Metal Binder Jetting (MBJ) is revolutionizing the manufacturing world with its ability to produce complex metal parts swiftly and efficiently. This technology stands at the intersection of traditional manufacturing and cutting-edge 3D printing, offering a range of applications across various industries. In this extensive guide, we’ll dive deep into the world of Metal Binder Jetting, exploring its composition, characteristics, applications, and more.
Overview of Metal Binder Jetting
Metal Binder Jetting is an additive manufacturing process that involves the deposition of a binding agent onto a bed of metal powder to create a solid part layer by layer. Unlike other 3D printing methods, MBJ does not require support structures and offers greater flexibility in material usage. This method is known for its speed, cost-effectiveness, and ability to produce parts with complex geometries.
Key Details:
- Process: Deposition of binding agent on metal powder.
- Materials Used: Metal powders such as stainless steel, titanium, and aluminum.
- Advantages: Cost-effective, high-speed production, complex geometries without supports.
- Applications: Automotive, aerospace, medical, and consumer products.
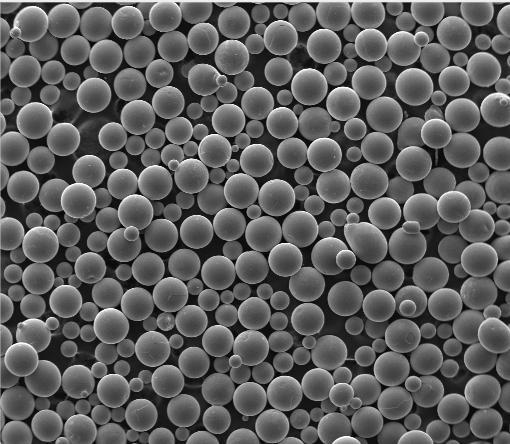
Types and Characteristics of Metal Powders Used in Binder Jetting
To fully understand Metal Binder Jetting, it’s essential to know the specific types of metal powders used. Here’s a look at ten popular metal powders, their composition, properties, and characteristics.
Metal Powder Types and Properties
Metal Powder | Composition | Properties | Characteristics |
---|---|---|---|
Stainless Steel 316L | Fe, Cr, Ni, Mo | Corrosion-resistant, high strength | Excellent for harsh environments, common in marine and medical industries |
Titanium Ti6Al4V | Ti, Al, V | High strength-to-weight ratio, biocompatible | Widely used in aerospace and medical implants due to its lightweight and biocompatibility |
Aluminum AlSi10Mg | Al, Si, Mg | Lightweight, good thermal properties | Popular in automotive and aerospace for lightweight components |
Inconel 625 | Ni, Cr, Mo, Nb | High temperature and corrosion resistance | Ideal for high-stress environments like aerospace and chemical processing |
Copper | Cu | Excellent electrical and thermal conductivity | Utilized in electrical components and heat exchangers |
Tool Steel M2 | Fe, Mo, Cr, V, W | High hardness and wear resistance | Common in tooling applications due to its durability |
Nickel Alloy 718 | Ni, Cr, Fe, Nb, Mo, Ti, Al | High strength, corrosion resistance | Used in turbine blades and other high-performance applications |
Bronze | Cu, Sn | Good wear resistance, low friction | Historically used in bearings, bushings, and sculptures |
Cobalt Chrome | Co, Cr, Mo | High wear and corrosion resistance | Preferred in dental and orthopedic implants for its biocompatibility and strength |
Stainless Steel 17-4PH | Fe, Cr, Ni, Cu, Nb | High strength, corrosion resistance | Utilized in aerospace, chemical, and petrochemical industries for its excellent mechanical properties |
Applications of Metal Binder Jetting
Metal Binder Jetting is versatile and finds applications across a wide array of industries. Let’s delve into the specific uses in various sectors.
Application Areas and Uses
Industry | Application | Details |
---|---|---|
Automotive | Lightweight components, prototyping | Produces durable, lightweight parts and allows for rapid prototyping and testing |
Aerospace | Engine components, structural parts | Creates complex, high-strength parts that can withstand extreme conditions |
Medical | Implants, surgical tools | Facilitates the production of biocompatible implants and customized surgical instruments |
Consumer Products | Jewelry, eyewear frames | Enables the creation of intricate designs and custom-made products |
Electronics | Heat sinks, connectors | Provides solutions for efficient thermal management and reliable electrical connections |
Industrial Equipment | Tools, machinery parts | Produces wear-resistant, high-strength parts for industrial machinery and tools |
Energy | Turbine blades, heat exchangers | Develops components that operate in high-temperature environments |
Defense | Weapon parts, protective gear | Ensures high precision and durability in critical defense applications |
Construction | Structural connectors, customized fittings | Enables the production of robust and custom-fit parts for construction projects |
Art and Design | Sculptures, architectural models | Allows artists and designers to create detailed and complex structures |
Specifications, Sizes, Grades, and Standards
Understanding the specifications, sizes, grades, and standards of the metal powders used in Binder Jetting is crucial for ensuring the quality and consistency of the final products.
Specifications and Standards
Metal Powder | Specifications | Sizes | Grades | Standards |
---|---|---|---|---|
Stainless Steel 316L | Particle size: 15-45 µm, purity >99% | 10 µm – 50 µm | Grade A, B, C | ASTM A240, ISO 5832-1 |
Titanium Ti6Al4V | Particle size: 20-45 µm, purity >99% | 10 µm – 50 µm | Grade 5, Grade 23 | ASTM F136, ISO 5832-3 |
Aluminum AlSi10Mg | Particle size: 20-60 µm, purity >99% | 15 µm – 50 µm | Grade 10, Grade 20 | ASTM B209, ISO 6361 |
Inconel 625 | Particle size: 15-53 µm, purity >99% | 15 µm – 45 µm | Grade 1, Grade 2 | ASTM B443, ISO 6208 |
Copper | Particle size: 15-45 µm, purity >99% | 10 µm – 40 µm | Grade A, Grade B | ASTM B152, ISO 431 |
Tool Steel M2 | Particle size: 15-53 µm, purity >99% | 15 µm – 45 µm | Grade M2 | ASTM A600, ISO 4957 |
Nickel Alloy 718 | Particle size: 15-45 µm, purity >99% | 15 µm – 50 µm | Grade A, Grade B | ASTM B637, ISO 6208 |
Bronze | Particle size: 15-45 µm, purity >99% | 15 µm – 50 µm | Grade A, Grade B | ASTM B427, ISO 1338 |
Cobalt Chrome | Particle size: 20-45 µm, purity >99% | 15 µm – 50 µm | Grade F75, Grade F799 | ASTM F1537, ISO 5832-4 |
Stainless Steel 17-4PH | Particle size: 15-45 µm, purity >99% | 15 µm – 50 µm | Grade 630, Grade 1 | ASTM A564, ISO 683-17 |
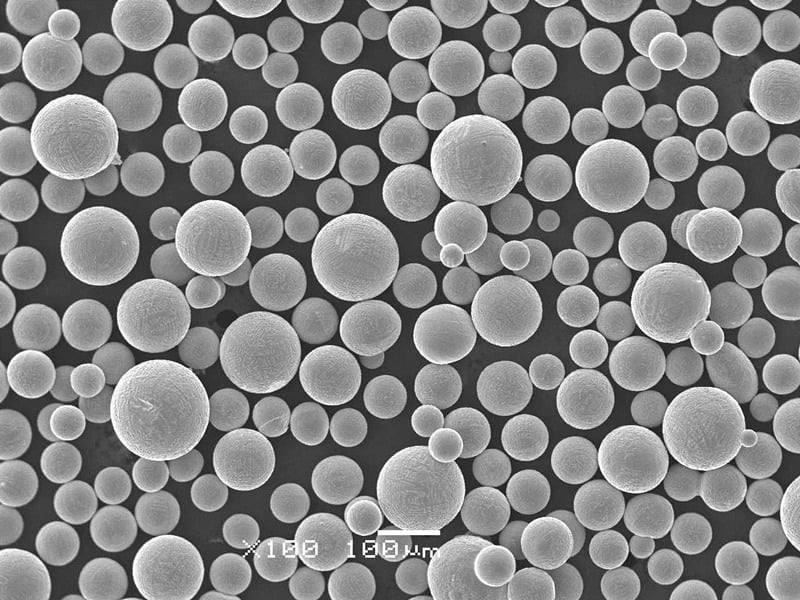
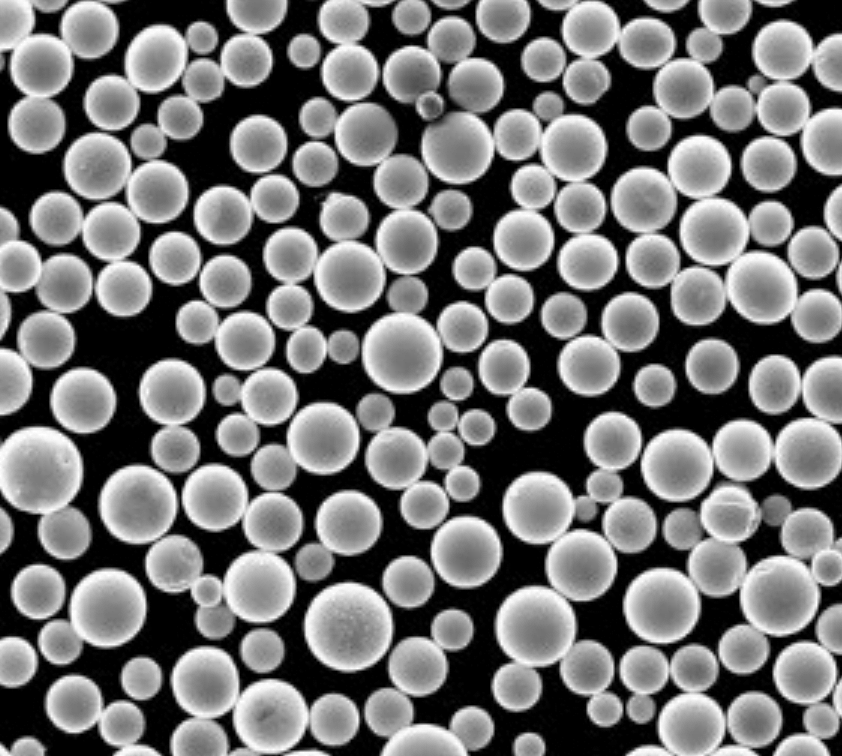
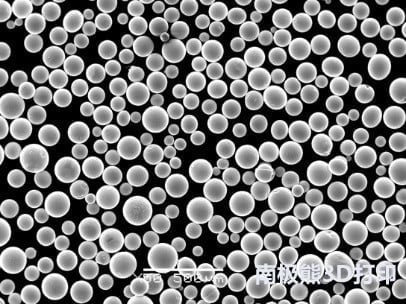
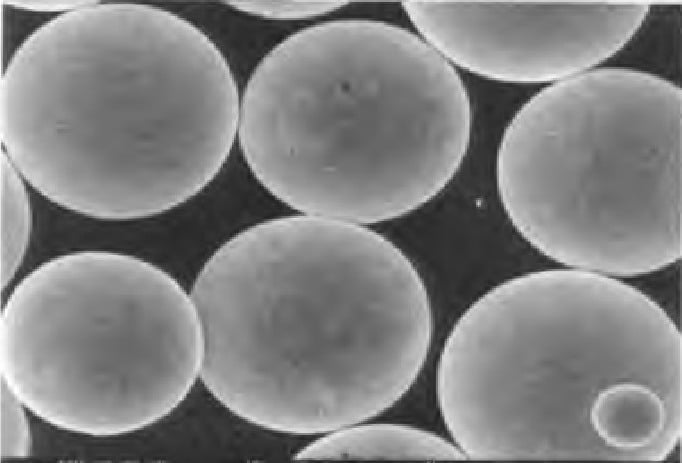
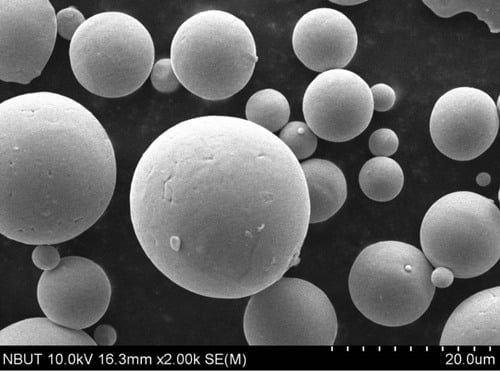
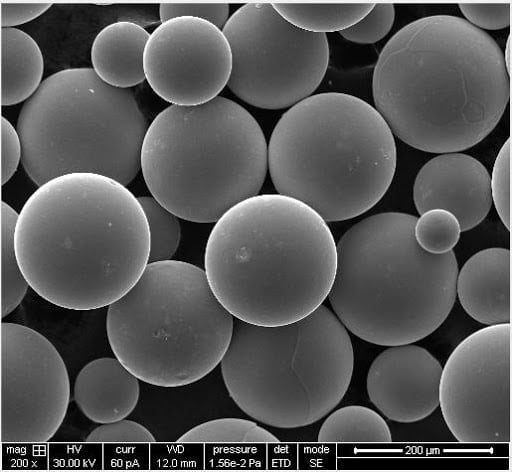
Suppliers and Pricing Details
Finding the right suppliers and understanding the pricing details are crucial steps in the implementation of Metal Binder Jetting technology.
Suppliers and Pricing
Supplier | Metal Powder | Price per kg | Region | Additional Services |
---|---|---|---|---|
Carpenter Technology | Stainless Steel 316L | $50 – $100 | North America | Custom alloy development, technical support |
Höganäs AB | Titanium Ti6Al4V | $200 – $300 | Europe, Asia | Powder customization, logistics support |
GKN Additive | Aluminum AlSi10Mg | $30 – $70 | Global | Design consultancy, R&D partnerships |
Sandvik Osprey | Inconel 625 | $150 – $250 | Europe, North America | Material testing, quality assurance |
American Elements | Copper | $20 – $50 | Global | Custom packaging, worldwide shipping |
LPW Technology | Tool Steel M2 | $70 – $120 | Europe, North America | Powder characterization, application support |
AP&C | Nickel Alloy 718 | $180 – $280 | North America, Europe | Particle size distribution analysis |
Kymera International | Bronze | $40 – $80 | North America, Europe | Alloy development, technical consultancy |
EOS GmbH | Cobalt Chrome | $120 – $220 | Global | Process optimization, customer training |
Oerlikon Metco | Stainless Steel 17-4PH | $50 – $100 | Global | Coating solutions, material testing |
Comparing Pros and Cons of Metal Binder Jetting
Every manufacturing technology comes with its set of advantages and limitations. Let’s compare the pros and cons of Metal Binder Jetting to provide a balanced view.
Advantages and Limitations
Aspect | Advantages | Limitations |
---|---|---|
Speed | High-speed production compared to traditional methods | Limited by printer size and complexity of design |
Cost | Cost-effective for small to medium production runs | High initial investment in equipment |
Material Versatility | Wide range of metal powders can be used | Powder handling and storage can be challenging |
Design Flexibility | Ability to produce complex geometries without supports | Surface finish may require post-processing |
Waste Reduction | Minimal material waste compared to subtractive manufacturing | Powder recycling and reuse considerations |
Part Performance | High-performance parts with tailored properties | Potential for porosity and internal defects |
Environmental Impact | Lower environmental impact due to reduced waste and energy consumption | Energy consumption during sintering process |
Customization | Easy customization and on-demand production | Limited to specific part sizes and production volumes |
In-Depth Look: Metal Binder Jetting Process
The Process Explained
Metal Binder Jetting involves several steps from start to finish. Here’s a detailed breakdown:
- Powder Spreading: A thin layer of metal powder is spread evenly across the build platform.
- Binder Deposition: A print head deposits a liquid binding agent onto the powder, adhering to the design.
- Layer Building: The process repeats layer by layer until the entire part is formed.
- Curing: The printed part is cured to harden the binder.
- Depowdering: Excess powder is removed from the printed part.
- Sintering: The part is sintered in a furnace to fuse the metal particles, enhancing strength and density.
- Post-Processing: Additional processes like machining, polishing, or coating may be applied to achieve the desired finish and properties.
Technical Insights
The success of Metal Binder Jetting heavily depends on the quality of the metal powder and the precision of the binder application. Factors like particle size distribution, binder composition, and sintering temperature play crucial roles in determining the final part’s properties.
Future Trends and Innovations
The future of Metal Binder Jetting looks promising with ongoing research and development aimed at enhancing the process and expanding its applications. Emerging trends include:
- Improved Material Diversity: Development of new metal powders to broaden the range of applications.
- Enhanced Precision: Advances in binder technology and print head accuracy for finer details.
- Integration with Other Technologies: Combining MBJ with other additive manufacturing methods for hybrid solutions.
- Sustainability Focus: Innovations aimed at reducing energy consumption and improving recyclability of materials.
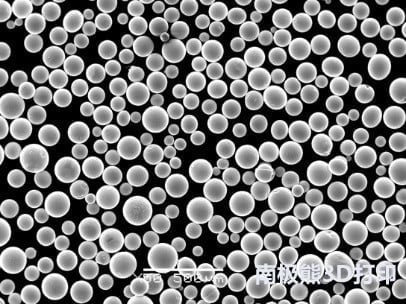
FAQs
Question | Answer |
---|---|
What metals can be used in Binder Jetting? | A wide range of metals including stainless steel, titanium, aluminum, and more. |
Is Metal Binder Jetting suitable for mass production? | Yes, particularly for small to medium production runs due to its speed and cost-effectiveness. |
How does Binder Jetting compare to other 3D printing methods? | It offers unique advantages like no need for support structures and faster production times. |
What are the typical applications of Metal Binder Jetting? | Applications span across industries such as aerospace, automotive, medical, and consumer products. |
What post-processing is required for Binder Jetting parts? | Post-processing may include sintering, machining, polishing, and coating. |
Can Binder Jetting produce parts with complex geometries? | Yes, it excels at creating intricate designs without the need for supports. |
How is the quality of Binder Jetting parts ensured? | Quality is ensured through precise control of powder characteristics, binder application, and sintering processes. |
What are the environmental benefits of Binder Jetting? | Reduced waste and energy consumption compared to traditional manufacturing methods. |
Are there any limitations to Binder Jetting? | Limitations include high initial equipment costs and potential for porosity in parts. |
How does Binder Jetting handle large-scale parts? | It is best suited for small to medium-sized parts; large-scale parts may face challenges in uniformity and strength. |
Conclusion
Metal Binder Jetting is a game-changing technology in the realm of additive manufacturing, offering unparalleled advantages in speed, cost, and design flexibility. From aerospace to medical implants, its applications are vast and varied. By understanding the intricacies of the process, the types of metal powders used, and the pros and cons, industries can leverage this technology to innovate and excel.
As Metal Binder Jetting continues to evolve, staying informed about the latest trends and advancements will be crucial for businesses looking to adopt this technology. With its potential to transform manufacturing processes, Metal Binder Jetting is poised to lead the way into a new era of production.
About 3DP mETAL
Product Category
CONTACT US
Any questions? Send us a message now! After receiving your message, we will process your request with a whole team.