Overview of Binder Jet 3D Printing
Binder jet 3D printing, often known as inkjet powder printing, is a groundbreaking technology that’s rapidly transforming the landscape of additive manufacturing. Unlike traditional 3D printing methods, binder jetting uses a binding agent to selectively bind areas of a powder bed. This process is repeated layer by layer to create a three-dimensional object.
What sets binder jetting apart? It’s faster, more versatile, and capable of using a wide range of materials, from metals to ceramics to composites. This article will delve deep into the world of binder jet 3D printing, exploring its intricacies, applications, and the specific metal powders that make it shine.
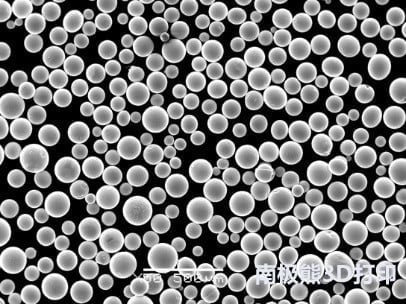
구성 바인더 제트 3D 프린팅
Binder jet 3D printing involves a unique blend of materials and processes. Here’s a closer look at the core components and their roles:
주요 구성 요소
- Powder Bed: The base material, which can be metal, ceramic, or composite powder.
- Binder: The adhesive agent that selectively bonds the powder particles together.
- Print Head: Deposits the binder in a precise pattern.
- Recoat Mechanism: Spreads a new layer of powder after each binding step.
Table: Common Metal Powders Used in Binder Jet 3D Printing
금속 분말 | 컴포지션 | 속성 | 특성 |
---|---|---|---|
스테인리스 스틸 316L | Fe, Cr, Ni, Mo | 높은 내식성, 연성 | 해양 및 의료 분야에 이상적 |
Inconel 625 | Ni, Cr, Mo, Nb | 고강도, 우수한 내피로성 | Suitable for aerospace and chemical industries |
구리 | Cu | 높은 전기 및 열 전도도 | 전기 부품에 사용 |
티타늄 Ti6Al4V | Ti, Al, V | 높은 강도-중량 비율 | Common in aerospace and biomedical fields |
알루미늄 AlSi10Mg | Al, Si, Mg | 가볍고 우수한 기계적 특성 | 자동차 및 항공우주 산업에서 사용 |
코발트-크롬(CoCr) | Co, Cr, Mo | 높은 내마모성 및 내식성 | 치과 및 정형외과 임플란트에 이상적 |
공구강 M2 | Fe, Mo, Cr, V, W | 높은 경도 및 내마모성 | Used in cutting tools and industrial applications |
니켈 합금 718 | Ni, Cr, Fe, Nb, Mo | 고강도 및 내식성 | Common in aerospace and power generation |
브론즈 | Cu, Sn | High strength and wear resistance | Used in sculptures and industrial applications |
텅스텐 카바이드(WC) | W, C | Extremely hard and dense | Used in cutting tools and wear-resistant parts |
Composition Analysis
The composition of the metal powders significantly impacts the final properties of the printed object. For instance, stainless steel 316L offers excellent corrosion resistance, making it suitable for marine and medical applications. On the other hand, titanium Ti6Al4V, with its high strength-to-weight ratio, is a staple in aerospace and biomedical fields.
의 특성 바인더 제트 3D 프린팅
Understanding the characteristics of binder jet 3D printing is crucial for appreciating its advantages and limitations.
주요 특징
- 속도: Binder jetting is one of the fastest 3D printing technologies available.
- 재료 다양성: Capable of printing metals, ceramics, and composites.
- No Need for Support Structures: The powder bed itself acts as a support.
- 포스트 프로세싱: Often requires post-printing sintering to enhance mechanical properties.
- 해상도: High-resolution printing, suitable for intricate designs.
Table: Key Characteristics of Binder Jet 3D Printing
특성 | 설명 |
---|---|
인쇄 속도 | Fast, ideal for large-scale production |
Material Range | Broad, includes metals, ceramics, and composites |
Support Structures | Not required, powder bed acts as support |
포스트 프로세싱 | Sintering or infiltration needed for final strength |
Printing Resolution | High, can produce detailed and complex geometries |
환경 영향 | Lower than traditional manufacturing due to less material waste |
비용 효율성 | Economical for large batch production |
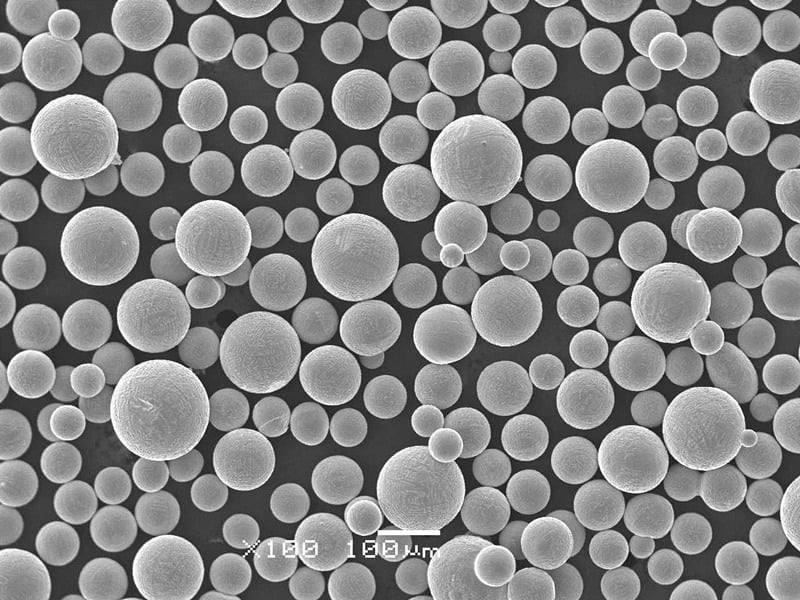
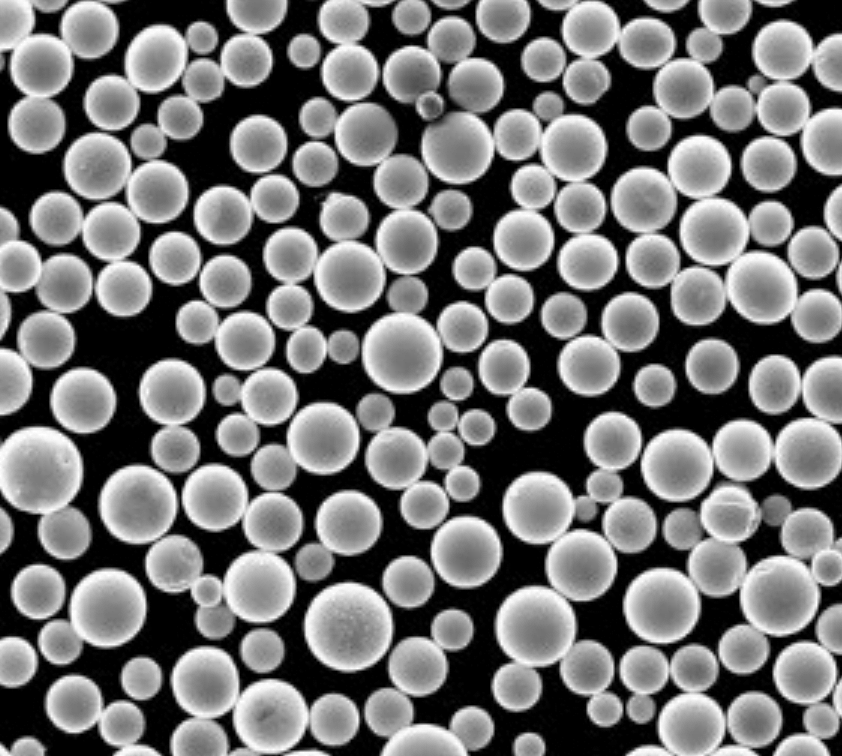
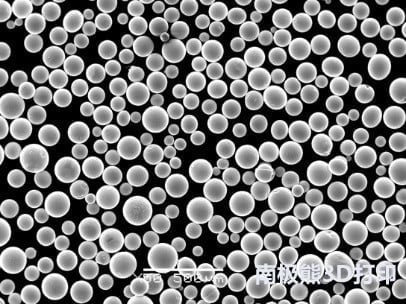
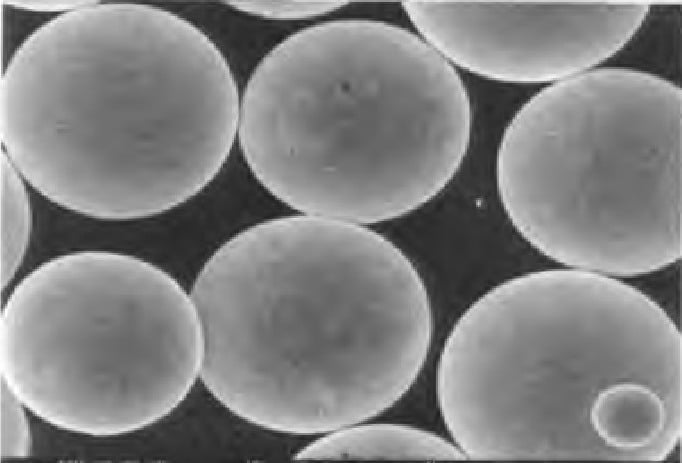
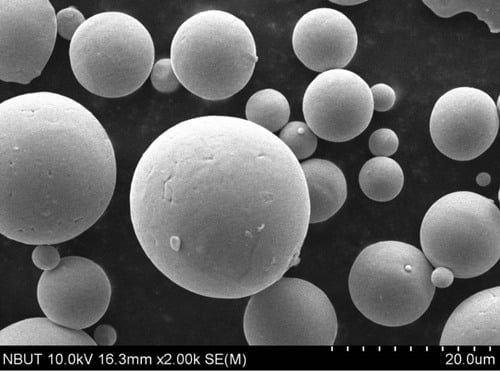
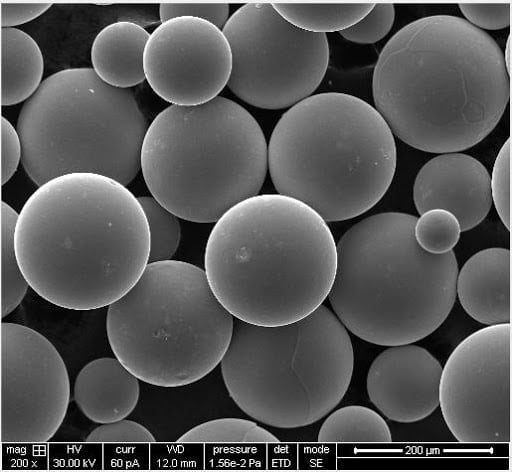
Advantages and Disadvantages
장점
- 빠른 생산 속도: Suitable for large-scale production runs.
- Versatile Material Use: Can handle a wide range of materials, making it adaptable to various industries.
- No Support Structures Needed: Reduces material waste and post-processing time.
- Detailed Geometries: High-resolution printing allows for intricate designs and complex geometries.
단점
- Post-Processing Required: Sintering and infiltration are often necessary to achieve desired material properties.
- Initial Setup Cost: High initial investment in equipment and materials.
- 재료 제한: Not all materials are suitable for binder jetting, particularly those that require high temperatures.
Applications of Binder Jet 3D Printing
Binder jet 3D printing is used across various industries due to its versatility and efficiency. Here’s a look at some key applications:
Table: Applications of Binder Jet 3D Printing
산업 | 신청 |
---|---|
항공 우주 | Engine components, turbine blades, structural parts |
자동차 | Prototypes, lightweight parts, custom components |
의학 (Yi-hak) | 인체 이식물, 보철물, 수술 기기 |
치과 | Crowns, bridges, orthodontic appliances |
소비재 | Jewelry, custom art, home décor |
산업 장비 | Tooling, molds, and fixtures |
전자제품 | Heat sinks, connectors, custom enclosures |
아키텍처 | Scale models, custom building components |
Art and Sculpture | Sculptures, complex artistic designs |
에너지 | Turbine parts, fuel nozzles, heat exchangers |
Case Studies and Examples
- 항공 우주: In the aerospace industry, binder jetting is used to produce complex turbine blades with internal cooling channels, which are impossible to manufacture using traditional methods.
- 의학 (Yi-hak): Binder jetting allows for the production of patient-specific implants, tailored to fit individual anatomical requirements, enhancing recovery and performance.
- 자동차: The automotive industry benefits from binder jetting through the creation of lightweight, high-strength components that improve fuel efficiency and performance.
사양, 크기, 등급 및 표준
Understanding the specifications, sizes, grades, and standards of binder jet 3D printing materials is crucial for ensuring quality and performance.
Table: Specifications of Metal Powders for Binder Jet 3D Printing
금속 분말 | 크기(미크론) | 학년 | 표준 |
---|---|---|---|
스테인리스 스틸 316L | 15-45 | ASTM F3184 | ISO 9001, ASTM A240 |
Inconel 625 | 15-53 | AMS 5666 | ISO 9001, AMS 5662 |
구리 | 10-50 | ASTM B170 | ISO 9001, ASTM B187 |
티타늄 Ti6Al4V | 15-45 | ASTM F2924 | ISO 9001, ASTM B348 |
알루미늄 AlSi10Mg | 20-63 | DIN EN 1706 | ISO 9001, ASTM B209 |
코발트-크롬(CoCr) | 15-53 | ASTM F75 | ISO 9001, ASTM F1537 |
공구강 M2 | 15-53 | ASTM A600 | ISO 9001, ASTM A681 |
니켈 합금 718 | 15-53 | AMS 5662 | ISO 9001, AMS 5596 |
브론즈 | 10-50 | ASTM B427 | ISO 9001, ASTM B584 |
텅스텐 카바이드(WC) | 15-45 | ISO 9001 | ISO 9001, ASTM B777 |
Importance of Standards
Adhering to standards such as ISO 9001 ensures that the materials used in binder jet 3D printing meet rigorous quality and performance criteria. This is especially critical in industries like aerospace and medical, where component failure is not an option.
공급업체 및 가격 세부 정보
Choosing the right supplier is crucial for obtaining high-quality metal powders and binders for binder jet 3D printing.
Table: Suppliers and Pricing of Metal Powders
공급자 | 금속 분말 | 가격(kg당) | 위치 | 웹사이트 |
---|---|---|---|---|
GKN 첨가제 | 스테인리스 스틸 316L | $120 | 글로벌 | GKN 첨가제 |
카펜터 기술 | Inconel 625 | $400 | 미국 | 카펜터 기술 |
회가나스 | 구리 | $90 | 글로벌 | [Höganäs](https://www.hoganas.com |
LPW 기술 | 티타늄 Ti6Al4V | $300 | 영국 | LPW 기술 |
적도 | 알루미늄 AlSi10Mg | $150 | 캐나다 | 적도 |
EOS GmbH | 코발트-크롬(CoCr) | $500 | 독일 | EOS GmbH |
산드빅 | 공구강 M2 | $200 | 스웨덴 | 산드빅 |
프렉스에어 표면 기술 | 니켈 합금 718 | $450 | 미국 | 프락세어 |
리오 틴토 | 브론즈 | $100 | 글로벌 | 리오 틴토 |
글로벌 텅스텐 및 분말 | 텅스텐 카바이드(WC) | $600 | 미국 | GTP |
Choosing a Supplier
When selecting a supplier, consider factors such as price, material quality, and proximity. Suppliers like GKN Additive and Carpenter Technology offer high-quality materials and have a global presence, ensuring reliable supply chains.
장단점 바인더 제트 3D 프린팅
Every technology has its strengths and weaknesses. Here’s a detailed comparison of the pros and cons of binder jet 3D printing:
Table: Pros and Cons of Binder Jet 3D Printing
측면 | 장점 | 단점 |
---|---|---|
속도 | Fast production, ideal for batch manufacturing | May require multiple runs for complex objects |
다양한 소재 | Can use a wide range of materials | Not all materials are compatible |
Support Structures | No need for additional supports | Powder bed may require extensive post-processing |
비용 | Economical for large-scale production | 높은 초기 설정 비용 |
해상도 | High detail, capable of intricate designs | Resolution can be lower than some other 3D printing methods |
환경 영향 | Lower material waste compared to traditional methods | Requires careful disposal of used powder |
Detailed Analysis
- 속도: One of the standout features of binder jetting is its speed. This makes it an attractive option for industries looking to scale up production quickly. However, for extremely complex designs, multiple printing runs may be necessary, which can offset the speed advantage.
- 다양한 소재: The ability to use a variety of materials, from metals to ceramics, gives binder jetting a versatile edge. However, the technology is not universally compatible with all materials, particularly those requiring high melting points.
- Support Structures: The powder bed serves as a natural support, eliminating the need for additional structures and reducing material waste. However, this can lead to a need for more extensive post-processing to remove excess powder.
- 비용: Binder jetting is cost-effective for large-scale production, but the initial investment in equipment and materials can be high. This makes it less accessible for small businesses or individual hobbyists.
- 해상도: While binder jetting offers high resolution, capable of producing detailed and intricate designs, it may not match the precision of some other 3D printing methods like SLS or SLA.
비교 바인더 제트 3D 프린팅 to Other 3D Printing Methods
Binder jetting isn’t the only 3D printing technology out there. Here’s how it stacks up against some other popular methods:
Table: Comparison of Binder Jet 3D Printing with Other Methods
측면 | 바인더 제트 3D 프린팅 | 용융 증착 모델링(FDM) | 선택적 레이저 소결(SLS) |
---|---|---|---|
속도 | Fast, suitable for large batches | Slower, more suited for prototypes | Moderate, good for detailed parts |
Material Range | Wide, includes metals, ceramics, composites | Limited, mainly plastics | Wide, mainly polymers and some metals |
Support Structures | Not required | Required | Not required |
비용 | High initial cost, economical for mass production | Lower initial cost, higher per-part cost | High initial and per-part cost |
해상도 | High, but can vary | 보통 | High, very detailed |
포스트 프로세싱 | Often required (sintering/infiltration) | 최소 | Often required (cooling/removal) |
세부 비교
- 속도: Binder jetting is generally faster than FDM and SLS, making it suitable for large-scale production runs. FDM is slower and more suited to rapid prototyping, while SLS offers moderate speed but excels in creating highly detailed parts.
- Material Range: Binder jetting stands out with its ability to use a wide range of materials, including metals and ceramics. FDM is primarily limited to plastics, whereas SLS can handle polymers and some metals.
- Support Structures: The powder bed in binder jetting and SLS negates the need for additional support structures, reducing material waste and simplifying post-processing. FDM, however, often requires support structures which need to be manually removed.
- 비용: The initial cost of binder jetting and SLS is high, but binder jetting is more economical for mass production. FDM has a lower initial cost but a higher per-part cost, making it less suitable for large-scale manufacturing.
- 해상도: While all three methods offer high resolution, SLS is often considered the best for producing highly detailed parts. Binder jetting provides a good balance of speed and resolution, and FDM offers moderate resolution, suitable for less detailed applications.
- 포스트 프로세싱: Binder jetting typically requires sintering or infiltration to achieve the desired mechanical properties, whereas FDM requires minimal post-processing. SLS often needs cooling and removal of excess powder, similar to binder jetting.
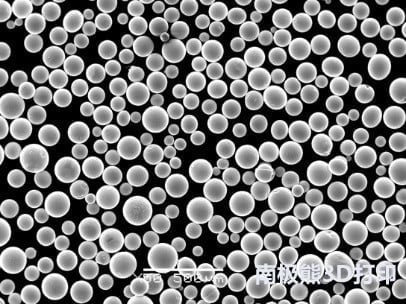
FAQ
질문 | 답변 |
---|---|
What is Binder Jet 3D Printing? | A 3D printing process using a binder to selectively join powder particles to form objects. |
What materials can be used? | Metals, ceramics, and composites. |
Is post-processing required? | Yes, usually sintering or infiltration is needed. |
How fast is Binder Jet 3D Printing? | It is one of the fastest 3D printing technologies. |
What are the key applications? | Aerospace, automotive, medical, dental, consumer goods, and more. |
Do I need support structures? | No, the powder bed acts as a natural support. |
What are the cost implications? | High initial setup cost, but economical for large-scale production. |
How does it compare to other 3D printing methods? | Faster, more versatile in material use, and capable of higher resolution than some methods. |
결론
Binder jet 3D printing is a versatile, efficient, and rapidly advancing technology that’s reshaping manufacturing across various industries. Whether you’re looking to produce complex aerospace components, customized medical implants, or intricate art pieces, binder jetting offers unparalleled speed and flexibility. With a deep understanding of its composition, characteristics, applications, and how it compares to other methods, you can harness the full potential of this innovative technology.
3DP mETAL 정보
제품 카테고리
문의하기
궁금한 점이 있으신가요? 지금 바로 문의하세요! 문의를 받으면 전체 팀이 함께 요청 사항을 처리합니다.