Welcome to our deep dive into Metal Injection Molding (MIM). If you’re curious about this sophisticated manufacturing process, you’re in the right place. MIM combines the flexibility of plastic injection molding with the strength and integrity of powdered metallurgy. It’s a fascinating blend of science and engineering, producing high-precision metal parts. Let’s explore everything you need to know about Metal Injection Molding, from its basics to its applications, materials, and much more.
Overview of Metal Injection Molding
Metal Injection Molding (MIM) is a manufacturing process that merges powdered metal and binder material to create highly detailed, complex metal parts. It’s a go-to for producing small, intricate components that would be difficult or impossible to make with traditional methods. MIM is ideal for industries such as aerospace, medical devices, and automotive, where precision and performance are paramount.
Key Details
- Process: Combines metal powders and binders, injects into molds, and sinters the parts.
- Applications: Aerospace, automotive, medical devices, consumer electronics.
- Advantages: High precision, complex geometries, material efficiency.
- Disadvantages: Initial setup costs, specific material requirements.
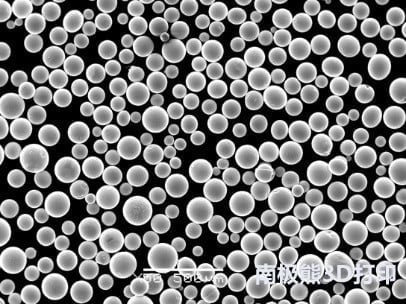
The Process of Metal Injection Molding
MIM involves several steps, each critical to ensuring the final product meets stringent specifications.
Steps Involved:
- Mixing: Metal powders are blended with a thermoplastic binder to form a feedstock.
- Injection Molding: The feedstock is heated and injected into a mold cavity to form a “green” part.
- Debinding: The binder is removed, usually through a chemical process, to leave a porous metal part.
- Sintering: The part is heated to near the melting point of the metal, causing the particles to fuse together.
- Post-Processing: Additional processes such as machining, heat treatment, or surface finishing may be required.
Types of Metal Powders Used in MIM
MIM can utilize a variety of metal powders, each with unique properties and applications. Here’s a detailed look at some of the most commonly used metal powders:
Metal Powder | Composition | Properties | Characteristics |
---|---|---|---|
Stainless Steel 316L | Fe, Cr, Ni, Mo | Corrosion resistance, high strength | Ideal for medical and food industry applications |
Stainless Steel 17-4 PH | Fe, Cr, Ni, Cu, Nb | Precipitation hardening, high strength | Used in aerospace and high-stress environments |
Carbonyl Iron | Fe | High purity, excellent magnetic properties | Suitable for electronic components |
Titanium Ti-6Al-4V | Ti, Al, V | High strength-to-weight ratio, corrosion resistance | Preferred for aerospace and medical implants |
Inconel 718 | Ni, Cr, Fe, Nb, Mo | Heat resistance, high strength | Used in high-temperature environments |
Copper | Cu | High electrical and thermal conductivity | Common in electrical components |
Cobalt-Chrome (Co-Cr) | Co, Cr, Mo | Wear resistance, biocompatibility | Widely used in medical implants |
Tungsten | W | High density, high melting point | Ideal for radiation shielding and aerospace |
Molybdenum | Mo | High melting point, corrosion resistance | Used in high-temperature applications |
Aluminum Al-Si | Al, Si | Lightweight, good thermal properties | Utilized in automotive and aerospace components |
Applications of Metal Injection Molding
MIM is versatile, finding applications across various industries. Here’s a look at some specific uses:
Industry | Application | Details |
---|---|---|
Aerospace | Turbine blades, fasteners | High strength, heat resistance |
Medical Devices | Surgical instruments, orthopedic implants | Biocompatibility, precision |
Automotive | Engine components, gears | Durability, complex geometries |
Consumer Electronics | Connectors, housings | Miniaturization, high volume |
Industrial | Cutting tools, bearings | Wear resistance, toughness |
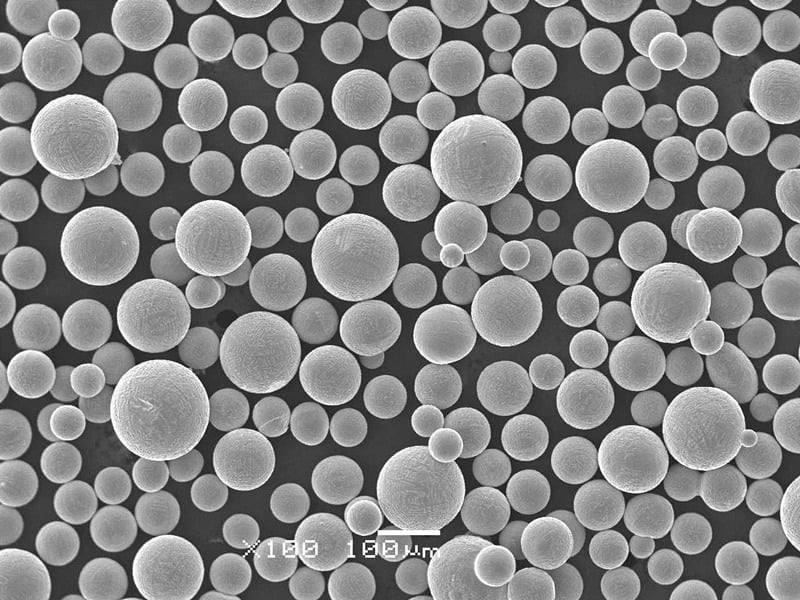
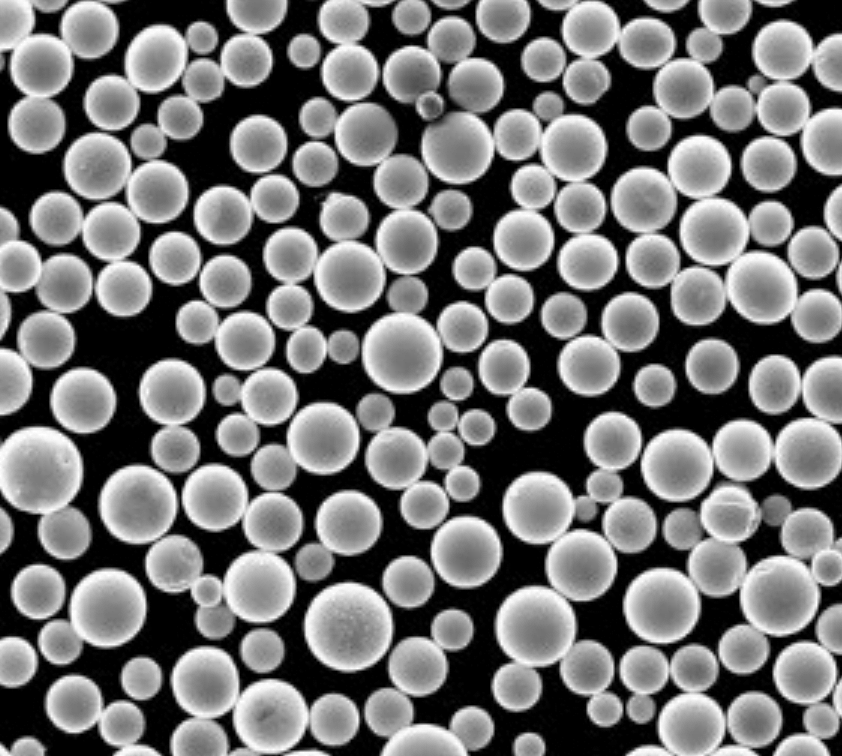
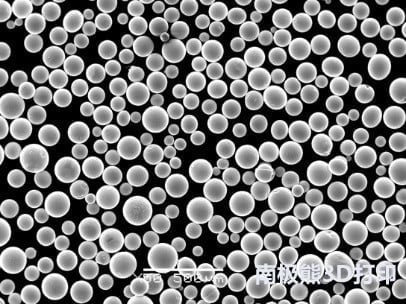
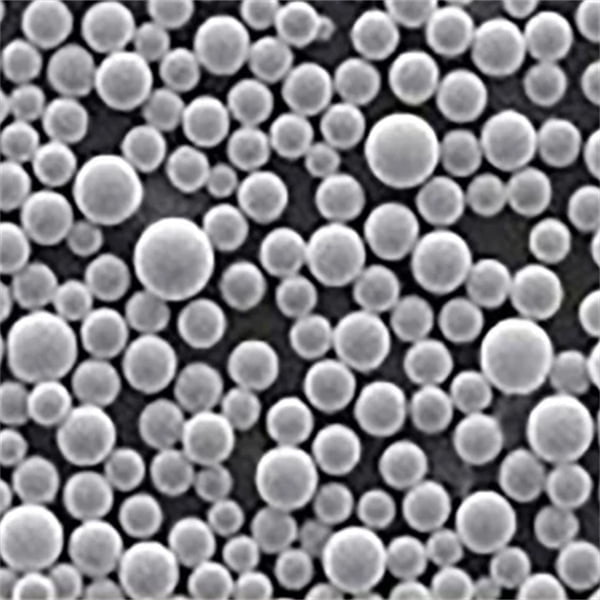
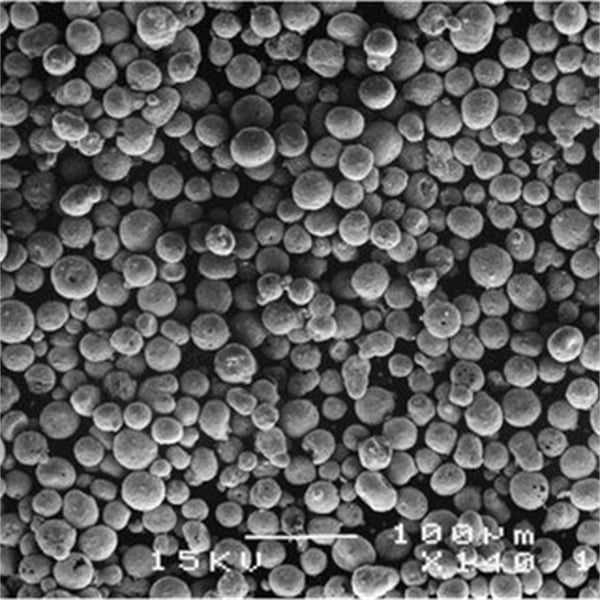
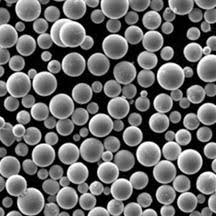
Specifications and Standards for Metal Injection Molding
Ensuring that MIM components meet rigorous specifications is crucial. Standards and specifications vary depending on the industry and application.
Specification | Details | Examples |
---|---|---|
ASTM Standards | Material properties, dimensions | ASTM F2885 (stainless steel), ASTM F75 (cobalt-chrome) |
ISO Standards | Quality management, process control | ISO 9001 (quality management), ISO 13485 (medical devices) |
Grade | Composition, performance | MPIF Standard 35 (metal powders), MIM-316L (specific grade) |
Size | Dimensional tolerances | Varies by part and application |
Surface Finish | Roughness, appearance | Ra value specifications, as low as 0.4 µm |
Suppliers and Pricing Details for Metal Injection Molding
Finding reliable suppliers and understanding pricing is essential for successful MIM projects.
Supplier | Location | Materials | Pricing |
---|---|---|---|
AMT | USA | Stainless steels, titanium | $0.50 – $5.00 per part |
Indo-MIM | India | Various metals | $0.30 – $4.00 per part |
Parmaco | Switzerland | Cobalt-chrome, tool steels | $0.40 – $6.00 per part |
ARC Group Worldwide | USA | Stainless steels, nickel alloys | $0.50 – $7.00 per part |
Dynacast | Global | Aluminum, zinc | $0.20 – $3.00 per part |
Advantages and Limitations of Metal Injection Molding
Understanding the pros and cons of MIM helps in making informed decisions about its application.
Advantages:
- Precision: Achieves complex geometries with high accuracy.
- Material Efficiency: Minimal waste compared to traditional machining.
- Strength: Produces high-strength components.
- Versatility: Can use a wide range of metals.
- Cost-Effective: Economical for high-volume production.
Limitations:
- Initial Costs: High setup costs for tooling and molds.
- Material Restrictions: Limited to specific metal powders.
- Part Size: Generally suitable for smaller components.
- Complexity: Process can be more complex than other manufacturing methods.
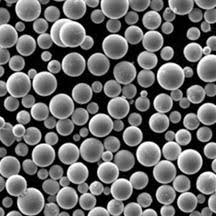
FAQs
Let’s address some common questions about MIM to wrap up this comprehensive guide.
Question | Answer |
---|---|
What is Metal Injection Molding? | MIM is a manufacturing process that combines powdered metals with binders, molded and sintered to create complex metal parts. |
What metals can be used in MIM? | Metals like stainless steel, titanium, nickel alloys, and more. |
What industries use MIM? | Aerospace, medical devices, automotive, consumer electronics, and industrial sectors. |
What are the advantages of MIM? | High precision, material efficiency, strength, versatility, and cost-effectiveness for large volumes. |
What are the limitations of MIM? | High initial costs, material restrictions, part size limitations, and process complexity. |
How does MIM compare to traditional manufacturing? | MIM allows for more complex geometries and material efficiency compared to traditional machining. |
Is MIM cost-effective? | Yes, especially for high-volume production, though initial setup costs are higher. |
What are typical applications of MIM? | High-precision components in aerospace, medical devices, automotive, and electronics. |
Can MIM produce large parts? | Generally, MIM is more suitable for small to medium-sized parts. |
How long does the MIM process take? | It varies by part complexity, but typically involves several stages from mixing to sintering. |
Conclusion
Metal Injection Molding is a powerful and versatile manufacturing technique that has revolutionized the production of complex metal parts. Whether you’re in aerospace, automotive, or medical devices, MIM offers unparalleled precision and efficiency. By understanding its process, materials, and applications, you can leverage MIM to meet your high-precision manufacturing needs. Dive into the world of Metal Injection Molding and unlock new possibilities for your projects.
Thank you for reading! If you have any more questions or need further information, feel free to reach out. Happy manufacturing!
About 3DP mETAL
Product Category
CONTACT US
Any questions? Send us a message now! After receiving your message, we will process your request with a whole team.