For decades, the aviation industry has relied on traditional manufacturing techniques to craft the marvels of modern flight. However, a revolution is brewing, fueled by the innovation of metal powder. Imagine crafting intricate aircraft components with unparalleled precision and design freedom, all while reducing weight and boosting performance. This is the transformative potential of metal powder in aviation.
の特徴 Metal Powder for Aviation
Not all metal powders are created equal. For the demanding world of aviation, metal powders need specific characteristics to ensure the safety and integrity of critical aircraft parts. Here’s a closer look at the key properties:
- 高純度: Aviation components endure extreme stresses and environmental conditions. Metal powders for these applications require exceptionally high purity levels, minimizing defects and maximizing structural integrity.
- タイトな粒度分布: Particle size plays a crucial role in the final properties of a metal powder component. A narrow particle size distribution ensures consistent material behavior and minimizes internal stresses during the manufacturing process.
- 真球度: Ideally, metal powder particles should be as close to perfect spheres as possible. This spherical shape enhances flowability, packing density, and ultimately, the mechanical properties of the final component.
- 流動性: Efficient and even distribution of the metal powder during the manufacturing process is critical. Powders with good flowability enable smooth production and minimize inconsistencies in the final product.
素材の選択:
The choice of 航空用金属粉 applications hinges on the specific component’s function and operational demands. Here are some of the most widely used metal powders and their defining characteristics:
メタルパウダー | 主要物件 | 一般的な用途 |
---|---|---|
Titanium Alloys (Ti-6Al-4V) | High strength-to-weight ratio, excellent corrosion resistance, biocompatibility | Airframe components, Landing gear parts, Engine housings |
Nickel Superalloys (Inconel 718) | Exceptional high-temperature strength, good oxidation resistance | Turbine blades, Exhaust nozzles, Afterburner components |
Aluminum Alloys (AlSi10Mg) | Lightweight, good strength and ductility | Interior components, Fuselage panels, Non-critical structural parts |
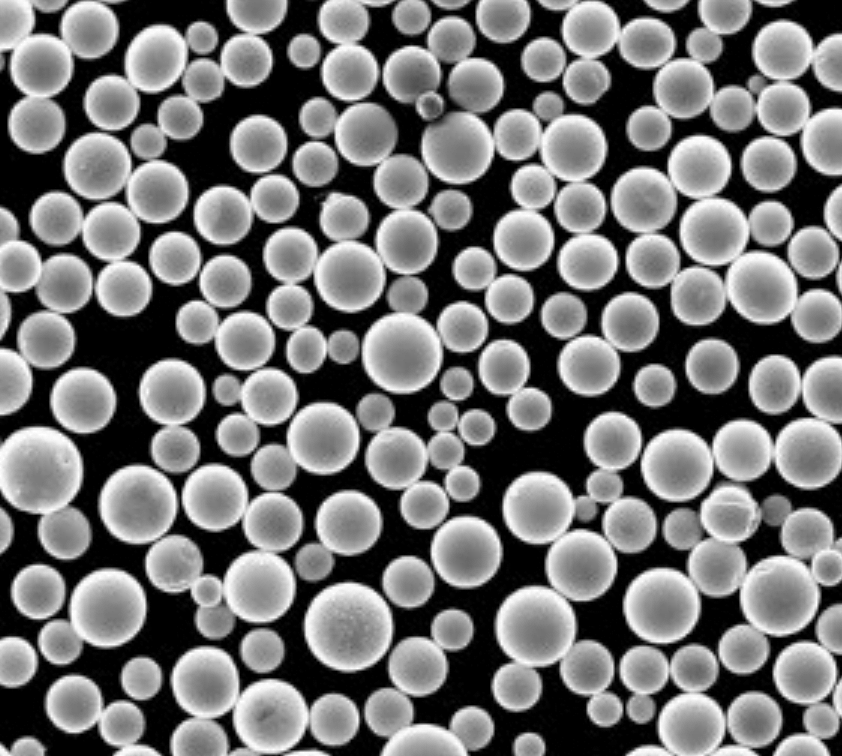
Preparation Methods of Metal Powder for Aviation
Several methods exist for producing metal powder with the exacting characteristics required for aviation applications. Here’s a breakdown of the most common techniques:
- ガス霧化: Molten metal is injected into a high-velocity gas stream, causing it to break up into fine droplets that rapidly solidify into spherical powder particles. This method offers excellent control over particle size and morphology.
- 水の霧化: Similar to gas atomization, but the molten metal is broken up into droplets using a high-pressure water jet. This technique is generally more cost-effective but may result in less spherical particles compared to gas atomization.
- Plasma Rotating Electrode Process (PREP): A high-temperature plasma torch melts a rotating electrode, generating a fine metal mist that rapidly cools and solidifies into powder. PREP is particularly well-suited for producing high-purity and reactive metal powders.
The Application of Metal Additive Manufacturing (AM) with Metal Powder
Metal Additive Manufacturing (AM), also known as 3D printing, has emerged as a game-changer in the aviation industry. This technology utilizes computer-aided design (CAD) data to build complex, three-dimensional structures layer-by-layer using metal powder. Here’s how metal AM with metal powder is revolutionizing aircraft manufacturing:
- 軽量化: Metal AM allows for the creation of intricate, lightweight structures with internal support features that would be impossible with traditional techniques. This translates to significant weight reduction in aircraft components, leading to improved fuel efficiency and increased range.
- デザインの自由: Metal AM eliminates the limitations of traditional machining, enabling the creation of complex geometries and internal channels. This design freedom allows for optimized components with improved functionality and performance.
- Part Consolidation: Metal AM can consolidate multiple parts into a single, lighter component. This reduces complexity, improves assembly efficiency, and minimizes potential failure points.
- ラピッドプロトタイピング: Metal AM allows for the rapid creation of functional prototypes, accelerating the design and development cycle for new aircraft components.
Case Study: Metal AM Transforming Turbine Blades
Turbine blades are some of the most critical and highly stressed components in an aircraft engine. Traditionally, they were manufactured from complex nickel superalloy castings requiring extensive machining. Metal AM offers a compelling alternative. By utilizing metal powder bed fusion (MPBF), manufacturers can create intricate turbine blades with internal cooling channels that enhance efficiency and reduce weight. This not only improves engine performance but also allows for the design of lighter, more fuel-efficient aircraft.
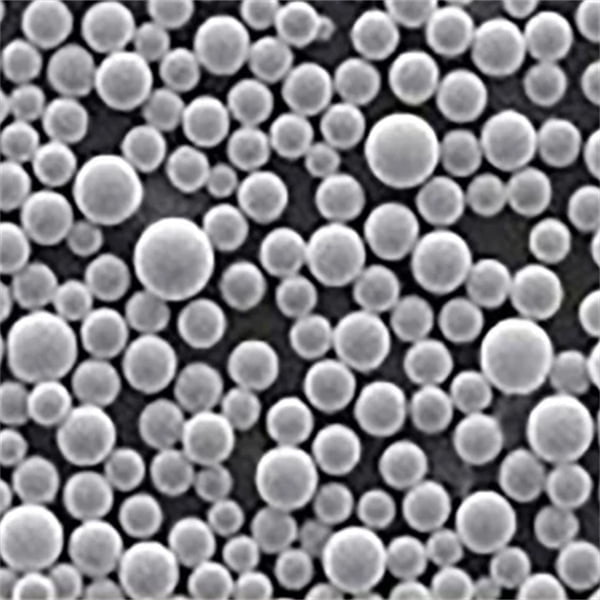
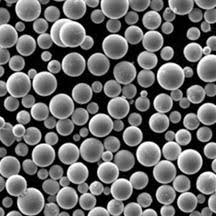
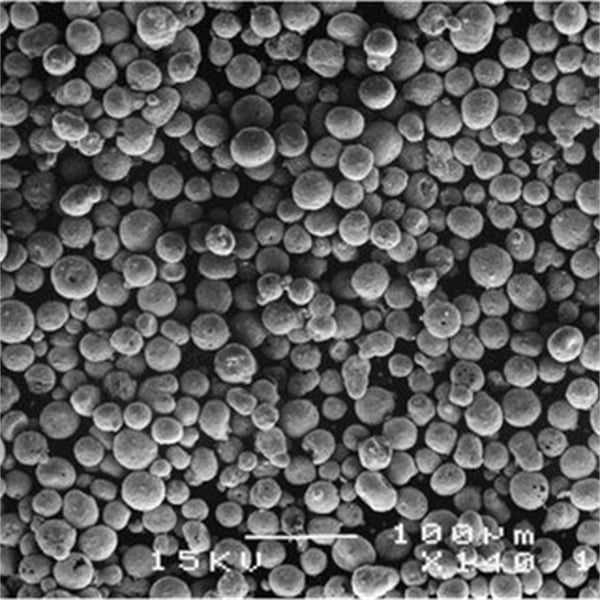
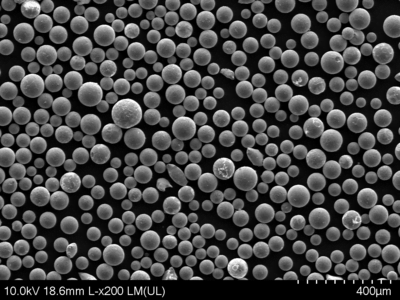
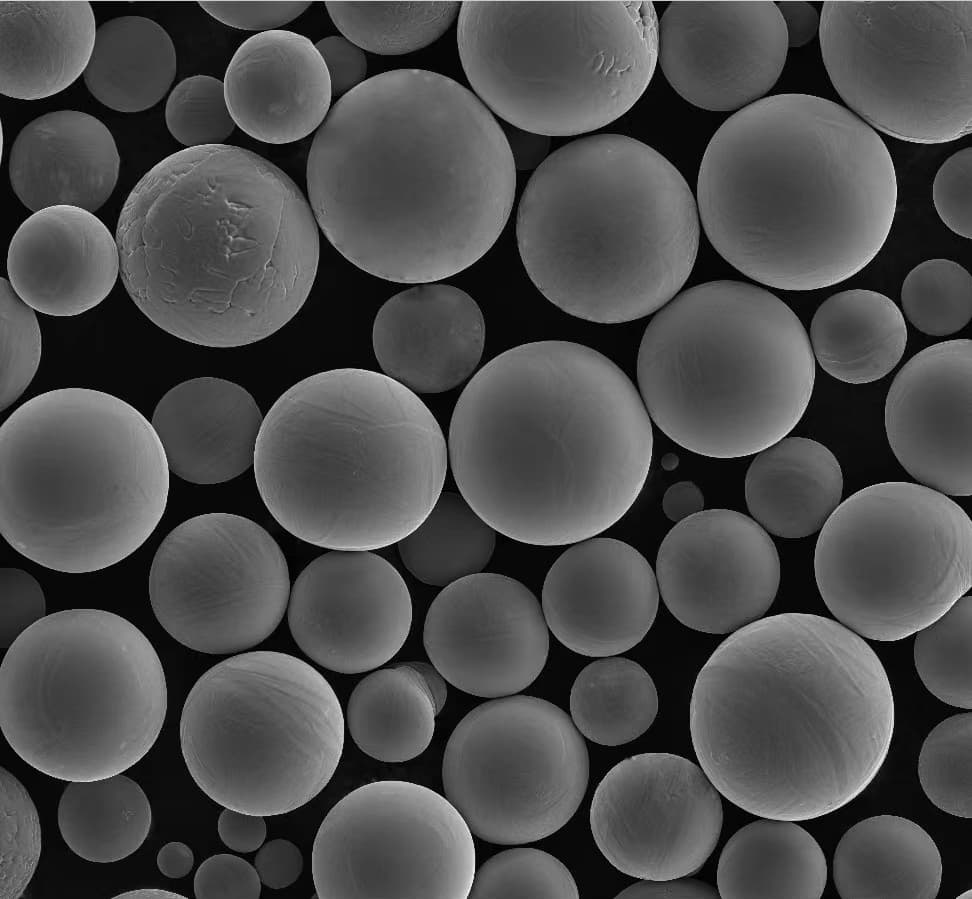
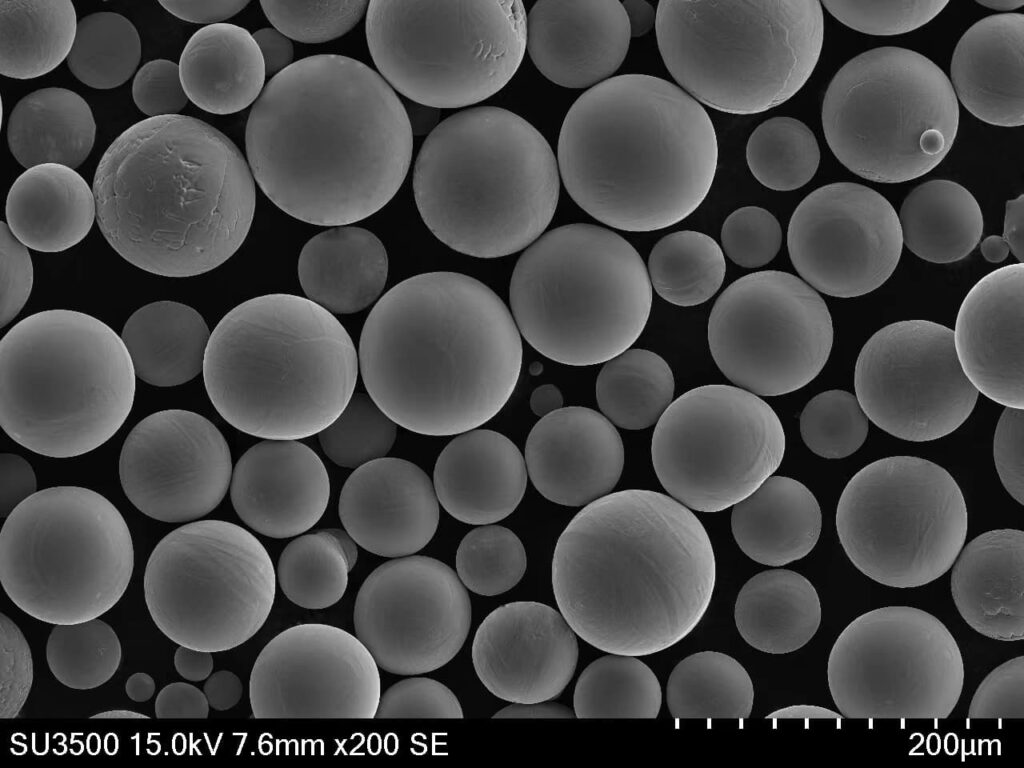
Advantages and Considerations of Metal Powder in Aviation
While metal powder offers tremendous potential for the aviation industry, there are also considerations to address:
メリット
- Reduced Weight: As highlighted earlier, metal powder’s ability to facilitate lightweight designs is a major advantage. Every pound shed from an aircraft translates to improved fuel efficiency, increased range, and potentially, higher payload capacity. In the fiercely competitive commercial airline market, even a minor weight reduction can translate to significant cost savings over the lifetime of an aircraft.
- パフォーマンスの向上: Metal AM with metal powder enables the creation of components with optimized internal features. For instance, intricate cooling channels in turbine blades or lightweight, high-strength structures for landing gear can significantly improve the overall performance of an aircraft.
- 設計の柔軟性: Unlike traditional manufacturing techniques that are limited by tooling and subtractive processes, metal AM offers unparalleled design freedom. Complex geometries, internal lattices, and weight-saving features can all be incorporated into designs, pushing the boundaries of what’s possible.
- 廃棄物の削減: Metal AM with metal powder is a more sustainable manufacturing method compared to traditional techniques. There’s significantly less material waste as unused powder can often be recycled and reused. This translates to a smaller environmental footprint for the aviation industry.
検討する:
- コストだ: Currently, metal AM with metal powder can be a more expensive manufacturing process compared to traditional methods, particularly for high-volume production. The cost of the metal powder itself, coupled with the relatively slow build times of AM machines, contributes to this higher cost.
- Part Qualification: Strict regulations govern the airworthiness of aircraft components. Metal AM parts need to undergo rigorous testing and qualification procedures to ensure they meet the demanding safety standards of the aviation industry. This adds time and complexity to the adoption of metal AM for critical components.
- 表面仕上げ: Metal AM components may have a rougher surface finish compared to traditionally machined parts. While post-processing techniques can improve surface quality, it adds another step to the manufacturing process.
- パウダーハンドリング: Metal powders, especially those used for high-performance applications, can be fine and susceptible to moisture absorption. Proper handling and storage procedures are crucial to ensure the quality and consistency of the powder.
The Future of Metal Powder in Aviation
The future of metal powder in aviation is undeniably bright. As technology advances, the cost of metal powder production is expected to decrease, making metal AM a more cost-competitive manufacturing option. Furthermore, ongoing research and development efforts are focused on improving build speeds, powder characteristics, and qualification processes, paving the way for wider adoption of metal AM in the aviation industry.
Potential Applications:
Beyond the current applications, metal powder holds promise for a wider range of uses in aviation, including:
- Additive Manufacturing of entire aircraft fuselages: While currently a futuristic notion, advancements in metal AM technology and increased build volumes could one day make the creation of entire aircraft fuselages through metal AM a reality. This would revolutionize aircraft design and manufacturing.
- Repair of critical components: Metal AM has the potential to revolutionize aircraft maintenance. Damaged components could be repaired using metal powder, potentially extending their lifespan and reducing costs associated with replacement parts.
- Personalization of aircraft components: Metal AM’s design freedom could enable the creation of customized aircraft components optimized for specific applications or airline requirements.
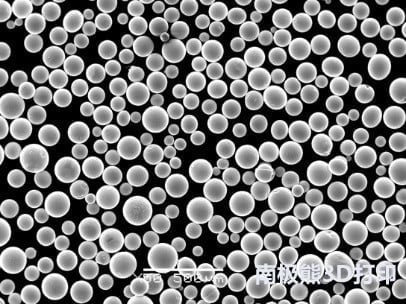
FAQ
Q: What are the different types of metal powder used in aviation?
A: Several metal powders are used in aviation, each with specific properties suited for various applications. Here are some of the most common:
- チタン合金(Ti-6Al-4V): Renowned for their high strength-to-weight ratio, excellent corrosion resistance, and biocompatibility, these powders are ideal for airframe components, landing gear parts, and engine housings.
- Nickel Superalloys (Inconel 718): These powders excel in high-temperature environments and offer good oxidation resistance, making them prime choices for turbine blades, exhaust nozzles,
- Aluminum Alloys (AlSi10Mg): Lightweight and boasting good strength and ductility, these powders are often used for interior components, fuselage panels, and non-critical structural parts.
Q: What are the advantages and disadvantages of metal AM compared to traditional manufacturing techniques?
A: Here’s a table summarizing the key advantages and disadvantages of metal AM with metal powder against traditional manufacturing techniques like machining and casting:
特徴 | Metal Additive Manufacturing (AM) | Traditional Techniques |
---|---|---|
デザインの自由 | ハイ | Limited by tooling and subtractive processes |
重量 | Potential for significant weight reduction | Weight reduction limited by material properties and design constraints |
複雑さ | Can create highly complex geometries | Limited in creating complex internal features |
Waste | Less material waste | Can generate significant scrap material |
利用料 | Currently more expensive (especially for high-volume production) | Established and often lower cost |
リードタイム | Can be slower than traditional methods | Lead times can be well-established |
Part Qualification | Requires rigorous testing and qualification for airworthiness | Qualification processes are generally well-defined |
Q: What are some of the environmental benefits of using metal powder in aviation?
A: Metal AM with metal powder offers several environmental advantages over traditional manufacturing techniques:
- 廃棄物の削減: As mentioned earlier, metal AM is a more sustainable process due to minimal material waste. Unused powder can often be recycled and reused, minimizing environmental impact.
- Lighter Aircraft: The weight reduction potential of metal powder translates to improved fuel efficiency for aircraft. This reduced fuel consumption directly lowers carbon emissions, contributing to a greener aviation industry.
- Optimized Designs: Metal AM allows for the creation of components with optimized internal features, potentially leading to improved engine performance and reduced fuel burn.
Q: What are the safety considerations for using metal powder in aviation?
A: The safety of aircraft components is paramount. Metal powder used in aviation needs to meet stringent quality standards to ensure the structural integrity and performance of the final parts. Here are some key safety considerations:
- Powder Purity: High purity levels are essential to minimize defects and maximize the structural integrity of components.
- Powder Characterization: Particle size distribution, flowability, and other powder characteristics significantly influence the final properties of the AM part. Consistent and well-characterized powder is crucial for safety.
- プロセス制御: Metal AM processes need to be precisely controlled to ensure consistent quality and repeatability in the production of critical aircraft components.
- Part Qualification: As with any new manufacturing technology, metal AM parts undergo rigorous testing and qualification procedures to demonstrate they meet the demanding safety standards set by aviation regulatory bodies.
結論
Metal powder is revolutionizing the aviation industry, offering a path towards lighter, more efficient, and sustainable aircraft. While challenges remain in terms of cost, qualification, and broader adoption, the future of metal powder in aviation is soaring high. As technology advances and barriers are overcome, metal powder promises to transform the way we design, manufacture, and fly in the years to come.
3DP mETALについて
製品カテゴリー
お問い合わせはこちら
何かご質問はありますか?今すぐメッセージを送信してください。あなたのメッセージを受信後、全チームで検討させていただきます。