Imagine a world where you can create intricate, high-strength metal components directly from a digital file. This isn’t science fiction; it’s the reality of EBM Additive Manufacturing, a revolutionary 3D printing technology that’s transforming the way we design and manufacture metal parts.
EBM, also known as Electron Beam Melting, utilizes a focused beam of high-energy electrons to melt metal powder layer by layer, meticulously building a three-dimensional object based on a computer-aided design (CAD) model. Think of it like a high-tech inkjet printer, but instead of ink cartridges, it uses metal powder and a supercharged electron beam as its “ink” and “printhead.”
This cutting-edge technology offers a plethora of advantages, making it ideal for applications where traditional manufacturing methods fall short. So, buckle up and get ready to dive into the fascinating world of EBM Additive Manufacturing!
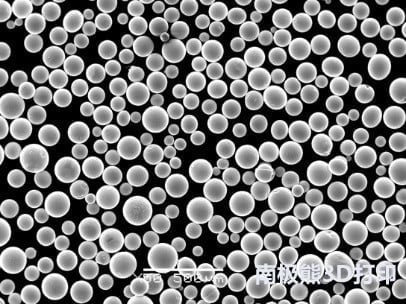
the EBM Arsenal: A Look at Popular Metal Powders
The foundation of any EBM project lies in the metal powder used. Just like artists have their favorite paints and sculptors their preferred clays, EBM specialists rely on a diverse arsenal of metal powders to bring their designs to life. Let’s explore some of the most popular options, along with their unique properties:
メタルパウダー | 作曲 | プロパティ | アプリケーション |
---|---|---|---|
ステンレススチール316L | 16-18% Chromium, 10-14% Nickel, 2-3% Molybdenum | Excellent corrosion resistance, high strength, biocompatible | Aerospace components, medical implants, chemical processing equipment |
チタン Ti6Al4V | 90%チタン、6%アルミニウム、4%バナジウム | 高い強度対重量比、優れた生体適合性、優れた耐食性 | Aerospace parts, medical implants, sporting goods |
インコネル 625 | Nickel-chromium-based superalloy | Exceptional high-temperature strength, corrosion resistance, good weldability | Gas turbine components, heat exchangers, rocket engine parts |
Cobalt Chrome (CoCr) | Cobalt and Chromium alloy | High wear resistance, biocompatible, good strength | Joint replacements, dental implants, cutting tools |
アルミニウム AlSi10Mg | Aluminum alloy with 10% Silicon and 0.5% Magnesium | Lightweight, good strength, high thermal conductivity | Automotive components, electronics enclosures, heat sinks |
銅 Cu | ピュアカッパー | Excellent electrical conductivity, high thermal conductivity | Heat exchangers, electrical connectors, waveguides |
MP1 Maraging Steel | High Nickel alloy with low Carbon content | Exceptional strength, good toughness, high dimensional stability | Aerospace parts, tooling, molds and dies |
Nickel Hastelloy C-276 | Nickel-chromium-molybdenum alloy | Superior corrosion resistance in harsh environments | Chemical processing equipment, pollution control systems, marine applications |
タングステンW | 純タングステン | High melting point, excellent wear resistance | High-temperature furnace components, electrodes, rocket engine nozzles |
Tantalum Ta | 純タンタル | 生体適合性、優れた耐食性 | Medical implants, capacitors, chemical processing equipment |
This list merely scratches the surface of the metal powders available for EBM. New and innovative materials are constantly being developed, pushing the boundaries of what’s possible. The choice of metal powder ultimately depends on the specific requirements of the application, such as strength, weight, corrosion resistance, and biocompatibility.
Applications of EBM Additive Manufacturing
EBM isn’t just a fancy technology; it’s a powerful tool that’s revolutionizing various industries. Here are some of the most prominent applications of EBM Additive Manufacturing:
- 航空宇宙: The ability to create lightweight, high-strength components like turbine blades and engine housings makes EBM a game-changer for the aerospace industry. EBM parts can help reduce fuel consumption and improve aircraft performance.
- 医療 EBM’s biocompatible metal powders pave the way for the creation of customized implants like knee replacements and hip joints. These implants offer excellent strength, durability, and biocompatibility, leading to improved patient outcomes.
- 自動車: From lightweight brackets to intricate transmission components, EBM is making its mark in the automotive industry. The ability to create complex geometries with minimal material waste allows for design optimization and improved fuel efficiency.
- エネルギーだ: EBM is used to create components for power generation equipment, such as turbine blades and heat exchangers. The high-temperature capabilities of some metal powders make them ideal for these demanding applications.
- 消費財: From customized bike frames to high-performance sports equipment, EBM is finding its way into the consumer goods market. The ability to create complex, lightweight parts with unique designs opens doors for innovative products that push the boundaries of performance and aesthetics.
Beyond these core applications, EBM is also used in various niche markets, including:
- ディフェンス EBM is used to create intricate components for military applications, such as weapon parts and guidance systems.
- Jewelry: The ability to create intricate and detailed designs with minimal material waste makes EBM an attractive option for high-end jewelry production.
- Research & Development: EBM’s versatility allows researchers and developers to create prototypes and test new materials and designs quickly and efficiently.
The potential applications of EBM Additive Manufacturing are vast and ever-expanding. As the technology matures and costs decrease, we can expect to see EBM play an even greater role in shaping the future of manufacturing across diverse industries.
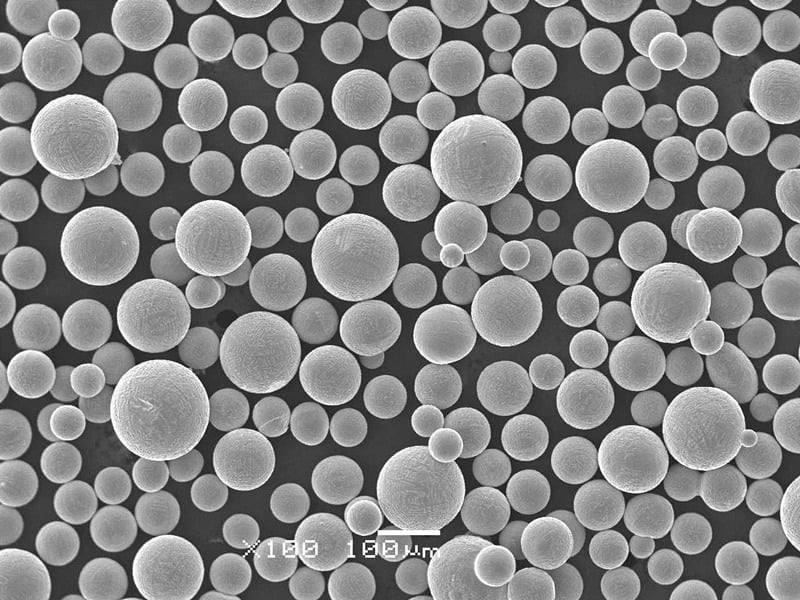
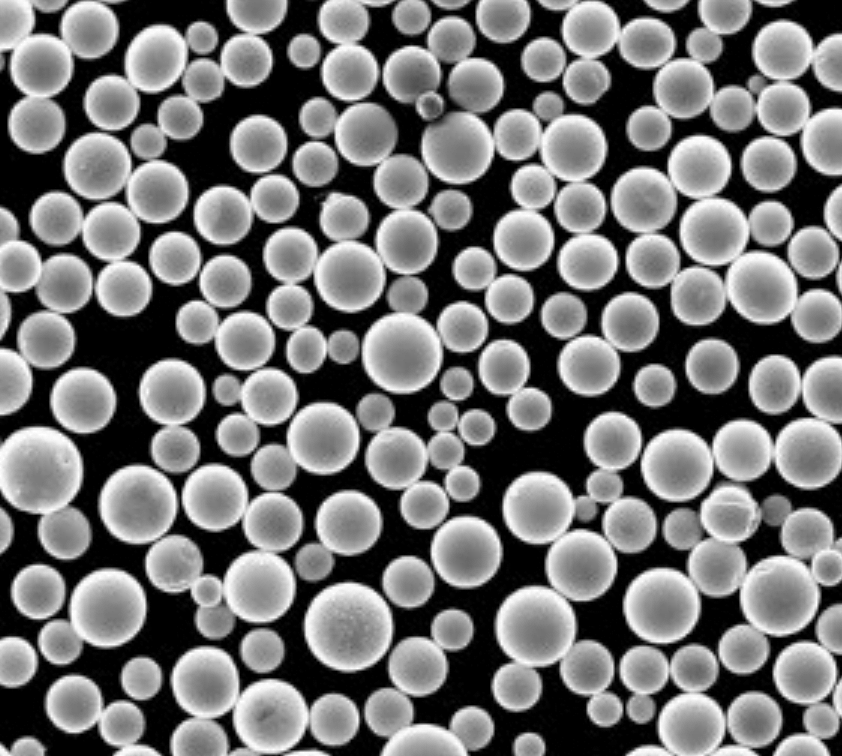
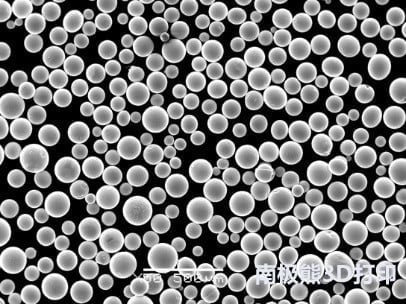
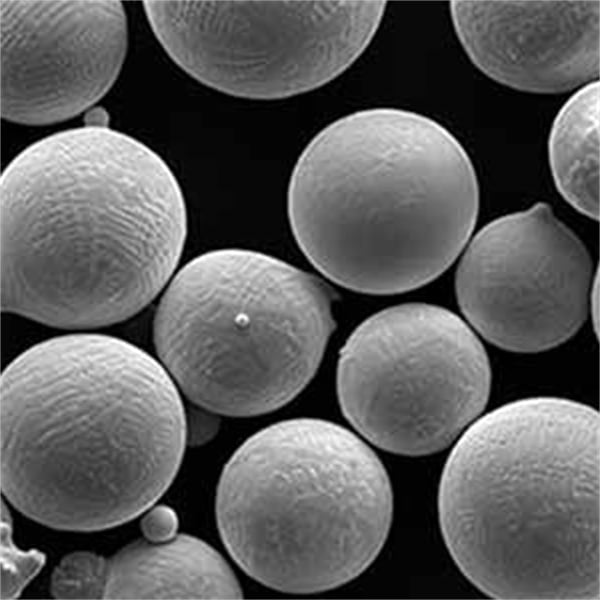
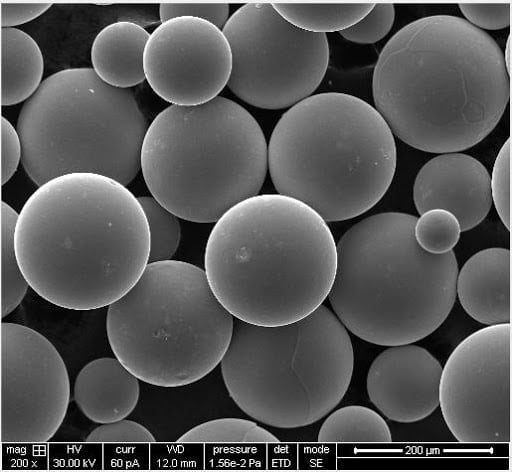
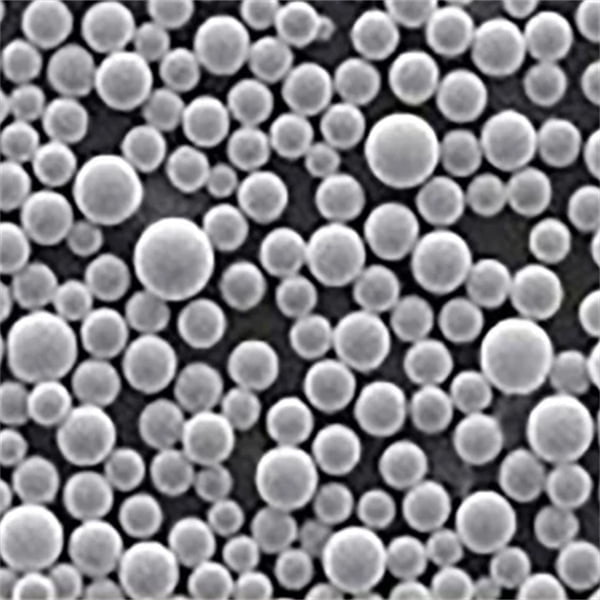
the Advantages: Why Choose EBM Additive Manufacturing?
EBM boasts a compelling set of advantages that make it a standout choice for specific applications. Here’s a closer look at some of the key benefits:
- デザインの自由: Unlike traditional manufacturing methods limited by subtractive processes, EBM allows for the creation of complex geometries with intricate internal features. This design freedom opens doors for parts with improved performance and lighter weight.
- High Strength and Density: EBM parts achieve near-net-shape densities, resulting in components with exceptional strength and durability. This makes EBM ideal for applications demanding high structural integrity.
- 素材の多様性: EBM works with a wide range of metal powders, including high-performance alloys and biocompatible materials. This versatility allows for the creation of parts specifically tailored for the application’s needs.
- 材料の無駄を最小限に抑える: EBM utilizes a powder-bed fusion process, minimizing material waste compared to traditional methods like machining. This not only reduces costs but also aligns with sustainable manufacturing practices.
- ニア・ネットシェイプ・マニュファクチャリング: EBM parts require minimal post-processing compared to other additive manufacturing techniques. This translates to faster production times and lower overall costs.
EBM shines in applications where traditional manufacturing methods struggle to deliver the desired level of complexity, strength, and material properties. For instance, imagine a lightweight aircraft component with intricate internal channels for enhanced heat dissipation. EBM can create such a part in a single build, whereas traditional methods might require multiple components and complex assembly processes.
Limitations of EBM Additive Manufacturing
While EBM offers a plethora of advantages, it’s essential to acknowledge its limitations:
- 高コスト: EBM machines and metal powders can be expensive compared to some traditional manufacturing methods. However, the cost-benefit analysis often favors EBM for parts requiring high complexity or performance that traditional methods struggle to achieve.
- 表面粗さ: EBM parts can have a slightly rougher surface finish compared to some other 3D printing techniques. This might necessitate additional post-processing steps depending on the application requirements.
- 限られたビルドサイズ: While EBM machines are growing in size, their build volumes are generally smaller compared to some other additive manufacturing technologies. This might limit the size of parts that can be produced using EBM.
- Vacuum Environment: The EBM process takes place in a vacuum chamber, adding complexity and potentially increasing production costs compared to non-vacuum based 3D printing methods.
Understanding these limitations is crucial for making informed decisions about whether EBM is the right choice for a particular application. It’s important to weigh the advantages against the limitations and consider the cost-benefit analysis in the context of the specific project requirements.
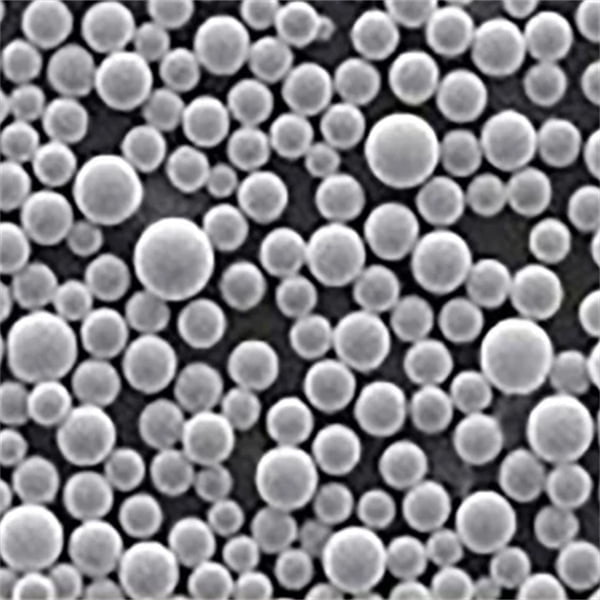
Advantages vs. Disadvantages
Here’s a table summarizing the key advantages and disadvantages of EBM Additive Manufacturing to provide a clearer picture:
特徴 | メリット | デメリット |
---|---|---|
デザインの自由 | Complex geometries, intricate internal features | Limited build size |
High Strength & Density | Near-net-shape densities, exceptional strength | Surface roughness might require post-processing |
素材の多様性 | Wide range of metal powders, including high-performance alloys | High cost of machines and metal powders |
Minimal Material Waste | Powder-bed fusion process minimizes waste | Vacuum environment adds complexity |
ニアネットシェイプ製造 | Less post-processing needed | Not suitable for all part sizes |
Ultimately, the decision to use EBM hinges on the specific needs of the project. For applications demanding high complexity, exceptional strength, and the use of unique materials, EBM can be a clear winner. However, for simpler parts or projects with less demanding material requirements, other additive manufacturing technologies or traditional methods might be more cost-effective.
the Specifications: A Look at EBM Printability
Just like any other technology, EBM has its own set of specifications to consider. Here’s a breakdown of some key parameters to keep in mind:
- 層の厚さ: EBM utilizes a layered building approach, and the layer thickness significantly impacts the resolution and surface finish of the final part. Typical layer thicknesses for EBM range from 30 to 100 microns.
- Minimum Feature Size: The minimum feature size achievable with EBM depends on the metal powder and machine capabilities. Generally, EBM can produce features as small as 50 microns.
- Build Volume: As mentioned earlier, EBM machines have limitations on the size of parts they can create. Build volumes can vary depending on the specific machine model, but they typically range from a few cubic centimeters to several hundred cubic centimeters.
- Accuracy and Tolerance: EBM parts can achieve high dimensional accuracy and tight tolerances. However, achieving ultra-fine tolerances might require additional post-processing techniques.
Understanding these specifications is essential for designing parts suitable for EBM production. Consulting with an EBM specialist during the design phase can help ensure the final part meets all functional and aesthetic requirements.
the Suppliers: Who Makes EBM Machines?
If you’re considering EBM for your project, you’ll need to know who the key players are in the EBM machine manufacturing landscape. Here are some of the leading suppliers of EBM machines:
- Arcam AB (GE Additive): A Swedish company acquired by GE Additive, Arcam is a pioneer in EBM technology and offers a range of machine models for various applications.
- EOS GmbH: A German multinational specializing in additive manufacturing technologies, EOS offers EBM machines known for their user-friendliness and reliability.
- Trumpf GmbH + Co. KG: A German multinational known for its industrial lasers and manufacturing solutions, Trumpf also offers EBM machines designed for high productivity and large build volumes.
- Renishaw plc: A British engineering and technology company, Renishaw offers EBM machines known for their precision and advanced features.
These are just a few of the major players in the EBM machine market. Each company offers a variety of machine models with different capabilities and price points. It’s crucial to research and compare the offerings of these suppliers to find the machine that best suits your specific needs and budget.
When selecting an EBM machine supplier, consider factors like:
- Machine capabilities: Build volume, layer thickness, material compatibility, etc.
- Machine reliability and uptime
- Service and support options
- Software compatibility
- Cost of ownership
Partnering with a reputable EBM machine supplier with a strong track record and excellent support is crucial for a successful EBM project.
Additionally, a growing number of service providers offer EBM printing services. These companies can handle the entire EBM production process, from design optimization to part printing and post-processing. This can be a valuable option for companies that lack the in-house expertise or resources to operate their own EBM machines.
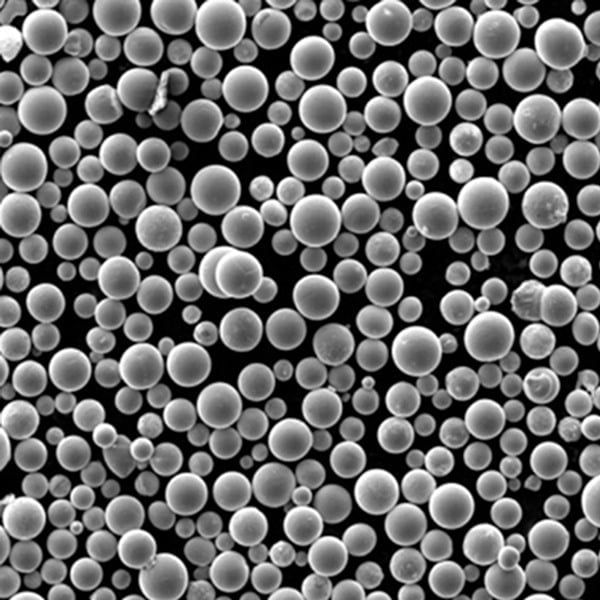
Unveiling the Future: The EBM Horizon
EBM Additive Manufacturing is a rapidly evolving technology with enormous potential. Here’s a glimpse into what the future holds for EBM:
- Advancements in Metal Powders: New metal powder formulations with improved properties like higher strength, better corrosion resistance, and even lighter weight are constantly being developed. This will expand the range of applications suitable for EBM.
- Larger Build Volumes: Machine manufacturers are continuously pushing the boundaries of build volume, allowing for the creation of even bigger and more complex parts with EBM.
- より速いビルド速度: Research is ongoing to improve the speed of the EBM process, making it more competitive with traditional manufacturing methods for high-volume production.
- コスト削減: As EBM technology matures and production volumes increase, we can expect to see a decrease in the cost of EBM machines and metal powders. This will make EBM more accessible to a wider range of companies and applications.
The future of EBM is bright. With continued advancements in technology and materials, EBM is poised to revolutionize how we design and manufacture complex metal parts across various industries.
よくあるご質問
Here’s a table addressing some of the most frequently asked questions about EBM Additive Manufacturing:
質問 | 回答 |
---|---|
What is the difference between EBM and Laser Beam Melting (LBM)? | Both EBM and LBM are powder-bed fusion additive manufacturing technologies that create parts layer by layer. However, the key difference lies in the energy source used to melt the metal powder. EBM utilizes a high-energy electron beam, while LBM uses a laser beam. This difference leads to some variations in process parameters, material compatibility, and surface finish. |
Is EBM safe? | EBM machines operate in a vacuum environment and utilize high-energy electron beams. Following proper safety protocols and using appropriate personal protective equipment (PPE) is crucial during operation and maintenance. Consulting the machine manufacturer’s safety guidelines is essential. |
What are the environmental benefits of EBM? | Compared to traditional subtractive manufacturing methods that generate significant material waste, EBM offers a more sustainable approach. The powder-bed fusion process minimizes material waste, and EBM is compatible with recycled metal powders in many cases. |
Can EBM be used for prototyping? | Absolutely! EBM’s ability to create complex geometries and near-net-shape parts makes it ideal for rapid prototyping of metal components. This allows for faster design iterations and product development cycles. |
How strong are EBM parts? | EBM parts achieve near-net-shape densities, resulting in components with exceptional strength and durability. The specific strength depends on the chosen metal powder, but EBM parts can be as strong or even stronger than traditionally manufactured counterparts. |
What kind of post-processing is required for EBM parts? | Compared to some other additive manufacturing technologies, EBM parts generally require minimal post-processing. However, some surface finishing techniques like sandblasting or machining might be needed depending on the application requirements. |
Is EBM right for my application? | EBM is a powerful tool, but it’s not a one-size-fits-all solution. Consider the complexity of your part, the required material properties, and the production volume. If your project demands high complexity, exceptional strength, and unique materials, EBM could be a perfect fit. However, for simpler parts or projects with less demanding requirements, other options might be more suitable. Consulting with an EBM expert can help you determine if EBM is the right choice for your specific needs. |
3DP mETALについて
製品カテゴリー
お問い合わせはこちら
何かご質問はありますか?今すぐメッセージを送信してください。あなたのメッセージを受信後、全チームで検討させていただきます。