Laser rapid prototyping (LRP) has revolutionized the way we approach design and manufacturing. From intricate jewelry pieces to robust aerospace components, this technology enables the creation of high-precision models at a speed and accuracy that traditional methods can’t match. But what exactly is laser rapid prototyping, and how does it work? Buckle up, as we dive into the depths of this fascinating technology, explore its intricacies, and unveil the secrets behind its efficacy.
Overview of Laser Rapid Prototyping
Laser rapid prototyping is a type of additive manufacturing (AM) process that uses laser technology to create three-dimensional objects from digital models. This process involves laying down successive layers of material, typically metal powder, and fusing them together using a high-powered laser beam. The result is a highly detailed and precise prototype that closely mimics the final product.
The appeal of LRP lies in its ability to produce complex geometries and fine details with minimal material waste. It’s like a magical 3D printer but on steroids. Now, let’s take a closer look at the specific metal powders used in this process.
Metal Powders Used in Laser Rapid Prototyping
To achieve the best results in laser rapid prototyping, selecting the right metal powder is crucial. Here’s a rundown of some of the most popular metal powders, their composition, properties, and applications.
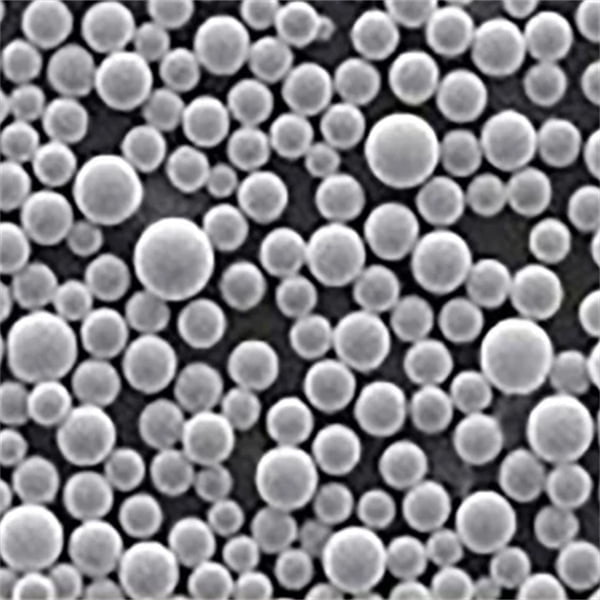
Popular Metal Powders for Laser Rapid Prototyping
Metal Powder | Composition | Properties | Applications |
---|---|---|---|
Titanium (Ti64) | 90% Ti, 6% Al, 4% V | Lightweight, high strength, corrosion-resistant | Aerospace, medical implants, automotive |
Stainless Steel (316L) | Iron, Chromium, Nickel, Molybdenum | High strength, corrosion resistance, good mechanical properties | Tooling, medical devices, food industry |
Aluminum (AlSi10Mg) | 90% Al, 10% Si, <1% Mg | Lightweight, good thermal properties, corrosion-resistant | Aerospace, automotive, consumer goods |
Inconel (IN718) | Nickel, Chromium, Iron, Molybdenum | High strength at high temperatures, oxidation-resistant | Aerospace, gas turbines, automotive |
Cobalt-Chrome (CoCr) | Cobalt, Chromium, Molybdenum | High strength, wear-resistant, biocompatible | Dental implants, medical devices, aerospace |
Maraging Steel (MS1) | Iron, Nickel, Cobalt, Molybdenum | High strength, good hardness, easily machinable | Tooling, aerospace, high-performance engineering parts |
Copper (Cu) | Pure Copper | Excellent thermal and electrical conductivity | Electronics, thermal management, automotive |
Bronze | Copper, Tin | Good mechanical properties, wear-resistant | Artistic sculptures, electrical connectors |
Nickel Alloy (Ni625) | Nickel, Chromium, Molybdenum, Niobium | High strength, corrosion-resistant, good weldability | Chemical processing, marine applications |
Tool Steel (H13) | Iron, Chromium, Molybdenum, Vanadium | High hardness, good toughness, heat-resistant | Tooling, die casting, injection molding |
Characteristics and Composition of Metal Powders
When it comes to the characteristics and composition of these metal powders, understanding the specifics can help you make informed decisions about their use.
Metal Powder | Particle Size (Microns) | Bulk Density (g/cm³) | Flowability (s/50g) | Melting Point (°C) |
---|---|---|---|---|
Titanium (Ti64) | 15-45 | 4.5 | 30 | 1660 |
Stainless Steel (316L) | 10-45 | 7.9 | 25 | 1400 |
Aluminum (AlSi10Mg) | 20-63 | 2.7 | 18 | 660 |
Inconel (IN718) | 15-53 | 8.2 | 28 | 1290 |
Cobalt-Chrome (CoCr) | 10-45 | 8.3 | 30 | 1350 |
Maraging Steel (MS1) | 10-45 | 8.1 | 25 | 1413 |
Copper (Cu) | 15-45 | 8.9 | 32 | 1084 |
Bronze | 20-45 | 8.8 | 30 | 950 |
Nickel Alloy (Ni625) | 10-45 | 8.4 | 28 | 1350 |
Tool Steel (H13) | 10-45 | 7.8 | 27 | 1420 |
Applications of Laser Rapid Prototyping
Laser rapid prototyping is widely used across various industries due to its versatility and precision. Let’s explore some common applications.
Applications and Uses of Laser Rapid Prototyping
Industry | Application | Description |
---|---|---|
Aerospace | Turbine Blades | High-strength, lightweight components with complex geometries |
Medical | Implants | Custom-fit, biocompatible implants for better patient outcomes |
Automotive | Prototypes | Rapid development and testing of new parts and designs |
Electronics | Heat Sinks | Efficient thermal management components |
Jewelry | Custom Pieces | Intricate designs and personalized jewelry items |
Tooling | Molds and Dies | Durable and precise tooling components for manufacturing |
Consumer Goods | Prototypes | Rapid iteration and testing of new product designs |
Defense | Components | High-performance parts for military applications |
Art | Sculptures | Detailed and complex artistic creations |
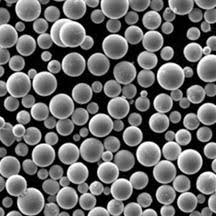
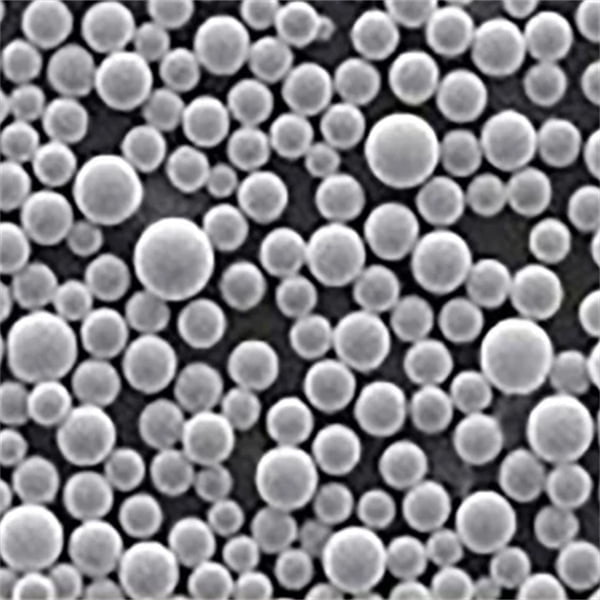
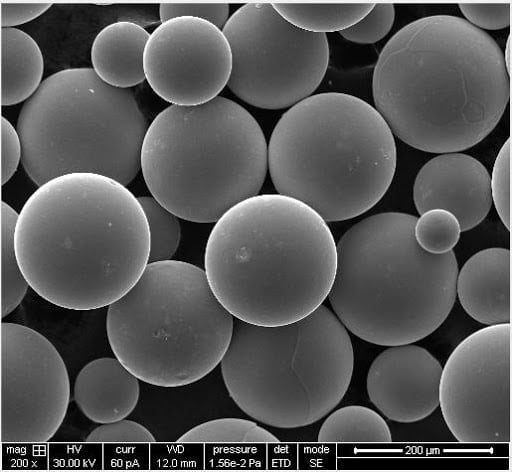
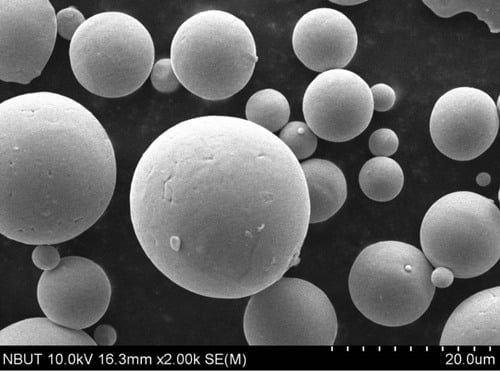
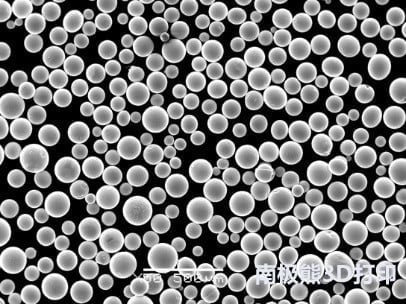
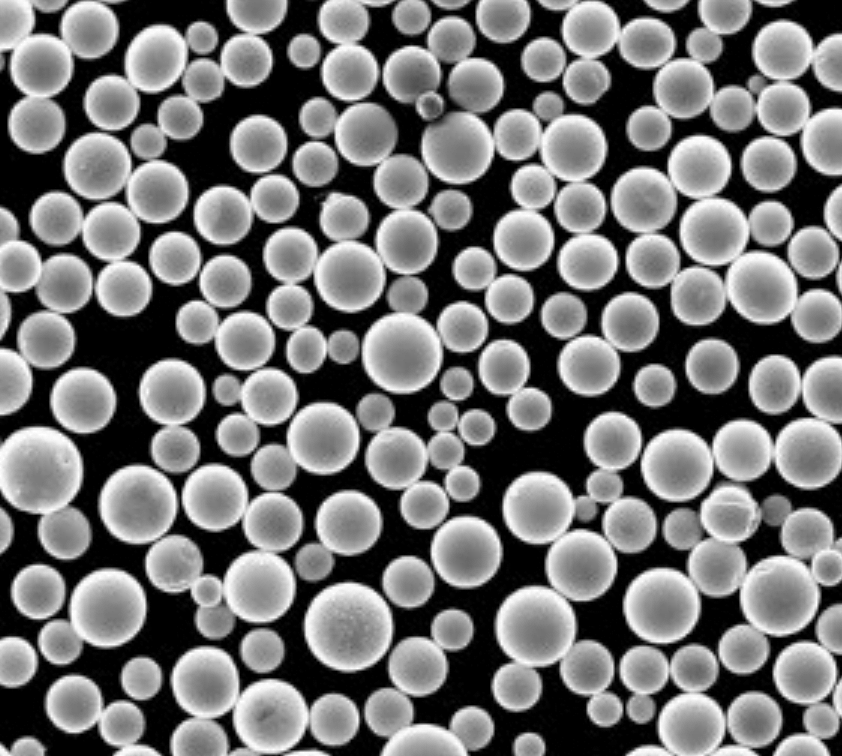
Specifications, Sizes, Grades, and Standards
Knowing the specifications, sizes, grades, and standards of metal powders used in laser rapid prototyping can help ensure that the right materials are chosen for specific applications.
Metal Powder | Size Range (Microns) | Grade | Standard |
---|---|---|---|
Titanium (Ti64) | 15-45 | Grade 5 | ASTM B348 |
Stainless Steel (316L) | 10-45 | 316L | ASTM A276 |
Aluminum (AlSi10Mg) | 20-63 | AlSi10Mg | DIN EN 1706 |
Inconel (IN718) | 15-53 | IN718 | ASTM B637 |
Cobalt-Chrome (CoCr) | 10-45 | CoCr | ISO 5832-4 |
Maraging Steel (MS1) | 10-45 | MS1 | AMS 6514 |
Copper (Cu) | 15-45 | OFHC | ASTM B170 |
Bronze | 20-45 | C93200 | ASTM B505 |
Nickel Alloy (Ni625) | 10-45 | Ni625 | ASTM B446 |
Tool Steel (H13) | 10-45 | H13 | ASTM A681 |
Suppliers and Pricing Details
Knowing where to source these metal powders and their pricing can be crucial for budgeting and procurement.
Supplier | Metal Powder | Price (USD/kg) | Contact Details |
---|---|---|---|
EOS | Titanium (Ti64) | $500 | www.eos.info |
Sandvik | Stainless Steel (316L) | $60 | www.materials.sandvik |
Carpenter Technology | Aluminum (AlSi10Mg) | $80 | www.cartech.com |
Höganäs | Inconel (IN718) | $300 | www.hoganas.com |
3D Systems | Cobalt-Chrome (CoCr) | $450 | www.3dsystems.com |
GKN Additive | Maraging Steel (MS1) | $200 | www.gkn.com |
Metal Powder Industries Federation | Copper (Cu) | $60 | www.mpif.org |
PyroGenesis | Bronze | $50 | www.pyrogenesis.com |
Praxair | Nickel Alloy (Ni625) | $350 | www.praxair.com |
Höganäs | Tool Steel (H13) | $100 | www.hoganas.com |
Advantages and Limitations of Laser Rapid Prototyping
Like any technology, laser rapid prototyping has its pros and cons. Understanding these can help you determine if it’s the right solution for your needs.
Pros and Cons of Laser Rapid Prototyping
Aspect | Advantages | Limitations |
---|---|---|
Speed | Faster production of prototypes compared to traditional methods | Higher initial setup costs |
Precision | High accuracy and detail in complex geometries | Limited build size depending on machine capabilities |
Material Efficiency | Minimal waste due to additive process | Limited material choices compared to traditional methods |
Customization | Easy customization and iteration | Requires expertise in CAD and laser technology |
Strength | Can produce strong, durable parts | Surface finish may require post-processing |
Versatility | Applicable across various industries | High energy consumption |
Comparing Laser Rapid Prototyping with Other Technologies
When compared to other prototyping and manufacturing technologies, laser rapid prototyping offers unique benefits and some trade-offs.
Technology | Pros | Cons |
---|---|---|
CNC Machining | High precision, suitable for large parts | Material waste, longer setup time |
Injection Molding | High production rate, low cost per part for large volumes | High initial mold cost, not suitable for prototypes |
Fused Deposition Modeling (FDM) | Low cost, easy to use | Lower precision and surface finish, limited material strength |
Stereolithography (SLA) | High detail and surface finish | Limited to photopolymer materials, post-processing needed |
Selective Laser Sintering (SLS) | Good mechanical properties, no support structures needed | Rough surface finish, limited material options |
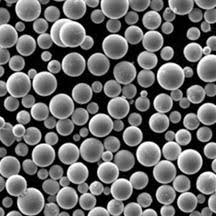
FAQ
Here are some frequently asked questions about laser rapid prototyping, answered in a straightforward and informative manner.
Question | Answer |
---|---|
What is laser rapid prototyping? | Laser rapid prototyping is an additive manufacturing process that uses lasers to fuse metal powder into precise, detailed 3D objects. |
How does laser rapid prototyping work? | It involves spreading a layer of metal powder and using a laser to melt and fuse the powder layer by layer to create a 3D object. |
What materials can be used in laser rapid prototyping? | Common materials include titanium, stainless steel, aluminum, Inconel, cobalt-chrome, maraging steel, copper, bronze, and nickel alloys. |
What are the advantages of laser rapid prototyping? | High precision, fast production, minimal material waste, and the ability to create complex geometries are some of the key advantages. |
Are there any limitations to laser rapid prototyping? | Yes, limitations include higher initial costs, limited material choices, and the need for post-processing to achieve desired surface finishes. |
What industries use laser rapid prototyping? | Industries such as aerospace, medical, automotive, electronics, jewelry, and tooling commonly use laser rapid prototyping. |
How does laser rapid prototyping compare to other manufacturing methods? | It offers faster production, higher precision, and better material efficiency but may have higher initial costs and energy consumption compared to some traditional methods. |
What is the typical size range for metal powders used in LRP? | The typical particle size range for metal powders used in LRP is between 10 and 63 microns. |
Can LRP be used for mass production? | While LRP is ideal for prototyping and small batch production, it’s not typically used for mass production due to its higher cost per unit compared to traditional methods like injection molding. |
What post-processing steps are required for LRP parts? | Post-processing steps may include heat treatment, surface finishing, machining, and polishing to achieve the desired properties and appearance. |
Conclusion
Laser rapid prototyping is a powerful tool that offers numerous benefits for creating detailed and precise prototypes quickly and efficiently. Whether you’re working in aerospace, medical, automotive, or any other industry, understanding the intricacies of this technology and the materials involved can help you leverage its full potential. By selecting the right metal powder, understanding its properties, and knowing the pros and cons, you can make informed decisions and achieve the best results for your projects.
From titanium’s lightweight strength to Inconel’s high-temperature resilience, the range of metal powders available for laser rapid prototyping ensures that there’s a material suited for every application. So, whether you’re crafting a new aerospace component or designing a custom piece of jewelry, laser rapid prototyping has got you covered.
About 3DP mETAL
Product Category
CONTACT US
Any questions? Send us a message now! After receiving your message, we will process your request with a whole team.