Imagine building complex objects layer by layer, with each layer meticulously crafted from a bed of tiny metallic particles. This isn’t science fiction; it’s the reality of Additive Manufacturing (AM), also known as 3D printing. But what fuels this revolutionary technology? The unsung heroes – 積層造形用粉末.
These fine-grained metallic marvels are the building blocks of AM creations. Each tiny particle, carefully chosen for its specific properties, gets fused together using lasers, electron beams, or binding agents, transforming digital blueprints into tangible objects.
But with a vast array of powder options available, selecting the right one becomes crucial for a successful AM project. Buckle up, as we delve into the fascinating world of Additive Manufacturing Powders!
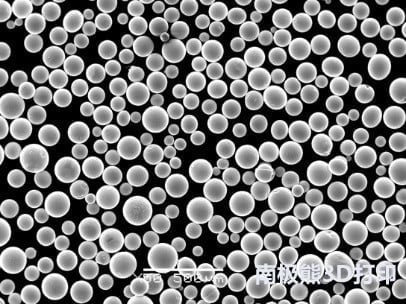
Types, Compositions, and Characteristics
Before exploring the specific heroes, let’s understand the broader powder landscape. Here’s a breakdown of the different types, compositions, and characteristics to consider:
パウダータイプ | Composition Examples | 特徴 |
---|---|---|
金属粉 | Titanium, Aluminum, Nickel alloys, Steel alloys | High strength, good thermal conductivity, wide range of properties depending on composition |
Polymer Powders | Nylon, Polycarbonate, ABS | Lightweight, good chemical resistance, limited mechanical properties |
Ceramic Powders | Alumina, Zirconia, Silicon carbide | High temperature resistance, wear resistance, electrically insulating or conductive depending on composition |
Within the realm of metal powders, diversity reigns supreme. The specific composition significantly impacts the final product’s properties. Here are some popular metal powder models to consider for your AM projects:
- Titanium Powders (Ti-6Al-4V): The workhorse of the metal powder world, Ti-6Al-4V offers an excellent balance of strength, weight, and corrosion resistance. Think of it as the titanium alloy you’d pick for building lightweight yet robust aerospace components.
- Stainless Steel Powders (316L): This versatile powder boasts excellent corrosion resistance, making it ideal for applications in harsh environments like marine or medical settings. Imagine crafting intricate surgical instruments or biocompatible implants with this reliable material.
- Aluminum Powders (AlSi10Mg): Lightweight and readily available, AlSi10Mg is a popular choice for applications where weight reduction is paramount. Think of it as the go-to powder for creating components in the automotive or aerospace industries where every gram counts.
- Nickel Superalloy Powders (Inconel 625): Known for their exceptional strength and resistance to high temperatures, Nickel superalloys like Inconel 625 are the champions of demanding environments. Imagine building parts for jet engines or industrial gas turbines that can withstand extreme heat and pressure.
- Cobalt-Chrome Powders (CoCrMo): Offering a potent combination of strength, biocompatibility, and wear resistance, CoCrMo powders are a mainstay in the medical device industry. Picture crafting durable yet biocompatible joint replacements or dental implants that seamlessly integrate with the human body.
- 銅粉: With superior thermal and electrical conductivity, copper powders are ideal for creating heat sinks or electrical components. Imagine building intricate heat exchangers or electrical connectors with the efficient heat transfer capabilities of copper.
- Tool Steel Powders (H13): H13 tool steel powders excel in applications requiring high wear resistance and dimensional stability. Think of them as the perfect choice for crafting durable molds, dies, or cutting tools that can withstand long-term use.
- タングステン粉: When it comes to sheer density and heat resistance, tungsten powders reign supreme. Imagine building components for radiation shielding or armor that can withstand extreme temperatures.
- Precious Metal Powders (Gold, Silver): Beyond functionality, precious metal powders like gold and silver add a touch of luxury and unique aesthetics to AM creations. Think of crafting intricate jewelry pieces or decorative objects with these valuable materials.
- Multi-Material Powders: Pushing the boundaries of innovation, multi-material powders combine different metals or materials in a single powder bed. Imagine creating components with graded properties or even integrating functional elements within a single build.
This is just a glimpse into the diverse world of Additive Manufacturing Powders. Remember, the ideal choice depends on the specific application’s needs.
応用例 積層造形用粉末
The possibilities unlocked by Additive Manufacturing Powders are truly astounding. Here’s a peek into some of the key applications:
アプリケーションエリア | 例 |
---|---|
航空宇宙: | Lightweight aircraft components, rocket engine parts, heat exchangers |
自動車: | Custom gears, lightweight chassis components, intricate engine parts |
医療 | Biocompatible implants, surgical instruments, prosthetics |
医療 | Biocompatible implants, surgical instruments, prosthetics |
Dental: | Custom dental crowns, bridges, implants |
消費財: | Jewelry, eyewear frames, personalized sporting equipment |
工具: | Complex molds, dies, cutting tools with intricate geometries |
エネルギーだ: | Heat exchangers for power plants, customized components for turbines |
エレクトロニクス: | Heat sinks for electronic devices, intricate electrical components |
Beyond these specific applications, Additive Manufacturing Powders are constantly pushing the boundaries of what’s possible. Imagine creating:
- Lightweight, high-strength prosthetics: Tailored to an individual’s needs, these prosthetics could offer unparalleled comfort and functionality.
- Customized implants with improved biocompatibility: Imagine implants that seamlessly integrate with the human body, reducing rejection risks.
- Complex heat exchangers with optimized performance: These heat exchangers could revolutionize efficiency in various industries.
The potential applications are truly endless, limited only by our imagination and the ongoing development of new powder materials and printing techniques.
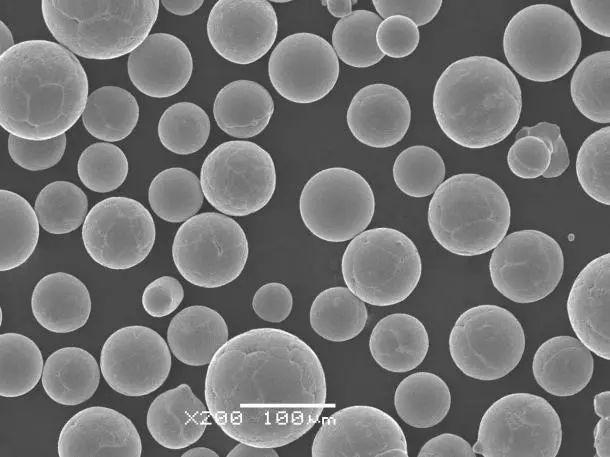
サイズ、等級、規格
Selecting the right powder requires a keen eye for detail. Here’s a breakdown of crucial specifications to consider:
仕様 | 説明 | 重要性 |
---|---|---|
粒径: | Measured in micrometers (µm), it determines surface area, flowability, and final part properties. | Finer powders create smoother surfaces but may be less flowable. |
粒度分布: | The range of particle sizes within the powder. | A narrow distribution ensures consistent material properties. |
Powder Flowability: | The ease with which the powder moves. | Good flowability is crucial for even deposition during printing. |
Powder Sphericity: | The shape of the particles, ideally spherical for optimal packing. | Spherical particles flow better and create denser parts. |
化学組成: | The specific elements and their proportions within the powder. | It dictates the final part’s mechanical and physical properties. |
パウダーグレード: | Denotes the purity and oxygen content of the powder. | Higher purity powders offer better mechanical properties. |
Standards Compliance: | Meeting industry standards ensures consistent quality and performance. | Examples include ASTM International standards for metal powders. |
Understanding these specifications empowers you to make informed decisions for your AM projects. Don’t hesitate to consult with powder manufacturers and AM experts to identify the perfect match for your needs.
サプライヤーと価格
のコスト 積層造形用粉末 varies depending on several factors, including the material type, particle size, grade, and demand. Here’s a table outlining some general price ranges:
素材タイプ | 価格帯(米ドル/kg) |
---|---|
チタンパウダー | $100 – $500 |
ステンレス鋼粉 | $50 – $200 |
アルミニウム粉末 | $20 – $100 |
Nickel Superalloy Powders | $200 – $1000 |
Cobalt-Chrome Powders | $100 – $300 |
Supplier Spotlight:
Several leading companies supply high-quality Additive Manufacturing Powders. Here are a few prominent players:
- ヘガネスAB A global leader in metal powder manufacturing, offering a wide range of materials and grades.
- AP Powder Company: Specializes in high-performance metal powders for demanding applications.
- Carpenter Additive: Provides metal powders specifically optimized for Additive Manufacturing processes.
- Sandvik Additive Manufacturing: Offers a comprehensive range of powders and AM services.
- LPWテクノロジー: Specializes in high-quality metal powders for laser powder bed fusion (LPBF) technology.
Remember, these are just a few examples. Numerous other suppliers cater to the growing demand for Additive Manufacturing Powders. Researching and comparing options is crucial to find the best fit for your budget and project requirements.
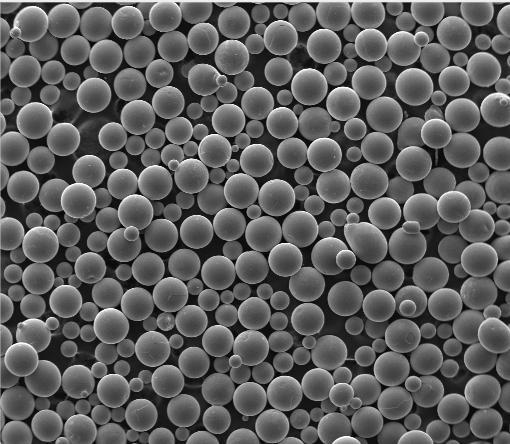
長所と短所 積層造形用粉末
Additive Manufacturing Powders unlock incredible possibilities, but like any technology, they have both advantages and limitations:
メリット
- デザインの自由: Create complex geometries impossible with traditional manufacturing techniques.
- 軽量化: Produce lighter components for improved efficiency in aerospace and automotive industries.
- マス・カスタマイゼーション: Craft personalized parts and products tailored to individual needs.
- 廃棄物の削減: Minimize material waste compared to subtractive manufacturing processes.
- オンデマンド製造: Produce parts closer to the point of use, reducing lead times and logistics complexity
デメリット
- Higher Material Costs: Additive Manufacturing Powders can be more expensive than traditionally manufactured materials.
- 限られたビルドサイズ: Current AM technologies have limitations on the size of parts that can be produced.
- 表面粗さ: Parts made with some powder types may require additional post-processing for a smooth finish.
- Process Qualification: The AM process needs to be qualified for each specific powder-part combination, adding time and cost.
- Powder Safety: Handling fine metal powders requires proper safety precautions to avoid inhalation or explosion risks.
電話をかける
Weighing the pros and cons is crucial before diving into the world of 積層造形用粉末. Consider the specific application, budget constraints, and desired part properties to make an informed decision.
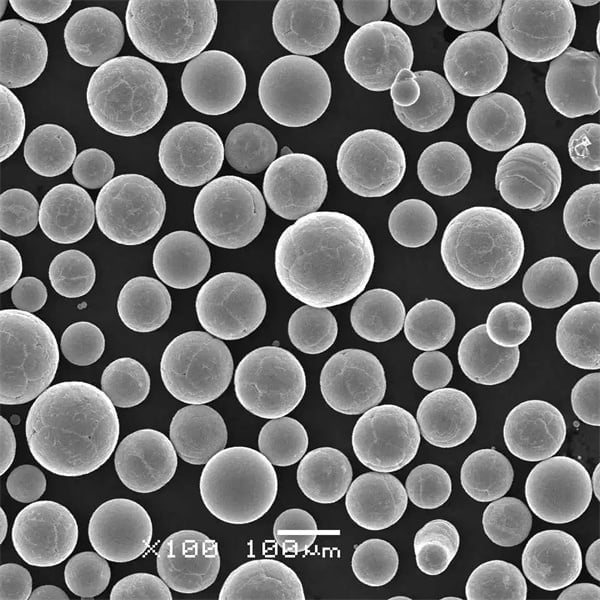
FAQ
Here are some frequently asked questions (FAQs) to shed further light on Additive Manufacturing Powders:
Q: Can I use recycled metal powders in Additive Manufacturing?
A: Yes, research into using recycled metal powders for AM is ongoing. However, the process requires strict controls to ensure consistent quality and avoid contamination.
Q: How are Additive Manufacturing Powders stored?
A: Powders are typically stored in moisture-controlled environments to prevent oxidation and ensure optimal flowability.
Q: What are the different methods for applying Additive Manufacturing Powders?
A: Several methods exist, including laser powder bed fusion (LPBF), electron beam melting (EBM), and binder jetting. Each method has its own advantages and limitations depending on the material and application.
Q: What are the future trends for Additive Manufacturing Powders?
A: The future looks bright for Additive Manufacturing Powders. We can expect advancements in:
- Development of new powder materials with enhanced properties.
- Improved powder production methods for lower costs and higher efficiency.
- Standardization of powder specifications for better consistency and quality control.
- Multi-material powders enabling creation of parts with graded properties or integrated functionalities.
As these trends unfold, Additive Manufacturing Powders will continue to revolutionize how we design and create objects, pushing the boundaries of what’s possible.
結論
Additive Manufacturing Powders are the building blocks of a transformative technology. From complex aerospace components to personalized medical implants, these tiny particles hold immense potential. By understanding the different powder types, their properties, and the factors influencing their selection, you can harness this power to create innovative solutions for a multitude of applications. As the technology continues to evolve and new materials emerge, the possibilities are truly limitless. So, are you ready to embrace the magic of Additive Manufacturing Powders?
3DP mETALについて
製品カテゴリー
お問い合わせはこちら
何かご質問はありますか?今すぐメッセージを送信してください。あなたのメッセージを受信後、全チームで検討させていただきます。