Metal alloy powders are an integral part of modern manufacturing, enabling a range of applications from 3D printing to advanced aerospace engineering. These powders consist of a blend of metal elements combined in various ratios to achieve specific properties. This article dives into the intricacies of metal alloy powders, discussing types, properties, applications, and more, while providing a comprehensive overview that caters to both newcomers and seasoned professionals in the field.
Overview of Metal Alloy Powders
Metal alloy powders are finely divided metals that have been mixed to form a composite with desirable properties for various industrial uses. These powders are essential in additive manufacturing, sintering processes, and coating applications. Understanding the specifics of these powders, such as their composition, properties, and uses, is crucial for optimizing their application in different sectors.
Key Details of Metal Alloy Powders
- Composition: Blend of two or more metals or a metal and a non-metal.
- Properties: Enhanced mechanical strength, corrosion resistance, electrical conductivity, etc.
- Applications: 3D printing, aerospace, automotive, medical implants, etc.
- Manufacturing Methods: Atomization, reduction, electrolysis, mechanical alloying.
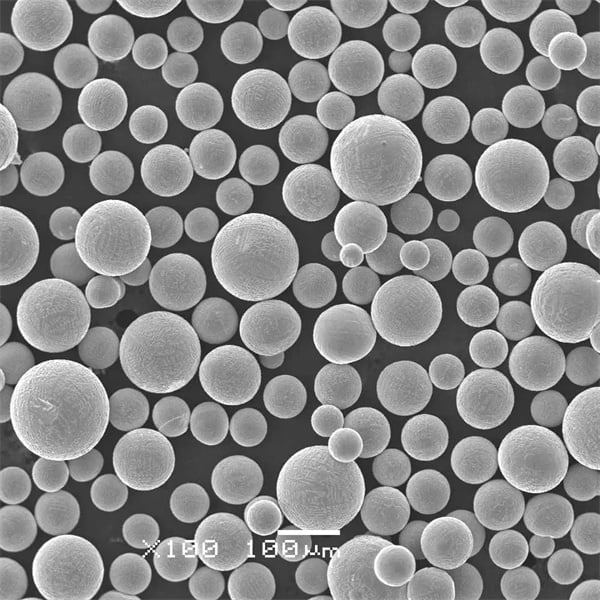
Types of Metal Alloy Powders
There are numerous types of metal alloy powders, each with specific compositions and properties tailored for distinct applications. Here, we list and describe ten notable metal alloy powders used in various industries.
Alloy Powder | Composition | Properties | Applications |
---|---|---|---|
Stainless Steel 316L | Fe, Cr, Ni, Mo | High corrosion resistance, ductility | Medical implants, food processing equipment |
Inconel 718 | Ni, Cr, Fe, Nb, Mo | High strength, oxidation resistance | Aerospace components, gas turbines |
Titanium Ti-6Al-4V | Ti, Al, V | Lightweight, high strength | Aerospace, biomedical devices |
Copper Alloy C18150 | Cu, Cr, Zr | Excellent electrical conductivity | Electrical contacts, welding electrodes |
Aluminum Alloy 6061 | Al, Mg, Si, Cu | Good mechanical properties, corrosion resistance | Automotive, aerospace structures |
Tool Steel H13 | Fe, Cr, Mo, V | High toughness, heat resistance | Die casting, extrusion tools |
Nickel Alloy 625 | Ni, Cr, Mo, Nb | Excellent fatigue and corrosion resistance | Chemical processing, marine applications |
Cobalt Chrome Alloy | Co, Cr, Mo | High wear and corrosion resistance | Dental implants, orthopedic implants |
Bronze Alloy CuSn8 | Cu, Sn | High strength, good wear resistance | Bearings, bushings, sculptures |
Magnesium Alloy AZ91D | Mg, Al, Zn | Lightweight, good castability | Automotive, electronics casings |
Applications of Metal Alloy Powders
Metal alloy powders find utility in numerous sectors due to their diverse and beneficial properties. Here’s a closer look at some of their most common applications:
Industry | Application | Benefits |
---|---|---|
Aerospace | Engine components, structural parts | High strength-to-weight ratio, durability |
Automotive | Engine parts, transmission systems | Wear resistance, lightweight |
Medical | Implants, surgical instruments | Biocompatibility, corrosion resistance |
Electronics | Conductive coatings, connectors | Electrical conductivity, reliability |
Tool and Die | Molds, cutting tools | Hardness, heat resistance |
Marine | Propellers, hull components | Corrosion resistance, durability |
Construction | Structural components, fixtures | Strength, wear resistance |
Defense | Armaments, vehicle parts | High strength, corrosion resistance |
Energy | Turbine blades, power generation | High temperature resistance, durability |
Art and Jewelry | Sculptures, fine jewelry | Aesthetic appeal, workability |
Specifications, Sizes, Grades, and Standards
Each type of metal alloy powder comes in various specifications, sizes, and grades to meet specific industry standards and requirements.
Alloy Powder | Sizes (µm) | Grades | Standards |
---|---|---|---|
Stainless Steel 316L | 15-45, 45-106 | ASTM F138, F139 | ISO 5832-1 |
Inconel 718 | 15-45, 45-106 | AMS 5662, 5663 | ASTM B637 |
Titanium Ti-6Al-4V | 15-45, 45-106 | Grade 5, Grade 23 | ASTM F136, F1472 |
Copper Alloy C18150 | 15-45, 45-106 | UNS C18150 | ASTM B188 |
Aluminum Alloy 6061 | 15-45, 45-106 | 6061-T6, 6061-O | ASTM B221, B209 |
Tool Steel H13 | 15-45, 45-106 | H13 | ASTM A681 |
Nickel Alloy 625 | 15-45, 45-106 | UNS N06625 | ASTM B443, B446 |
Cobalt Chrome Alloy | 15-45, 45-106 | ASTM F75, F1537 | ISO 5832-4 |
Bronze Alloy CuSn8 | 15-45, 45-106 | CuSn8 | ASTM B505 |
Magnesium Alloy AZ91D | 15-45, 45-106 | AZ91D | ASTM B93, B94 |
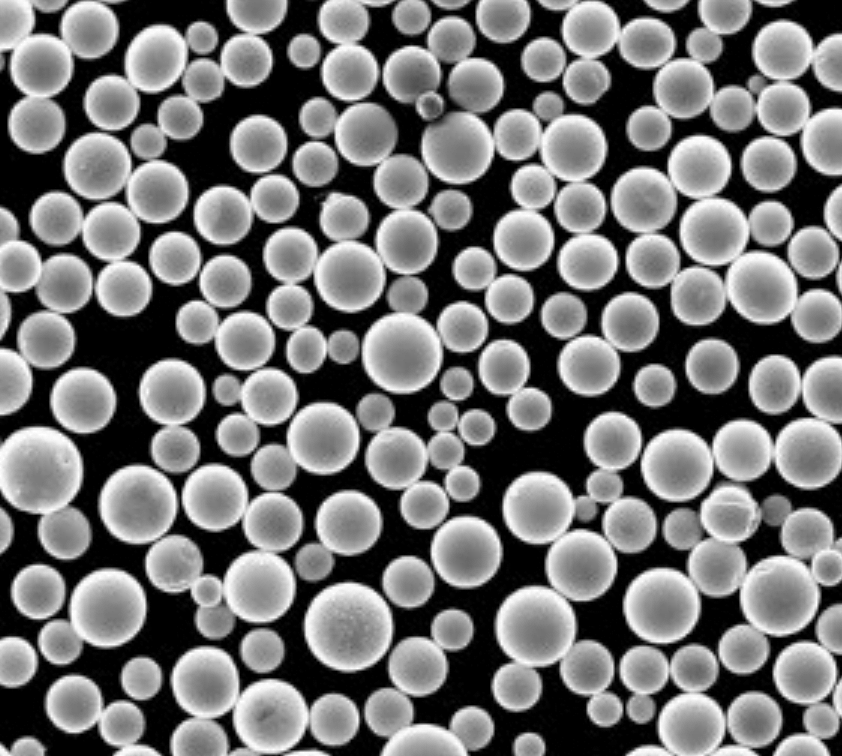
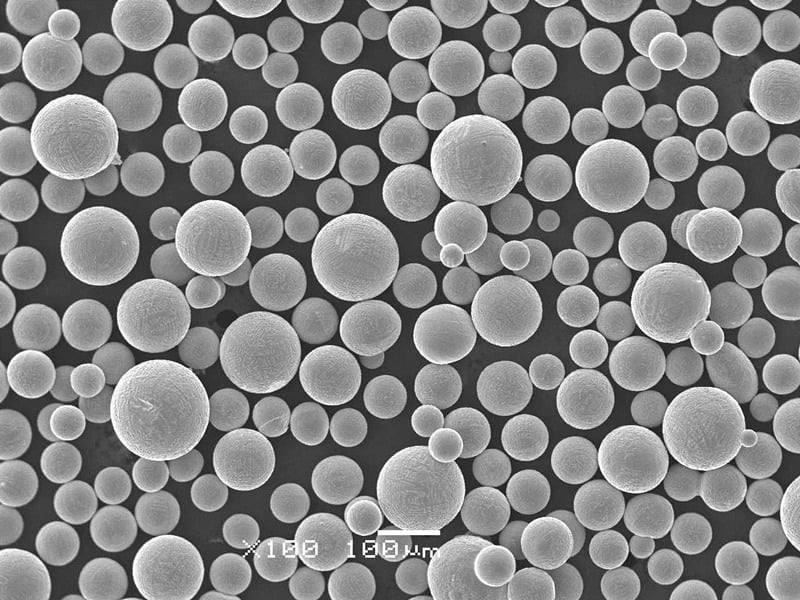
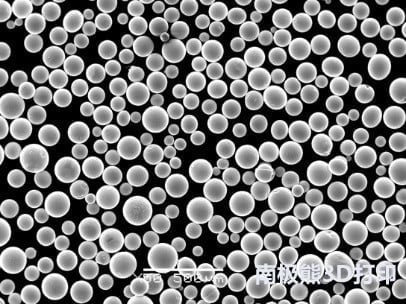
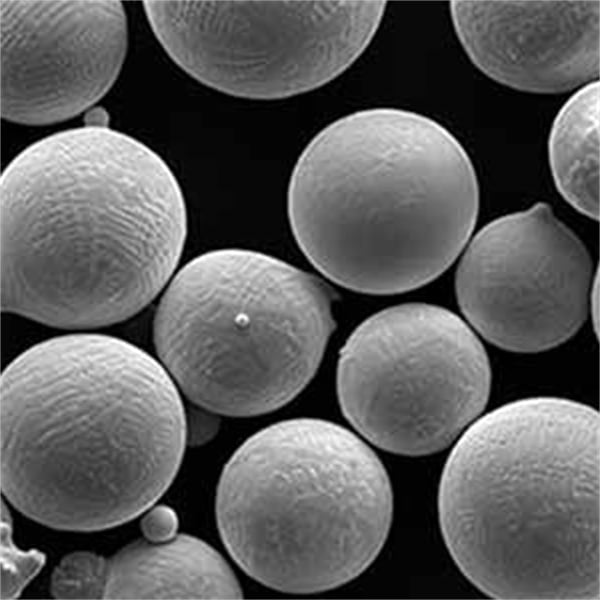
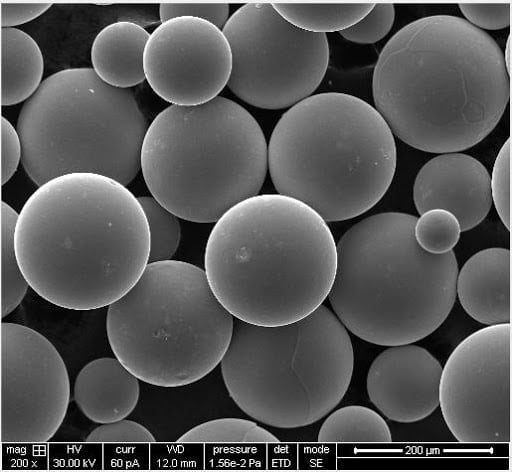
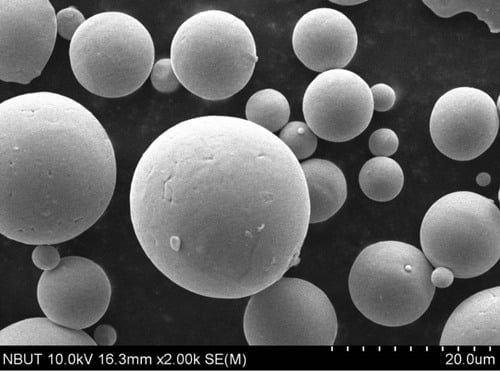
Suppliers and Pricing Details
Here’s a list of some of the leading suppliers of metal alloy powders along with approximate pricing details.
Supplier | Alloy Powder | Price Range (USD/kg) | Location |
---|---|---|---|
Höganäs AB | Stainless Steel 316L | $50 – $70 | Sweden |
Carpenter Technology | Inconel 718 | $100 – $150 | USA |
ATI Specialty Metals | Titanium Ti-6Al-4V | $200 – $250 | USA |
Sandvik Osprey | Copper Alloy C18150 | $30 – $50 | UK |
EOS GmbH | Aluminum Alloy 6061 | $40 – $60 | Germany |
GKN Hoeganaes | Tool Steel H13 | $70 – $90 | USA |
Kennametal Inc. | Nickel Alloy 625 | $150 – $200 | USA |
Straumann | Cobalt Chrome Alloy | $120 – $170 | Switzerland |
Belmont Metals | Bronze Alloy CuSn8 | $20 – $40 | USA |
Rima Group | Magnesium Alloy AZ91D | $50 – $80 | Brazil |
Advantages of Metal Alloy Powders
Metal alloy powders offer a multitude of advantages, making them a preferred choice in various manufacturing processes. Let’s explore these benefits in detail.
High Customizability
One of the standout advantages is the ability to tailor the composition to meet specific needs. Whether it’s enhancing strength, improving corrosion resistance, or achieving a particular electrical conductivity, metal alloy powders can be engineered to deliver precise properties.
Superior Mechanical Properties
Compared to pure metals, alloys typically exhibit superior mechanical properties. This includes increased tensile strength, hardness, and toughness, making them ideal for high-stress applications.
Enhanced Corrosion Resistance
Many alloy powders, such as stainless steel and nickel-based alloys, offer excellent resistance to corrosion, which is crucial for applications in harsh environments, such as marine and chemical processing industries.
Versatility in Applications
From aerospace components that demand high strength-to-weight ratios to biomedical implants requiring biocompatibility, the versatility of metal alloy powders is unmatched. They can be used across a wide range of industries, demonstrating their adaptability.
Economic Efficiency
Although the initial cost of alloy powders might be higher, the long-term benefits such as durability, reduced maintenance costs, and enhanced performance often result in significant economic efficiency over the product lifecycle.
Disadvantages of Metal Alloy Powders
While metal alloy powders offer numerous benefits, they also come with certain limitations that need to be considered.
High Cost
The production of metal alloy powders can be expensive, especially for high-performance alloys like titanium and nickel-based powders. This can be a limiting factor for small-scale operations or applications with tight budget constraints.
Complex Manufacturing Process
The manufacturing process of metal alloy powders, such as atomization or mechanical alloying, is complex and requires specialized equipment and expertise. This can pose challenges for manufacturers new to the field.
Potential for Contamination
During the production and handling of metal alloy powders, there is a risk of contamination which can affect the properties and performance of the final product. Strict quality control measures are necessary to mitigate this risk.
Limited Availability
Certain high-demand alloy powders might have limited availability due to the complexities involved in their production and the scarcity of raw materials. This can lead to supply chain disruptions and increased lead times.
Comparing Pros and Cons of Metal Alloy Powders
To make an informed decision, it’s essential to weigh the pros and cons of metal alloy powders. Here’s a comparative table that highlights the key advantages and disadvantages.
Aspect | Advantages | Disadvantages |
---|---|---|
Cost | Long-term economic efficiency | High initial cost |
Mechanical Properties | Superior strength, hardness, toughness | Complex manufacturing process |
Corrosion Resistance | Enhanced resistance to environmental factors | Potential for contamination |
Application Versatility | Suitable for diverse industries | Limited availability of certain alloys |
Customizability | Tailored properties for specific needs | Requires specialized expertise |
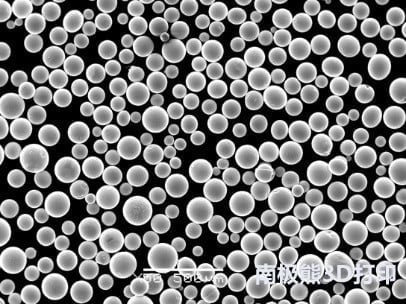
FAQs
What are metal alloy powders?
Metal alloy powders are finely divided mixtures of metals, sometimes combined with non-metals, designed to have specific properties for industrial applications such as 3D printing, sintering, and coating.
How are metal alloy powders made?
They are produced through various methods such as atomization, reduction, electrolysis, and mechanical alloying. These processes involve breaking down metals into fine particles and blending them to form a uniform powder.
What are the common applications of metal alloy powders?
Common applications include aerospace components, automotive parts, medical implants, electrical connectors, tooling, and marine equipment due to their diverse and enhanced properties.
Why are metal alloy powders expensive?
The production of metal alloy powders involves sophisticated and energy-intensive processes, which, along with the cost of raw materials, contribute to their high price.
Can metal alloy powders be recycled?
Yes, metal alloy powders can often be recycled. The process involves re-melting and re-alloying, though it requires careful control to maintain the desired properties.
How do I choose the right metal alloy powder for my application?
Consider factors like mechanical properties, corrosion resistance, electrical conductivity, application environment, and cost. Consulting with suppliers and material scientists can also help in selecting the appropriate alloy.
Are there any health risks associated with handling metal alloy powders?
Yes, handling metal powders can pose health risks if proper safety measures are not followed. Inhalation of fine particles can cause respiratory issues, and some metals may have specific toxicities. Using protective equipment and adhering to safety guidelines is crucial.
What is the difference between metal alloy powders and pure metal powders?
Metal alloy powders consist of a combination of metals (and sometimes non-metals) designed to enhance certain properties, whereas pure metal powders consist of a single type of metal. Alloys typically offer superior properties compared to pure metals.
Can metal alloy powders be used in additive manufacturing?
Absolutely. Metal alloy powders are widely used in additive manufacturing (3D printing) due to their ability to produce complex geometries with tailored properties.
Who are the leading suppliers of metal alloy powders?
Some leading suppliers include Höganäs AB, Carpenter Technology, ATI Specialty Metals, Sandvik Osprey, and EOS GmbH, among others. These suppliers offer a range of alloy powders catering to different industrial needs.
Conclusion
Metal alloy powders are a cornerstone of modern manufacturing, offering unparalleled customizability and performance across a wide range of applications. By understanding their properties, applications, and potential drawbacks, businesses and engineers can make informed decisions that leverage the full potential of these advanced materials. Whether it’s for aerospace, medical, automotive, or other industrial sectors, metal alloy powders continue to drive innovation and efficiency, paving the way for the next generation of manufacturing technologies.
About 3DP mETAL
Product Category
CONTACT US
Any questions? Send us a message now! After receiving your message, we will process your request with a whole team.