Overview of Laser Beam Powder Bed Fusion (PBF-LB)
In the realm of additive manufacturing, few technologies are as transformative as Laser Beam Powder Bed Fusion (PBF-LB). This process, a cornerstone of modern 3D printing, allows for the precise creation of complex metal parts by fusing metal powders layer by layer using a high-powered laser. But what makes PBF-LB so revolutionary, and why is it gaining traction across various industries? Let’s dive into the fascinating world of PBF-LB to uncover its secrets and understand its growing significance.
Importance of PBF-LB in Additive Manufacturing
The shift from traditional manufacturing to additive processes like PBF-LB marks a significant leap in how we produce metal components. No longer confined by the limitations of subtractive manufacturing, where material is removed from a solid block, PBF-LB offers unprecedented design freedom, reduced material waste, and the ability to create highly intricate geometries that were once thought impossible. This process is now a key player in industries such as aerospace, automotive, and medical devices, where precision and material performance are paramount.
The Science Behind Laser Beam Powder Bed Fusion (PBF-LB)
How PBF-LB Works: The Process Explained
Laser Beam Powder Bed Fusion (PBF-LB) is a complex yet elegant process that begins with a digital 3D model. This model is sliced into thin layers, which are then used to guide the laser as it selectively melts and fuses metal powder, layer by layer, until the part is fully formed. The precision of the laser ensures that each layer is perfectly aligned with the previous one, resulting in a highly accurate and robust final product.
The process can be broken down into the following steps:
- Powder Spreading: A thin layer of metal powder is spread across the build platform.
- Laser Scanning: The laser scans the surface, melting the powder in specific areas based on the 3D model.
- Solidification: The molten metal cools and solidifies, forming a solid layer.
- Layer Repetition: The platform lowers, and a new layer of powder is spread, repeating the process until the entire part is complete.
Understanding the Role of Lasers and Powder Beds
The success of PBF-LB hinges on the interplay between the laser and the metal powder bed. The laser’s energy must be precisely controlled to ensure that the metal powder melts uniformly, without causing defects like warping or porosity. The powder bed, typically composed of fine metal particles, must be evenly distributed and have the right flow characteristics to ensure consistent layer formation.
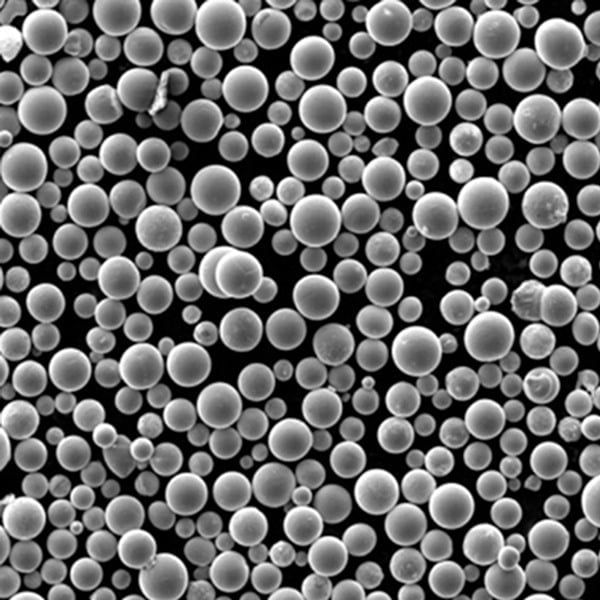
Types of Metal Powders Used in PBF-LB
Composition and Properties of Popular Metal Powders
Not all metal powders are created equal. The properties of the metal powder, including particle size, shape, and composition, directly influence the quality and performance of the final part. In PBF-LB, commonly used metal powders include:
- Titanium (Ti-6Al-4V): Known for its excellent strength-to-weight ratio and corrosion resistance, widely used in aerospace and medical implants.
- Stainless Steel (316L): Offers good corrosion resistance and mechanical properties, suitable for a wide range of industrial applications.
- Inconel (IN718): A nickel-based superalloy with exceptional high-temperature performance, often used in jet engines and gas turbines.
- Aluminum (AlSi10Mg): Lightweight and strong, ideal for automotive and aerospace applications where weight savings are critical.
- Cobalt-Chrome (CoCr): Highly resistant to wear and corrosion, commonly used in dental and orthopedic implants.
- Copper (Cu): Excellent thermal and electrical conductivity, used in electronics and heat exchangers.
- Maraging Steel (MS1): High-strength steel with good machinability, often used in tooling and aerospace components.
- Nickel Alloy (Hastelloy X): Resistant to oxidation and carburization, suitable for high-temperature applications.
- Tool Steel (H13): Offers high hardness and wear resistance, used in molds and dies.
- Tungsten (W): Extremely dense and heat-resistant, used in aerospace and military applications.
Specific Metal Powder Models with Descriptions
Now, let’s delve into specific models of these metal powders and what makes them unique:
- Ti-6Al-4V ELI: A grade of titanium alloy with extra-low interstitials, providing improved toughness and fracture resistance, ideal for medical implants.
- 316L Stainless Steel Fine Powder: Offers finer particles for enhanced surface finish and detail resolution, commonly used in high-precision applications.
- Inconel 718 Premium: A high-purity version of Inconel 718, offering superior mechanical properties and resistance to cracking in demanding environments.
- AlSi10Mg Enhanced: Modified for improved flowability and reduced porosity, ensuring consistent quality in large-scale production.
- CoCr-Mo: A cobalt-chrome-molybdenum alloy with enhanced wear resistance, particularly suitable for load-bearing implants.
- CuCrZr: A copper-chromium-zirconium alloy offering higher strength than pure copper, used in high-stress electronic components.
- MS1 Tool Steel: A maraging steel powder with optimized particle size distribution for improved print quality and mechanical performance.
- Hastelloy X Advanced: Features enhanced oxidation resistance and mechanical properties at elevated temperatures, ideal for extreme environments.
- H13 Tool Steel Plus: An upgraded tool steel with improved thermal fatigue resistance, perfect for demanding die-casting applications.
- W-Re Alloy: A tungsten-rhenium alloy offering better ductility and strength at high temperatures compared to pure tungsten.
Key Characteristics of Laser Beam Powder Bed Fusion (PBF-LB)
Material Properties: Strength, Durability, and More
The material properties of parts produced via PBF-LB are influenced by both the choice of metal powder and the specific process parameters used during printing. Some key material properties include:
- Tensile Strength: The maximum stress the material can withstand while being stretched or pulled. Materials like Ti-6Al-4V and Inconel 718 are known for their high tensile strength.
- Hardness: The resistance of the material to deformation, particularly permanent deformation like scratches or indentations. Tool steels like H13 excel in hardness.
- Ductility: The ability of the material to deform under tensile stress, often crucial in applications requiring flexibility, such as aerospace components.
- Thermal Conductivity: How well the material conducts heat, an important factor for applications involving high temperatures or thermal cycling. Copper is a standout in this category.
- Corrosion Resistance: The ability of the material to withstand degradation due to reactions with the environment, such as oxidation or rusting. Stainless steel 316L and cobalt-chrome alloys are highly valued for their corrosion resistance.
Surface Finish and Dimensional Accuracy
PBF-LB is renowned for its ability to produce parts with excellent surface finish and dimensional accuracy. However, these qualities are highly dependent on factors like:
- Powder Particle Size: Finer powders generally lead to smoother surfaces but may also require more precise handling and increased cost.
- Laser Parameters: The laser’s power, speed, and focus can all impact the final surface finish and accuracy. Optimizing these parameters is crucial for achieving the desired quality.
- Post-Processing: Techniques like machining, polishing, or heat treatment can be used to enhance the surface finish and dimensional accuracy of PBF-LB parts.
Advantages and Limitations of Laser Beam Powder Bed Fusion (PBF-LB)
Why Choose PBF-LB? A Look at the Benefits
PBF-LB offers several advantages that make it a preferred choice for high-precision manufacturing:
- Design Freedom: The ability to create complex geometries that are impossible with traditional manufacturing methods.
- Material Efficiency: Minimal waste, as material is only used where it is needed, reducing costs and environmental impact.
- Customization: Perfect for producing customized parts or low-volume production runs where traditional methods would be cost-prohibitive.
- Speed: Faster turnaround times compared to traditional manufacturing, especially for complex or highly detailed parts.
- High Precision: Exceptional accuracy and surface finish, making it ideal for components where tolerances are critical.
Limitations and Challenges of PBF-LB
Despite its many advantages, PBF-LB also has some limitations:
- Cost: The initial investment in PBF-LB equipment and materials can be high, making it less accessible for smaller operations.
- Material Limitations: Not all metals are suitable for PBF-LB, and the available metal powders can be expensive.
- Post-Processing Requirements: Parts often require significant post-processing to achieve the desired surface finish and mechanical properties.
- Build Size Constraints: The size of parts that can be produced is limited by the size of the build chamber, which may not be suitable for very large components.
- Technical Complexity: The process requires a deep understanding of both the technology and the materials involved, which can be a barrier to entry for some manufacturers.
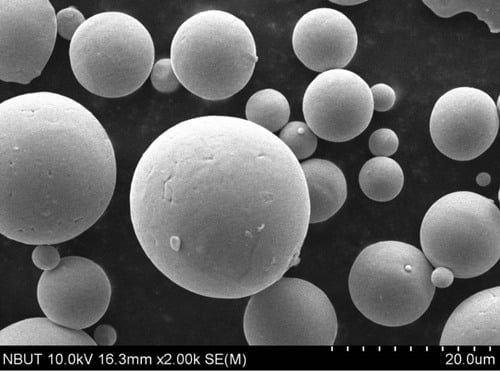
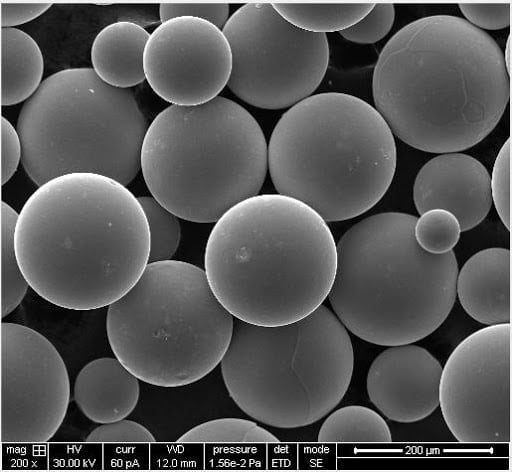
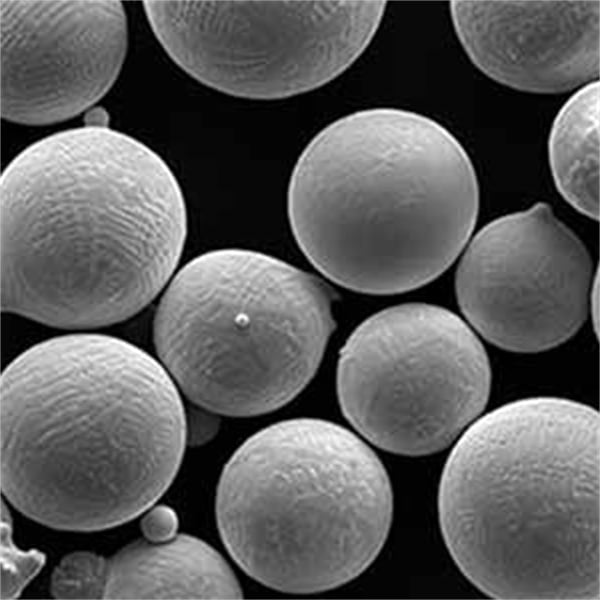
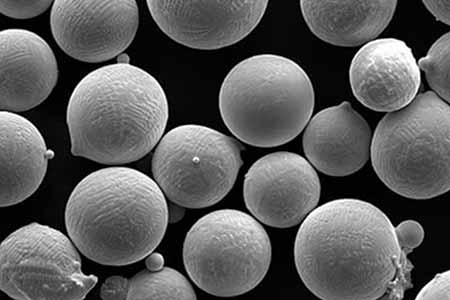
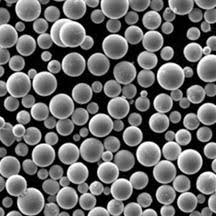
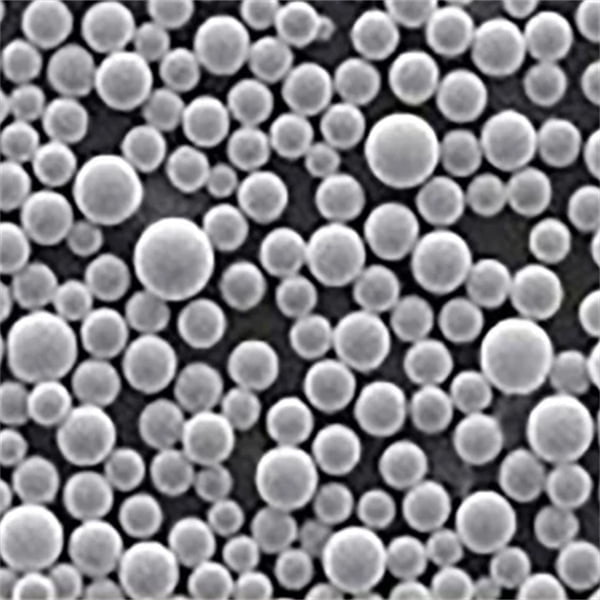
Applications of Laser Beam Powder Bed Fusion (PBF-LB)
Industries and Use Cases: Aerospace, Automotive, and Beyond
PBF-LB has found applications across a wide range of industries, thanks to its versatility and precision. Some notable examples include:
- Aerospace: The ability to produce lightweight, strong, and complex parts makes PBF-LB ideal for aerospace applications, such as turbine blades, engine components, and structural elements.
- Automotive: PBF-LB is used to create high-performance components like exhaust manifolds, heat exchangers, and custom engine parts, helping to reduce weight and improve fuel efficiency.
- Medical: Custom implants, prosthetics, and surgical instruments are commonly produced using PBF-LB, offering tailored solutions that match the patient’s unique anatomy.
- Energy: Components for gas turbines, oil and gas exploration, and renewable energy systems benefit from the high strength and temperature resistance of PBF-LB-produced parts.
- Tooling: The ability to produce intricate molds and dies with conformal cooling channels improves the efficiency and lifespan of tools used in manufacturing.
Future Potential: Expanding the Horizons of PBF-LB
The future of PBF-LB is bright, with ongoing research and development pushing the boundaries of what is possible. Emerging trends and potential future applications include:
- Multi-Material Printing: The ability to print with multiple materials in a single build, allowing for parts with varying properties or functionalities.
- Larger Build Volumes: Advances in machine design may allow for the production of larger parts, expanding the range of possible applications.
- Advanced Alloys: The development of new metal powders and alloys tailored specifically for PBF-LB could lead to improved part performance and new applications.
- Integration with AI and Machine Learning: Using AI to optimize the printing process and predict outcomes could lead to greater efficiency and consistency in PBF-LB production.
Specifications and Standards for PBF-LB
Understanding Size, Grades, and Standards
PBF-LB parts are often subject to strict specifications and standards to ensure they meet the required performance and safety criteria. Some key considerations include:
- Powder Size Distribution: The range of particle sizes in the metal powder, typically measured in microns. This affects the flowability and packing density of the powder.
- Powder Purity: The level of impurities in the metal powder, which can impact the mechanical properties and consistency of the final part.
- Build Volume: The maximum size of the part that can be produced, determined by the dimensions of the build chamber.
- Layer Thickness: The thickness of each layer of powder, typically ranging from 20 to 100 microns, which affects the surface finish and build time.
- Standards: Common standards for PBF-LB include ASTM F2924 for titanium alloys and ASTM F3055 for nickel alloys, among others.
Comparing Metal Powders: Pros and Cons
Comparing Different Metal Powders Used in PBF-LB
Choosing the right metal powder is crucial for the success of a PBF-LB project. Let’s compare some of the most popular options:
Metal Powder | Strengths | Weaknesses | Applications |
---|---|---|---|
Ti-6Al-4V | High strength-to-weight ratio, corrosion-resistant | Expensive, challenging to process | Aerospace, medical implants |
316L Stainless Steel | Good corrosion resistance, widely available | Lower strength compared to other alloys | Industrial, consumer goods |
Inconel 718 | Excellent high-temperature performance | High cost, difficult to machine | Aerospace, energy |
AlSi10Mg | Lightweight, good mechanical properties | Limited high-temperature performance | Automotive, aerospace |
CoCr | High wear resistance, biocompatible | Brittle, expensive | Medical, dental implants |
Copper | Excellent thermal and electrical conductivity | Difficult to process, prone to oxidation | Electronics, heat exchangers |
Maraging Steel (MS1) | High strength, good machinability | Susceptible to corrosion, requires heat treatment | Tooling, aerospace |
Hastelloy X | High oxidation resistance, good ductility | Expensive, limited availability | High-temperature environments |
H13 Tool Steel | High hardness, wear resistance | Prone to cracking, requires careful processing | Tooling, die-casting |
Tungsten | Extremely dense, heat-resistant | Difficult to process, heavy | Aerospace, military applications |
Suppliers and Pricing of Metal Powders for PBF-LB
Top Suppliers of Metal Powders
Several companies specialize in producing high-quality metal powders for PBF-LB. Here are some of the leading suppliers:
Supplier | Metal Powders Offered | Specialization | Location |
---|---|---|---|
Höganäs AB | Ti-6Al-4V, 316L Stainless Steel, Inconel 718 | Wide range of metal powders, high-quality standards | Sweden |
LPW Technology | AlSi10Mg, Inconel 718, CoCr | Focus on additive manufacturing, customized powder solutions | UK |
Sandvik | 316L Stainless Steel, Hastelloy X, Maraging Steel | High-performance alloys, advanced manufacturing capabilities | Sweden |
GKN Additive | Ti-6Al-4V, AlSi10Mg, H13 Tool Steel | Specializes in metal powders for additive manufacturing | Germany |
Carpenter Technology | Ti-6Al-4V, 316L Stainless Steel, Copper | Wide range of metal powders, focus on aerospace and medical | USA |
Praxair Surface Technologies | Inconel 718, CoCr, H13 Tool Steel | High-purity powders, extensive experience in aerospace | USA |
AP&C (GE Additive) | Ti-6Al-4V, AlSi10Mg, Inconel 718 | Specializes in titanium and aluminum alloys, high-quality control | Canada |
Aubert & Duval | Hastelloy X, Maraging Steel, Tungsten | High-performance alloys, focus on aerospace and energy | France |
Arcam (GE Additive) | Ti-6Al-4V, AlSi10Mg, Inconel 718 | Focus on electron beam melting, high-purity powders | Sweden |
Tekna | Ti-6Al-4V, Inconel 718, CoCr | Focus on plasma atomization, high-quality metal powders | Canada |
Pricing Details and Availability
The cost of metal powders for PBF-LB can vary widely depending on factors like material type, particle size, and purity. Here is a general price range for some common metal powders:
Metal Powder | Approximate Price (per kg) | Availability |
---|---|---|
Ti-6Al-4V | $300 – $500 | Widely available, high demand |
316L Stainless Steel | $50 – $100 | Widely available, relatively affordable |
Inconel 718 | $200 – $400 | Available, high demand in aerospace |
AlSi10Mg | $60 – $120 | Widely available, used in various industries |
CoCr | $300 – $600 | Available, used in medical and dental applications |
Copper | $100 – $200 | Available, specialized use in electronics |
Maraging Steel (MS1) | $100 – $200 | Available, used in tooling and aerospace |
Hastelloy X | $400 – $800 | Available, high cost due to specialized use |
H13 Tool Steel | $80 – $150 | Available, used in die-casting and tooling |
Tungsten | $500 – $1000 | Available, high cost due to density and processing challenges |
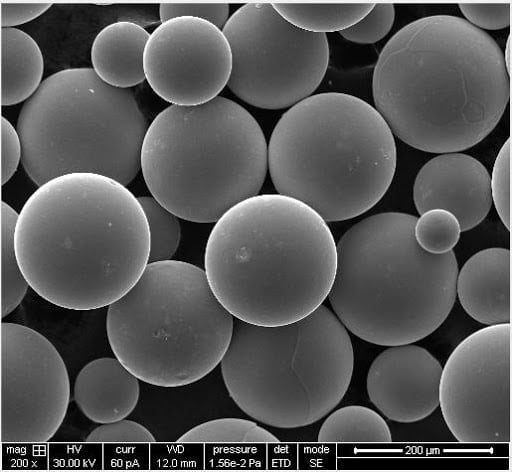
FAQ
Question | Answer |
---|---|
What is Laser Beam Powder Bed Fusion (PBF-LB)? | PBF-LB is an additive manufacturing process that uses a high-powered laser to selectively melt and fuse metal powders, layer by layer, to create complex 3D parts. |
What materials can be used in PBF-LB? | Common materials include titanium alloys, stainless steel, Inconel, aluminum alloys, cobalt-chrome, copper, and tool steels, among others. |
What are the advantages of PBF-LB? | PBF-LB offers design freedom, material efficiency, customization, speed, and high precision, making it ideal for complex and high-performance parts. |
What are the limitations of PBF-LB? | Limitations include high cost, material restrictions, post-processing requirements, build size constraints, and technical complexity. |
Which industries use PBF-LB? | PBF-LB is widely used in aerospace, automotive, medical, energy, and tooling industries, among others. |
How does the choice of metal powder affect PBF-LB? | The choice of metal powder impacts the material properties, surface finish, and overall quality of the final part, making it crucial to select the right powder for the application. |
What is the future of PBF-LB? | The future of PBF-LB includes advancements in hybrid manufacturing, AI integration, new metal alloys, in-situ monitoring, and sustainability initiatives. |
Conclusion
Laser Beam Powder Bed Fusion (PBF-LB) is a revolutionary technology that is transforming the landscape of additive manufacturing. With its ability to produce complex, high-performance metal parts with precision and efficiency, PBF-LB is finding applications across a wide range of industries, from aerospace to medical devices. As the technology continues to evolve, driven by innovations in metal powders, process optimization, and sustainability, the future of PBF-LB looks incredibly promising.
Whether you’re an engineer, a manufacturer, or simply someone interested in the cutting-edge world of 3D printing, understanding the intricacies of PBF-LB is key to staying ahead in this rapidly evolving field. With the right knowledge, materials, and tools, the possibilities of what can be achieved with PBF-LB are virtually limitless.
About 3DP mETAL
Product Category
CONTACT US
Any questions? Send us a message now! After receiving your message, we will process your request with a whole team.