Overview of Atomization
原子化 (げんしか) is a process widely used in various industries to convert bulk liquid into a spray or powder form through the application of energy. This method is crucial in fields such as pharmaceuticals, metallurgy, and chemical engineering due to its ability to create fine, uniform particles. Understanding atomization is essential for optimizing processes that require precise particle sizes and distributions.
What is Atomization?
At its core, atomization involves breaking down a liquid into smaller droplets or particles. This can be achieved through different methods, including ultrasonic, hydraulic, pneumatic, and electrostatic atomization. Each technique has unique characteristics and applications, making atomization a versatile tool in manufacturing and processing.
Key Aspects of Atomization
- Types of Atomization: Various methods such as ultrasonic, pneumatic, and hydraulic.
- アプリケーション: Utilized in industries like pharmaceuticals, food processing, and metallurgy.
- メリット: Enhanced control over particle size and distribution, improved product quality.
- 課題: Equipment cost, maintenance, and the need for precise control parameters.
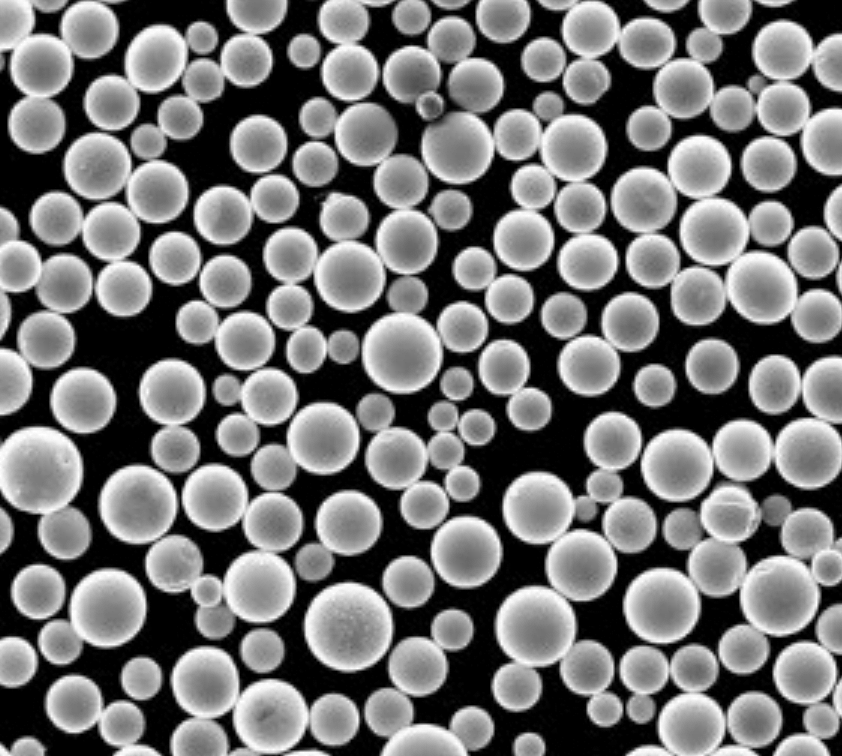
種類 原子化 (げんしか) 方法
Different atomization techniques cater to specific industrial needs, from creating metal powders to producing fine mists for cooling or coating. Here, we’ll dive into the most common atomization methods:
超音波霧化
This method uses high-frequency sound waves to create vibrations in the liquid, causing it to break into fine droplets. It’s particularly useful for creating uniform particle sizes.
プロパティ
- Particle Size: 1-10 microns
- Applications: Drug delivery systems, spray drying
- Advantages: High uniformity, low energy consumption
- Disadvantages: Limited to low-viscosity liquids
Pneumatic Atomization
Pneumatic atomization involves using compressed air to atomize liquids. This technique is common in spray painting and coating applications.
プロパティ
- Particle Size: 10-50 microns
- Applications: Paint spraying, agricultural spraying
- Advantages: Versatile, suitable for various viscosities
- Disadvantages: Higher energy consumption compared to ultrasonic
Hydraulic Atomization
In hydraulic atomization, high-pressure liquid is forced through a small nozzle, creating fine droplets. It’s widely used in fuel injection systems and industrial spray applications.
プロパティ
- Particle Size: 50-200 microns
- Applications: Fuel injection, fire suppression systems
- Advantages: Simple setup, effective for high-viscosity fluids
- Disadvantages: Nozzle wear, high pressure requirements
Electrostatic Atomization
This method uses electrostatic forces to charge liquid particles, which then disperse due to repulsion between like charges. It’s highly efficient for coating and agricultural applications.
プロパティ
- Particle Size: 1-50 microns
- Applications: Coating, agricultural spraying
- Advantages: High transfer efficiency, reduced overspray
- Disadvantages: Sensitive to environmental conditions
Metal Powder Models and Their Descriptions
In metallurgy, atomization is a key process for producing metal powders with specific properties required for various applications. Here are some notable metal powder models:
1. Stainless Steel 316L Powder
組成:
- クロム:16-18%
- ニッケル10-14%
- モリブデン2-3%
プロパティ
- 耐蝕性
- 高い引張強度
アプリケーション
- 医療用インプラント
- 航空宇宙コンポーネント
2. Titanium Alloy Powder (Ti-6Al-4V)
組成:
- チタン:90%
- アルミニウム:6%
- バナジウム:4%
プロパティ
- 軽量
- 高い強度重量比
アプリケーション
- 航空宇宙部品
- Biomedical devices
3. Copper Powder
組成:
- Copper: 99.9%
プロパティ
- 優れた導電性
- 高い熱伝導率
アプリケーション
- 電気部品
- 熱交換器
4. Aluminum Alloy Powder (AlSi10Mg)
組成:
- Aluminum: 90%
- Silicon: 10%
- Magnesium: 0.4-0.6%
プロパティ
- 軽量
- 良好な鋳造性
アプリケーション
- 自動車用部品
- 構造コンポーネント
5. Nickel Alloy Powder (Inconel 718)
組成:
- ニッケル50-55%
- クロム:17-21%
- Iron: 4.75-5.5%
- Niobium: 4.75-5.5%
プロパティ
- 高温耐性
- 耐蝕性
アプリケーション
- ガスタービン
- Jet engines
6. Iron Powder
組成:
- Iron: 99.5%
プロパティ
- 高い磁気特性
- Good compressibility
アプリケーション
- 粉末冶金
- Magnetic materials
7. Cobalt-Chromium Alloy Powder (CoCrMo)
組成:
- Cobalt: 60%
- Chromium: 27-30%
- モリブデン5-7%
プロパティ
- 高い耐摩耗性
- 生体適合性
アプリケーション
- Dental implants
- 整形外科インプラント
8.タンタル粉末
組成:
- Tantalum: 99.9%
プロパティ
- 高い融点
- 耐蝕性
アプリケーション
- 医療機器
- エレクトロニクス
9. Molybdenum Powder
組成:
- Molybdenum: 99.9%
プロパティ
- 高温安定性
- 良好な熱伝導率
アプリケーション
- High-temperature furnaces
- エレクトロニクス
10. Magnesium Alloy Powder
組成:
- Magnesium: 90%
- Aluminum: 9%
- Zinc: 1%
プロパティ
- 軽量
- 高い強度重量比
アプリケーション
- Automotive industry
- 航空宇宙コンポーネント
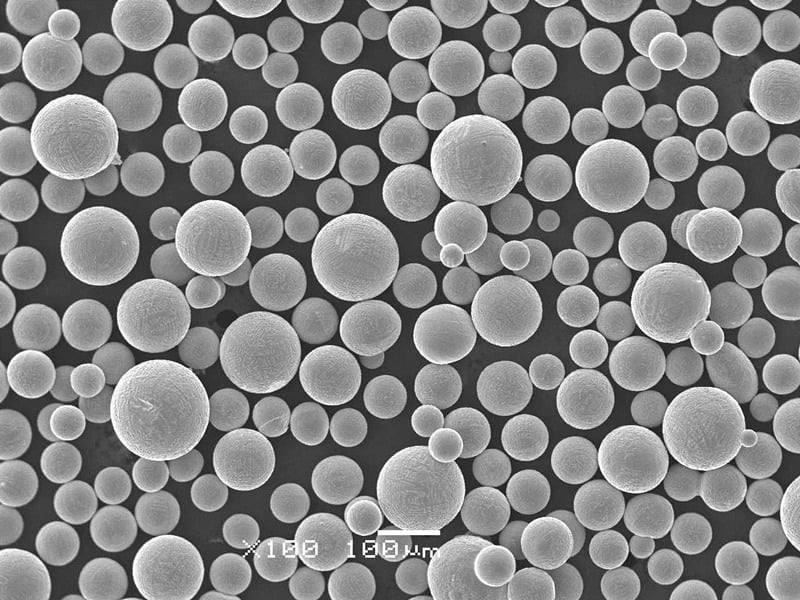
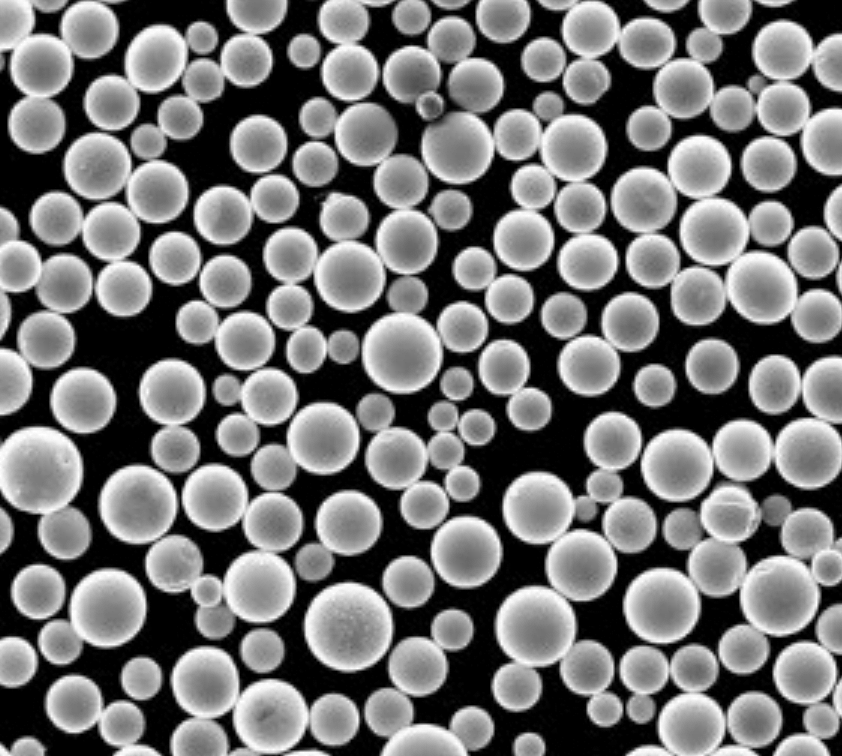
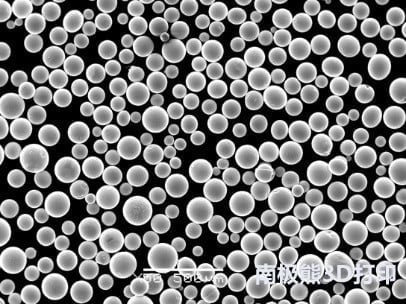
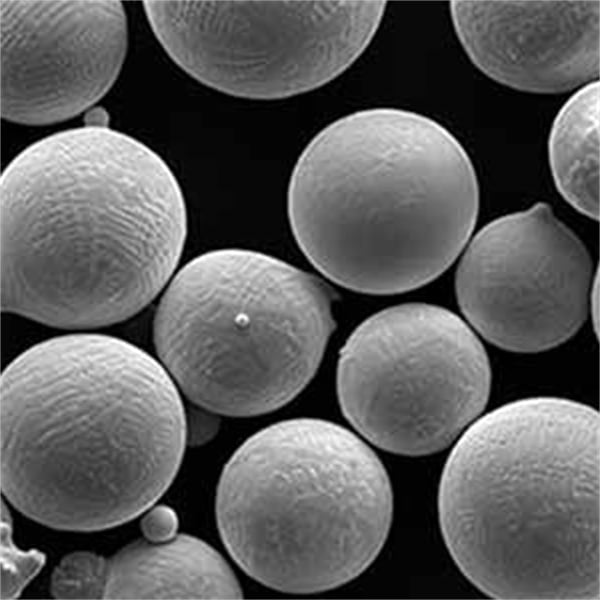
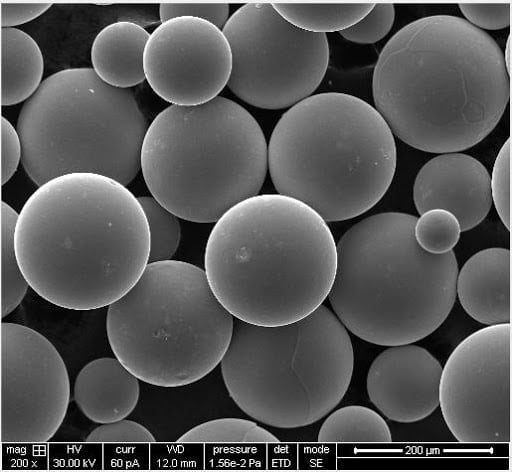
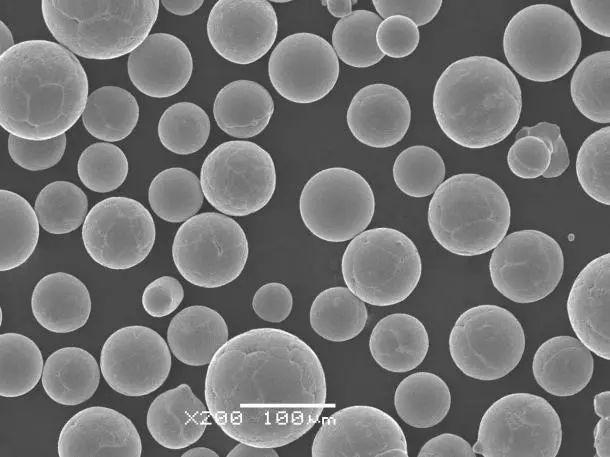
応用例 原子化 (げんしか)
Atomization finds applications across a diverse range of industries. Here are some key sectors where atomization plays a crucial role:
Pharmaceutical Industry
Atomization is used in the production of fine powders for inhalers, enhancing drug delivery efficiency.
Food and Beverage Industry
In this industry, atomization is used for spray drying, which helps in creating powdered forms of products like milk, coffee, and spices.
冶金学
Atomization is essential for producing metal powders used in additive manufacturing and powder metallurgy.
農業
Pneumatic and electrostatic atomization techniques are used for pesticide and fertilizer spraying, ensuring even distribution and minimizing waste.
コーティングと塗料
Atomization techniques provide uniform coating layers, enhancing the quality and durability of the finish.
Fuel Injection Systems
Hydraulic atomization is used in fuel injectors to create fine fuel mist, improving combustion efficiency.
仕様、サイズ、等級、規格
When selecting metal powders or atomization equipment, understanding specifications, sizes, grades, and standards is crucial.
金属粉
メタルパウダー | 粒子サイズ | グレード | 標準 |
---|---|---|---|
ステンレススチール316L | 15~45ミクロン | ASTM F138 | ISO 5832-1 |
チタン合金 (Ti-6Al-4V) | 20-53 microns | 23年次 | ASTM B348 |
銅 | 25〜45ミクロン | C11000 | ASTM B170 |
アルミニウム合金 (AlSi10Mg) | 10-45マイクロメートル | EN AW-6061 | ISO 3522 |
Nickel Alloy (Inconel 718) | 15-53ミクロン | AMS 5662 | ASTM B637 |
鉄 | 20~50ミクロン | AISI 1008 | ASTM B241 |
Cobalt-Chromium (CoCrMo) | 15~45ミクロン | F75 | ASTM F1537 |
タンタル | 10-45マイクロメートル | ASTM F560 | ISO 13782 |
モリブデン | 15~45ミクロン | Mo1 | ASTM B386 |
Magnesium Alloy | 20~50ミクロン | AZ91D | ASTM B403 |
Atomization Equipment
Equipment Type | 仕様 | 標準 |
---|---|---|
Ultrasonic Atomizer | Frequency: 20 kHz | ASTM E1138 |
Pneumatic Atomizer | Air Pressure: 1-5 bar | ISO 12100 |
Hydraulic Atomizer | Pressure: 50-200 bar | ISO 5167 |
Electrostatic Atomizer | Voltage: 10-30 kV | ASTM D618 |
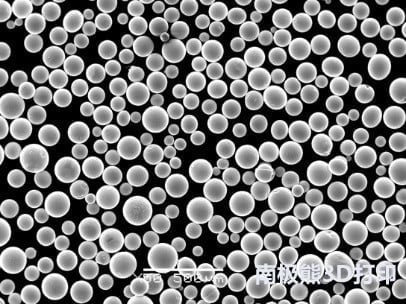
サプライヤーと価格詳細
Finding the right supplier and understanding pricing details is essential for businesses looking to implement atomization processes.
金属粉サプライヤー
サプライヤー | メタルパウダー | 価格(kgあたり) | 連絡先 |
---|---|---|---|
Advanced Powder & Coatings | ステンレススチール316L | $100 | www.apc.com |
Global Titanium | チタン合金 (Ti-6Al-4V) | $300 | www.globaltitanium.com |
Copper Industries Inc. | 銅 | $50 | www.copperindustries.com |
Alumetal Corp. | アルミニウム合金 (AlSi10Mg) | $70 | www.alumetalcorp.com |
Superalloys Inc. | Nickel Alloy (Inconel 718) | $200 | www.superalloys.com |
Atomization Equipment Suppliers
サプライヤー | Equipment Type | 価格の範囲 | 連絡先 |
---|---|---|---|
Atomizer World | Ultrasonic Atomizer | $10,000 – $50,000 | www.atomizerworld.com |
SprayTech Solutions | Pneumatic Atomizer | $5,000 – $25,000 | www.spraytechsolutions.com |
Hydraulic Systems Inc. | Hydraulic Atomizer | $15,000 – $60,000 | www.hydraulicsystems.com |
ElectroStatic Inc. | Electrostatic Atomizer | $20,000 – $80,000 | www.electrostaticinc.com |
の長所と短所を比較する 原子化 (げんしか) 方法
超音波霧化
長所だ:
- High uniformity
- Low energy consumption
- Suitable for fine particles
短所だ:
- Limited to low-viscosity liquids
- 高いイニシャルコスト
Pneumatic Atomization
長所だ:
- 多用途
- Suitable for various viscosities
短所だ:
- Higher energy consumption
- Nozzle clogging issues
Hydraulic Atomization
長所だ:
- Simple setup
- Effective for high-viscosity fluids
短所だ:
- Nozzle wear
- High pressure requirements
Electrostatic Atomization
長所だ:
- High transfer efficiency
- Reduced overspray
短所だ:
- Sensitive to environmental conditions
- Requires precise control
Advantages of Atomization
Atomization offers several advantages across different industries:
Enhanced Particle Control
Atomization allows for precise control over particle size and distribution, which is critical in applications like pharmaceuticals and additive manufacturing.
Improved Product Quality
By creating uniform particles, atomization improves the consistency and quality of the final product, whether it’s a metal powder or a food ingredient.
汎用性
With multiple methods available, atomization can be adapted to suit various liquids and applications, from low-viscosity solutions to high-viscosity suspensions.
エネルギー効率
Some atomization methods, like ultrasonic atomization, are energy efficient, reducing operational costs over time.
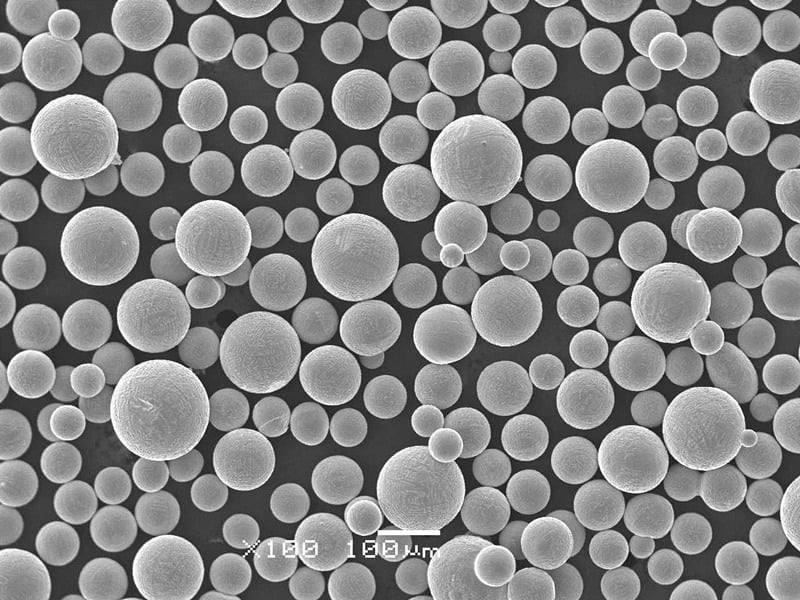
のデメリット 原子化 (げんしか)
Despite its many benefits, atomization also presents some challenges:
高いイニシャルコスト
The equipment required for atomization, especially advanced systems like ultrasonic and electrostatic atomizers, can be expensive.
メンテナンス要件
Atomizers, particularly hydraulic and pneumatic types, require regular maintenance to prevent issues like nozzle clogging and wear.
Complex Control Systems
Methods like electrostatic atomization need precise control systems to maintain efficiency and effectiveness, which can complicate the setup and operation.
Environmental Sensitivity
Some atomization techniques are sensitive to environmental conditions like humidity and temperature, affecting their performance and reliability.
FAQ
What is atomization used for?
Atomization is used to create fine droplets or particles from a liquid. It is widely applied in industries such as pharmaceuticals, metallurgy, food processing, and agriculture to improve product quality and process efficiency.
What are the different types of atomization?
The main types of atomization include ultrasonic, pneumatic, hydraulic, and electrostatic atomization. Each method has its own advantages, disadvantages, and specific applications.
Which atomization method is the most energy-efficient?
Ultrasonic atomization is generally considered the most energy-efficient method due to its low power consumption and high particle uniformity.
Can atomization be used for high-viscosity liquids?
Yes, hydraulic atomization is particularly effective for high-viscosity liquids, making it suitable for applications like fuel injection and industrial spraying.
What are the main challenges of using atomization?
The primary challenges include high initial equipment costs, maintenance requirements, the need for precise control systems, and sensitivity to environmental conditions.
How does atomization improve product quality?
By producing uniform particles, atomization enhances the consistency and quality of products. This is crucial in industries like pharmaceuticals, where precise dosages and delivery methods are essential.
3DP mETALについて
製品カテゴリー
お問い合わせはこちら
何かご質問はありますか?今すぐメッセージを送信してください。あなたのメッセージを受信後、全チームで検討させていただきます。