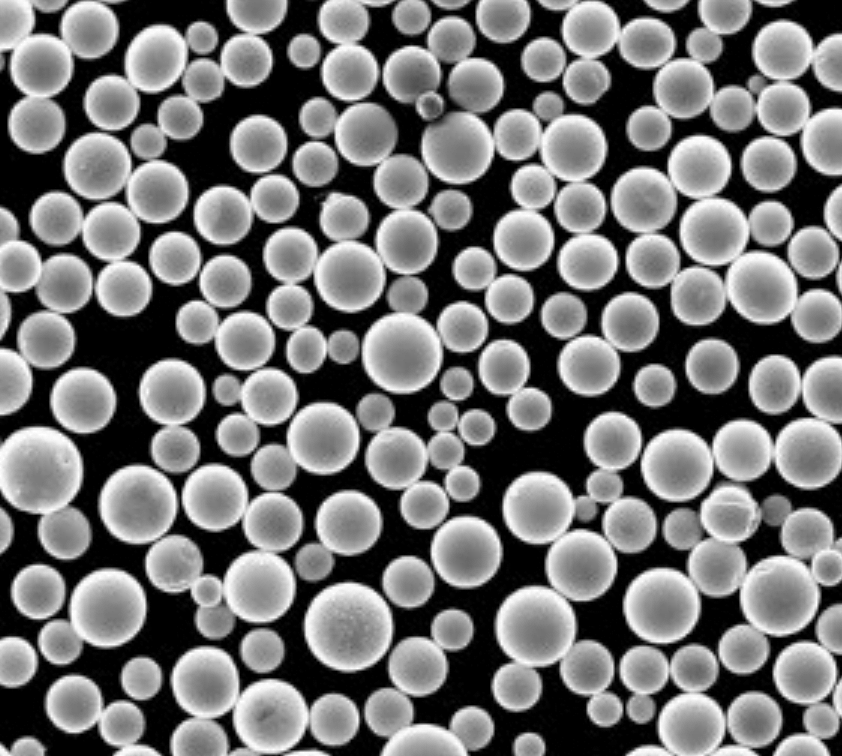
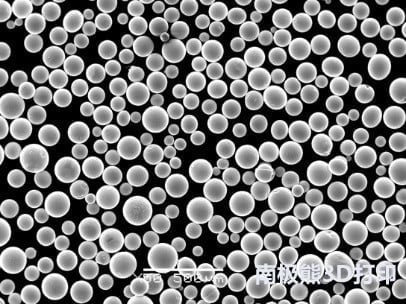
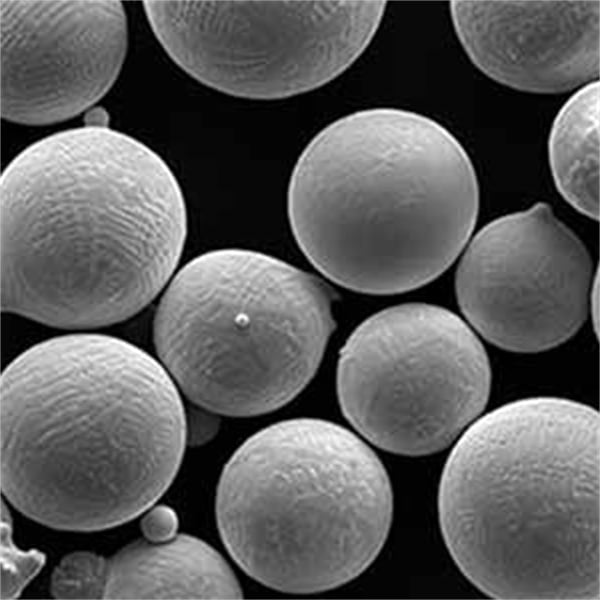
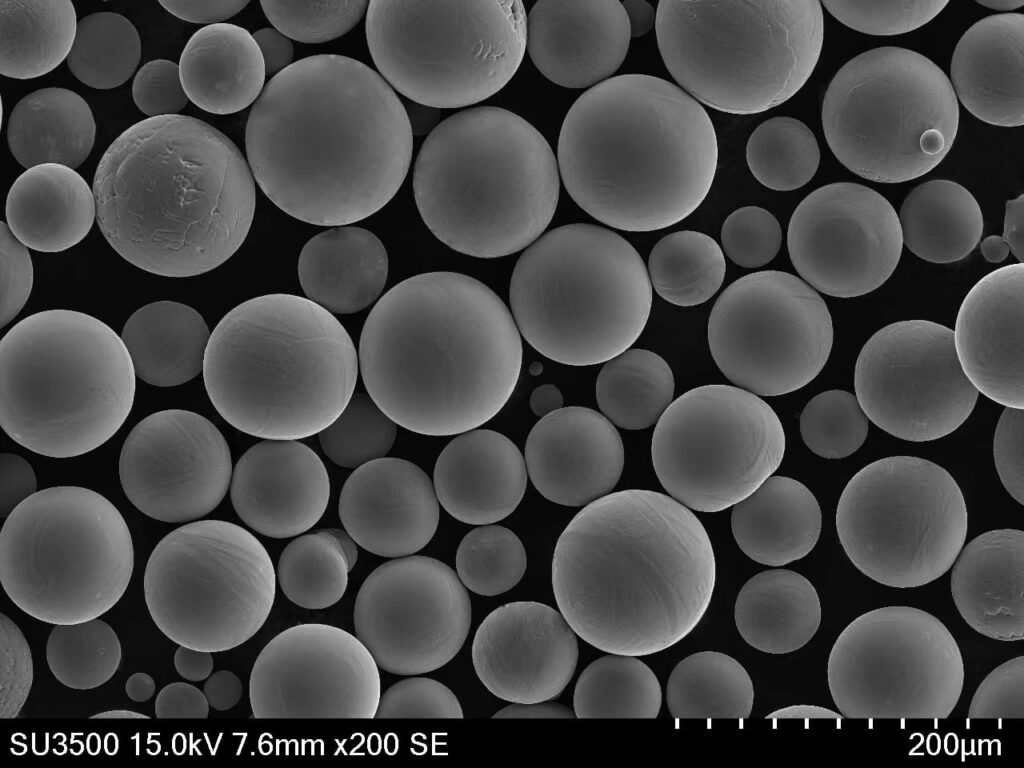
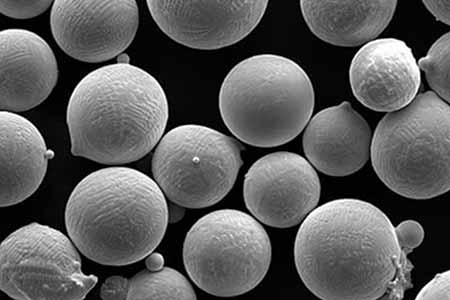
仕様、サイズ、等級、規格
When selecting Inconel for 3D printing, it’s important to consider the specific grades and standards to ensure compatibility with your application.
グレード | スタンダード | 仕様 | サイズ |
---|---|---|---|
インコネル 625 | ASMB443、AMS5666 | 58-63% Ni, 20-23% Cr, 8-10% Mo, 3.15-4.15% Nb | Powder sizes: 15-45µm, 45-100µm |
インコネル718 | 午前5662、午前5663 | 50-55% Ni, 17-21% Cr, 4.75-5.5% Nb, 2.8-3.3% Mo | Powder sizes: 15-45µm, 45-105µm |
Inconel 713 | AMS 5382, ASTM B637 | 70% Ni, 12% Cr, 4.5% Mo, 6% Nb, 0.6% Ti | Powder sizes: 15-53µm, 45-150µm |
Inconel 738 | AMS 5390, ASTM B637 | 61% Ni, 16% Cr, 8.5% Co, 2.6% W, 1.75% Ta | Powder sizes: 20-63µm, 45-105µm |
Inconel 600 | ASTM B168, AMS 5540 | 72% Ni, 14-17% Cr, 6-10% Fe | Powder sizes: 15-53µm, 45-150µm |
Inconel HX | AMS 5587, ASTM B572 | 47% Ni, 22% Cr, 9% Mo, 18% Fe | Powder sizes: 15-53µm, 45-105µm |
Inconel 617 | AMS 5887, ASTM B167 | 44.5-61% Ni, 20-24% Cr, 10-15% Co, 8-10% Mo | Powder sizes: 20-63µm, 45-150µm |
Inconel X-750 | AMS 5542, ASTM B637 | 70% Ni, 15-17% Cr, 5-9% Fe, 2.25-2.75% Ti | Powder sizes: 15-45µm, 45-105µm |
Inconel 706 | AMS 5708, ASTM B637 | 42.5% Ni, 16% Cr, 2.8% Ti, 1.5% Nb, 3% Mo | Powder sizes: 20-63µm, 45-105µm |
Inconel MA754 | AMS 5711, ASTM B637 | 76% Ni, 20% Cr, 1.5% Fe, 0.6% Y | Powder sizes: 15-53µm, 45-150µm |
サプライヤーと価格詳細
Finding the right supplier for Inconel powder is crucial for quality and cost-effectiveness. Here are some well-known suppliers and their pricing details:
Inconel Powder Model | 価格帯(kgあたり) | 備考 | |
---|---|---|---|
ヘガネス | Inconel 625, 718 | $400 – $600 | Leading global producer, high purity |
カーペンター・テクノロジー | Inconel 625, 738 | $450 – $700 | High-performance materials, wide availability |
LPW テクノロジー | Inconel 625, 718 | $500 – $750 | Specializes in metal powders for AM |
サンドビック オスプレイ | Inconel 625, 718 | $420 – $680 | High-quality powders, various grades |
Praxis Powder Technology | Inconel 625, 713 | $450 – $700 | Customized powder solutions, reliable quality |
アルカムAB(GEアディティブ) | Inconel 625, 738 | $480 – $720 | Industry leader in additive manufacturing |
EOS GmbH | Inconel 625, 718 | $450 – $700 | Wide range of materials for 3D printing |
AMETEK 特殊金属製品 | Inconel 625, 617 | $430 – $690 | Diverse applications, high purity |
テクナ・アドバンスト・マテリアルズ | Inconel 625, HX | $500 – $750 | Advanced spherical powders for AM |
3Dシステムズ | Inconel 625, 718 | $460 – $720 | Comprehensive 3D printing solutions |
Comparing the Pros and Cons of 3D Printing Inconel
When considering 3D printing with Inconel, it’s helpful to weigh the advantages and limitations side by side.
長所 | 欠点 |
---|---|
高い強度と耐久性 | High cost of material and processing |
優れた高温性能 | Requires specialized equipment |
優れた耐食性 | Thermal stress management necessary |
Ability to create complex geometries | Limited availability of some powder grades |
Suitable for critical applications | Potential for warping during printing |
FAQ About 3D Printing Inconel
質問 | 回答 |
---|---|
What is Inconel used for in 3D printing? | Inconel is used for high-performance parts in aerospace, automotive, energy, marine, and medical industries due to its strength, heat resistance, and corrosion resistance. |
Why is Inconel expensive? | The cost of Inconel is high because of the complex alloying process and the high content of expensive elements like nickel and chromium. |
Can Inconel be 3D printed? | Yes, Inconel can be 3D printed using powder bed fusion techniques, which allow for the creation of complex and precise geometries. |
What are the challenges of 3D printing with Inconel? | Challenges include managing thermal stresses, preventing warping, and the need for specialized equipment and expertise. |
Which industries benefit the most from 3D printing Inconel? | Aerospace, automotive, energy, marine, and medical industries benefit greatly due to Inconel’s performance in extreme conditions. |
How does Inconel compare to other 3D printing metals? | Inconel offers superior high-temperature and corrosion resistance compared to many other metals, but it is also more expensive and difficult to process. |
What are the typical sizes of Inconel powders for 3D printing? | Inconel powders for 3D printing typically range from 15µm to 150µm, depending on the specific application and printing technology. |
Who are the leading suppliers of Inconel powder? | Leading suppliers include Höganäs, Carpenter Technology, LPW Technology, Sandvik Osprey, and Arcam AB. |
Is 3D printing with Inconel sustainable? | 3D printing with Inconel can be more sustainable due to reduced material waste and the ability to produce parts on-demand, reducing overproduction. |
What are the future trends in 3D printing Inconel? | Future trends include advancements in powder production, improved printing techniques to reduce defects, and broader adoption across industries. |
結論
3D printing with Inconel opens up a world of possibilities for creating durable, high-performance components across various industries. While it comes with challenges such as high costs and processing difficulties, the benefits of using Inconel—especially in critical applications—far outweigh the drawbacks. As technology advances, we can expect even more innovative uses and improved methods for 3D printing with this remarkable material. Whether you’re in aerospace, automotive, energy, or medical fields, Inconel could be the key to unlocking new levels of performance and efficiency in your projects.
3DP mETALについて
製品カテゴリー
お問い合わせはこちら
何かご質問はありますか?今すぐメッセージを送信してください。あなたのメッセージを受信後、全チームで検討させていただきます。