In the realm of mold making, where precision and durability reign supreme, M2 Mold Steel Power stands as a champion. Renowned for its exceptional balance of toughness, wear resistance, and heat tolerance, this workhorse material has become the cornerstone for countless industrial applications. But what exactly imbues M2 mold steel with such power? Let’s delve into the fascinating world of this metal, exploring its composition, properties, and the diverse applications it empowers.
Composition and Key Properties of M2 Mold Steel Power
M2 mold steel belongs to the high-speed steel (HSS) family. Imagine a metal that can withstand the intense heat generated during high-speed machining – that’s the essence of HSS. M2 achieves this feat through a carefully balanced recipe of elements. Here’s a breakdown of its key ingredients:
Element | Function | Percentage (wt%) |
---|---|---|
Carbon (C) | Provides hardness and wear resistance | 0.86-0.94 |
Silicon (Si) | Improves hardenability and reduces brittleness | 0.20-0.45 |
Manganese (Mn) | Enhances strength and hardenability | 0.20-040 |
Chromium (Cr) | Contributes to wear resistance and corrosion protection | 3.80-4.50 |
Molybdenum (Mo) | The star player! Enhances red hardness (hot hardness) – a crucial property for mold steels | 4.70-5.20 |
Vanadium (V) | Refines grain structure and improves toughness | 1.70-2.10 |
This unique blend grants M2 mold steel a formidable set of properties:
- High Hardness: After proper heat treatment, M2 boasts exceptional hardness, enabling it to hold its shape and resist wear during demanding molding processes. Think of it like a resolute warrior, unwavering against the forces trying to dull its edge.
- Superior Wear Resistance: M2 excels at resisting abrasive wear, a significant concern in mold making. Imagine repeatedly pressing hot plastic into a mold – M2 can handle this punishment without succumbing to excessive wear, ensuring consistent part quality over extended production runs.
- Red Hardness (Hot Hardness): This is where M2 truly shines. Unlike some steels that soften significantly at elevated temperatures, M2 retains a good portion of its hardness even when hot. In the high-heat environment of molding operations, this property is paramount. It’s like a blacksmith’s hammer that stays strong even when glowing red-hot.
- Good Toughness: Despite its impressive hardness, M2 doesn’t become overly brittle. This balance between strength and flexibility allows the steel to withstand sudden impacts and thermal stresses that could potentially crack a more rigid material. Imagine a strong tree that can bend in the wind without breaking – that’s the ideal balance M2 strives for.
These properties, combined with its machinability and good dimensional stability after heat treatment, make M2 mold steel a versatile and reliable choice for a wide range of applications.
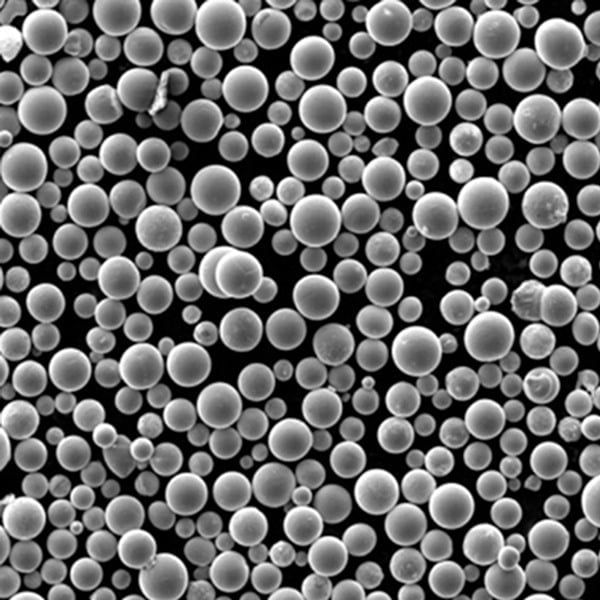
Applications of M2 Mold Steel Power
M2 mold steel’s robust characteristics translate into a multitude of applications across various industries. Let’s explore some prominent examples:
- Plastic Injection Molding: This is perhaps the most common domain for M2. Its ability to withstand the heat and pressure of molten plastic injection, coupled with its wear resistance, makes it ideal for producing a vast array of plastic parts, from intricate electronics housings to everyday utensils.
- Die Casting: In scenarios involving the high-pressure casting of molten metals like aluminum or zinc, M2’s thermal stability and resistance to erosion from molten metal come into play. Think of it as a sturdy container that can handle the intense heat and pressure of molten metal being forced into shape.
- Extrusion Dies: For applications requiring the continuous forming of plastic or metal shapes, M2’s wear resistance proves invaluable. Imagine a cookie cutter that can handle countless batches of dough without losing its shape – that’s the kind of durability M2 brings to extrusion dies.
- Punching and Blanking Tools: When it comes to punching precise shapes out of sheet metal, M2’s ability to maintain a sharp edge translates to clean and consistent parts. Think of a skilled tailor’s shears that can cut through fabric with precision – that’s the kind of sharpness M2 offers in punching and blanking applications.
- Cold Forming Tools: M2’s toughness makes it suitable for cold forming processes, where metal is shaped at room temperature. Imagine a blacksmith’s hammer that can deform metal without chipping or cracking – that’s the kind of strength M2 brings to cold forming tools.
Beyond these core applications, M2 Mold Steel Power finds its way into a diverse range of industries, including:
- Automotive: From engine components to trim parts, M2’s durability ensures consistent production of high-quality automotive components.
- Aerospace: In the demanding aerospace industry, M2’s ability to withstand harsh environments and maintain dimensional stability makes it suitable for specific aerospace components.
- Electronics: The intricate world of electronics relies on M2 for molds used to produce electronic connectors and other critical components.
- Construction: Certain specialized construction applications, such as tools for forming concrete or metal building components, can benefit from M2’s strength and wear resistance.
This is not an exhaustive list, but it showcases the versatility and widespread use of M2 mold steel. However, it’s important to acknowledge that no single material reigns supreme in every scenario.
Specifications, Sizes, and Grades
When selecting M2 Mold Steel Power for your specific application, several factors come into play. Here’s a breakdown of key considerations:
- Specifications and Standards: M2 mold steel adheres to various international and national standards, ensuring consistent quality across different regions. Some common standards include ASTM A681 (US), EN ISO 4957 (Europe), and JIS G3405 (Japan). Understanding these standards helps you select M2 that meets the required specifications for your application.
- Sizes and Grades: M2 mold steel is available in various shapes and sizes, including bars, plates, and rounds. The specific size you require will depend on the geometry of the mold you’re creating. Additionally, M2 comes in different grades with slight variations in composition to cater to specific needs. For instance, some grades might offer slightly higher wear resistance or improved machinability depending on the manufacturer. Consulting with a steel supplier or a qualified engineer is recommended to determine the optimal size and grade for your project.
Here’s a table summarizing the specifications, sizes, and grades of M2 mold steel:
Feature | Description |
---|---|
Specifications | ASTM A681, EN ISO 4957, JIS G3405 (and others) |
Sizes | Bars, plates, rounds (various dimensions) |
Grades | Variations in composition for specific needs (consult supplier for details) |
Pricing: The cost of M2 mold steel fluctuates based on factors like market demand, size, grade, and supplier. Generally, it falls within the mid-range for tool steels.
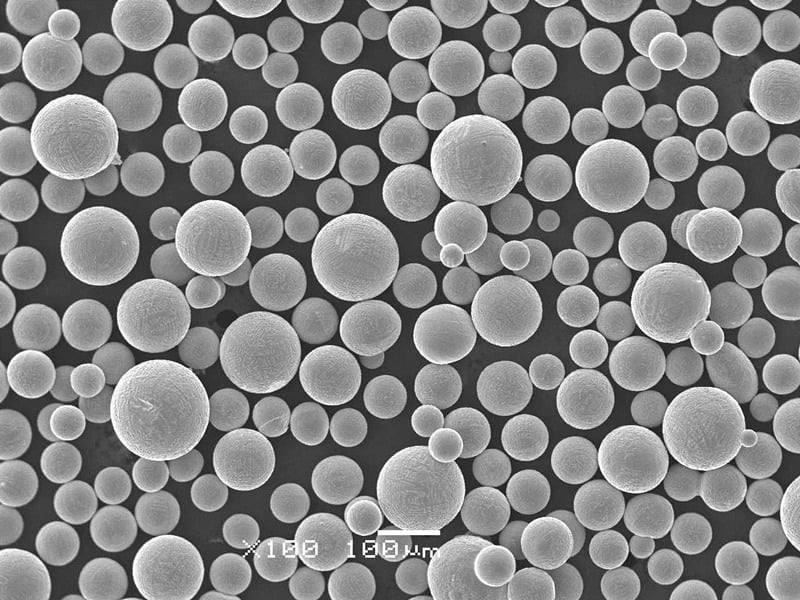
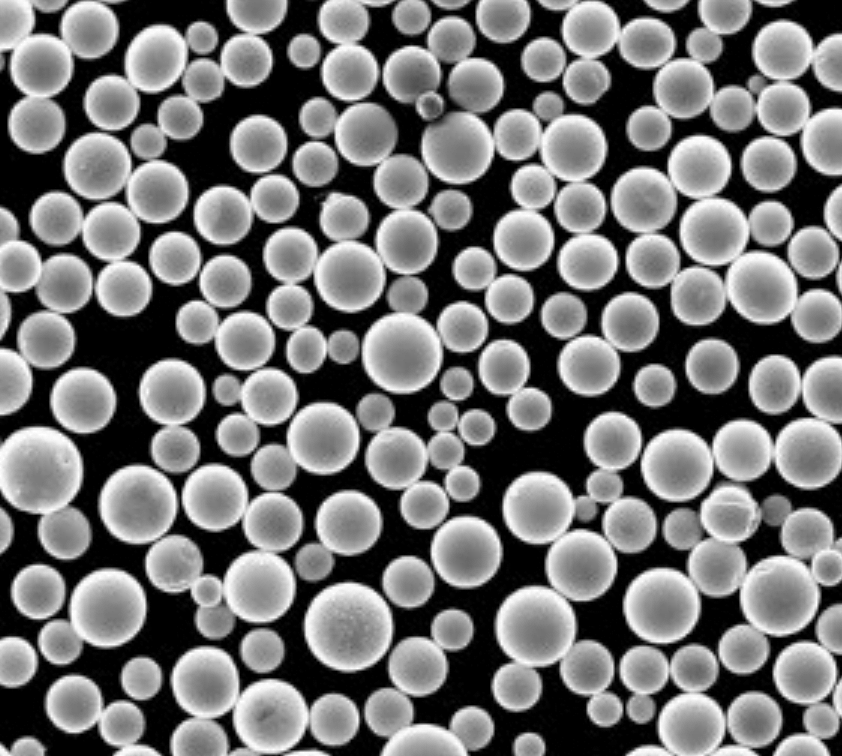
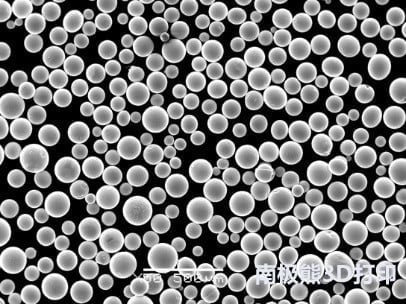
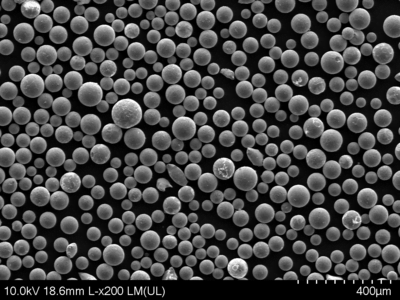
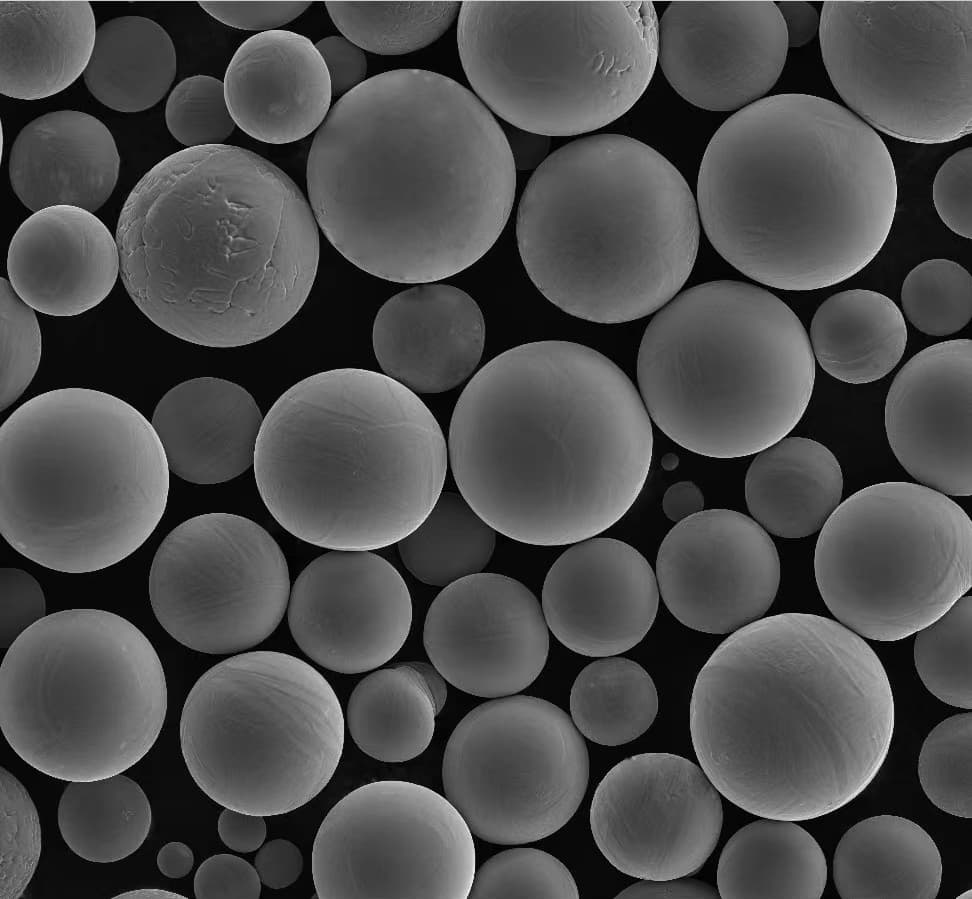
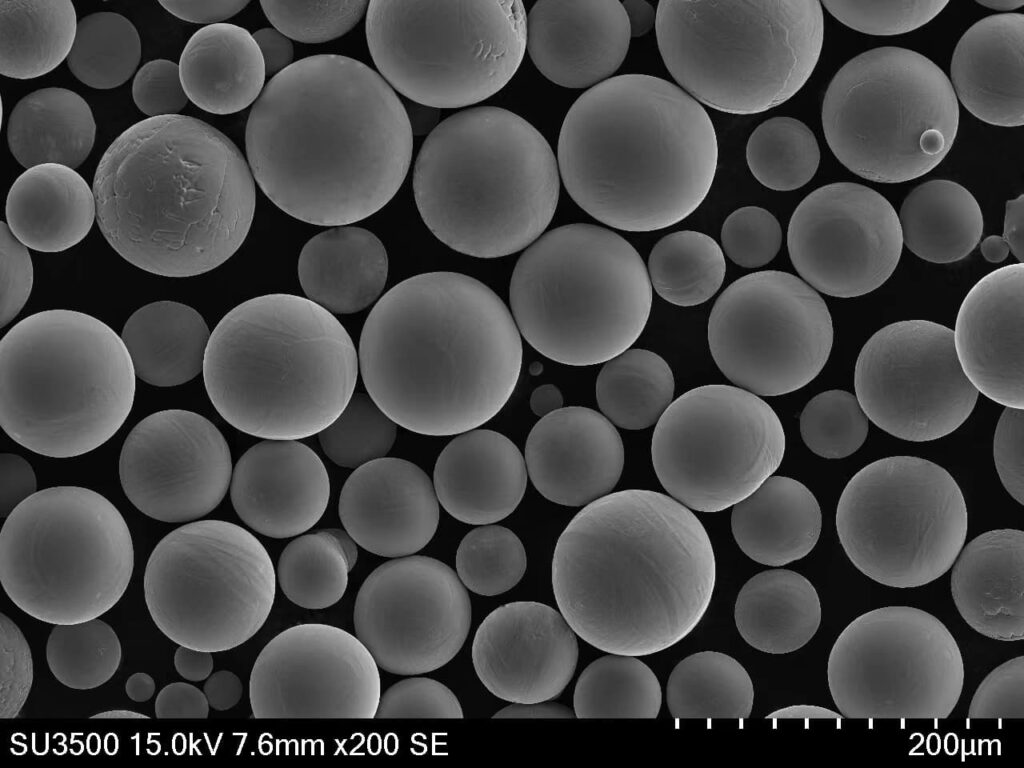
Pros and Cons of M2 Mold Steel
Like any material, M2 mold steel has its own set of advantages and limitations. Here’s a balanced perspective to help you make an informed decision:
Pros:
- Exceptional balance of properties: M2 offers a compelling combination of hardness, wear resistance, red hardness, and good toughness, making it suitable for a wide range of applications.
- Versatility: Across various industries and molding processes, M2 demonstrates its adaptability.
- Good machinability: Compared to some other tool steels, M2 offers relatively good machinability, simplifying the mold-making process.
- Dimensional stability: After proper heat treatment, M2 retains its shape well, ensuring consistent part dimensions.
- Wide availability: M2 is a readily available material from numerous steel suppliers.
Cons:
- Not the hardest tool steel: While hard, M2 isn’t the absolute hardest tool steel option. For applications requiring the absolute highest hardness, other options might be more suitable.
- Corrosion resistance: M2 exhibits moderate corrosion resistance. If corrosion is a significant concern, other tool steel grades with improved corrosion resistance might be necessary.
- Brittle at very low temperatures: While generally tough, M2 can become somewhat brittle at extremely low temperatures. Consider alternative materials if your application involves very cold environments.
The key takeaway is that M2 offers a well-rounded set of properties at a reasonable cost, making it a popular choice for a vast array of molding applications. However, it’s crucial to evaluate your specific needs and potential limitations before finalizing your material selection.
Additional Considerations: Beyond the core pros and cons, factors like heat treatment requirements, environmental conditions, and desired surface finish can influence your choice. Consulting with a qualified materials engineer or a knowledgeable steel supplier is recommended for a comprehensive evaluation of your specific project needs.
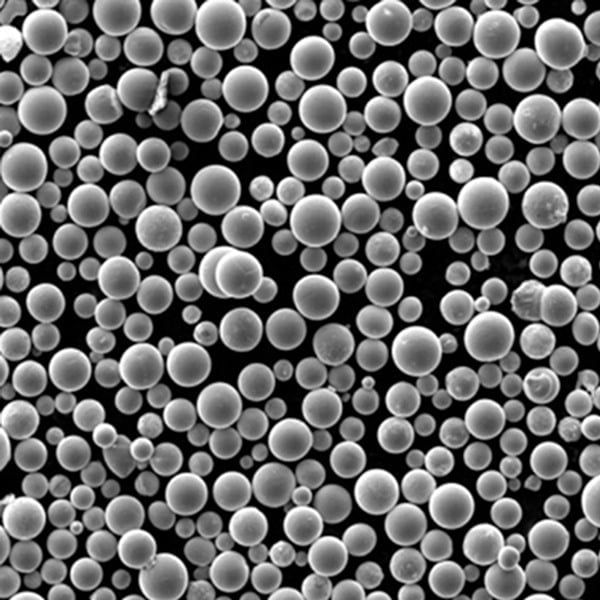
FAQ
Here’s a compilation of frequently asked questions (FAQ) to provide further clarity on M2 mold steel:
Q: How does M2 mold steel compare to other tool steels?
A: M2 occupies a valuable middle ground within the vast spectrum of tool steels. It offers a good balance of hardness, wear resistance, and toughness at a reasonable cost. Here’s a quick comparison against two other commonly used tool steels:
- H13 Tool Steel: Slightly tougher than M2 but with lower wear resistance. A good choice for applications requiring some impact resistance along with good wear resistance. For example, H13 might be suitable for molds used with abrasive materials or for cold forming processes.
- D2 Tool Steel: Significantly harder than M2, making it ideal for applications demanding the absolute highest wear resistance. However, D2 is also more difficult to machine and exhibits lower toughness compared to M2. Imagine a diamond versus a sapphire – the diamond offers superior hardness but can chip more easily, whereas the sapphire provides a good balance of hardness and toughness.
The best tool steel selection depends on the specific requirements of your application. Consider factors like hardness needs, wear resistance requirements, toughness demands, and budget constraints when making your choice.
Q: Are there any specific metal powder models of M2 mold steel available?
A: While M2 mold steel is traditionally produced through conventional ingot metallurgy, advancements in metal additive manufacturing (3D printing) have opened doors for the creation of metal powders specifically designed for M2 tool steel. Here are some notable examples:
- Höganäs M2: A gas-atomized tool steel powder from Höganäs AB that offers excellent powder flowability and dimensional control, making it suitable for various additive manufacturing processes like laser beam melting (LBM).
- AMPO® M2 Powder: Developed by AM Powder Company, this gas-atomized powder boasts high purity and good printability for applications in LBM and electron beam melting (EBM) additive manufacturing.
- SLM Solutions M 2.1: Tailored for selective laser melting (SLM), this metal powder from SLM Solutions offers a good balance of properties similar to conventionally produced M2 tool steel.
Metal powder versions of M2 mold steel offer several potential benefits, including:
- Design flexibility: Additive manufacturing allows for the creation of complex mold geometries that might be challenging or impossible to produce through traditional machining techniques.
- Reduced waste: The layer-by-layer nature of additive manufacturing minimizes material wastage compared to subtractive machining processes used with conventional M2 bars or blocks.
- Potential for performance optimization: Research is ongoing to explore the possibility of tailoring the microstructure of metal powders to achieve enhanced properties compared to conventionally produced M2 mold steel.
It’s important to note that metal additive manufacturing with M2 tool steel powders is still a developing technology. Factors like printer compatibility, post-processing requirements, and overall cost-effectiveness need careful consideration. Consulting with a qualified additive manufacturing service provider is recommended to determine if leveraging metal AM with M2 powder is suitable for your specific project.
Q: What are some key considerations when heat treating M2 mold steel?
A: Proper heat treatment is crucial to unlocking the full potential of M2 mold steel. Here’s a breakdown of essential aspects to consider:
- Austenitizing Temperature: This initial heating stage prepares the steel for transformation. For M2, the austenitizing temperature typically falls within the range of 790-820°C (1450-1500°F).
- Quenching: Rapid cooling from the austenitizing temperature is essential for achieving the desired hardness. Common quenching mediums for M2 include oil, air, or various water-based quenchants. The selection of the quenching medium depends on the specific size and geometry of the mold to avoid cracking.
- Tempering: This subsequent heating to a lower temperature helps to relieve internal stresses and achieve the desired balance of hardness and toughness. Tempering temperatures for M2 typically range from 510-540°C (950-1000°F).
Consulting with a heat treatment specialist or referring to established heat treatment guidelines for M2 mold steel is vital to ensure optimal performance and avoid potential issues like warping or cracking.
About 3DP mETAL
Product Category
CONTACT US
Any questions? Send us a message now! After receiving your message, we will process your request with a whole team.