Imagine a world where complex metal parts, once relegated to the realm of science fiction, spring to life layer by layer. This isn’t a utopian dream; it’s the reality of Metal Additive Manufacturing (MAM), also known as metal 3D printing. MAM is transforming how we design, prototype, and produce metal components, ushering in a new era of innovation and efficiency.
This article delves deep into the fascinating world of MAM, exploring its operational principles, the advantages it offers over traditional methods, and the diverse applications it’s revolutionizing. We’ll also unpack some of the challenges associated with MAM and explore the exciting future it holds.
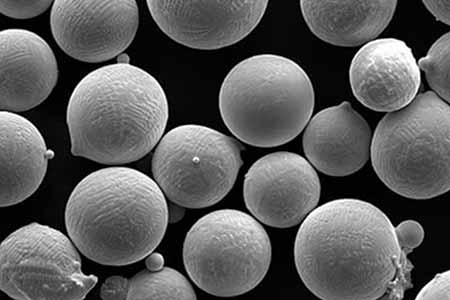
Operational Principle of Metal Additive Manufacturing (MAM)
At its core, MAM operates like a sophisticated 3D printer for metals. Here’s a breakdown of the magic behind this technology:
- Digital Blueprint: The journey begins with a computer-aided design (CAD) model of the desired metal part. This intricate digital blueprint serves as the roadmap for the MAM process.
- Material Preparation: Depending on the chosen MAM technique, the metal can be delivered in various forms like powder, wire, or even molten metal.
- Layer-by-Layer Creation: The MAM machine takes center stage now. Guided by the digital blueprint, a high-powered energy source, typically a laser, melts the metal material either in a powder bed (powder bed fusion) or directly onto a build plate (directed energy deposition). These molten layers meticulously fuse together, building the part one layer at a time.
- Support Removal: After the build process is complete, the part is often encased in support structures that held it in place during printing. These supports are meticulously removed, revealing the final metallic masterpiece.
Advantages of Metal Additive Manufacturing (MAM)
MAM boasts a compelling array of advantages that are reshaping the metalworking landscape:
- デザインの自由: Unlike traditional subtractive manufacturing techniques like machining, MAM isn’t constrained by the limitations of tools and material removal. This opens doors to creating intricate internal features, lightweight lattice structures, and complex geometries that were previously impossible to achieve.
- ラピッドプロトタイピング: Gone are the days of lengthy and expensive prototyping processes. MAM allows for the creation of functional prototypes quickly and iteratively, accelerating the design validation cycle and speeding up product development.
- 廃棄物の削減: Traditional manufacturing often generates significant scrap metal. MAM, on the other hand, utilizes a near-net-shape approach, minimizing material waste and promoting sustainability.
- 軽量化: MAM excels at creating lightweight yet strong components by incorporating internal lattice structures. This is a game-changer for industries like aerospace and automotive, where weight reduction translates to improved fuel efficiency and performance.
- マス・カスタマイゼーション: MAM’s ability to produce complex geometries on-demand makes it ideal for mass customization. Imagine creating personalized medical implants or customized components for niche applications – the possibilities are endless.
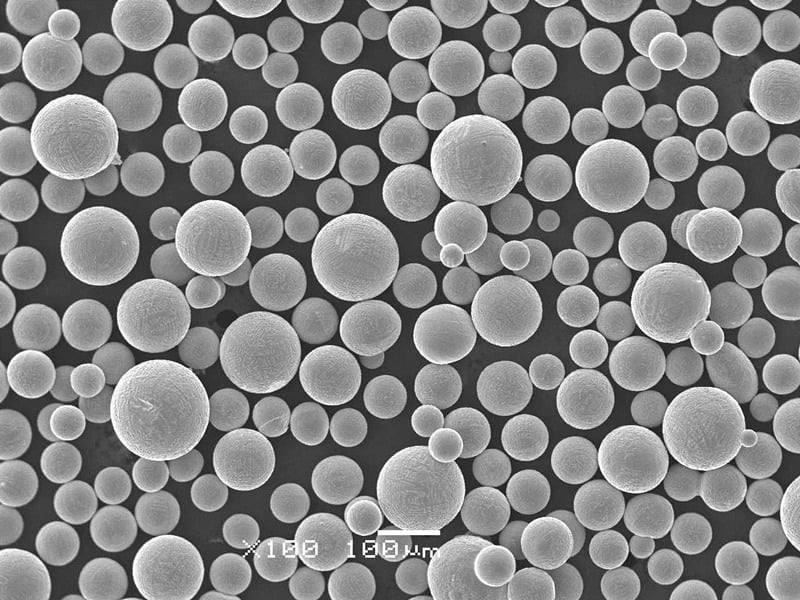
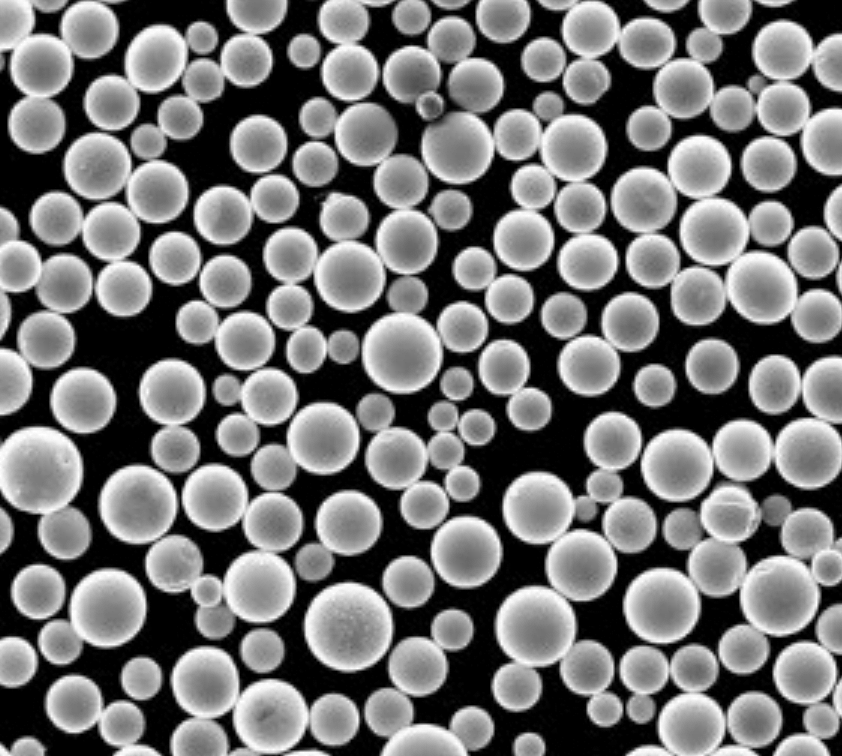
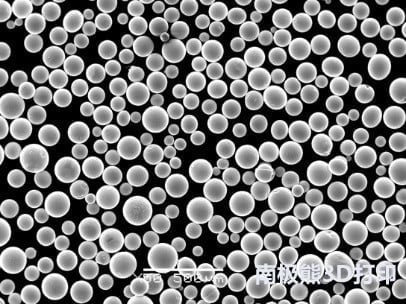
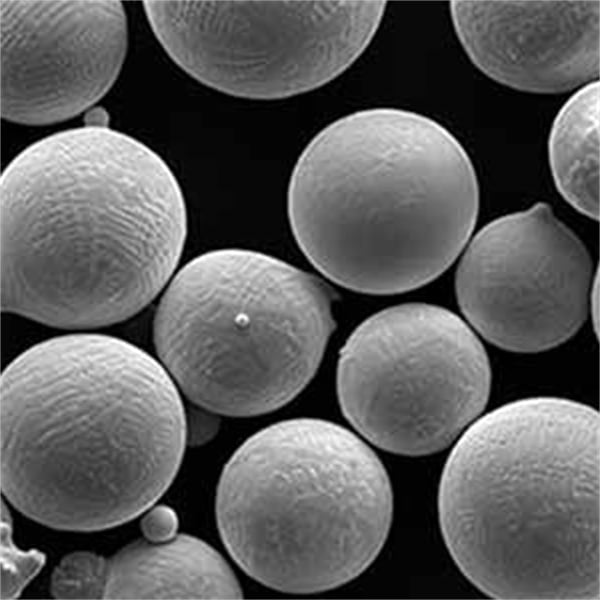
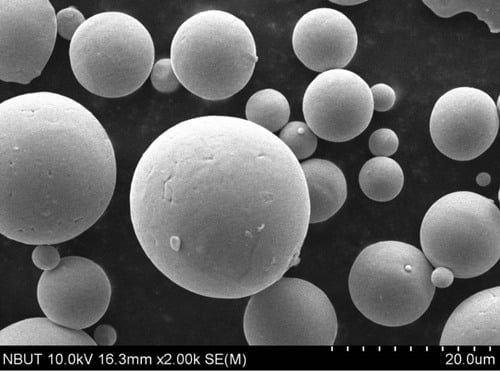
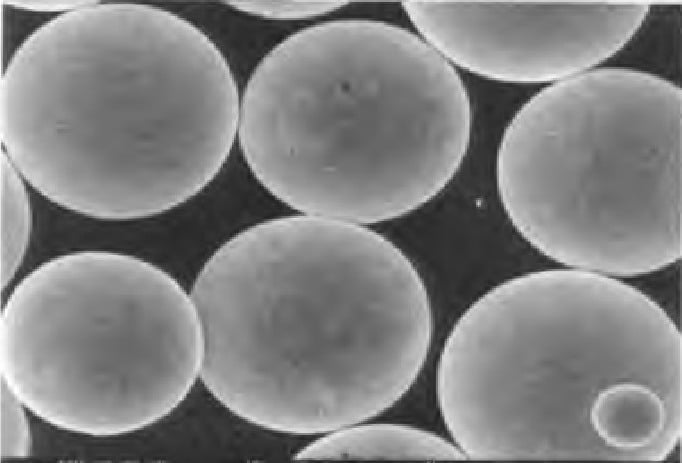
Applications of Metal Additive Manufacturing (MAM)
The versatility of MAM is truly remarkable. Here’s a glimpse into some of the industries where MAM is making significant waves:
- 航空宇宙: The ability to create lightweight, high-strength components like brackets, engine parts, and heat exchangers is propelling MAM’s adoption in the aerospace industry.
- 自動車: From lightweight race car components to intricate fuel injectors, MAM is helping automakers push the boundaries of performance and efficiency.
- 医療と歯科 Custom-made prosthetics, dental implants, and surgical instruments crafted with MAM are revolutionizing healthcare by offering personalized solutions and improved patient outcomes.
- 消費財: From customized jewelry and sporting equipment to complex watch components, MAM is making its mark in the consumer goods sector, enabling the creation of unique and innovative products.
Challenges and Considerations in Metal Additive Manufacturing (MAM)
While MAM offers a treasure trove of benefits, it’s important to acknowledge some of the challenges associated with this technology:
- コストだ: High upfront costs for MAM equipment and materials can be a barrier for entry, particularly for smaller companies.
- 後処理: Removing support structures and achieving desired surface finishes can add time and complexity to the MAM process.
- 材料の制限: While the range of materials compatible with MAM is expanding, it doesn’t encompass all the alloys traditionally used in metalworking.
- デザインの専門家: Unlocking the full potential of MAM requires specialized design skills and an understanding of the technology’s capabilities and limitations.
The Future of Metal Additive Manufacturing (MAM)
The future of MAM is brimming with exciting possibilities. Here are some key trends to watch:
- Advancements in Material Science: Researchers are constantly developing new metal alloys specifically optimized for MAM, pushing the boundaries of strength, weight, and printability.
- マルチマテリアル印刷: The ability to combine different metals or even metals with other materials within a single build opens doors to creating components with unique properties tailored to specific applications.
- Increased Automation: Automation of the MAM process, including powder handling, support structure removal, and post-processing, will further streamline production and reduce costs.
- Integration with AI: Artificial intelligence (AI) has the potential to revolutionize MAM by optimizing build parameters, predicting potential defects, and personalizing the manufacturing process for each part.
- Standardization and Certification: As MAM adoption grows, establishing industry-wide standards and certifications for materials, processes, and parts will be crucial for ensuring quality and promoting wider acceptance.
The Bottom Line: MAM – A Transformative Technology with a Bright Future
Metal Additive Manufacturing (MAM) is more than just a sophisticated 3D printing technology; it’s a transformative force reshaping the metalworking landscape. From unlocking design freedom to promoting sustainability and accelerating innovation, MAM offers a compelling value proposition across diverse industries. While challenges remain, advancements in materials, automation, and integration with AI promise to address these hurdles and pave the way for even wider adoption. As MAM continues to evolve, one thing is certain: the future of metalworking is undoubtedly intertwined with the magic of 3D printing.
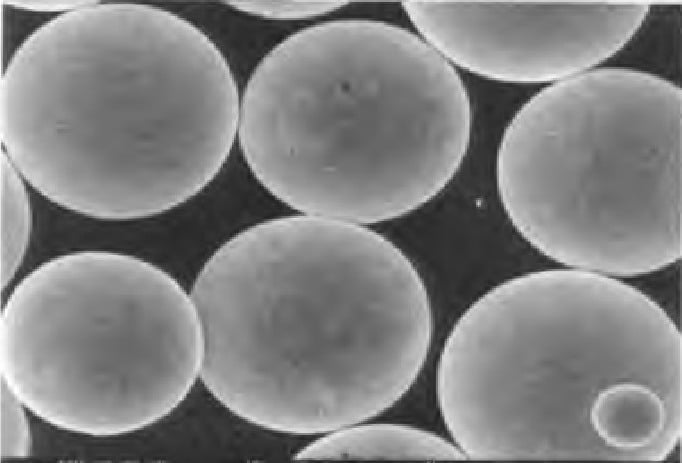
FAQ
Here’s a breakdown of some frequently asked questions about MAM, presented in a clear and concise table format for easy understanding:
質問 | 回答 |
---|---|
What are the different types of MAM technologies? | There are several MAM techniques, with the most common being Powder Bed Fusion (PBF) and Directed Energy Deposition (DED). PBF uses a laser to melt metal powder in a bed, layer by layer, while DED melts metal wire or powder directly onto a build plate. |
What materials can be used in MAM? | The range of materials compatible with MAM is constantly expanding. Common materials include titanium alloys, stainless steel, aluminum alloys, and nickel alloys. |
How strong are metal parts made with MAM? | MAM parts can be as strong, or even stronger, than traditionally manufactured components. The strength depends on the chosen material, the MAM process used, and the post-processing techniques employed. |
What are the surface finish options for MAM parts? | MAM parts can be achieved in a variety of surface finishes, ranging from a rough as-printed state to a smooth, polished finish. The desired finish determines the post-processing techniques required. |
Is MAM suitable for mass production? | While MAM excels in prototyping and low-volume production, it’s still evolving for high-volume applications. However, advancements in speed and automation are making MAM increasingly attractive for mass production scenarios. |
In Conclusion
Metal Additive Manufacturing (MAM) offers a glimpse into a future where metalworking transcends traditional limitations. With its ability to create complex geometries, reduce waste, and accelerate innovation, MAM is poised to revolutionize industries from aerospace to medicine. As the technology continues to mature and challenges are addressed, MAM’s potential to transform metalworking seems limitless. This captivating technology is more than just a manufacturing process; it’s a gateway to a world of boundless possibilities.
3DP mETALについて
製品カテゴリー
お問い合わせはこちら
何かご質問はありますか?今すぐメッセージを送信してください。あなたのメッセージを受信後、全チームで検討させていただきます。