인코넬 분말, a superhero amongst metal powders, transforms the way we design and manufacture critical components. But what exactly is this wonder material, and how does it revolutionize various industries? Buckle up, because we’re about to embark on a journey into the fascinating world of Inconel powder!
What is Inconel Powder?
Imagine grinding down a superalloy, Inconel, into a fine, metallic dust. That’s essentially Inconel powder! Inconel itself is a family of nickel-based superalloys renowned for their exceptional strength, high-temperature resistance, and impressive resistance to corrosion. When reduced to a powder form, Inconel retains these remarkable properties, making it a game-changer in additive manufacturing (3D printing).
the Composition: A Blend of Strength
Nickel forms the foundation of Inconel powder, typically constituting around 70%. Chromium, another key player, contributes to its resistance to oxidation and high-temperature performance. Other alloying elements, such as niobium, molybdenum, and iron, are strategically incorporated to fine-tune specific properties based on the desired application. The exact composition varies depending on the specific Inconel grade, like Inconel 625 or Inconel 718, each formulated to excel in particular environments.
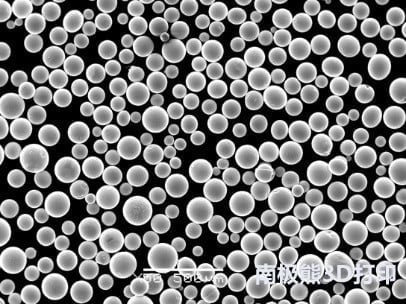
The Manufacturing Method of 인코넬 분말
Here’s a peek behind the curtain of Inconel powder’s creation:
- 원자화: The most common method involves turning molten Inconel into a mist of tiny droplets through high-pressure gas or water atomization. These droplets rapidly solidify into a fine powder with a spherical shape, ideal for 3D printing processes.
- Plasma Rotating Electrode Technique (PERC): This technique utilizes a rotating electrode partially submerged in molten Inconel. A high-temperature plasma torch melts the electrode, and the centrifugal force ejects tiny droplets that solidify into a powder with a more irregular morphology.
- 화학 기상 증착(CVD): This method involves decomposing gaseous precursors onto a heated substrate, allowing Inconel to build up layer by layer in powder form. CVD-produced Inconel powder offers exceptional purity and control over particle size.
Advantages and Considerations of Different Techniques:
기술 | 장점 | 고려 사항 |
---|---|---|
원자화 | Established, cost-effective, good flowability | May require post-processing to achieve desired particle size and morphology |
PERC | High purity, tailorable particle size and morphology | Relatively complex and expensive |
CVD | Exceptional purity, precise control over particle size and morphology | Limited production capacity, high cost |
Common Applications of Inconel Powder
Inconel powder’s unique blend of properties unlocks possibilities in various sectors:
- 항공우주: Inconel powder finds its calling in jet engine components like turbine blades and combustors. Their ability to withstand extreme temperatures and harsh environments makes them irreplaceable in the relentless pursuit of efficient and powerful aircraft.
- 화학 처리: Inconel powder’s exceptional resistance to corrosion makes it ideal for manufacturing equipment handling harsh chemicals and high temperatures, ensuring process safety and longevity.
- Energy Production: From components in nuclear reactors to parts in advanced gas turbines, Inconel powder plays a crucial role in the reliable and efficient generation of power.
- 의료 기기: When biocompatibility is paramount, Inconel powder steps up. Certain grades can be used for medical implants requiring exceptional strength and corrosion resistance, potentially improving patient outcomes.
Beyond these core applications, Inconel powder’s potential extends to various other fields, including:
- Automotive: High-performance engine components and parts exposed to extreme temperatures.
- Marine Engineering: Shafts, propellers, and other components that need to withstand the harsh saltwater environment.
- Defense and Security: Components requiring a combination of strength, heat resistance, and corrosion resistance.
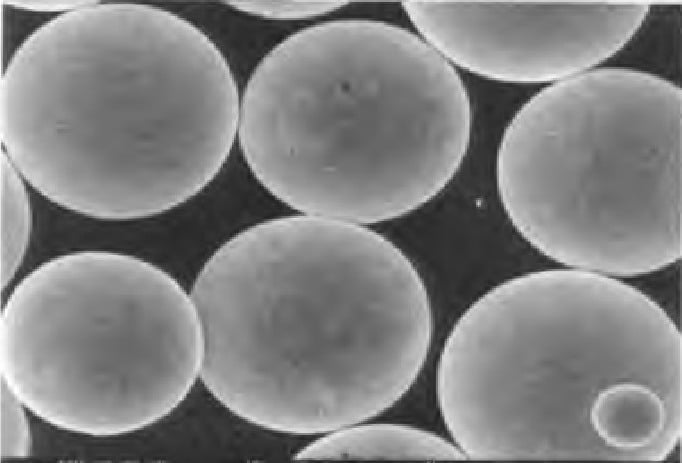
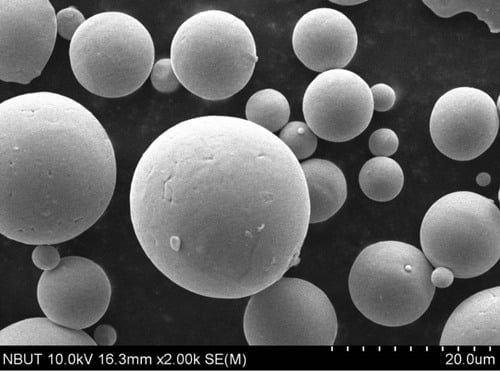
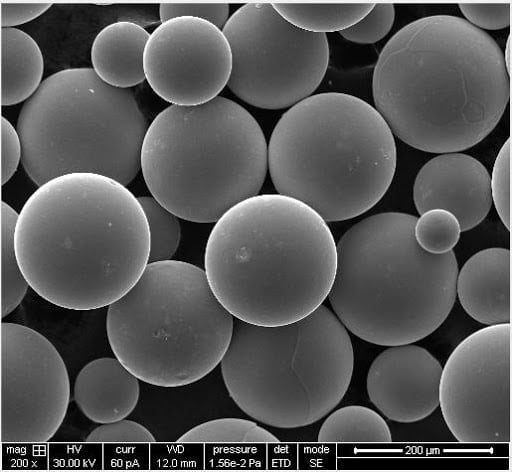
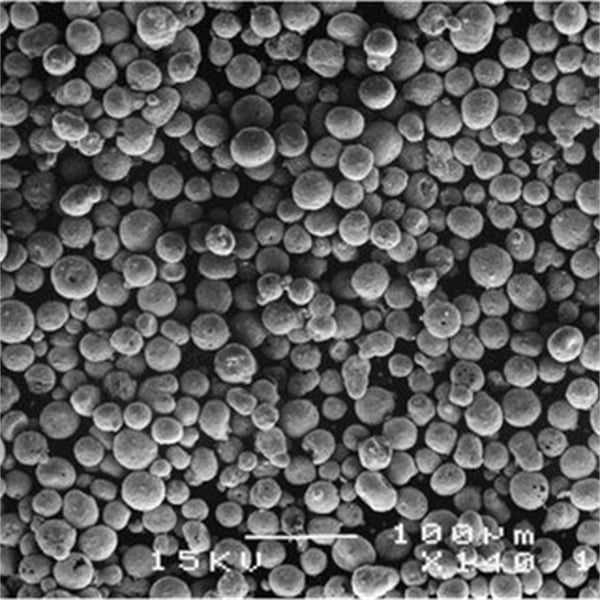
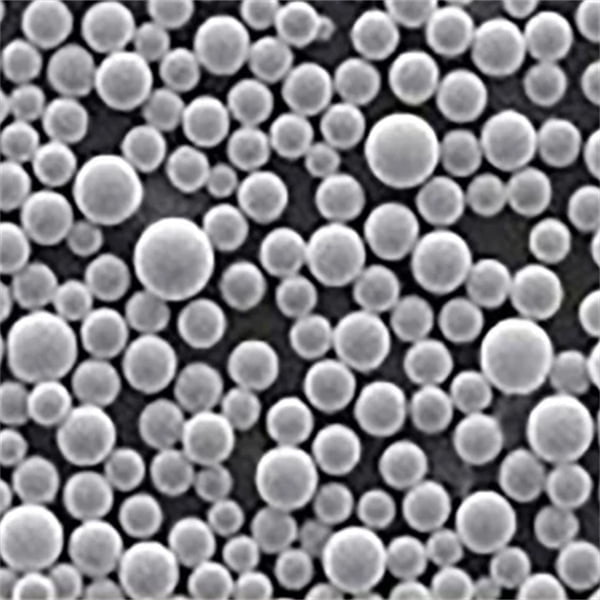
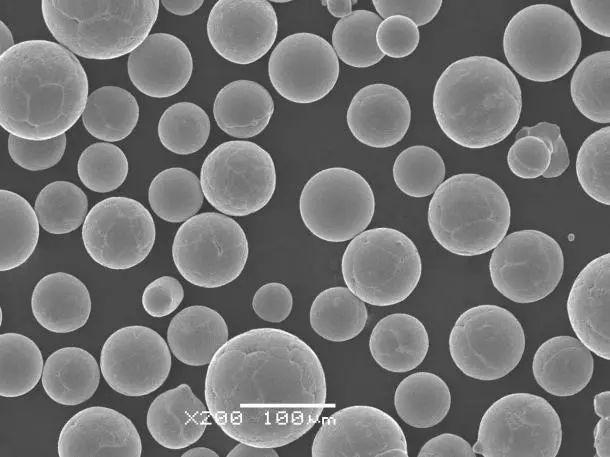
방법 인코넬 분말 is Processed into the Final Product
Once the magic of Inconel powder is complete, it’s transformed into a functional marvel through various techniques:
- 적층 제조(3D 프린팅): This revolutionary technology allows for the creation of complex, near-net-shape components layer-by-layer using Inconel powder. This minimizes material waste and enables the design of intricate geometries impossible with traditional manufacturing techniques.
- Laser Beam Melting (LBM): A high-powered laser beam selectively melts Inconel powder particles, fusing them layer-by-layer to build the desired 3D structure. LBM offers exceptional precision and control over the final product’s properties.
- 전자 빔 용융(EBM): Similar to LBM, EBM utilizes an electron beam in a vacuum environment to melt Inconel powder particles. This method is particularly suited for applications requiring tight control over oxygen content and minimizing oxidation effects.
- 바인더 분사: This technique involves inkjet printing a binder onto a bed of Inconel powder, selectively creating the desired 3D shape. The part is then heat-treated to solidify the metal particles and remove the binder.
Choosing the Right Technique:
The selection of the most suitable processing technique depends on several factors, including:
- Complexity of the part geometry: Additive manufacturing excels at creating intricate shapes.
- Dimensional accuracy and surface finish: LBM and EBM offer superior precision compared to binder jetting.
- 생산량: Binder jetting might be more suitable for larger batches, while LBM and EBM are ideal for prototypes and low-volume production.
- 머티리얼 속성: Specific techniques might be better suited to preserve desired properties in the final product.
Advantages of Using Inconel Powder in Additive Manufacturing:
- 자유로운 디자인: Unleash creativity with the ability to design complex geometries that traditional manufacturing struggles with.
- 경량화: Create components with intricate internal structures, reducing weight without compromising strength.
- 재료 효율성: Minimize material waste compared to traditional subtractive manufacturing techniques.
- 신속한 프로토타이핑: Expedite the prototyping process, allowing for quicker design iterations and faster product development cycles.
Considerations for Using Inconel Powder:
- 비용: Inconel powder itself and the additive manufacturing processes can be expensive compared to traditional techniques.
- 표면 마감: While some techniques offer good surface finishes, post-processing might be required for specific applications.
- 지원 구조: Certain geometries might require temporary support structures during the printing process, which need to be removed afterwards and can leave marks.
Cost Considerations of Inconel Powder
Inconel powder, a premium material, comes with a price tag reflecting its exceptional properties. Here’s a breakdown of the cost factors:
- 재료비: The base price of Inconel powder itself is higher compared to many other metal powders due to the complex alloying elements and production processes involved.
- 파우더 특성: Factors like particle size, morphology, and purity can influence the cost. For instance, finer powders or those with tighter size distribution might command a premium.
- Manufacturing Technique: The chosen additive manufacturing technique also plays a role. Techniques like EBM, with their higher precision and vacuum environment requirements, can be more expensive compared to binder jetting.
Despite the initial cost considerations, the benefits of using Inconel powder can outweigh the upfront investment. Here’s why:
- 재료 낭비 감소: Additive manufacturing minimizes material waste compared to traditional techniques, potentially leading to significant cost savings in the long run.
- 경량화 잠재력: The ability to create lightweight components with intricate structures can translate to fuel efficiency benefits in industries like aerospace, ultimately leading to cost savings.
- Performance Advantages: Inconel components’ exceptional strength, high-temperature resistance, and corrosion resistance can lead to extended lifespans and reduced maintenance costs.
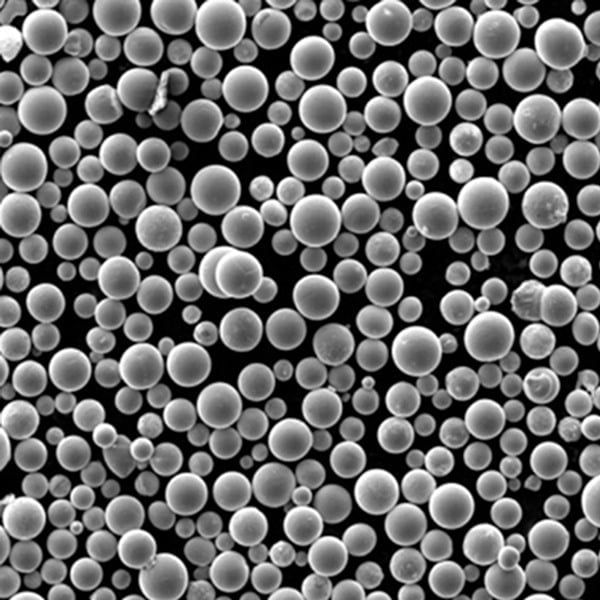
Future Outlook: The Untapped Potential of 인코넬 분말
The future of Inconel powder is gleaming bright. Here are some exciting trends to watch:
- Advancements in Powder Production: Research efforts are focused on developing more cost-effective and efficient methods for producing Inconel powder with even better control over particle size, morphology, and purity.
- Emerging Additive Manufacturing Techniques: Novel 3D printing technologies are constantly evolving, offering faster printing speeds, improved resolution, and the ability to combine multiple materials within a single print, potentially unlocking unprecedented design possibilities for Inconel components.
- Exploration of New Applications: As the technology matures and costs become more competitive, we can expect to see 인코넬 분말 integrated into a wider range of industries, further revolutionizing manufacturing processes and product design.
FAQ
질문 | 답변 |
---|---|
Q: How strong is Inconel powder compared to other metal powders? | A: Inconel powder boasts exceptional strength, surpassing many other commonly used metal powders like stainless steel or aluminum. The specific strength depends on the chosen Inconel grade and the processing technique used. |
Q: Is Inconel powder safe to handle? | A: Inconel powder, like most metal powders, can pose inhalation hazards if not handled properly. It’s crucial to follow recommended safety precautions, including using appropriate personal protective equipment (PPE) like respirators and gloves when handling the powder. |
Q: Can Inconel powder be recycled? | A: Yes, Inconel powder can be recycled to a certain extent. The specific recycling process depends on the contamination level of the used powder. Generally, uncontaminated Inconel powder can be reintroduced back into the manufacturing process, promoting sustainability. |
Q: What are the limitations of using Inconel powder? | A: Despite its remarkable properties, Inconel powder does have some limitations to consider. As mentioned earlier, the cost of the material and the additive manufacturing processes can be higher compared to traditional techniques. Additionally, surface finish might require post-processing for certain applications, and support structures used during printing can leave marks on the final product. |
Q: Where can I find more information about Inconel powder? | A: Several resources offer detailed information about Inconel powder. Suppliers of Inconel powder often provide technical datasheets detailing the properties and specifications of their products. Additionally, industry associations and research institutions publish informative articles and reports on Inconel powder and additive manufacturing technologies. |
3DP mETAL 정보
제품 카테고리
문의하기
궁금한 점이 있으신가요? 지금 바로 문의하세요! 문의를 받으면 전체 팀이 함께 요청 사항을 처리합니다.