Overview of Metal Injection Moulding (MIM)
Metal Injection Moulding (MIM) is a manufacturing process that combines the versatility of plastic injection moulding with the strength and integrity of powdered metallurgy. It’s an ideal method for producing complex, high-volume metal parts with exceptional precision. MIM is particularly advantageous when creating intricate geometries that would be difficult or impossible to achieve with traditional metalworking processes.
The process involves mixing finely powdered metal with a binder material to create a feedstock, which is then shaped into the desired form using injection moulding. After moulding, the part undergoes a debinding process to remove the binder, followed by sintering, where the metal particles fuse together at high temperatures to form a dense, solid part.
Why is MIM Important?
MIM offers several advantages over conventional metalworking techniques, including reduced material waste, lower production costs for high volumes, and the ability to create complex shapes with tight tolerances. This process is particularly valuable in industries such as automotive, aerospace, medical devices, and consumer electronics, where precision and performance are paramount.
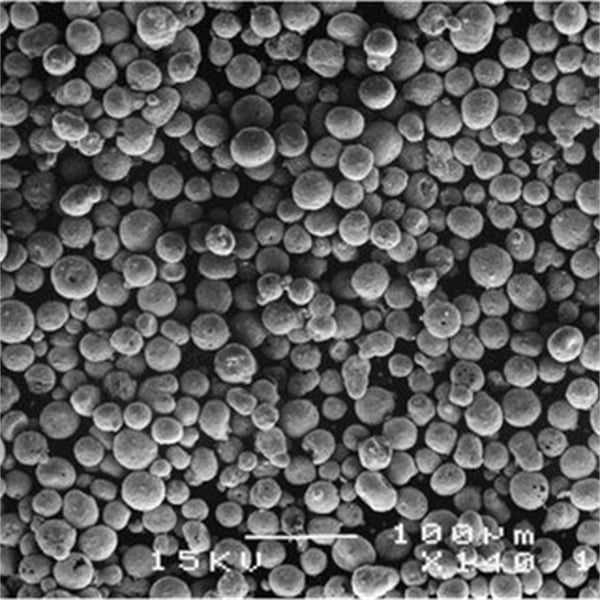
Composition of Metal Injection Moulding Feedstock
The feedstock used in Metal Injection Moulding consists of a blend of metal powders and binders. The choice of metal powder depends on the specific requirements of the final part, including its mechanical properties, corrosion resistance, and cost.
Types of Metal Powders Used in MIM
Metal Powder | Composition | Properties | Common Applications |
---|---|---|---|
316L Stainless Steel | Iron (Fe), Chromium (Cr), Nickel (Ni), Molybdenum (Mo) | High corrosion resistance, excellent mechanical properties | Medical devices, aerospace components, automotive parts |
17-4 PH Stainless Steel | Iron (Fe), Chromium (Cr), Nickel (Ni), Copper (Cu) | High strength, good corrosion resistance | Aerospace, military, and surgical instruments |
Cobalt-Chrome | Cobalt (Co), Chromium (Cr), Molybdenum (Mo) | Exceptional wear and corrosion resistance, biocompatibility | Medical implants, dental prosthetics |
Titanium (Ti-6Al-4V) | Titanium (Ti), Aluminum (Al), Vanadium (V) | High strength-to-weight ratio, excellent corrosion resistance | Aerospace, medical implants, high-performance automotive parts |
Inconel 718 | Nickel (Ni), Chromium (Cr), Iron (Fe), Molybdenum (Mo) | High temperature and corrosion resistance | Turbine blades, aerospace, and chemical processing equipment |
M2 Tool Steel | Iron (Fe), Tungsten (W), Molybdenum (Mo), Vanadium (V) | High hardness, wear resistance | Cutting tools, dies, and molds |
Fe-Ni Soft Magnetic Alloys | Iron (Fe), Nickel (Ni) | High magnetic permeability, low coercivity | Magnetic cores, sensors, and actuators |
Tungsten Heavy Alloys | Tungsten (W), Nickel (Ni), Iron (Fe), Copper (Cu) | High density, radiation shielding | Counterweights, radiation shielding, vibration damping devices |
Copper Alloys | Copper (Cu), Zinc (Zn), Tin (Sn), Nickel (Ni) | High electrical and thermal conductivity | Electrical connectors, heat sinks, plumbing fittings |
Aluminum Alloys | Aluminum (Al), Silicon (Si), Magnesium (Mg) | Lightweight, good corrosion resistance | Automotive components, consumer electronics, aerospace parts |
Key Characteristics of Metal Powders in MIM
The selection of metal powders is critical in determining the final properties of the MIM component. The metal powders must possess the following characteristics:
- Particle Size and Distribution: The powders used in MIM typically have particle sizes ranging from 2 to 20 microns. A narrow particle size distribution is preferred to ensure uniform packing and reduce defects.
- Shape: Spherical powders are generally preferred for MIM because they offer better flow properties and packing density, which are crucial for the injection moulding process.
- Purity: High purity metal powders are essential to avoid contamination, which can lead to defects and reduced mechanical properties in the final part.
- Binder Compatibility: The metal powder must be compatible with the binder used in the feedstock to ensure homogenous mixing and optimal processing.
Characteristics of Metal Injection Moulding
Metal Injection Moulding offers a unique set of characteristics that make it an attractive manufacturing process for various industries. These characteristics stem from the combination of powdered metallurgy and plastic injection moulding techniques.
High Complexity and Precision
MIM is capable of producing parts with complex geometries and fine details that would be challenging to achieve with other manufacturing methods. This precision is particularly beneficial for industries where intricate designs and tight tolerances are essential, such as medical devices and aerospace components.
Material Efficiency
One of the key advantages of MIM is its material efficiency. The process generates minimal waste compared to traditional metalworking methods, as excess material can often be recycled back into the process. This efficiency not only reduces costs but also contributes to sustainability efforts.
Mechanical Properties
Parts produced through MIM exhibit mechanical properties that are comparable to those of wrought materials. The sintering process ensures that the metal particles fuse together to form a dense, solid structure, resulting in parts with high strength, hardness, and wear resistance.
Versatility in Material Choices
MIM is compatible with a wide range of metal powders, allowing manufacturers to select the material that best suits the application. This versatility extends to the ability to create parts with tailored properties, such as specific strength-to-weight ratios, corrosion resistance, or magnetic properties.
Cost-Effectiveness for High Volumes
While the initial tooling and setup costs for MIM can be high, the process becomes highly cost-effective for large production runs. The ability to produce high volumes of complex parts with minimal waste translates into significant cost savings.
Applications of Metal Injection Moulding
Metal Injection Moulding is utilized across a wide range of industries due to its ability to produce complex, high-performance parts at scale. Below, we explore some of the key applications of MIM, highlighting how this process is driving innovation in various sectors.
Automotive Industry
In the automotive sector, MIM is used to produce components that require high precision and strength, such as gear systems, turbocharger parts, and fuel injector nozzles. The process allows for the production of lightweight, durable parts that contribute to improved fuel efficiency and performance.
Aerospace Industry
The aerospace industry benefits from MIM’s ability to produce lightweight, high-strength components that can withstand extreme temperatures and pressures. Common applications include turbine blades, structural components, and fasteners.
Medical Devices
MIM is particularly well-suited for the medical industry, where biocompatibility and precision are critical. The process is used to manufacture surgical instruments, orthodontic brackets, and implantable devices. Materials like titanium and cobalt-chrome are commonly used for their excellent mechanical properties and biocompatibility.
Consumer Electronics
In the consumer electronics sector, MIM is employed to create small, complex components such as connectors, hinges, and casings. The ability to produce parts with fine details and tight tolerances is essential for the miniaturization of electronic devices.
Firearms and Defense
The firearms industry utilizes MIM to produce components like trigger assemblies, sight mounts, and safety mechanisms. The process’s precision and ability to produce high-strength parts make it ideal for manufacturing firearm components that must meet strict safety and performance standards.
Industrial Applications
MIM is also used in various industrial applications, including the production of cutting tools, gears, and fasteners. The process’s ability to create wear-resistant, high-strength parts makes it valuable in industrial settings where durability and performance are critical.
Dental Prosthetics
In the dental industry, MIM is used to produce prosthetic components such as crowns, bridges, and abutments. The process allows for the creation of custom-fitted, biocompatible parts that offer superior strength and longevity compared to traditional materials.
Energy Sector
The energy sector utilizes MIM to manufacture components for power generation and oil and gas exploration. Parts such as turbine blades, valve components, and drilling tools benefit from the process’s ability to produce high-strength, corrosion-resistant parts that can withstand harsh environments.
Jewelry and Luxury Goods
MIM is also gaining traction in the jewelry and luxury goods market, where it is used to produce intricate designs with precious metals. The process allows for the creation of detailed, custom pieces that are both durable and aesthetically pleasing.
Sporting Goods
In the sporting goods industry, MIM is used to produce components for golf clubs, firearms, and high-performance bicycles. The process enables the creation of lightweight, high-strength parts that enhance the performance and durability of sports equipment.
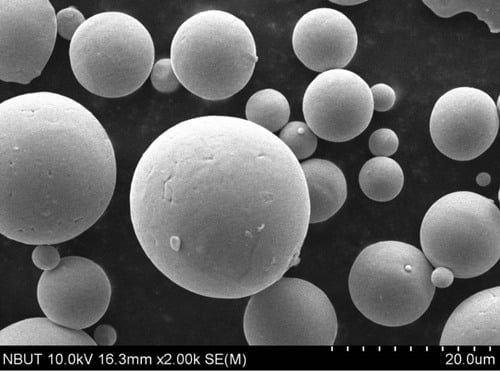
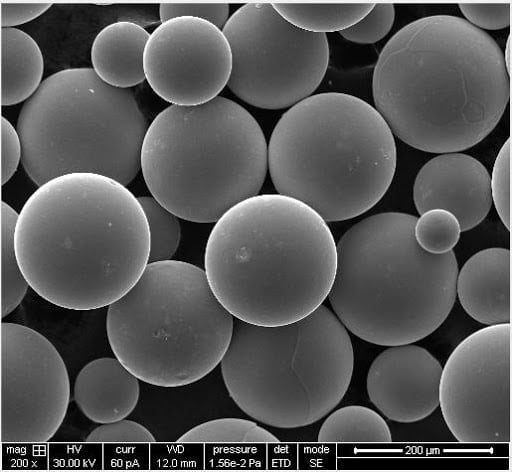
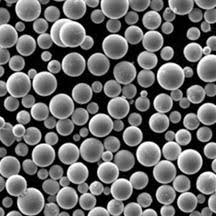
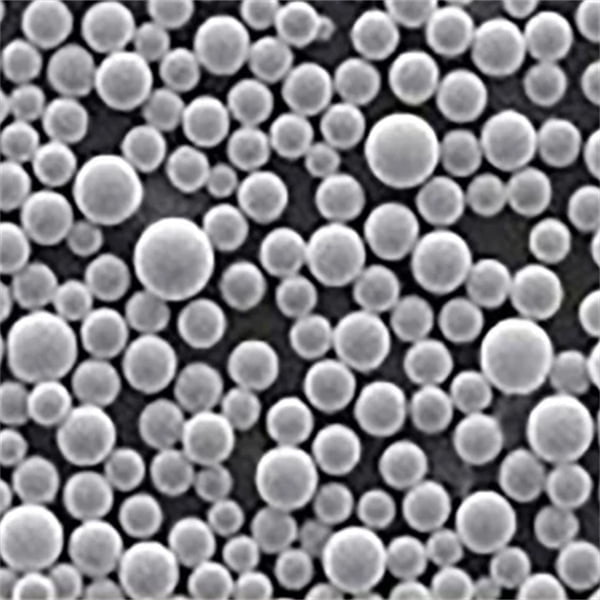
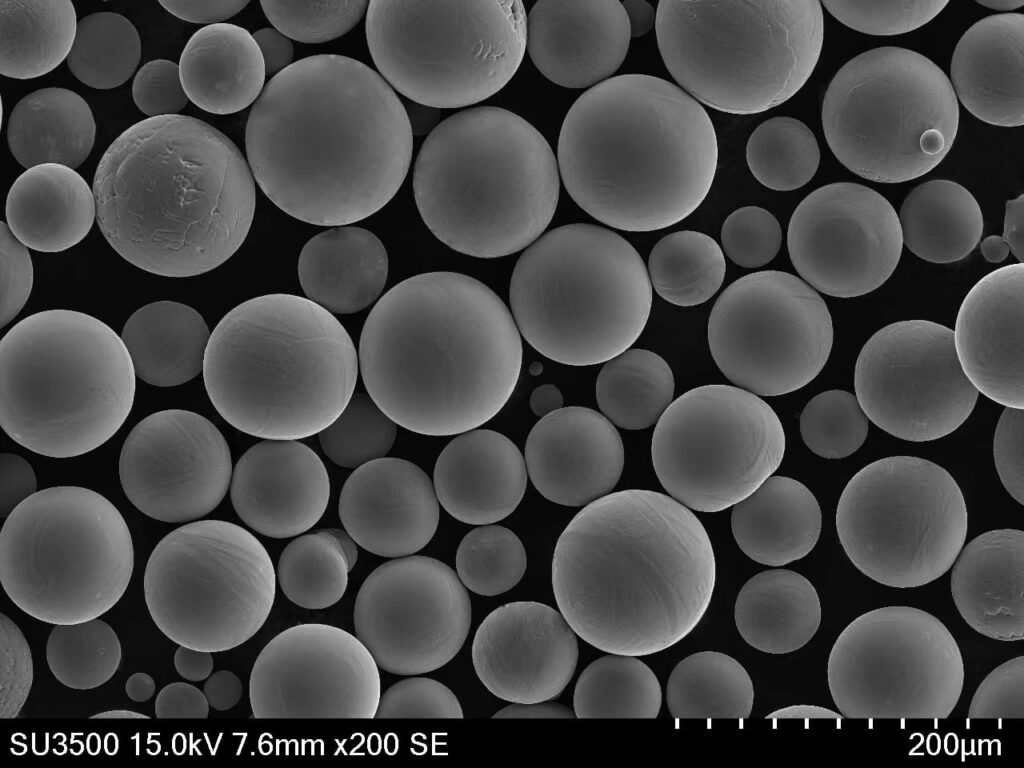
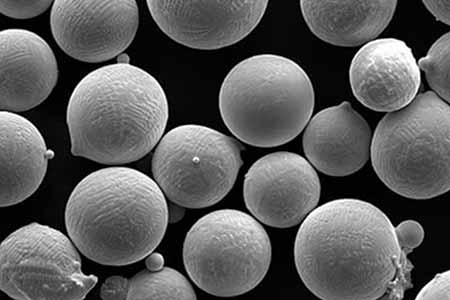
Specifications, Sizes, and Standards in Metal Injection Moulding
When it comes to Metal Injection Moulding, understanding the specifications, sizes, and standards is crucial for ensuring the quality and performance of the final product. These parameters are often dictated by the application and industry requirements.
Common Specifications and Standards
Specification/Standard | Description | Applications |
---|---|---|
ASTM F2885 | Standard specification for MIM of stainless steel alloys | Used in the manufacturing of medical devices, surgical instruments, and aerospace components |
ISO 22068 | International standard for MIM process control and quality assurance | Applied across industries to ensure consistent quality and performance in MIM-produced parts |
MPIF Standard 35 | Material standards for metal powders and sintered metal parts | Widely used in automotive, aerospace, and industrial applications to standardize material properties |
ISO 5755 | Standard for sintered metal components, including tolerances and dimensions | Ensures dimensional accuracy and uniformity in MIM parts |
AMS 7715 | Aerospace material specification for MIM of nickel-based alloys | Essential for aerospace components that require high-temperature resistance and corrosion resistance |
DIN 30910 | German standard for metal injection moulded parts | Commonly used in European manufacturing industries for quality assurance in MIM parts |
JIS Z2550 | Japanese standard for powder metallurgy, including MIM processes | Ensures consistent quality in MIM parts used in automotive and consumer electronics in Japan |
MIL-STD-883 | Military standard for microelectronic components, including MIM parts | Applied in the production of defense and military equipment to ensure reliability and performance |
Size Ranges and Tolerances
MIM allows for the production of parts with a wide range of sizes and tolerances. The size of the part is typically limited by the capacity of the injection moulding machine and the sintering process.
- Part Size: MIM parts typically range from 0.1 grams to 100 grams, with some specialized processes capable of producing parts up to 250 grams.
- Tolerances: Standard tolerances for MIM parts are typically ±0.5% of the dimension, but tighter tolerances of ±0.3% can be achieved with secondary operations.
Material Grades
The material grade used in MIM is selected based on the required mechanical properties, corrosion resistance, and cost considerations. Below are some common material grades used in MIM:
Material Grade | Description | Applications |
---|---|---|
316L (UNS S31603) | Low-carbon austenitic stainless steel with excellent corrosion resistance | Medical implants, aerospace components |
17-4 PH (UNS S17400) | Precipitation-hardening stainless steel with high strength | Aerospace, military, and surgical instruments |
Ti-6Al-4V (Grade 5) | Titanium alloy with a high strength-to-weight ratio | Aerospace, medical implants, high-performance parts |
Inconel 718 (UNS N07718) | Nickel-chromium alloy with high-temperature strength and corrosion resistance | Turbine blades, aerospace, and chemical processing |
Cobalt-Chrome (ASTM F75) | Alloy with exceptional wear and corrosion resistance | Medical implants, dental prosthetics |
Suppliers and Pricing Details for Metal Injection Moulding
The supply chain for MIM materials and services is global, with numerous suppliers offering a wide range of metal powders, binders, and MIM processing equipment. Pricing varies depending on the material, part complexity, and production volume.
Key Suppliers in the MIM Industry
Supplier | Products Offered | Location | Price Range |
---|---|---|---|
Advanced Metalworking | Metal powders, binders, MIM equipment | USA | $50 – $200/kg (powders) |
Sandvik Materials | High-performance metal powders | Sweden | $80 – $250/kg (depending on alloy) |
GKN Hoeganaes | Metal powders, custom MIM solutions | USA | $60 – $180/kg |
Hitachi Metals | Specialty metal powders, MIM parts | Japan | $90 – $300/kg |
Molyworks Materials | Recycled metal powders, sustainable MIM solutions | USA | $70 – $220/kg |
Carpenter Technology | Premium metal powders, aerospace-grade materials | USA | $100 – $350/kg |
CNPC Powder | Wide range of metal powders for MIM | China | $40 – $150/kg |
Epson Atmix | Ultra-fine metal powders, MIM binders | Japan | $100 – $300/kg |
HC Starck Solutions | Refractory metals, MIM powders | Germany | $120 – $400/kg (for Tungsten alloys) |
Mimete Srl | Custom MIM powders and services | Italy | $80 – $250/kg |
Pricing Considerations
The cost of MIM parts is influenced by several factors, including:
- Material Type: High-performance materials like titanium and Inconel are more expensive than standard stainless steels.
- Part Complexity: More complex parts with intricate geometries may require more advanced tooling and longer production times, increasing costs.
- Production Volume: Higher production volumes typically lead to lower per-part costs due to economies of scale.
- Secondary Operations: Additional processes like machining, heat treatment, or surface finishing can add to the overall cost of MIM parts.
Advantages and Disadvantages of Metal Injection Moulding
While Metal Injection Moulding offers numerous benefits, it also comes with certain limitations. Understanding these pros and cons is essential for determining whether MIM is the right manufacturing process for a particular application.
Advantages of Metal Injection Moulding
Advantage | Description |
---|---|
Complex Geometry | MIM can produce parts with intricate designs and fine details that are difficult to achieve with other methods. |
High Precision | The process allows for tight tolerances and precise dimensions, essential for critical applications. |
Material Efficiency | MIM generates minimal waste, making it a cost-effective and environmentally friendly process. |
Versatility | MIM is compatible with a wide range of materials, allowing for customization of part properties. |
Scalability | The process is highly scalable, making it ideal for large production runs. |
Disadvantages of Metal Injection Moulding
Disadvantage | Description |
---|---|
High Initial Costs | The initial tooling and setup costs for MIM can be high, making it less economical for small production runs. |
Material Limitations | Not all metals are suitable for MIM, and the process may not be ideal for very large or very small parts. |
Debinding and Sintering Complexity | The debinding and sintering steps require precise control to avoid defects and ensure consistent quality. |
Post-Processing Requirements | Some parts may require additional machining, heat treatment, or surface finishing, adding to the overall cost. |
Cycle Time | MIM typically has longer cycle times compared to plastic injection moulding, due to the additional sintering process. |
Metal Injection Moulding Process Flow
Understanding the process flow of Metal Injection Moulding is crucial for optimizing production and ensuring high-quality parts. The process can be broken down into several key steps, each of which plays a critical role in the final product’s quality and performance.
1. Feedstock Preparation
The first step in the MIM process is preparing the feedstock, a mixture of metal powders and a binder system. The binder helps to bind the metal particles together, allowing them to be moulded into the desired shape. The feedstock is typically prepared by mixing the metal powder with the binder at elevated temperatures to ensure homogeneity.
2. Injection Moulding
Once the feedstock is prepared, it is fed into an injection moulding machine. The machine heats the feedstock to a temperature where the binder becomes fluid, allowing the material to be injected into a mould cavity. The mould is designed to shape the feedstock into the desired geometry, with complex features and fine details. After injection, the moulded part, known as a “green part,” is cooled and ejected from the mould.
3. Debinding
The green part still contains a significant amount of binder, which must be removed before sintering. The debinding process typically involves a combination of solvent extraction and thermal decomposition. During solvent extraction, the part is immersed in a solvent that dissolves the primary binder component. This is followed by thermal debinding, where the remaining binder is removed by heating the part in a controlled atmosphere.
4. Sintering
After debinding, the part is sintered at high temperatures, typically between 1,200°C and 1,450°C, depending on the material. During sintering, the metal particles fuse together, resulting in a dense, solid part with properties similar to those of wrought materials. The sintering process also causes the part to shrink, usually by about 15-20%, which must be accounted for during the
design phase.
5. Post-Processing
In some cases, MIM parts may require additional post-processing steps to achieve the desired properties or finish. Common post-processing operations include machining, heat treatment, surface finishing, and coating. These steps can help to improve the dimensional accuracy, mechanical properties, and aesthetics of the final part.
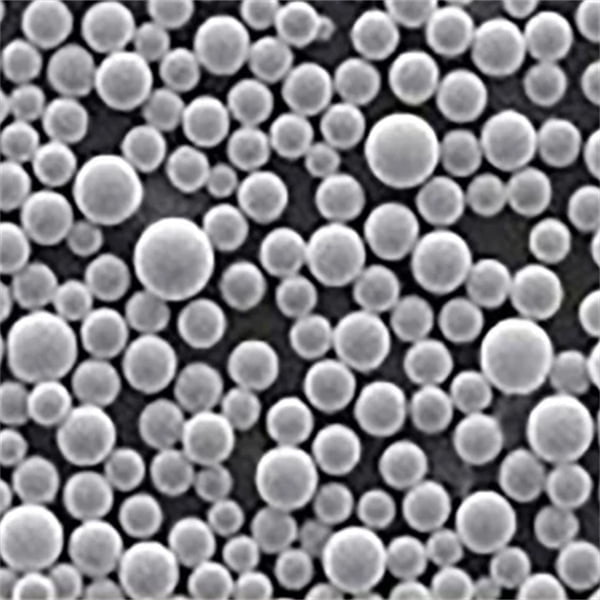
FAQ
Question | Answer |
---|---|
What is MIM? | Metal Injection Moulding (MIM) is a manufacturing process that combines the techniques of plastic injection moulding and powdered metallurgy to produce complex metal parts with high precision. |
What materials can be used in MIM? | A wide range of materials can be used in MIM, including stainless steel, titanium, cobalt-chrome, and various nickel-based alloys. |
What are the advantages of MIM? | MIM offers several advantages, including the ability to produce complex geometries, high material efficiency, and scalability for large production runs. |
What are the limitations of MIM? | Some limitations of MIM include high initial costs, material limitations, and the need for precise control during the debinding and sintering processes. |
How does MIM compare to traditional manufacturing methods? | Compared to traditional methods like machining or casting, MIM is more suitable for high-volume production of complex parts with tight tolerances and minimal waste. |
What industries use MIM? | MIM is used in a variety of industries, including automotive, aerospace, medical devices, consumer electronics, and firearms. |
What are the typical sizes of MIM parts? | MIM parts typically range in size from 0.1 grams to 100 grams, with some processes capable of producing parts up to 250 grams. |
Can MIM parts be post-processed? | Yes, MIM parts can undergo post-processing steps such as machining, heat treatment, and surface finishing to enhance their properties and finish. |
What is the cost of MIM parts? | The cost of MIM parts varies depending on the material, complexity, and production volume. However, MIM is generally cost-effective for large production runs. |
What are the typical applications of MIM? | Typical applications of MIM include automotive components, aerospace parts, medical devices, and consumer electronics. |
Conclusion
Metal Injection Moulding is a transformative manufacturing process that continues to gain traction across a wide range of industries. Its ability to produce complex, high-performance parts with exceptional precision and material efficiency makes it a valuable tool for modern manufacturing. As technology advances and new materials are developed, the potential applications for MIM will only continue to expand.
Whether you’re in the automotive, aerospace, medical, or electronics industry, understanding the capabilities and benefits of MIM can help you make informed decisions about your manufacturing processes. With its unique combination of versatility, scalability, and precision, Metal Injection Moulding is poised to play a critical role in the future of manufacturing.
About 3DP mETAL
Product Category
CONTACT US
Any questions? Send us a message now! After receiving your message, we will process your request with a whole team.