Additive manufacturing is revolutionizing the world of manufacturing by enabling the creation of complex, highly detailed parts directly from digital designs. Among the various additive manufacturing techniques, Laser Powder Bed Fusion (LPBF) has emerged as one of the most popular methods, particularly in the production of metal components. But what exactly is LPBF, and how does it work? In this comprehensive guide, we’ll delve deep into the world of LPBF, exploring its process, materials, applications, advantages, and limitations. We’ll also take a closer look at specific metal powders used in LPBF and compare them across various parameters.
Overview of Laser Powder Bed Fusion (LPBF)
Laser Powder Bed Fusion is an advanced additive manufacturing process that uses a high-powered laser to selectively fuse fine metal powder particles together, layer by layer, to create a solid, three-dimensional object. This technology is part of a broader category of additive manufacturing processes known as powder bed fusion (PBF), which also includes electron beam melting (EBM) and selective laser sintering (SLS). However, LPBF is unique in its ability to produce high-resolution metal parts with intricate geometries and superior mechanical properties.
LPBF is widely used across various industries, including aerospace, automotive, medical, and industrial manufacturing, where precision, strength, and material efficiency are paramount. This technique allows for the production of complex metal parts that would be impossible or prohibitively expensive to manufacture using traditional methods like machining or casting.
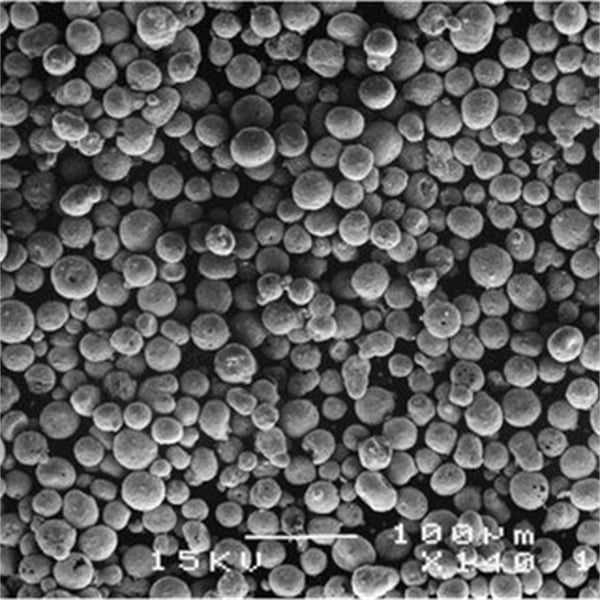
How Laser Powder Bed Fusion Works
LPBF involves several key steps, from design to final product. Here’s an overview of the process:
- Digital Design Creation: The process begins with the creation of a digital 3D model using computer-aided design (CAD) software. This model serves as the blueprint for the object to be manufactured.
- Powder Spreading: A thin layer of metal powder, typically ranging from 20 to 100 microns in thickness, is evenly spread across the build platform. The powder is kept in a reservoir and spread using a recoater blade or roller.
- Laser Scanning: A high-powered laser beam selectively fuses the powder particles together according to the digital design. The laser is guided by a set of mirrors, known as galvos, which precisely control the laser’s movement across the powder bed.
- Layer-by-Layer Building: After one layer is fused, the build platform lowers by the thickness of one layer, and a new layer of powder is spread. The laser then fuses the new layer, bonding it to the previous one. This process repeats until the entire object is built.
- Post-Processing: Once the build is complete, the excess powder is removed, and the part is subjected to various post-processing steps, such as heat treatment, machining, or surface finishing, to achieve the desired properties and surface quality.
- Final Inspection: The finished part undergoes thorough inspection and testing to ensure it meets the required specifications and quality standards.
Key Benefits of Laser Powder Bed Fusion
LPBF offers several advantages over traditional manufacturing methods and other additive manufacturing techniques:
- Design Flexibility: LPBF enables the creation of highly complex geometries that would be impossible to produce using conventional methods. This includes internal structures, lattices, and intricate details that can be optimized for weight, strength, and functionality.
- Material Efficiency: Since LPBF is an additive process, it only uses the material necessary to build the part, resulting in minimal waste. This contrasts with subtractive methods like machining, where material is removed from a larger block, often resulting in significant waste.
- High Precision: LPBF can produce parts with extremely tight tolerances and fine details, making it ideal for applications where precision is critical.
- Rapid Prototyping: LPBF allows for the quick production of prototypes, enabling faster design iterations and reducing the time to market for new products.
- Strong, Functional Parts: LPBF produces parts with mechanical properties comparable to those made using traditional manufacturing methods. This makes it suitable for producing functional end-use components, not just prototypes.
Composition of Metal Powders Used in Laser Powder Bed Fusion
The quality and composition of the metal powder used in LPBF are crucial to the success of the process and the properties of the final part. Below, we’ll explore some of the most commonly used metal powders in LPBF, along with their specific compositions and properties.
Metal Powder | Composition | Properties | Applications |
---|---|---|---|
316L Stainless Steel | Fe, Cr (16-18%), Ni (10-14%), Mo (2-3%) | High corrosion resistance, good mechanical properties, weldable | Medical implants, food processing equipment, marine parts |
AlSi10Mg | Al (balance), Si (9-11%), Mg (0.2-0.5%) | High strength-to-weight ratio, good thermal conductivity | Aerospace components, automotive parts, heat exchangers |
Inconel 718 | Ni (50-55%), Cr (17-21%), Fe (balance) | High temperature resistance, excellent strength and corrosion resistance | Gas turbines, aerospace parts, nuclear reactors |
Ti6Al4V | Ti (90%), Al (6%), V (4%) | High strength-to-weight ratio, excellent biocompatibility | Medical implants, aerospace components, high-performance automotive parts |
Maraging Steel (1.2709) | Fe, Ni (18-19%), Co (8.5-9.5%), Mo (4.5-5.2%), Ti (0.6-0.8%) | High strength, toughness, easy to machine | Tooling, aerospace components, high-strength parts |
Cobalt-Chrome (CoCr) | Co (balance), Cr (27-30%), Mo (5-7%) | High wear and corrosion resistance, biocompatible | Dental implants, medical devices, turbine blades |
Hastelloy X | Ni (47%), Cr (22%), Mo (9%), Fe (18%) | Excellent high-temperature strength, corrosion resistance | Aerospace, chemical processing, gas turbines |
Copper (Cu) | Cu (99.9%) | High thermal and electrical conductivity | Electrical components, heat exchangers, inductors |
Aluminum 6061 | Al (97.9-99%), Mg (0.8-1.2%), Si (0.4-0.8%) | High strength-to-weight ratio, good corrosion resistance | Structural components, automotive parts, aerospace |
Tool Steel (H13) | Fe, Cr (4.75-5.5%), Mo (1.1-1.75%), V (0.8-1.2%) | High hardness, wear resistance, toughness | Tooling, molds, dies, high-strength components |
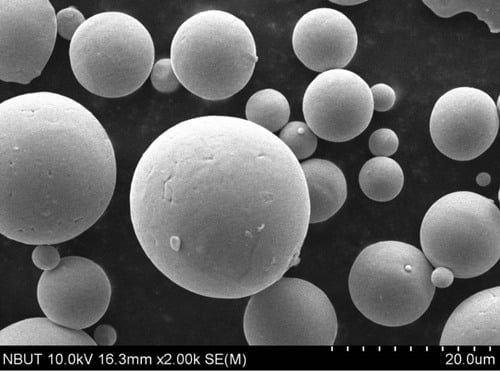
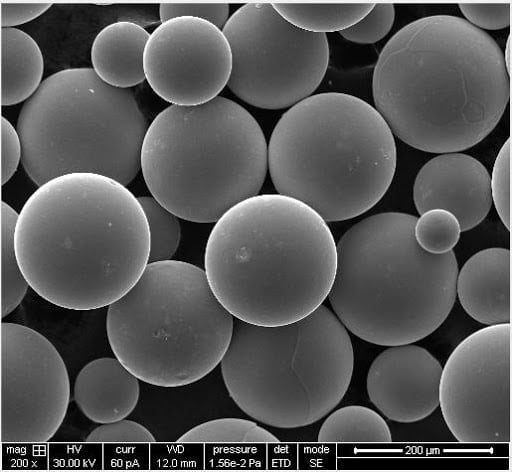
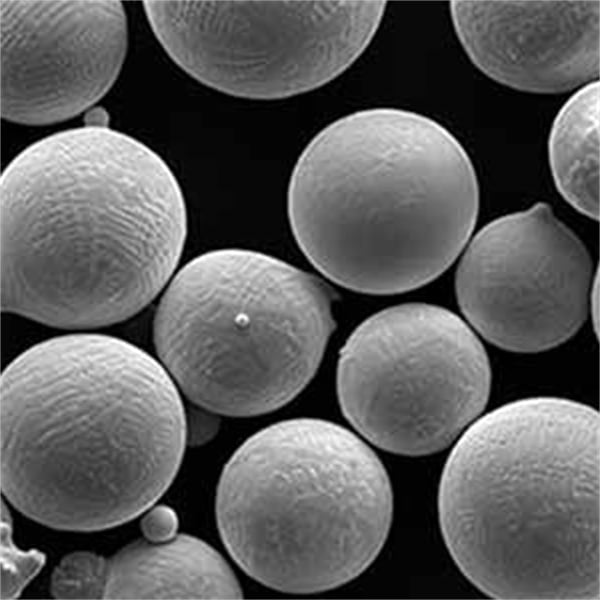
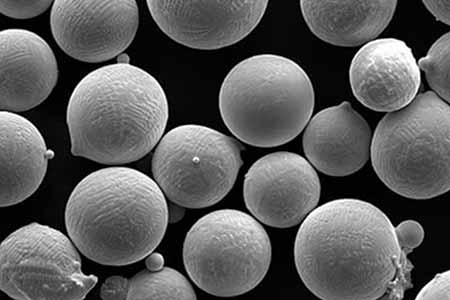
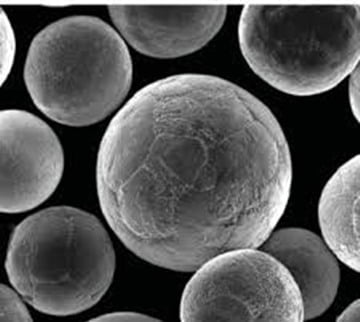
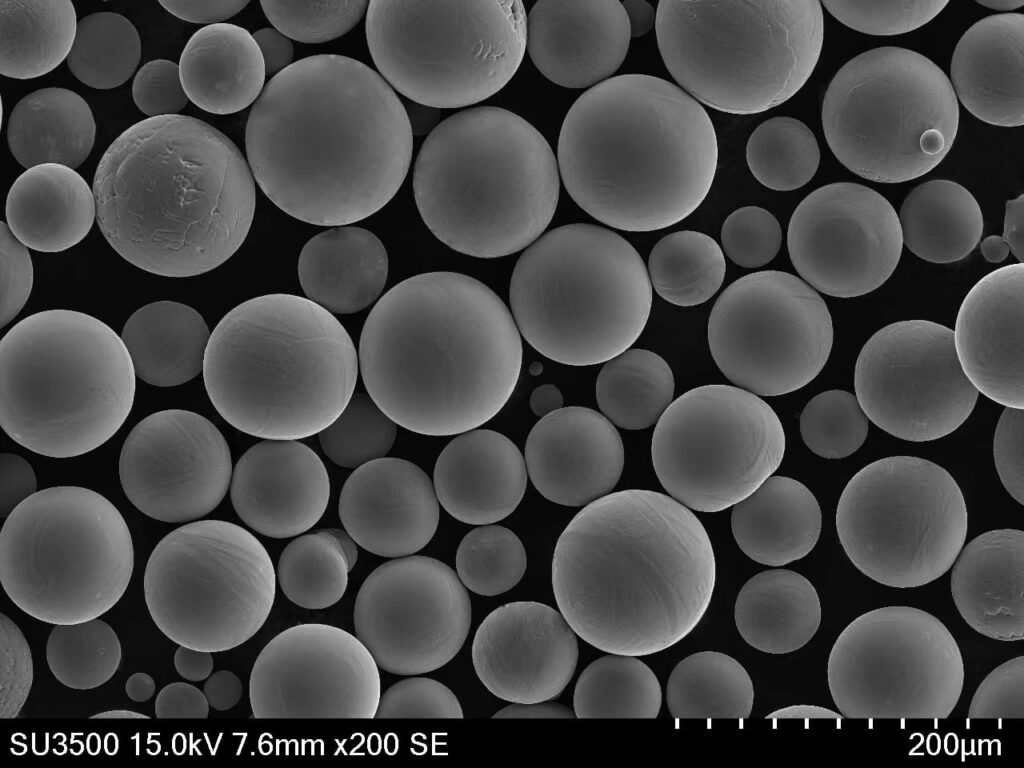
Characteristics of Laser Powder Bed Fusion Materials
When selecting a metal powder for LPBF, it’s essential to consider the material’s characteristics and how they align with the requirements of the application. Here are some of the critical characteristics to consider:
- Particle Size Distribution: The size and distribution of powder particles significantly impact the flowability and packing density of the powder, which in turn affects the quality of the final part. A narrow particle size distribution is generally preferred for consistent layer deposition and optimal part density.
- Morphology: The shape of the powder particles (e.g., spherical, irregular) influences the flowability and packing density of the powder. Spherical particles are generally preferred in LPBF because they flow better and pack more densely, leading to higher-quality parts.
- Chemical Composition: The chemical composition of the powder directly affects the mechanical properties, corrosion resistance, and other performance characteristics of the final part. It’s crucial to use powders with a consistent and controlled composition to achieve the desired material properties.
- Purity: High-purity powders are essential for producing parts with consistent mechanical properties and minimizing the risk of defects. Impurities can lead to issues such as porosity, poor mechanical performance, and reduced corrosion resistance.
- Flowability: The ability of the powder to flow smoothly and evenly during the recoating process is critical to achieving uniform layer thickness and high-quality parts. Poor flowability can result in inconsistent layers, defects, and reduced part quality.
- Reactivity: Some metal powders, particularly those containing aluminum, titanium, or magnesium, are highly reactive and require careful handling and storage to prevent oxidation or contamination. Inert gas environments are often used during the LPBF process to mitigate these risks.
Applications of Laser Powder Bed Fusion
LPBF is a versatile technology that finds applications in a wide range of industries. Here are some of the key applications where LPBF is making a significant impact:
Industry | Application | Details |
---|---|---|
Aerospace | Turbine blades, structural components | High-temperature alloys like Inconel 718 and Hastelloy X are used for their strength and heat resistance |
Automotive | Engine components, lightweight structures | Aluminum alloys and titanium are used to reduce weight while maintaining strength |
Medical | Implants, surgical instruments | Biocompatible materials like Ti6Al4V and Cobalt-Chrome are used for their strength and compatibility |
Dental | Crowns, bridges, dental implants | Cobalt-Chrome and titanium are commonly used for their biocompatibility and strength |
Tooling | Molds, dies, cutting tools | Tool steels like H13 and Maraging Steel are used for their hardness and wear resistance |
Energy | Heat exchangers, turbine components | Copper and nickel-based superalloys are used for their thermal conductivity and high-temperature performance |
Jewelry | Custom designs, intricate details | Precious metals like gold and silver can be used to create unique, detailed pieces |
Electronics | Heat sinks, connectors, inductors | Copper and aluminum alloys are used for their excellent thermal and electrical conductivity |
Defense | Lightweight armor, specialized components | High-strength materials like titanium and Inconel are used for their durability and weight savings |
Research & Development | Prototyping, material testing | Various materials are used to explore new applications and push the boundaries of what LPBF can achieve |
Advantages and Limitations of Laser Powder Bed Fusion
While LPBF offers numerous advantages, it also has its limitations. Understanding these pros and cons is essential when deciding whether LPBF is the right technology for a particular application.
Advantages | Limitations |
---|---|
Design Freedom: Ability to create complex, intricate geometries that are impossible with traditional methods | Cost: High initial investment in equipment and materials |
Material Efficiency: Minimal waste due to additive nature of the process | Build Size Limitations: Limited by the size of the build chamber |
High Precision: Capable of producing parts with tight tolerances and fine details | Post-Processing Requirements: Parts often require additional post-processing |
Strong Functional Parts: Mechanical properties comparable to traditionally manufactured parts | Limited Material Options: Not all materials are suitable for LPBF |
Rapid Prototyping: Quick turnaround from design to finished part | Surface Finish: Parts may require surface finishing to achieve desired quality |
Customization: Ability to produce customized, one-off parts economically | Powder Handling: Requires careful handling and storage of metal powders due to reactivity and safety concerns |
Specifications, Sizes, Grades, and Standards for LPBF Materials
When working with LPBF, it’s essential to understand the specifications, sizes, grades, and standards that apply to the materials used in the process. Here is an overview of some of the key considerations:
Material | Size Range (Microns) | Common Grades | Standards |
---|---|---|---|
316L Stainless Steel | 15-45, 45-105 | ASTM A240, A276, A312 | ASTM F3184, ISO 5832-1 |
AlSi10Mg | 20-63, 45-105 | EN AW-6082, EN AW-5083 | DIN EN 1706, ISO 3522 |
Inconel 718 | 15-45, 45-105 | AMS 5662, AMS 5663 | ASTM F3055, ISO 15156 |
Ti6Al4V | 15-45, 45-105 | ASTM B348, ASTM F136 | ASTM F2924, ISO 5832-3 |
Maraging Steel (1.2709) | 15-45, 45-105 | DIN 1.2709, AMS 6514 | ASTM A579, ISO 4957 |
Cobalt-Chrome (CoCr) | 15-45, 45-105 | ASTM F75, F1537 | ASTM F2924, ISO 5832-4 |
Hastelloy X | 15-45, 45-105 | AMS 5754, AMS 5536 | ASTM B435, ASTM B572 |
Copper (Cu) | 15-45, 45-105 | C11000, C10100 | ASTM B170, ASTM B152 |
Aluminum 6061 | 15-45, 45-105 | ASTM B221, ASTM B308 | ASTM F3318, ISO 3522 |
Tool Steel (H13) | 15-45, 45-105 | ASTM A681, JIS SKD61 | ASTM A681, ISO 4957 |
Suppliers and Pricing Details for LPBF Metal Powders
Finding reliable suppliers and understanding the pricing structure for LPBF metal powders is crucial for planning and budgeting. Here’s an overview of some well-known suppliers and the price range for different types of metal powders:
Supplier | Metal Powder | Price Range (per kg) | Details |
---|---|---|---|
Höganäs | Stainless Steel, Tool Steel, Titanium | $80 – $200 | Offers a wide range of metal powders for LPBF |
Carpenter Additive | Nickel Alloys, Stainless Steel, Titanium | $100 – $250 | Known for high-quality, aerospace-grade powders |
Sandvik Additive Manufacturing | Stainless Steel, Titanium, Cobalt-Chrome | $90 – $230 | Provides metal powders optimized for additive manufacturing |
GKN Additive | Stainless Steel, Aluminum, Tool Steel | $70 – $180 | Offers metal powders tailored for LPBF applications |
LPW Technology (Carpenter) | Inconel, Maraging Steel, Aluminum | $110 – $300 | Specializes in high-performance powders for critical applications |
AP&C (GE Additive) | Titanium, Aluminum, Nickel Alloys | $120 – $350 | High-quality powders with a focus on aerospace and medical applications |
Tekna | Titanium, Aluminum, Nickel Alloys | $100 – $320 | Advanced powders with controlled particle sizes |
EOS | Various (Nickel, Aluminum, Stainless) | $90 – $250 | Offers a variety of metal powders designed specifically for EOS machines |
Renishaw | Stainless Steel, Titanium, Inconel | $100 – $270 | Known for consistent, high-quality powders |
Aubert & Duval | Titanium, Aluminum, Tool Steel | $110 – $300 | Specializes in metal powders for high-stress applications |
Comparing Pros and Cons of Different Metal Powders for LPBF
When selecting a metal powder for LPBF, it’s essential to weigh the pros and cons of each option. Below is a comparative table highlighting the advantages and limitations of some of the most commonly used metal powders:
Metal Powder | Advantages | Limitations |
---|---|---|
316L Stainless Steel | Excellent corrosion resistance, good mechanical properties, easy to weld | Relatively lower strength compared to other alloys |
AlSi10Mg | High strength-to-weight ratio, good thermal conductivity, lightweight | Lower corrosion resistance compared to stainless steel |
Inconel 718 | High temperature resistance, excellent strength and corrosion resistance | Expensive, challenging to machine |
Ti6Al4V | High strength-to-weight ratio, excellent biocompatibility, good corrosion resistance | Expensive, highly reactive, requires inert gas environment |
Maraging Steel (1.2709) | High strength, toughness, easy to machine | Susceptible to corrosion, requires heat treatment |
Cobalt-Chrome (CoCr) | High wear and corrosion resistance, biocompatible | Expensive, hard to machine, limited availability |
Hastelloy X | Excellent high-temperature strength, corrosion resistance | Expensive, difficult to machine, limited availability |
Copper (Cu) | High thermal and electrical conductivity, easy to work with | High reactivity, oxidation risk, challenging to process with LPBF |
Aluminum 6061 | High strength-to-weight ratio, good corrosion resistance, lightweight | Lower strength compared to other aluminum alloys, not as heat-resistant as Inconel or Titanium |
Tool Steel (H13) | High hardness, wear resistance, toughness, good for tooling applications | Prone to cracking during processing, requires heat treatment |
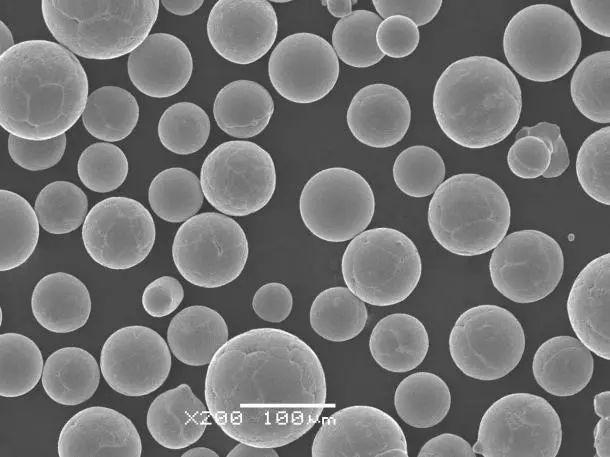
FAQs
To further enhance your understanding of Laser Powder Bed Fusion, we’ve compiled a list of frequently asked questions along with detailed answers.
Question | Answer |
---|---|
What is Laser Powder Bed Fusion (LPBF)? | LPBF is an additive manufacturing process that uses a laser to fuse metal powder layer by layer to create a solid object. |
What are the common materials used in LPBF? | Common materials include stainless steel, aluminum alloys, titanium alloys, Inconel, maraging steel, and cobalt-chrome. |
How does LPBF differ from other additive manufacturing methods? | LPBF is unique in its ability to produce high-resolution metal parts with intricate geometries, using a laser to fuse the powder. |
What are the advantages of using LPBF for manufacturing? | Advantages include design flexibility, material efficiency, high precision, rapid prototyping, and the ability to produce strong, functional parts. |
What are the limitations of LPBF? | Limitations include high costs, build size restrictions, post-processing requirements, and the need for specialized materials. |
How do I choose the right metal powder for LPBF? | Consider factors like particle size distribution, morphology, chemical composition, purity, flowability, and reactivity. |
What industries benefit most from LPBF? | Industries like aerospace, automotive, medical, dental, tooling, energy, and electronics benefit greatly from LPBF. |
Is LPBF suitable for mass production? | While LPBF is excellent for prototyping and small to medium production runs, it may not be the most cost-effective option for high-volume production. |
How does the quality of the metal powder affect the final part? | The quality of the metal powder impacts the mechanical properties, surface finish, and overall performance of the final part. |
Can LPBF produce multi-material parts? | LPBF is primarily used for single-material parts, but there are ongoing developments in multi-material printing technologies. |
Conclusion
Laser Powder Bed Fusion is a powerful additive manufacturing technology that offers unparalleled design freedom, material efficiency, and the ability to produce high-quality metal parts with complex geometries. While it comes with its challenges and limitations, LPBF continues to advance, making it an increasingly viable option for a wide range of applications across various industries. Whether you’re looking to prototype a new design, produce custom parts, or explore the possibilities of metal additive manufacturing, LPBF is a technology worth considering.
As the field of additive manufacturing continues to evolve, we can expect to see further improvements in LPBF technology, including new materials, larger build sizes, and enhanced process control. Staying informed about these developments will be key to leveraging the full potential of LPBF in your manufacturing endeavors.
About 3DP mETAL
Product Category
CONTACT US
Any questions? Send us a message now! After receiving your message, we will process your request with a whole team.