Have you ever wondered how intricate metal parts are formed? Imagine a world where metal isn’t just about hefty sheets or robust bars, but a versatile material that can be manipulated on a microscopic level. This is the fascinating realm of アトマイズ金属粉, where molten metal is transformed into a fine, free-flowing powder with unique properties and a vast array of applications. Buckle up, because we’re about to embark on a journey into the wonderful world of atomized metal powders!
Characteristics of Atomized Metal Powders
Unlike their bulk counterparts, atomized metal powders boast some truly remarkable characteristics. Here’s a closer look at what sets them apart:
- High Flowability: Imagine pouring sand – that’s the essence of flowability. Atomized metal powders, due to their spherical or near-spherical shapes, flow freely, making them ideal for processes like additive manufacturing (3D printing) and metal injection molding (MIM).
- High Packing Density: Think packing tennis balls versus packing pebbles. The smooth, spherical nature of atomized powders allows them to pack tightly together, maximizing the amount of metal powder in a given space. This is crucial for creating strong and dense final products.
- Controlled Porosity: Porosity refers to the existence of tiny air pockets within the material. In atomized powders, porosity can be precisely controlled. This opens doors for applications like filters, where a specific level of porosity is essential for optimal performance.
- Tailored Properties: The beauty of atomization lies in its ability to control particle size, morphology (shape), and even composition. This allows manufacturers to create powders with properties specifically suited for their desired application.
So, how do these remarkable powders come into existence?
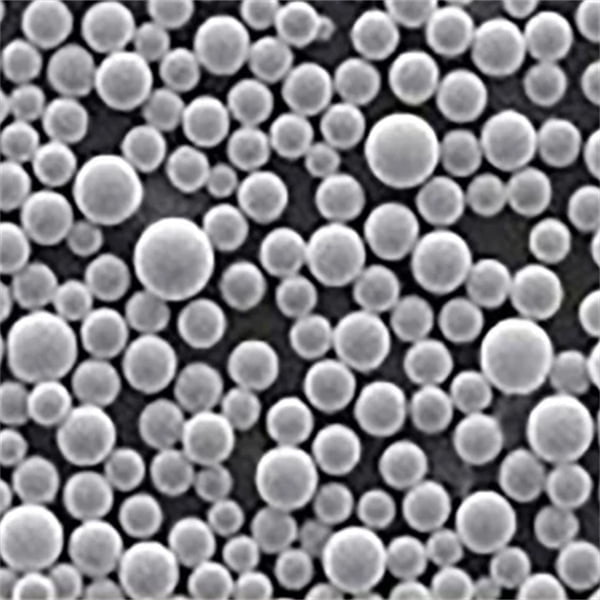
Preparation Methods of アトマイズ金属粉
There are two primary methods for creating atomized metal powders:
- 水の霧化: This method involves breaking down a stream of molten metal with a high-pressure water jet. The resulting metal droplets rapidly solidify into fine powders. Water atomization is a cost-effective technique, particularly suited for producing iron and steel powders. However, the high-pressure water can introduce some oxide contamination into the powder.
- ガス霧化: In this method, an inert gas like argon or nitrogen is used to break up the molten metal stream. This creates cleaner powders with lower oxygen content compared to water atomization. Gas atomization is ideal for high-performance applications and reactive metals like titanium and aluminum. However, it’s generally a more expensive process compared to water atomization.
Now that we’ve explored the creation process, let’s delve into the exciting world of applications!
Applications of Atomized Metal Powders
Atomized metal powders are revolutionizing various industries with their unique properties and versatility. Here are some of the most prominent applications:
- アディティブ・マニュファクチャリング(3Dプリンティング): The ability of atomized powders to flow freely and bond together precisely makes them perfect for 3D printing. Complex metal parts can be created layer by layer, opening doors for innovation in aerospace, automotive, and medical industries.
- 金属射出成形(MIM): MIM is a game-changer for producing intricate and near-net-shape metal parts. A mixture of atomized metal powder and binder is molded into the desired shape and then heat-treated to remove the binder and fuse the metal particles, resulting in high-precision metal components.
- 溶射: This technique involves spraying atomized metal powders onto a surface to create a protective coating. Think of it like painting with metal! Thermal spraying is used to enhance wear resistance, corrosion resistance, and thermal properties of various components.
- ろう付け: Brazing is a joining technique that utilizes molten metal to bond two similar or dissimilar metals. Atomized metal powders, with their controlled melting points and flow characteristics, are finding increasing use in brazing applications for their efficiency and precision.
- その他の用途 The applications of atomized metal powders extend far beyond these examples. They are used in catalysts, pigments, conductive inks, and even in pyrotechnics to create dazzling firework displays!
As with any technology, there are factors to consider when choosing atomized metal powders.
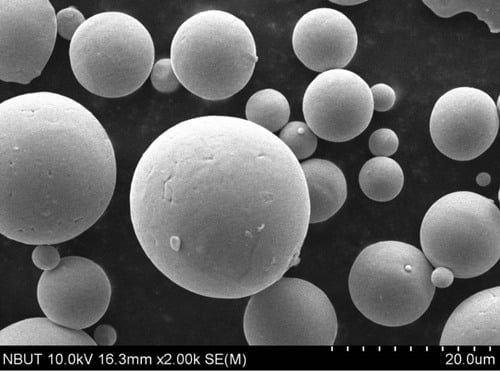
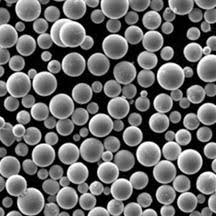
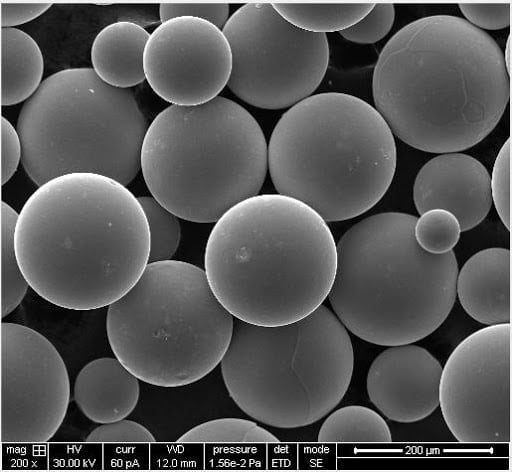
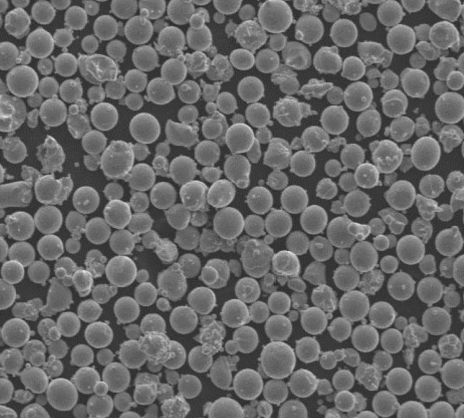
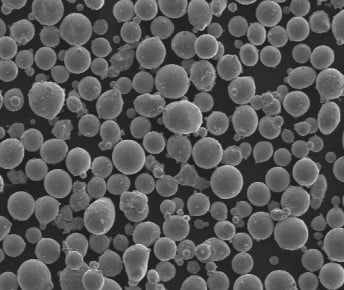
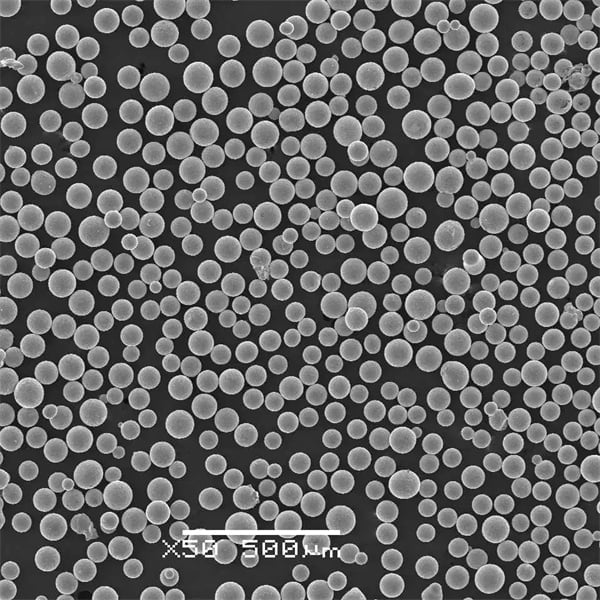
Selection Considerations for アトマイズ金属粉
Selecting the right atomized metal powder for your application is crucial. Here are some key factors to ponder:
- Material: The type of metal (iron, aluminum, titanium, etc.) will obviously depend on the desired properties of the final product.
- 粒子径と分布: The size and distribution of the powder particles significantly impact flowability, packing density, and the final product’s surface finish. For instance, finer powders offer smoother surface finishes but may be challenging to handle due to reduced flowability. Conversely, larger particles flow more freely but can result in a rougher surface finish.
- Morphology (Shape): Remember the discussion about spherical shapes and flowability? The morphology of the powder particles also plays a role. Perfectly spherical particles offer the best flowability, while irregular shapes can improve packing density.
- 化学組成: The presence of impurities like oxygen can affect the final product’s properties. The choice between water or gas atomization often hinges on the desired level of purity.
- コストだ: Production methods and material type significantly impact the cost of atomized metal powders. Striking a balance between cost and desired properties is essential.
Now, let’s address some of the burning questions you might have about atomized metal powders!
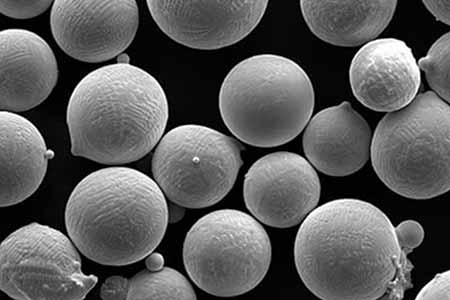
FAQ
Here’s a table addressing some frequently asked questions about atomized metal powders:
質問 | 回答 |
---|---|
What are the advantages of atomized metal powders over traditional metalworking methods? | Atomized powders offer several advantages: greater design flexibility (especially in 3D printing), minimal material waste, precise control over properties, and the ability to create near-net-shape components. |
Are there any limitations to using atomized metal powders? | While versatile, atomized powders have limitations. They can be more expensive than traditional methods for some applications. Additionally, achieving desirable mechanical properties in the final product may require post-processing techniques. |
What’s the future outlook for atomized metal powders? | The future of atomized metal powders is incredibly bright! Advancements in atomization technology will lead to even finer and more precisely controlled powders. This, coupled with the ongoing development of 3D printing and MIM techniques, will undoubtedly propel atomized metal powders towards even wider adoption across various industries. |
3DP mETALについて
製品カテゴリー
お問い合わせはこちら
何かご質問はありますか?今すぐメッセージを送信してください。あなたのメッセージを受信後、全チームで検討させていただきます。