Imagine a material that can withstand the scorching inferno of a jet engine or the relentless bite of arctic pipelines. That’s the realm of ニッケル基超合金, a class of metallic marvels pushing the boundaries of strength and heat resistance. But what exactly are these super performers, and how do they achieve their extraordinary properties? Buckle up, because we’re diving deep into the fascinating world of nickel-based superalloys!
An Overview: The Allure of Nickel
At the heart of these superalloys lies, unsurprisingly, nickel. This versatile metal forms the foundation, typically constituting around 50-75% of the total composition. But nickel alone wouldn’t be enough. Picture a superhero needing a trusty sidekick – that’s where other elements come in. Strategic additions of chromium, cobalt, molybdenum, tungsten, and a sprinkle of others like niobium, tantalum, and aluminum, create a potent cocktail that unlocks the true potential of these alloys.
These alloying elements work in two main ways:
- Solid Solution Strengthening: Imagine tiny, invisible soldiers dispersed throughout the nickel matrix. These are the alloying elements, like chromium and molybdenum, that stiffen the material by making it harder for atoms to slide past each other, boosting strength at high temperatures.
- Precipitation Strengthening: Here’s where things get interesting. Certain elements, like aluminum and titanium, form microscopic particles within the nickel matrix when cooled down under controlled conditions. These particles, called gamma prime (γ’) precipitates, act like tiny roadblocks, hindering the movement of dislocations (defects in the atomic arrangement) and further enhancing the alloy’s strength, especially at elevated temperatures.
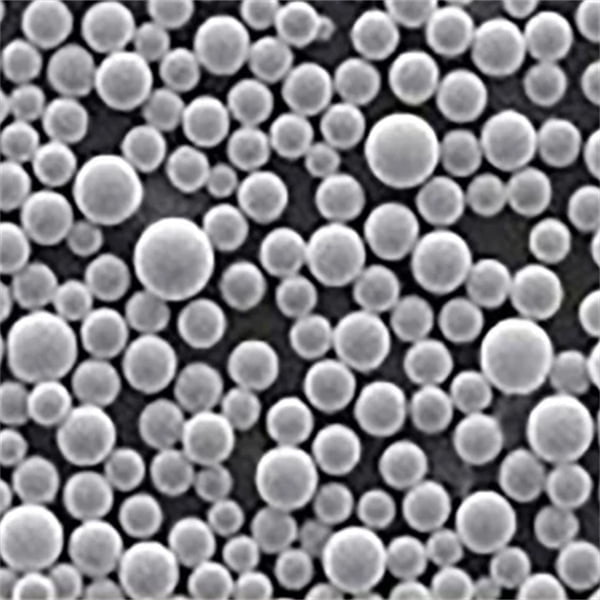
Key Properties of ニッケル基超合金
- Exceptional High-Temperature Strength: These alloys can retain their strength at temperatures exceeding 1000°C (1832°F) – a far cry from your average steel that starts to soften well below that mark. This makes them ideal for applications where heat is a constant adversary.
- Superior Oxidation Resistance: Hot environments often come with the threat of oxidation, where the material reacts with oxygen and weakens. Nickel-based superalloys are formulated to resist this degradation, thanks to elements like chromium that form a protective oxide layer on the surface.
- Creep Resistance: Imagine a material slowly deforming under constant stress at high temperatures – that’s creep. Nickel-based superalloys excel in resisting this creep, making them perfect for components that bear heavy loads for extended periods in hot environments.
- 耐食性: Many of these alloys offer good resistance to corrosion, especially against hot gases and chemicals encountered in demanding applications.
Unveiling Metal Powders for Additive Manufacturing
Now, let’s delve into the world of metal additive manufacturing (AM), where nickel-based superalloys are taking center stage. AM, also known as 3D printing, allows for the creation of complex shapes layer by layer using metal powders. This opens exciting possibilities for crafting intricate components for applications where traditional manufacturing methods might struggle. Here are some notable metal powder models for nickel-based superalloys, each catering to specific needs:
- AM Inconel 625: This workhorse powder offers a good balance of strength, oxidation resistance, and fabricability. It’s a popular choice for jet engine components, heat exchangers, and various industrial applications.
- AM Inconel 718: A step up in strength from Inconel 625, this powder excels in high-temperature environments and offers good corrosion resistance. It’s widely used in aerospace components, turbine blades, and demanding industrial applications.
- AM Rene 41: This powder boasts superior high-temperature strength and creep resistance, making it ideal for hot sections of jet engines and industrial gas turbines.
- AM Waspaloy: Offering a combination of strength, oxidation resistance, and good weldability, this powder is used in applications like turbine discs, combustor liners, and other aerospace components.
- AM Haynes 282: This powder shines in high-temperature environments with exceptional oxidation resistance, making it a prime choice for parts exposed to hot corrosive gases, like in chemical processing equipment and rocket engine components.
- AM CM247LC: This cobalt-chromium-based superalloy powder offers excellent creep resistance and high-temperature strength, targeting applications in advanced gas turbines and power generation.
- AM Atlas Copco AM 250: This powder is specifically designed for additive manufacturing, offering a good balance of strength, ductility, and printability for complex geometries used in demanding industrial applications.
- AM SLM Solutions SX Ni 600: This gas-atomized powder delivers high strength and good oxidation resistance, making it suitable for aerospace components, turbine blades, and demanding industrial applications. Compared to some other options, it might offer slightly lower creep resistance, but its printability makes it a good choice for intricate geometries.
- AM EOS NickelAlloy IN718: This powder, based on the popular Inconel 718 composition, is optimized for laser additive manufacturing. It offers excellent mechanical properties similar to wrought Inconel 718, making it a strong contender for high-performance applications in aerospace and demanding industrial sectors.
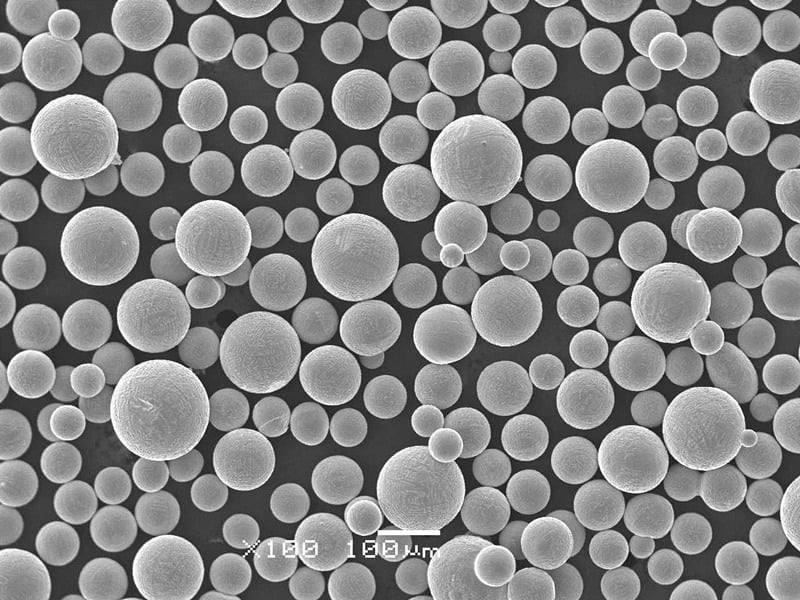
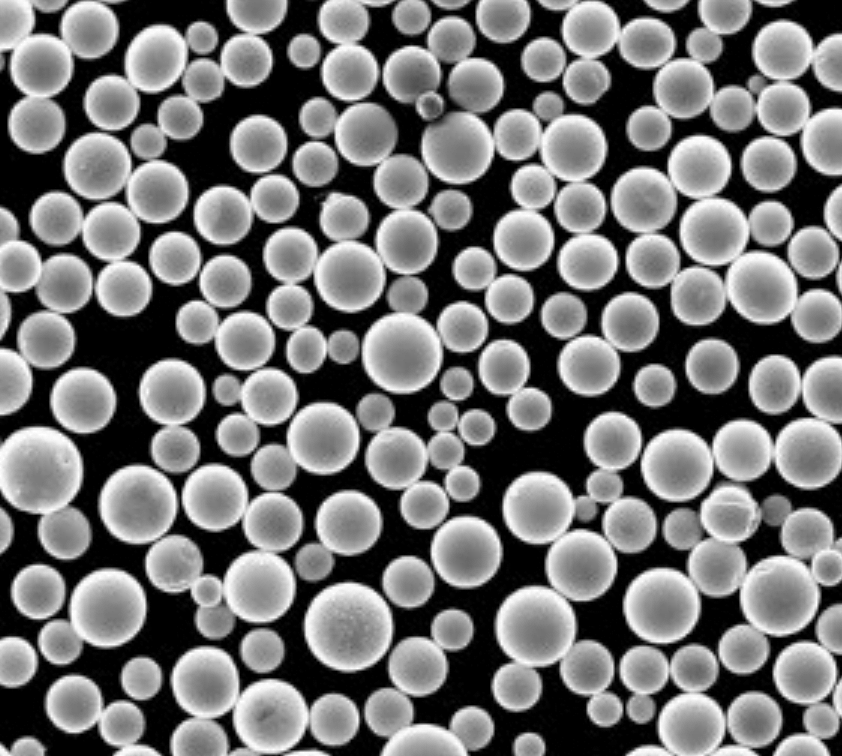
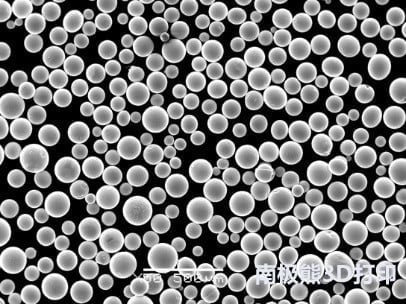
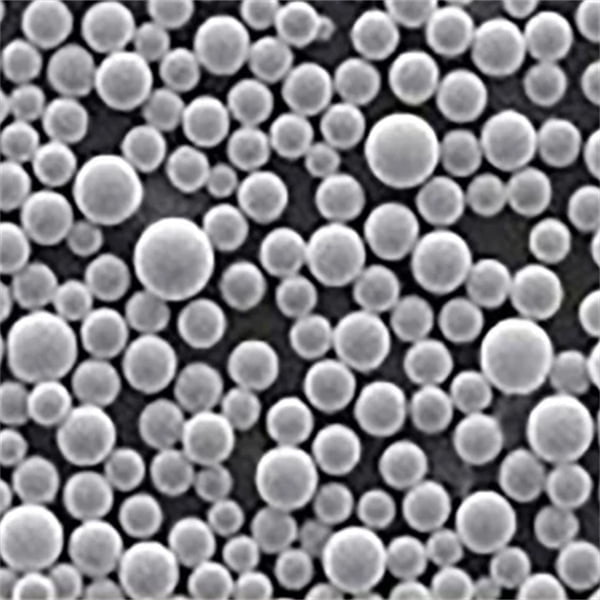
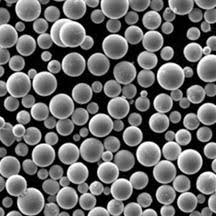
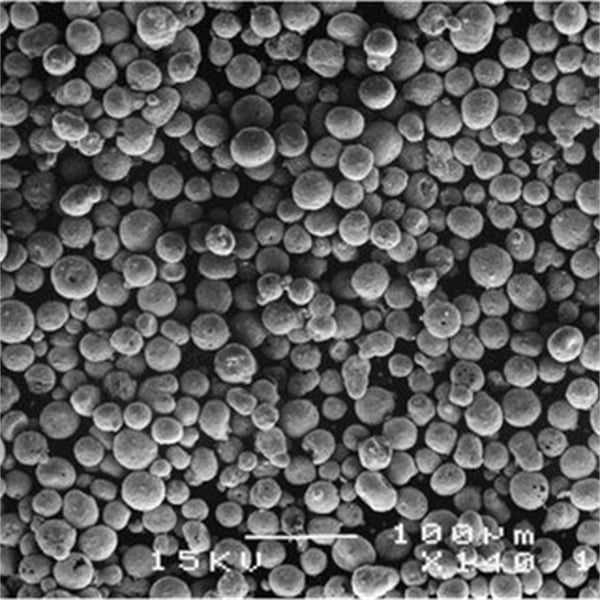
Choosing the Right Powder
Selecting the ideal metal powder depends on the specific application’s demands. Here are some key factors to consider:
- Required Properties: Is high-temperature strength, creep resistance, oxidation resistance, or a combination of these most critical? Different powders excel in various areas.
- AMプロセス: The chosen powder needs to be compatible with the specific additive manufacturing process, like laser melting (SLM) or electron beam melting (EBM).
- 印刷可能: Some powders flow better during the printing process, leading to smoother surface finishes and less post-processing work.
- コストだ: Metal powders can vary significantly in price, and finding the right balance between cost and desired properties is crucial.
The Future of Metal Powders:
The development of metal powders for nickel-based superalloys is a rapidly evolving field. Researchers are continuously exploring new compositions and manufacturing techniques to achieve:
- 機械的特性の向上: Even higher strength, better creep resistance, and enhanced oxidation resistance are ongoing targets.
- Reduced Cost: Making these advanced powders more cost-effective will broaden their adoption in various industries.
- 持続可能性: Developing environmentally friendly production processes for metal powders is becoming increasingly important.
Beyond Powders: Wrought and Cast Superalloys
While metal powders are making a splash in additive manufacturing, traditional wrought and cast forms of nickel-based superalloys remain prevalent. These forms offer established properties and well-understood processing techniques, making them suitable for various applications. Here’s a quick comparison:
- Wrought Superalloys: Produced through processes like forging and rolling, wrought superalloys offer excellent strength and good uniformity in properties. They are widely used in discs, rings, and other structural components for jet engines and gas turbines.
- Cast Superalloys: These alloys are formed by pouring molten metal into molds. Casting allows for complex shapes but might have slightly lower strength compared to wrought forms. They are commonly used in turbine blades and other intricate components requiring high-temperature performance.
応用例 ニッケル基超合金
Nickel-based superalloys are the go-to materials for applications where the heat is on – literally. Here’s a glimpse into their diverse world:
Aero Engines:
Imagine the fiery inferno within a jet engine. Turbine blades and discs, constantly battling scorching temperatures exceeding 1000°C (1832°F) and immense centrifugal forces, rely heavily on nickel-based superalloys. Their exceptional high-temperature strength, creep resistance, and good oxidation resistance make them irreplaceable in modern jet engines, enabling efficient and powerful flight.
Gas Turbines:
Similar to jet engines, gas turbines used in power generation require components that can withstand high temperatures and pressure. Nickel-based superalloys play a crucial role in turbine blades, combustor liners, and other critical parts, ensuring efficient and reliable energy production.
化学処理:
Chemical plants often handle harsh environments with corrosive chemicals and extreme temperatures. Nickel-based superalloys, with their good corrosion resistance and high-temperature strength, are well-suited for heat exchangers, reactor vessels, and other equipment exposed to demanding chemical processes.
Oil and Gas Industry:
Drilling deep into the Earth’s crust exposes equipment to extreme temperatures and pressure. Nickel-based superalloys find application in downhole tools, wellhead components, and other equipment that needs to withstand these harsh conditions.
その他の用途
The reach of nickel-based superalloys extends beyond these core sectors. They can be found in:
- Rocket engine components
- Heat exchangers for geothermal energy
- Land-based gas turbines
- Incineration plants
- Medical implants (due to their biocompatibility in some cases)
A Look at the Numbers: Properties Compared
Here’s a table summarizing the key properties of different nickel-based superalloy forms:
A Look at the Numbers: Properties Compared (Continued)
プロパティ | Wrought Superalloys | Cast Superalloys | Metal Powders (AM) |
---|---|---|---|
引張強さ (MPa) | 1000-1400 | 700-1200 | 900-1300 (depending on powder) |
降伏強度 (MPa) | 700-1100 | 500-900 | 600-1000 (depending on powder) |
クリープ抵抗 | 素晴らしい | 調子が良い | Varies depending on powder composition and processing |
抗酸化性 | 調子が良い | 調子が良い | Varies depending on powder composition |
アプリケーション | Discs, rings, structural components | Turbine blades, complex shapes | Can be used for both, potential for complex geometries |
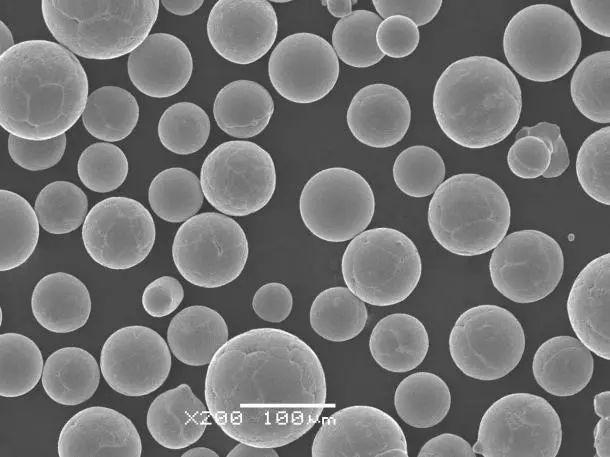
利点と限界
Nickel-based superalloys offer undeniable advantages, but like any material, they come with limitations. Here’s a balanced perspective:
メリット
- Exceptional High-Temperature Performance: Their ability to retain strength and resist creep at scorching temperatures makes them irreplaceable in many demanding applications.
- Superior Oxidation Resistance: They can withstand hot, oxidizing environments without succumbing to degradation.
- Good Corrosion Resistance: Many alloys offer good resistance to various corrosive agents, expanding their usability.
- 汎用性がある: The wide range of available compositions allows for tailoring properties to specific needs.
- Potential for Complex Geometries: Additive manufacturing with metal powders opens doors for creating intricate shapes that might be challenging with traditional methods.
制限:
- 高コスト: Nickel and other elements used in these alloys can be expensive, driving up the overall material cost.
- Fabrication Challenges: Working with ニッケル基超合金 can be difficult due to their inherent strength and work hardening tendencies.
- 限られた延性: These alloys tend to be less ductile (malleable) compared to some other materials, making them less forgiving in situations requiring some flexibility.
- Environmental Concerns: The extraction and processing of some elements used in these alloys can have environmental impacts.
よくあるご質問
Q: Are nickel-based superalloys the same as stainless steel?
A: No, while both offer corrosion resistance, they have distinct properties. Nickel-based superalloys excel in high-temperature applications, while stainless steel is generally better suited for moderate temperatures and offers a wider range of corrosion resistance depending on the specific type.
Q: Can nickel-based superalloys be recycled?
A: Yes, they can be recycled through various techniques. Recycling not only reduces environmental impact but also helps conserve resources.
Q: What are some future trends for nickel-based superalloys?
A: The future looks bright for these alloys. Research is focused on developing new compositions with even better properties, reducing production costs, and exploring more sustainable manufacturing processes. Additive manufacturing is also expected to play a growing role in creating complex components using nickel-based superalloy powders.
Q: Where can I find more information about specific nickel-based superalloys?
A: Several reputable sources offer detailed information on these alloys. Here are a few suggestions:
- The websites of major manufacturers of nickel-based superalloys, such as Special Metals Corporation, Haynes International, and ATI.
- Material property databases like MatWeb or ASM International’s AlloySource.
- Technical publications and articles from engineering societies like TMS (The Minerals, Metals & Materials Society) or ASM International.
結論
Nickel-based superalloys are not glamorous materials; they don’t have the shine of gold or the allure of a dazzling diamond. But behind the scenes, in the heart of jet engines, gas turbines, and other demanding applications, they play a vital role. Their exceptional ability to withstand scorching temperatures, resist creep and oxidation, and offer good corrosion resistance makes them the unsung heroes of extreme environments. As technology continues to push boundaries, the development of new nickel-based superalloys with even better properties is sure to keep them at the forefront of innovation. So, the next time you board a plane or witness the power of a gas turbine, remember the silent heroes within – the nickel-based superalloys, the steely backbone of extreme tech.
3DP mETALについて
製品カテゴリー
お問い合わせはこちら
何かご質問はありますか?今すぐメッセージを送信してください。あなたのメッセージを受信後、全チームで検討させていただきます。