Overview of Metal Powder Atomization
Metal powder atomization is a fascinating and complex process that plays a critical role in various industries, from aerospace and automotive to medical and electronics. At its core, atomization involves transforming molten metal into fine powder particles, which can then be used in additive manufacturing (3D printing), powder metallurgy, and other high-precision applications. But what makes this process so special? Let’s dive deep into the world of metal powder atomization, exploring its types, techniques, benefits, and the specific metal powder models that are revolutionizing the industry.
Types of Metal Powder Atomization
Different atomization techniques are employed to produce metal powders, each with its own unique set of characteristics and suitable applications. Here’s a breakdown of the primary methods:
Gas Atomization
Gas atomization uses a high-pressure gas stream to disintegrate molten metal into fine droplets, which solidify into powder particles. This method is widely used for its ability to produce highly spherical particles with a uniform size distribution.
Water Atomization
In water atomization, a high-pressure water jet is used to atomize molten metal. This technique is cost-effective and suitable for producing irregularly shaped particles, making it ideal for applications requiring high surface area powders.
Centrifugal Atomization
Centrifugal atomization involves rotating a crucible at high speeds to fling molten metal outward, forming droplets that solidify into powder. This method is used for producing coarse powders with high purity levels.
Ultrasonic Atomization
Ultrasonic atomization employs high-frequency sound waves to create vibrations that break up the molten metal into fine droplets. It’s known for producing very fine and uniform powders, albeit at a higher cost.
Plasma Atomization
In plasma atomization, a plasma torch melts the metal, and the molten metal is atomized by the plasma gas flow. This technique is particularly used for producing high-purity, spherical powders for critical applications like biomedical implants and aerospace components.
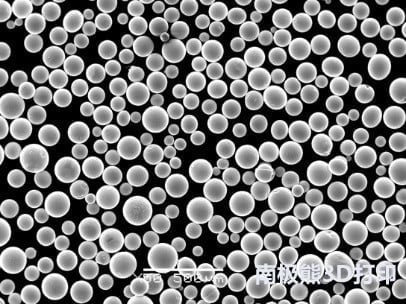
Detailed Metal Powder Models
Here’s a look at ten specific metal powder models, detailing their compositions, properties, and applications:
Model | Composition | Properties | Applications |
---|---|---|---|
316L Stainless Steel | Fe-Cr-Ni-Mo | Corrosion-resistant, high strength | Medical implants, aerospace components |
Ti-6Al-4V | Ti-Al-V | High strength-to-weight ratio, biocompatible | Aerospace, medical devices, automotive |
Inconel 718 | Ni-Cr-Fe | High temperature and corrosion resistance | Gas turbines, jet engines, nuclear reactors |
AlSi10Mg | Al-Si-Mg | Lightweight, good thermal conductivity | Automotive, aerospace, heat exchangers |
Copper | Cu | Excellent electrical and thermal conductivity | Electronics, heat sinks, 3D printing |
Cobalt-Chrome | Co-Cr | High wear resistance, biocompatible | Dental implants, orthopedic implants |
H13 Tool Steel | Fe-Cr-Mo-V | High hardness, thermal fatigue resistance | Injection molds, die casting |
Nickel 625 | Ni-Cr-Mo | Excellent fatigue and thermal resistance | Marine applications, chemical processing |
Tungsten Carbide | WC-Co | Extremely hard, wear-resistant | Cutting tools, mining equipment |
Aluminum 6061 | Al-Mg-Si | High strength, lightweight | Structural components, automotive parts |
Applications of Metal Powder Atomization
Metal powders produced through atomization are used in a wide array of industries. Here’s a look at some of the most significant applications:
Industry | Applications |
---|---|
Aerospace | Engine components, structural parts, turbine blades |
Automotive | Engine parts, lightweight structures, brake components |
Medical | Implants, prosthetics, surgical instruments |
Electronics | Conductive inks, heat sinks, connectors |
Manufacturing | Additive manufacturing, powder metallurgy |
Tooling | Cutting tools, molds, dies |
Energy | Nuclear reactors, power generation components |
Advantages of Metal Powder Atomization
Metal powder atomization offers numerous benefits, making it a preferred choice for high-precision manufacturing processes.
High Purity and Consistency
The atomization process allows for the production of powders with high purity levels and consistent particle sizes, essential for critical applications.
Versatility
Different atomization techniques can produce a wide range of powder sizes and shapes, catering to diverse industrial needs.
Enhanced Mechanical Properties
Atomized metal powders often exhibit superior mechanical properties, such as improved strength, wear resistance, and thermal stability.
Cost-Effectiveness
Although some atomization methods are more expensive, the overall cost-effectiveness comes from the high yield and minimal waste associated with these processes.
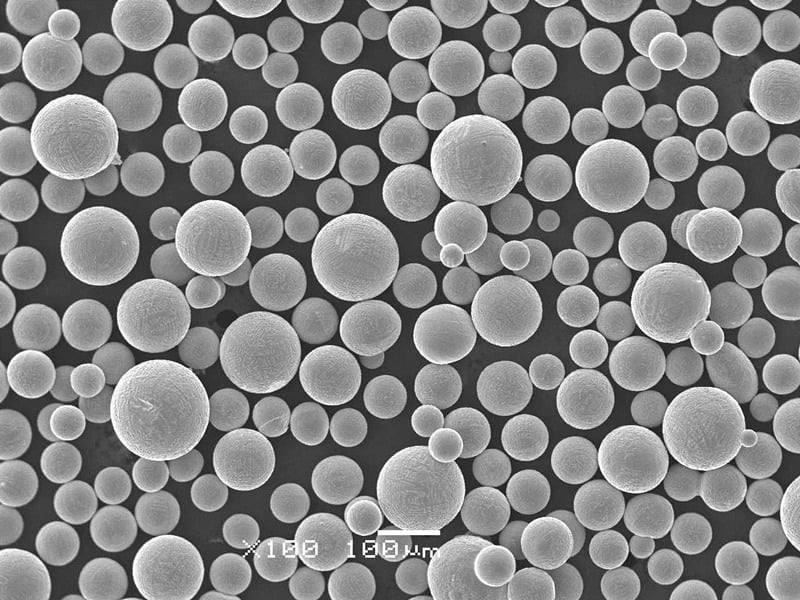
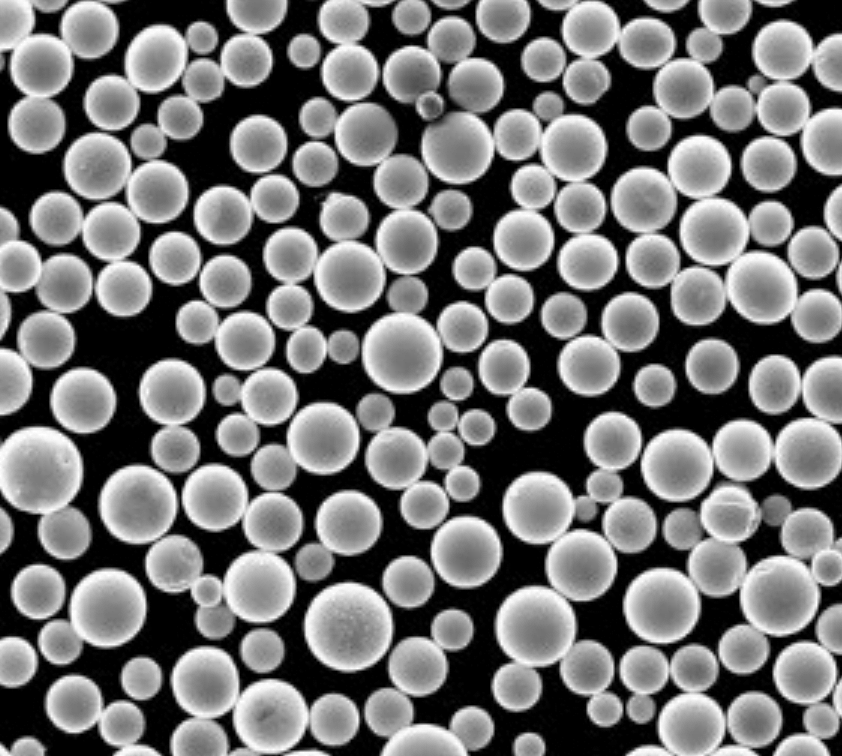
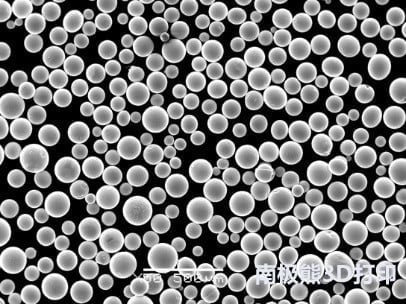
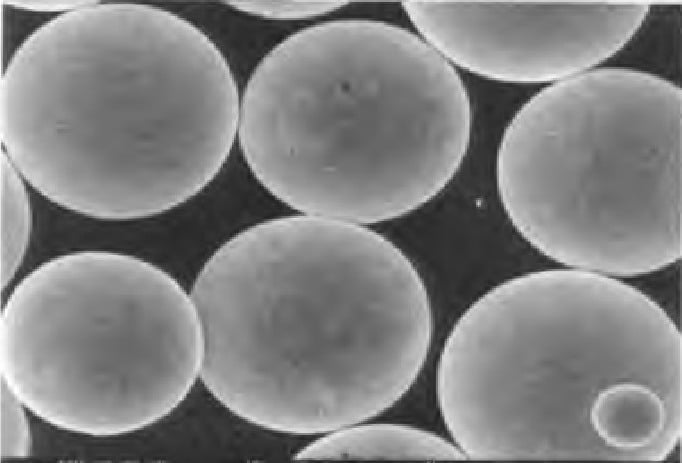
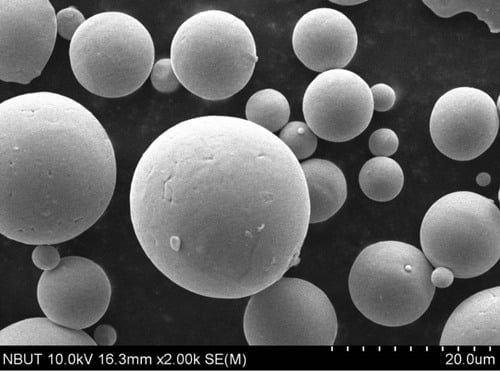
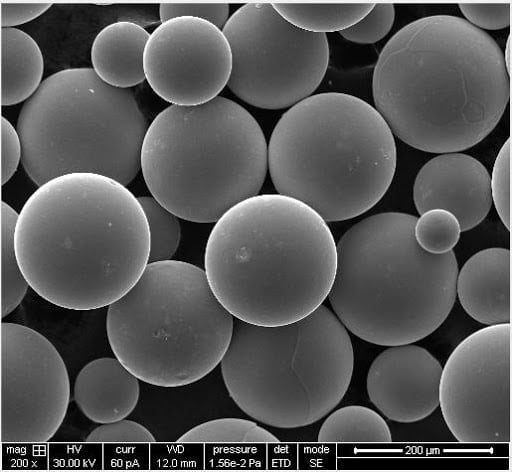
Disadvantages of Metal Powder Atomization
Despite its many benefits, metal powder atomization does have some limitations.
High Initial Cost
The setup costs for atomization equipment and technology can be quite high, posing a barrier for smaller enterprises.
Energy Intensive
Some atomization methods, like plasma and ultrasonic atomization, require significant energy inputs, increasing operational costs.
Complex Process Control
Maintaining precise control over the atomization process can be challenging, necessitating skilled operators and advanced monitoring systems.
Specifications, Sizes, Grades, and Standards
Metal powders are classified based on various specifications, sizes, grades, and standards to ensure they meet industry requirements.
Specification | Details |
---|---|
Particle Size | Ranges from nanometers to micrometers, tailored per application |
Purity | Varies by model, typically >99% for high-end applications |
Density | Measured in g/cm³, affects material performance |
Flowability | Assessed for powder handling and processing |
Sphericity | Indicates the roundness of particles, crucial for 3D printing |
Standards | ASTM, ISO, AMS, MIL, DIN |
Suppliers and Pricing Details
Various suppliers offer metal powders with differing prices based on composition, purity, and quantity. Here are some examples:
Supplier | Product | Price (per kg) | Contact |
---|---|---|---|
Höganäs | 316L Stainless Steel | $150 | www.hoganas.com |
Sandvik | Ti-6Al-4V | $200 | www.materials.sandvik |
LPW Technology | Inconel 718 | $250 | www.lpwtechnology.com |
Carpenter Powder | AlSi10Mg | $180 | www.carpentertechnology.com |
Tekna | Copper | $100 | www.tekna.com |
Oerlikon | Cobalt-Chrome | $220 | www.oerlikon.com |
GKN Powder Metallurgy | H13 Tool Steel | $140 | www.gknpm.com |
Advanced Powders | Nickel 625 | $230 | www.advancedpowders.com |
Kennametal | Tungsten Carbide | $300 | www.kennametal.com |
American Elements | Aluminum 6061 | $120 | www.americanelements.com |
Comparing Metal Powder Atomization Methods
Here’s a comparative analysis of different atomization methods based on various parameters:
Parameter | Gas Atomization | Water Atomization | Centrifugal Atomization | Ultrasonic Atomization | Plasma Atomization |
---|---|---|---|---|---|
Particle Shape | Spherical | Irregular | Coarse | Fine and Uniform | Highly Spherical |
Purity Level | High | Moderate | High | Very High | Extremely High |
Cost | Moderate | Low | Moderate | High | Very High |
Energy Consumption | Moderate | Low | Moderate | High | Very High |
Application Suitability | Wide | Industrial | Specialty | High Precision | Critical Applications |
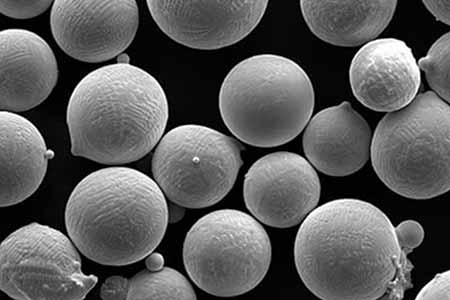
FAQs
Q: What is metal powder atomization?
A: Metal powder atomization is a process where molten metal is disintegrated into fine particles to create metal powders used in various manufacturing processes.
Q: What are the benefits of gas atomization?
A: Gas atomization produces highly spherical and consistent particles, offering high purity and excellent mechanical properties.
Q: Which industries use atomized metal powders?
A: Industries like aerospace, automotive, medical, electronics, and manufacturing utilize atomized metal powders for various applications.
Q: What factors affect the cost of metal powders?
A: Factors include the type of metal, atomization method, particle size, purity level, and supplier pricing.
Q: How is particle size controlled during atomization?
A: Particle size is controlled by adjusting the atomization parameters such as gas or liquid pressure, temperature, and flow rate.
Q: What are the environmental impacts of metal powder atomization?
A: Energy consumption and emissions from certain atomization methods can impact the environment, though efforts are being made to develop more sustainable practices.
Q: Can metal powders be recycled?
A: Yes, metal powders can be recycled and reused in various applications, contributing to sustainability in manufacturing.
Conclusion
Metal powder atomization is a pivotal technology in modern manufacturing, enabling the production of high-quality metal powders for a diverse range of applications. From aerospace components to medical implants, the atomized powders offer unparalleled advantages in terms of purity, consistency, and mechanical properties. By understanding the different atomization methods, specific metal powder models, and their applications, industries can make informed decisions to optimize their manufacturing processes. As technology advances, we can expect even more innovative applications and improvements in metal powder atomization, driving the future of high-precision manufacturing.
About 3DP mETAL
Product Category
CONTACT US
Any questions? Send us a message now! After receiving your message, we will process your request with a whole team.