Imagine a material so strong it can withstand the scorching heat of a jet engine, so resistant to corrosion it can laugh off years of exposure to harsh chemicals. This isn’t science fiction; this is the world of Inconel, a nickel-chromium superalloy renowned for its exceptional properties. But what if we told you there’s a way to create complex shapes from this remarkable material? Enter the fascinating realm of 인코넬 3D 프린팅, a technology that’s revolutionizing manufacturing across various industries.
3D Printing Technology of 인코넬 3D 프린팅
3D printing, also known as additive manufacturing, disrupts traditional manufacturing by building objects layer by layer based on a digital model. This allows for the creation of intricate geometries that would be impossible or incredibly difficult with conventional techniques like machining. Inconel, with its inherent strength and resistance to heat, presents a unique challenge for 3D printing. However, advancements in the field have given rise to several powerful techniques specifically suited for this superalloy.
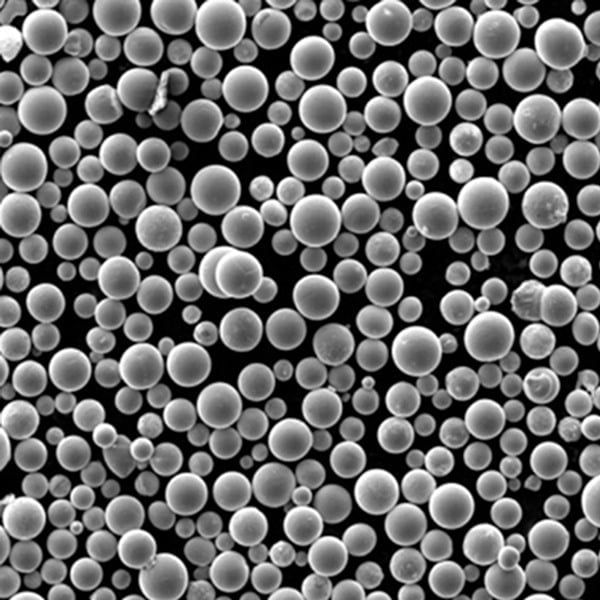
Several Main Technologies for Inconel 3D Printing
1. Laser Beam Melting (LBM): Often referred to as Selective Laser Melting (SLM) or Direct Metal Laser Sintering (DMLS), LBM is a popular choice for 인코넬 3D 프린팅. It works by focusing a high-powered laser beam on a bed of Inconel powder, melting it layer by layer according to the design. This process boasts excellent precision and can produce parts with near-net shapes, minimizing the need for post-processing. However, LBM can be expensive due to the high-powered lasers involved and requires careful control of the printing environment to prevent warping and cracking.
2. Electron Beam Melting (EBM): Similar to LBM, EBM utilizes a high-energy beam, but in this case, it’s an electron beam that melts the Inconel powder in a vacuum chamber. This method offers several advantages, including the ability to print larger parts and a reduced risk of oxidation compared to LBM. However, EBM setups are generally more expensive than LBM systems, and the surface finish of printed parts might require additional treatment.
3. Binder Jetting (BJ): This method takes a different approach. A liquid binder is selectively deposited onto a bed of Inconel powder, adhering the particles together according to the design. The part is then heat-treated to solidify the binder and achieve the desired strength. BJ is generally faster and less expensive than LBM or EBM. However, the post-processing steps can be more extensive, and the final part density might be slightly lower compared to other techniques.
Choosing the Right Technique: The selection of the optimal 3D printing technique for Inconel depends on various factors like the desired part complexity, size, strength requirements, budget, and surface finish needs. LBM offers a good balance between precision, strength, and cost for intricate parts. EBM might be suitable for larger components requiring a high degree of strength and corrosion resistance. BJ can be a cost-effective option for simpler shapes where a slightly lower density is acceptable.
Advantages of 3D Printing Inconel
The ability to 3D print Inconel unlocks a treasure trove of benefits for manufacturers. Here are some key advantages that make this technology so compelling:
- 자유로운 디자인: Unlike traditional subtractive methods like machining, 3D printing allows for the creation of complex geometries with internal channels, lattices, and other intricate features. This design freedom enables the development of lighter, more efficient components for various applications.
- 리드 타임 단축: 3D printing eliminates the need for complex tooling and lengthy machining processes. This translates to faster turnaround times, allowing manufacturers to get prototypes and end-use parts into production quicker.
- 재료 효율성: 3D printing utilizes only the necessary material for the design, minimizing waste compared to subtractive techniques. This is particularly beneficial for expensive materials like Inconel.
- 향상된 성능: The ability to create complex internal structures with 3D printing can lead to lighter, stronger parts with superior heat dissipation properties. This is especially advantageous for applications in aerospace, energy, and motorsports.
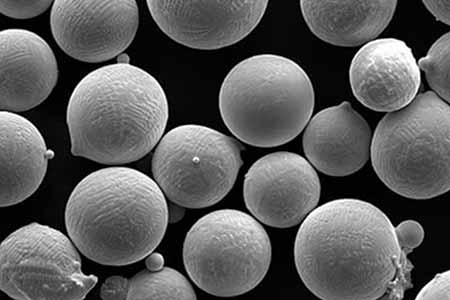
Applications of 3D Printing Inconel
The exceptional properties of Inconel, coupled with the design freedom of 3D printing, make this technology a game-changer across various industries. Here are some prominent applications:
- 항공우주: Inconel’s ability to withstand extreme temperatures and harsh environments makes it ideal for jet engine components like combustors, turbine blades, and afterburners. 3D printing allows for the creation of lightweight, high-performance parts with intricate cooling channels, optimizing engine efficiency.
- 화학 처리: Inconel’s exceptional resistance to corrosion makes it perfect for valves, pumps, and piping in chemical plants. 3D printing enables the creation of complex components with internal flow paths that optimize performance and resist corrosion in harsh chemical environments. This can lead to lighter, more efficient equipment with reduced maintenance needs.
- Energy Production: Inconel plays a vital role in energy applications due to its high-temperature strength and corrosion resistance. 3D printing is being utilized to create components for gas turbines, nuclear reactors, and geothermal power plants. For instance, 3D-printed Inconel heat exchangers can improve efficiency in power generation by withstanding extreme temperatures and pressures.
- 의료 기기: Inconel’s biocompatibility and resistance to corrosion make it suitable for certain medical implants. 3D printing allows for the creation of customized implants with intricate structures that can better fit a patient’s anatomy. This can lead to improved patient outcomes and faster recovery times.
- Motorsport: The relentless pursuit of performance in motorsports makes Inconel a valuable material. 3D-printed Inconel components like exhaust manifolds and turbocharger housings can be lightweight and highly durable, enabling race cars to achieve peak performance without sacrificing reliability.
- Luxury Goods: Beyond its industrial applications, Inconel’s unique combination of strength and aesthetics has found a niche in the world of luxury goods. 3D printing allows for the creation of high-end watch components, jewelry, and other bespoke items with intricate designs that showcase the material’s distinctive properties.
Challenges and Considerations for 인코넬 3D 프린팅
While 3D printing offers exciting possibilities for Inconel, there are certain challenges and considerations to keep in mind:
- 비용: Inconel is a high-priced material, and 3D printing processes can also be expensive due to the specialized equipment and expertise required. This can limit the technology’s adoption for certain applications.
- 표면 마감: The surface finish of 3D-printed Inconel parts might require additional post-processing treatments depending on the specific application. This can add to the overall cost and production time.
- 지원 구조: 3D printing often requires the use of support structures to prevent warping and cracking during the build process. Removing these supports can be a delicate process, and any imperfections on the part’s surface might necessitate further finishing.
- 머티리얼 속성: The properties of 3D-printed Inconel can vary slightly compared to traditionally manufactured Inconel due to the unique solidification process involved in additive manufacturing. Careful optimization of printing parameters is crucial to achieve the desired mechanical properties.
- Expertise: Successful 3D printing of Inconel requires a high level of expertise in both the material and the specific printing technology. Partnering with a qualified 3D printing service provider with experience in handling Inconel is essential.
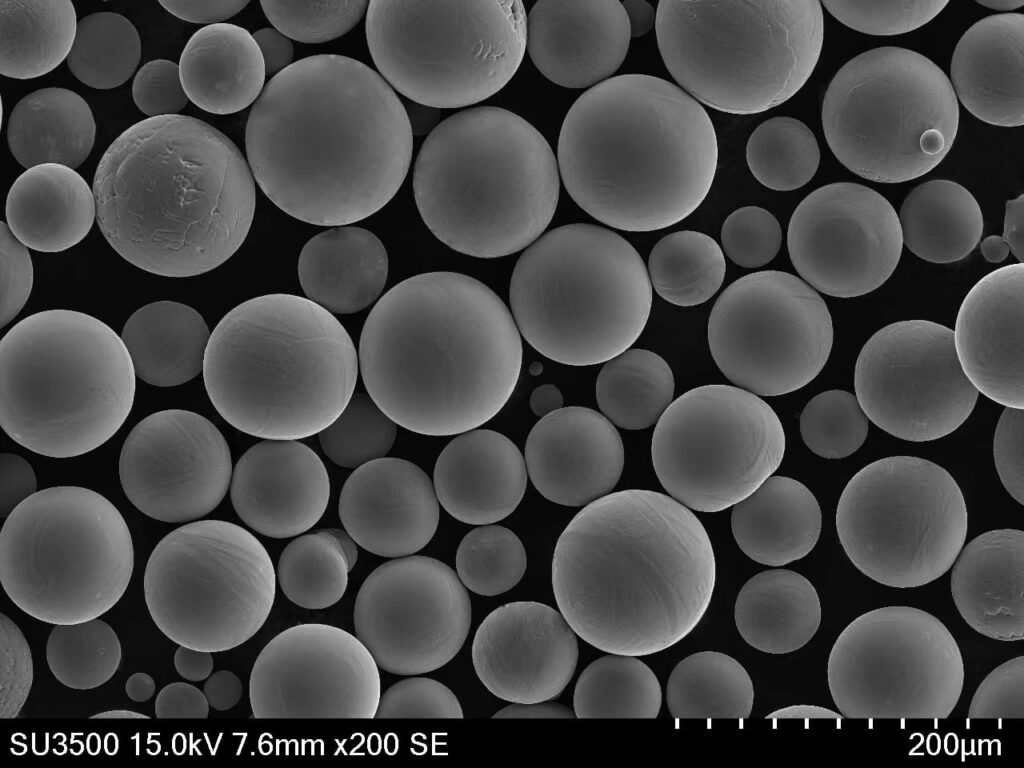
FAQ
Q: What are the benefits of 3D printing Inconel compared to traditional manufacturing techniques?
A: 3D printing offers several advantages over traditional methods like machining for Inconel parts. These include design freedom for creating complex geometries, reduced lead times, improved material efficiency, and the potential for lighter, stronger components.
Q: What are the main challenges associated with 3D printing Inconel?
A: The primary challenges include the high cost of the material and the 3D printing process itself. Surface finish, support structure removal, achieving desired material properties, and the need for expertise are other considerations.
Q: Which industries are benefiting most from 3D printing Inconel?
A: Aerospace, chemical processing, energy production, medical devices, and motorsports are some of the leading industries utilizing 3D-printed Inconel for its exceptional properties.
Q: Is 3D-printed Inconel as strong as traditionally manufactured Inconel?
A: With proper optimization of printing parameters, 3D-printed Inconel can achieve mechanical properties comparable to traditionally manufactured Inconel. However, careful selection of the printing process and post-processing techniques are crucial.
Q: Where can I find a service provider for 3D printing Inconel parts?
A: Several 3D printing service providers offer expertise in handling Inconel. Look for companies with a proven track record in working with this material and ensure they possess the necessary equipment and know-how for your specific application.
결론
Inconel 3D printing represents a significant leap forward in manufacturing capabilities. By unlocking the potential to create complex, high-performance parts from this remarkable superalloy, this technology is transforming various industries. As advancements continue and costs become more competitive, we can expect 3D-printed Inconel to play an even greater role in shaping the future of manufacturing.
3DP mETAL 정보
제품 카테고리
문의하기
궁금한 점이 있으신가요? 지금 바로 문의하세요! 문의를 받으면 전체 팀이 함께 요청 사항을 처리합니다.