Imagine holding the power to turn a blob of molten metal into a million tiny, perfectly round particles. That’s the magic of 金属粉末噴霧装置, a technological marvel that underpins countless industries. From the lightweight components in your car to the life-saving implants in your body, metal powders play a crucial role in shaping our world. But how exactly does this equipment work, and what are the different methods used to create these microscopic marvels? Buckle up, because we’re diving deep into the fascinating world of metal powder atomization!
The Speed Demon of Powder Production
ガスアトマイゼーション is a widely used method for producing spherical powders with a narrow particle size distribution. Here’s how it works:
- 金属を溶かす: The metal feedstock is first melted in a furnace, typically an induction furnace that uses electromagnetic fields to heat the metal efficiently and minimize contamination.
- The Big Squeeze: The molten metal is then forced through a tiny nozzle at high pressure. Imagine squeezing toothpaste out of a tube, but with molten metal and a whole lot more force!
- Gaseous Disruption: A high-velocity gas stream, often inert gases like nitrogen or argon, disrupts the molten metal stream as it exits the nozzle. This forceful breakup creates a fine mist of metal droplets.
- Solidification on the Fly: As the tiny droplets travel through the chamber, they rapidly cool and solidify into spherical metal powder particles.
- Separation and Collection: The cooled powder particles are separated from the gas stream using cyclones or filters, and voila! You have a batch of pristine metal powder ready for further processing.
Think of gas atomization like a high-tech metal rain shower. The molten metal is the rain, the nozzle is the cloudhead, and the gas stream is the wind that breaks the raindrops into smaller, uniform droplets. This method excels at producing high-quality powders for demanding applications like additive manufacturing (3D printing) and high-performance components.
ガスアトマイズの利点
- Spherical Powders: Gas atomization produces highly spherical powders with excellent flowability, making them ideal for 3D printing and other powder-bed fusion processes.
- Narrow Size Distribution: The controlled gas stream allows for precise control over the particle size distribution, ensuring consistent properties in the final product.
- 高純度: The use of inert gases minimizes oxidation and contamination during the process, leading to high-purity powders.
Disadvantages of Gas Atomization:
- High Energy Consumption: The high-pressure gas and molten metal processing require significant energy input, making it a relatively expensive method.
- Limited Production Rates: Compared to other methods, gas atomization typically has lower production rates, making it less suitable for high-volume applications.
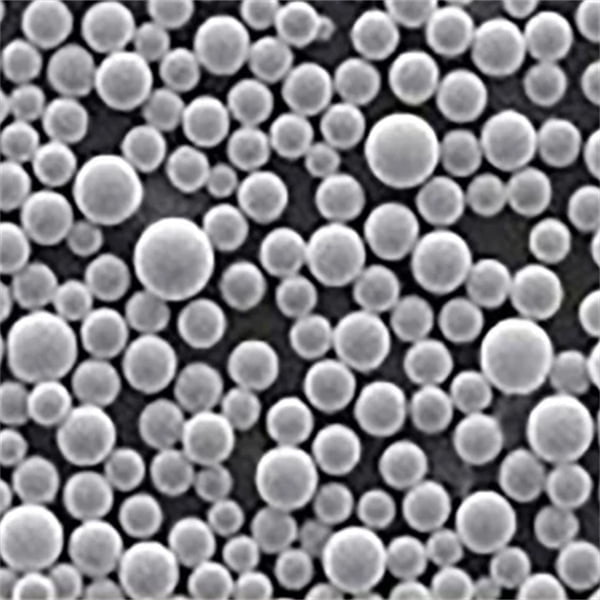
The Spinning Specialist for Diverse Powders
Centrifugal atomization offers a different approach, using centrifugal force to create metal powders. Here’s the breakdown:
- Melted Metal, Again: Similar to gas atomization, the metal feedstock is first melted in a furnace.
- Spinning Into Action: The molten metal is then fed into a rapidly spinning disc or mold. Imagine a potter’s wheel spinning at breakneck speed, but instead of clay, it’s flinging molten metal!
- Centrifugal Force Takes Over: As the disc spins at high speed, the centrifugal force throws the molten metal outwards towards the periphery.
- Breaking Up is Hard to Do (But Rewarding): The molten metal breaks up into fine droplets due to the centrifugal force and surface tension. These droplets then solidify into metal powder particles as they cool in the surrounding atmosphere.
- Collecting the Microscopic Bounty: The metal powder particles are collected from the chamber using filters or cyclones.
Think of centrifugal atomization as a high-speed metal splatter party. The spinning disc acts like a centrifuge, flinging the molten metal outwards where it breaks up into a shower of tiny particles. This method is particularly useful for producing powders with a broader particle size distribution, making it suitable for applications like metal injection molding (MIM) and thermal spraying.
Advantages of Centrifugal Atomization:
- Versatile Particle Sizes: Centrifugal atomization allows for a wider range of particle size distributions compared to gas atomization, offering greater flexibility for different applications.
- Relatively Lower Energy Consumption: Compared to gas atomization, this method uses less energy to create the atomizing force, making it potentially more cost-effective for certain applications.
- Higher Production Rates: Centrifugal atomization can achieve higher production rates than gas atomization, making it more suitable for high-volume powder production.
Disadvantages of Centrifugal Atomization:
- Less Spherical Powders: The powders produced by centrifugal atomization tend to be less spherical compared to gas atomization. This can affect flowability and packing density, which may be a drawback for some applications.
- 内部欠陥の可能性: Due to the rapid solidification during centrifugal atomization, there’s a higher chance of internal defects like porosity in the powder particles. This can impact the mechanical properties of the final product.
Choosing Between Gas and Centrifugal Atomization:
The choice between gas and centrifugal atomization depends on several factors, including:
- Desired Powder Properties: If highly spherical powders with a narrow size distribution are crucial, gas atomization is the preferred choice. For broader size distributions, centrifugal atomization might be suitable.
- 応募資格 The specific application will dictate the powder properties needed. For instance, 3D printing often demands highly spherical powders, while thermal spraying might have more flexibility in particle size requirements.
- 生産量: If high-volume production is a priority, centrifugal atomization might be a more cost-effective option due to its higher production rates.
Beyond Gas and Centrifugal: Exploring Other Atomization Techniques
While gas and centrifugal atomization are the most common methods, there are other techniques used for specific applications:
- 水の霧化: This method uses a high-pressure water jet to break up the molten metal stream. It’s cost-effective but produces less spherical powders with a broader size distribution, making it suitable for less demanding applications.
- Electrolytic Atomization: This technique utilizes an electrolytic cell to break down the metal feedstock into particles. It offers high purity and control over particle size but is limited in production capacity and metal types.
- Rapid Solidification Techniques: Techniques like melt spinning and laser atomization involve rapid solidification of the molten metal, leading to unique powder properties like amorphous structures or very fine particle sizes. These methods are used for specialized applications in research and development.
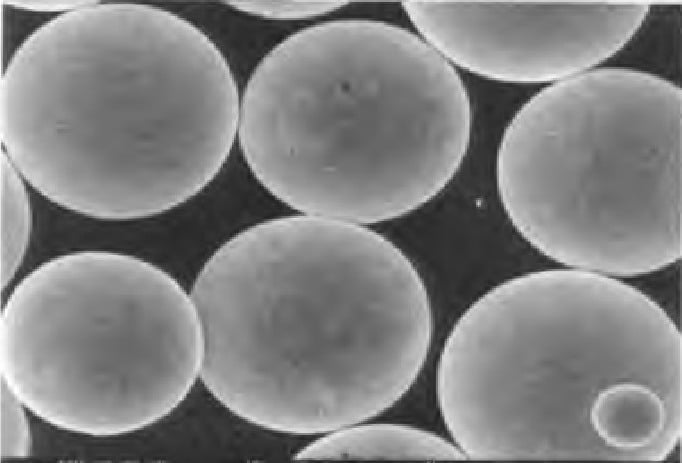
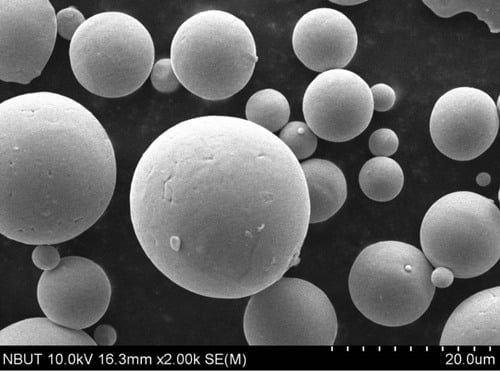
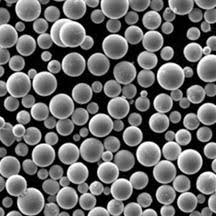
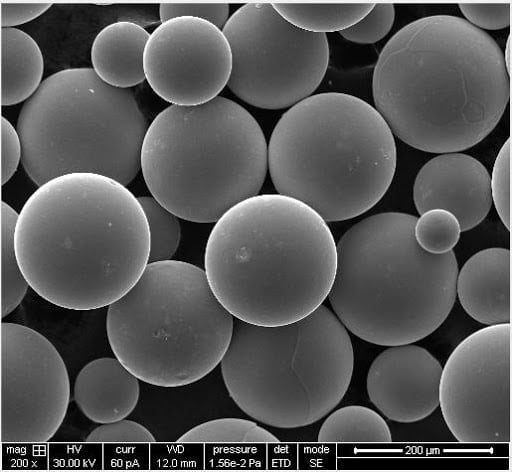
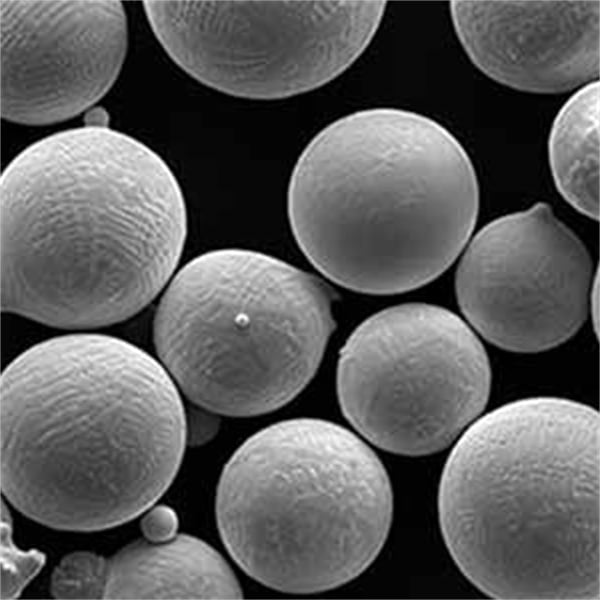
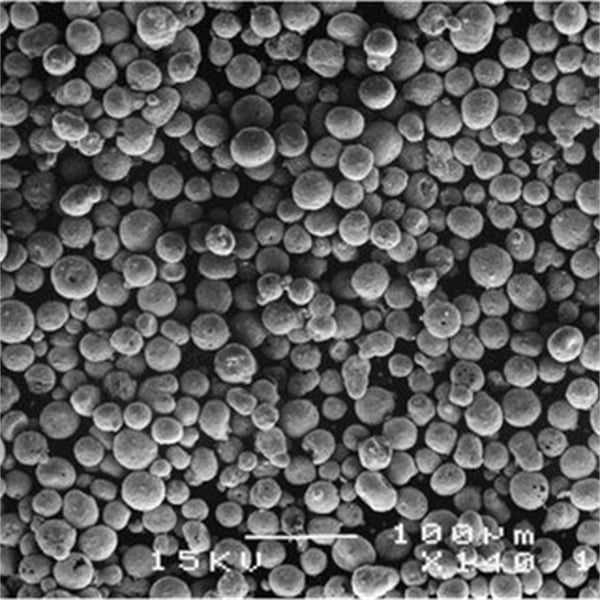
Key Components of Metal Powder Atomization Equipment
Regardless of the specific atomization method, some key components are common to most equipment setups:
- Melting Furnace: This unit, typically an induction furnace, heats the metal feedstock to its molten state.
- Atomization Chamber: This enclosed chamber houses the atomization nozzle, disc, or other atomizing element.
- Atomizing Medium: The gas stream (inert gas for gas atomization) or the spinning disc (for centrifugal atomization) provides the force to break up the molten metal.
- Cooling System: A cooling system rapidly cools the metal droplets as they travel through the chamber, promoting solidification into powder particles.
- Separation and Collection System: Cyclones or filters separate the metal powder particles from the gas stream or surrounding atmosphere.
- Control System: A control system monitors and regulates various parameters like furnace temperature, gas flow rate, and disc speed for optimal powder production.
Process Parameters of Metal Powder Atomization Equipment
The properties of the final metal powder are highly dependent on the process parameters used in the atomization equipment. Some critical parameters include:
- 溶融温度: The temperature at which the metal is melted significantly impacts the viscosity and flow properties of the molten metal, ultimately affecting the size and morphology of the powder particles.
- Atomization Pressure/Speed: In gas atomization, the gas pressure and in centrifugal atomization, the disc speed, play a crucial role in the force applied to break up the molten metal stream. Higher pressure/speed leads to finer powder particles.
- 冷却速度: The rate at which the metal droplets cool down determines the microstructure and properties of the powder particles. Rapid cooling can lead to the formation of non-equilibrium phases or even amorphous structures.
The application for the metal powder will dictate the optimal process parameters. For instance, 3D printing might require finer powders with a narrow size distribution, achieved through specific settings for melt temperature, atomization pressure, and cooling rate.
の応用 Metal Powder Atomization Equipment
Metal powders produced through atomization equipment find applications in a vast array of industries. Here are some key examples:
- アディティブ・マニュファクチャリング(3Dプリンティング): Metal powders are a cornerstone of 3D printing technologies like laser beam melting and electron beam melting. The spherical shape and narrow size distribution of gas-atomized powders are particularly well-suited for these processes, enabling the creation of complex, near-net-shape metal components.
- 金属射出成形(MIM): Centrifugal atomization powders with a broader size distribution are often used in MIM. MIM allows for the mass production of complex metal parts with intricate shapes, leveraging the excellent flowability of metal powders.
- 溶射: Metal powders are used in thermal spraying processes like plasma spraying and high-velocity oxy-fuel (HVOF) use metal powders to create wear-resistant coatings, corrosion-resistant layers, and functionally graded materials on various substrates. The choice of powder properties, including size, shape, and composition, is crucial for achieving the desired coating characteristics.
- Aerospace and Defense: Metal powder atomization plays a vital role in aerospace and defense applications. The ability to create lightweight, high-strength metal components through 3D printing and other powder-based technologies is revolutionizing aircraft and spacecraft design. Additionally, thermal spraying with metal powders is used to enhance the performance and lifespan of critical components in these demanding environments.
- 自動車産業: The automotive industry is increasingly utilizing metal powders for components like engine parts, gearboxes, and lightweight body structures. Metal 3D printing allows for the creation of complex, high-performance components with reduced weight, leading to improved fuel efficiency and overall vehicle performance.
- 医療用インプラント Metal powders are used to manufacture biocompatible implants like hip replacements and knee joints. The ability to tailor the powder properties allows for the creation of implants with excellent biocompatibility and mechanical properties that closely mimic natural bone tissue.
- Electronics and Consumer Goods: Metal powders are finding applications in electronics for components like heat sinks and EMI shielding. Additionally, metal 3D printing is being explored for the creation of customized consumer goods like jewelry and sporting equipment.
The Future of Metal Powder Atomization Equipment
The future of metal powder atomization equipment is brimming with exciting possibilities. Here are some key trends to watch:
- Development of Novel Atomization Techniques: Researchers are exploring new atomization techniques like ultrasonic and roto-molding atomization that offer potential advantages in terms of powder morphology, size distribution, and production efficiency.
- Advanced Process Control Systems: Continuous advancements in automation and sensor technology are leading to the development of more sophisticated process control systems for atomization equipment. These systems will enable real-time monitoring and optimization of process parameters, ensuring consistent and high-quality powder production.
- 持続可能性に焦点を当てる: There’s a growing emphasis on developing sustainable practices in metal powder atomization. This includes exploring ways to reduce energy consumption, minimize waste generation, and utilize recycled materials in the powder production process.
- Integration with Additive Manufacturing: As metal 3D printing continues to evolve, there will be a closer integration between atomization equipment and 3D printing systems. This could involve the development of in-situ atomization techniques where metal powders are produced on-demand for immediate use in 3D printing processes.
In conclusion, metal powder atomization equipment plays a transformative role in shaping our world. From the intricate components in our cars to the life-saving implants in our bodies, metal powders are revolutionizing countless industries. As technology continues to advance, we can expect even more innovative applications and advancements in 金属粉末噴霧装置, pushing the boundaries of what’s possible in the world of materials science and manufacturing.
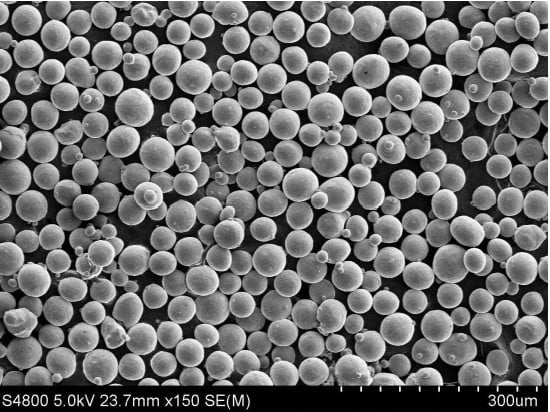
FAQ
質問 | 回答 |
---|---|
What are the different types of metal powder atomization equipment? | The two most common types are gas atomization and centrifugal atomization. Other methods include water atomization, electrolytic atomization, and rapid solidification techniques. |
What factors influence the choice of atomization method? | The desired powder properties (size, shape, distribution), application requirements, and production volume are key factors. |
What are the key components of metal powder atomization equipment? | Melting furnace, atomization chamber, atomizing medium, cooling system, separation and collection system, and control system. |
What are some critical process parameters in metal powder atomization? | Melt temperature, atomization pressure/speed, and cooling rate significantly impact the final powder properties. |
What are the main applications of metal powders produced by atomization? | Additive manufacturing (3D printing), metal injection molding (MIM), thermal spraying, aerospace and defense, automotive industry, medical implants, and electronics are some key applications. |
What are some future trends in metal powder atomization equipment? | Development of novel atomization techniques, advanced process control systems, focus on sustainability, and integration with additive manufacturing are some exciting trends to watch. |
3DP mETALについて
製品カテゴリー
お問い合わせはこちら
何かご質問はありますか?今すぐメッセージを送信してください。あなたのメッセージを受信後、全チームで検討させていただきます。