Welcome to the fascinating world of metallic powders! If you’ve ever been curious about the tiny particles that make up some of the most innovative materials in modern manufacturing, you’re in the right place. This guide will delve deep into metallic powders, exploring their types, compositions, properties, applications, and much more. Whether you’re a seasoned engineer, a curious student, or just someone with a keen interest in materials science, there’s something here for you.
Overview of Metallic Powders
Metallic powders are fine particles of metals used in various industrial applications. These powders are essential in manufacturing, offering unique properties that make them suitable for creating complex shapes, achieving specific mechanical properties, and producing materials with enhanced performance characteristics. From additive manufacturing (3D printing) to powder metallurgy and beyond, metallic powders play a crucial role in modern technology.
Key Details
- Definition: Finely divided particles of metal.
- Production Methods: Atomization, reduction, electrolysis, mechanical alloying.
- Applications: Additive manufacturing, powder metallurgy, thermal spraying, MIM (Metal Injection Molding).
- Advantages: High precision, material efficiency, complex shapes, customizable properties.
- Disadvantages: Cost, handling hazards, powder consistency.
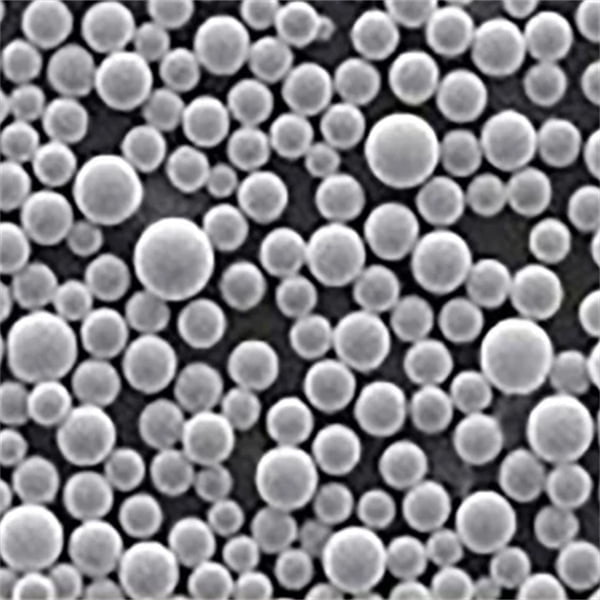
Types of Metallic Powders
1. Aluminum Powder
Aluminum powder is lightweight, corrosion-resistant, and highly conductive. It’s widely used in automotive parts, aerospace components, and fireworks.
Composition: Pure aluminum or aluminum alloys.
Properties:
- Lightweight
- High thermal and electrical conductivity
- Good corrosion resistance
Applications:
- Automotive parts
- Aerospace components
- Additive manufacturing
2. Copper Powder
Copper powder is known for its excellent electrical and thermal conductivity. It’s a key material in electronics, batteries, and conductive inks.
Composition: Pure copper or copper alloys.
Properties:
- Excellent electrical conductivity
- High thermal conductivity
- Antimicrobial properties
Applications:
- Electronics
- Batteries
- Conductive inks
3. Iron Powder
Iron powder is versatile, used in various applications from automotive to industrial manufacturing. It’s known for its magnetic properties and strength.
Composition: Pure iron or iron alloys.
Properties:
- High magnetic permeability
- Strong and durable
- Cost-effective
Applications:
- Powder metallurgy
- Magnetic materials
- Automotive parts
4. Titanium Powder
Titanium powder is highly valued for its strength, lightweight nature, and corrosion resistance, making it ideal for aerospace and medical implants.
Composition: Pure titanium or titanium alloys.
Properties:
- High strength-to-weight ratio
- Excellent corrosion resistance
- Biocompatible
Applications:
- Aerospace components
- Medical implants
- Additive manufacturing
5. Nickel Powder
Nickel powder is used in batteries, catalysts, and electronics due to its excellent corrosion resistance and high-temperature stability.
Composition: Pure nickel or nickel alloys.
Properties:
- Excellent corrosion resistance
- High-temperature stability
- Good mechanical properties
Applications:
- Batteries
- Catalysts
- Electronics
6. Stainless Steel Powder
Stainless steel powder combines the benefits of iron and chromium, offering corrosion resistance and strength. It’s used in a wide range of applications.
Composition: Iron-chromium alloys.
Properties:
- Corrosion resistance
- High strength
- Wear resistance
Applications:
- Medical devices
- Food processing equipment
- Additive manufacturing
7. Cobalt Powder
Cobalt powder is crucial in high-performance alloys and battery materials, known for its magnetic properties and high melting point.
Composition: Pure cobalt or cobalt alloys.
Properties:
- High melting point
- Magnetic properties
- Wear resistance
Applications:
- High-performance alloys
- Batteries
- Cutting tools
8. Zinc Powder
Zinc powder is widely used in protective coatings and batteries due to its anti-corrosion properties and electrochemical behavior.
Composition: Pure zinc or zinc alloys.
Properties:
- Anti-corrosion properties
- Good electrochemical behavior
- High reactivity
Applications:
- Protective coatings
- Batteries
- Chemical reagents
9. Tungsten Powder
Tungsten powder is used in high-temperature applications and radiation shielding, valued for its high density and melting point.
Composition: Pure tungsten or tungsten alloys.
Properties:
- High density
- High melting point
- Excellent wear resistance
Applications:
- High-temperature applications
- Radiation shielding
- Cutting tools
10. Magnesium Powder
Magnesium powder is lightweight and has high specific strength, used in aerospace, automotive, and electronics industries.
Composition: Pure magnesium or magnesium alloys.
Properties:
- Lightweight
- High specific strength
- Good machinability
Applications:
- Aerospace components
- Automotive parts
- Electronics
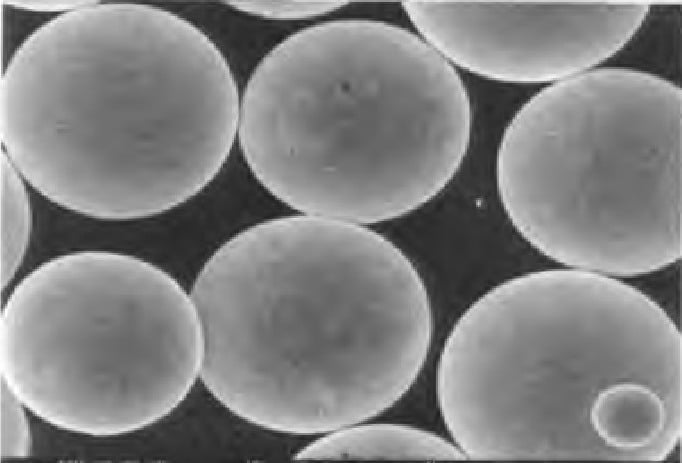
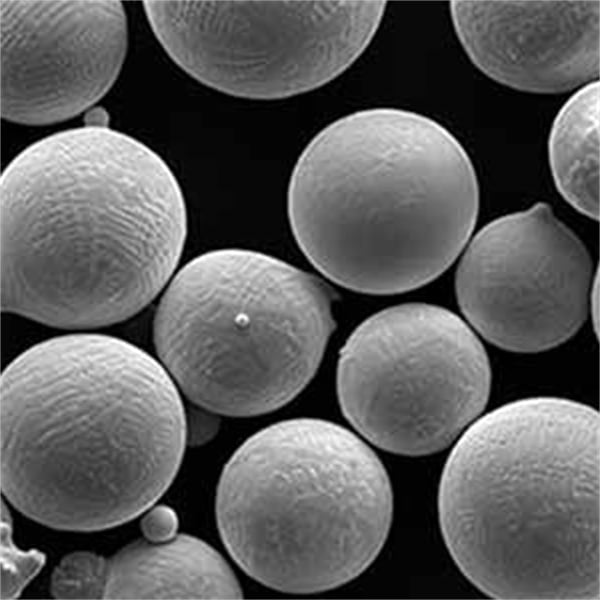
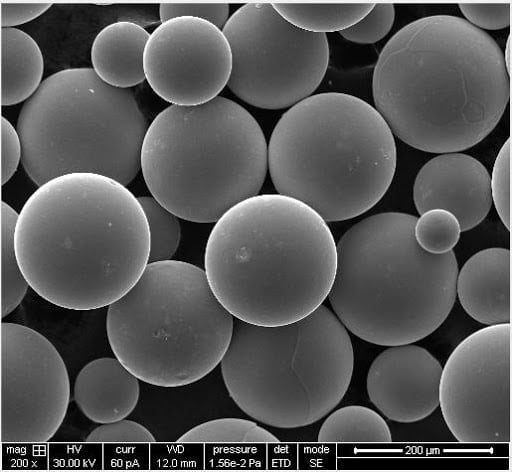
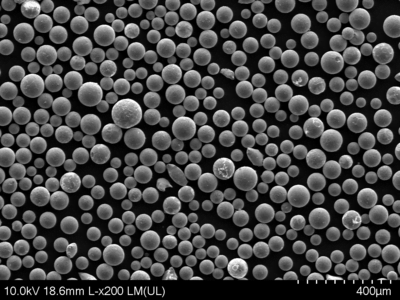
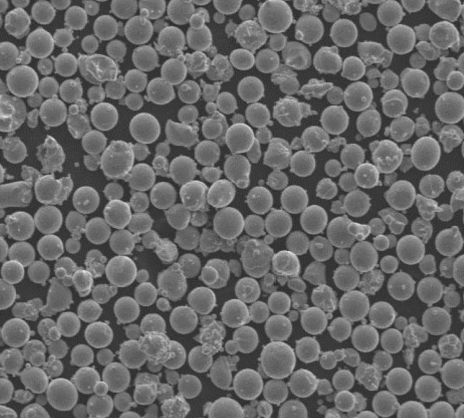
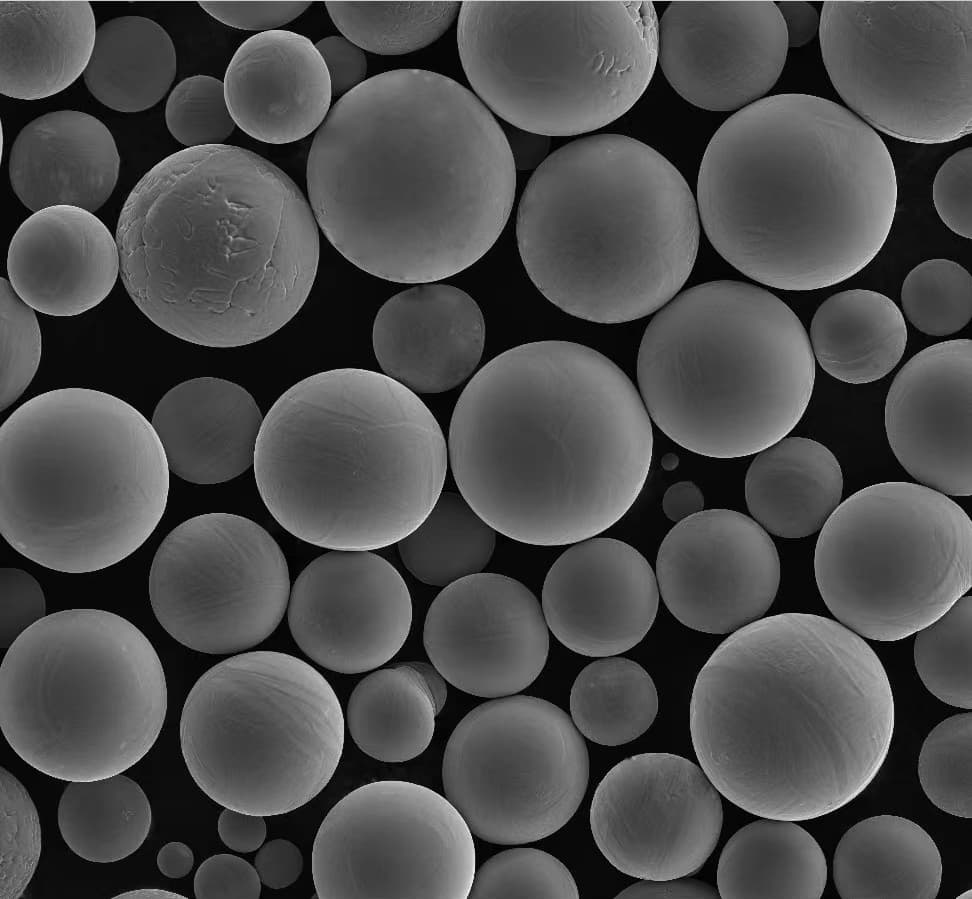
Properties and Characteristics of Metallic Powders
Type | Composition | Properties | Applications |
---|---|---|---|
Aluminum Powder | Pure aluminum or alloys | Lightweight, conductive, corrosion-resistant | Automotive, aerospace, fireworks |
Copper Powder | Pure copper or alloys | Conductive, antimicrobial | Electronics, batteries, conductive inks |
Iron Powder | Pure iron or alloys | Magnetic, strong, cost-effective | Powder metallurgy, automotive |
Titanium Powder | Pure titanium or alloys | Strong, lightweight, biocompatible | Aerospace, medical implants |
Nickel Powder | Pure nickel or alloys | Corrosion-resistant, stable at high temps | Batteries, catalysts, electronics |
Stainless Steel Powder | Iron-chromium alloys | Corrosion-resistant, strong, wear-resistant | Medical devices, food processing |
Cobalt Powder | Pure cobalt or alloys | High melting point, magnetic, wear-resistant | High-performance alloys, batteries |
Zinc Powder | Pure zinc or alloys | Anti-corrosion, electrochemical | Protective coatings, batteries |
Tungsten Powder | Pure tungsten or alloys | High density, high melting point, wear-resistant | High-temp applications, radiation shielding |
Magnesium Powder | Pure magnesium or alloys | Lightweight, high specific strength, machinable | Aerospace, automotive, electronics |
Applications of Metallic Powders
Additive Manufacturing
Additive manufacturing, or 3D printing, is revolutionizing how we produce complex parts. Metallic powders are essential in this process, allowing for high precision and material efficiency. Metals like titanium and aluminum are particularly popular in aerospace and medical industries due to their lightweight and strong properties.
Powder Metallurgy
Powder metallurgy is a manufacturing process where metallic powders are compacted and sintered to create solid parts. This method is cost-effective and allows for producing components with intricate shapes and specific properties, commonly used in automotive and industrial applications.
Thermal Spraying
Thermal spraying involves spraying metallic powders onto surfaces to create coatings that enhance wear resistance, corrosion resistance, or thermal insulation. This technique is widely used in aerospace, automotive, and industrial machinery.
Metal Injection Molding (MIM)
MIM combines the versatility of plastic injection molding with the strength and integrity of metal. Metallic powders are mixed with a binder to create a feedstock, which is then injected into a mold. This process is ideal for producing small, complex parts with high precision.
Batteries
Metallic powders like nickel and cobalt are crucial in battery production, especially in rechargeable batteries like lithium-ion. These metals provide the necessary electrochemical properties to store and release energy efficiently.
Electronics
Copper and silver powders are commonly used in electronics due to their excellent electrical conductivity. They are used in conductive inks, printed circuits, and various electronic components.
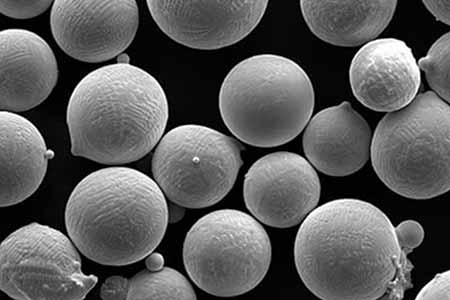
Comparing Metallic Powders: Advantages and Disadvantages
Type | Advantages | Disadvantages |
---|---|---|
Aluminum Powder | Lightweight, corrosion-resistant, conductive | Can be expensive, handling hazards |
Copper Powder | Excellent conductivity, antimicrobial | Oxidizes easily, relatively expensive |
Iron Powder | Cost-effective, strong, magnetic | Prone to rust, requires protective coating |
Titanium Powder | High strength-to-weight ratio, biocompatible | Expensive, reactive in powder form |
Nickel Powder | Corrosion-resistant, high-temp stability | Expensive, health hazards if inhaled |
Stainless Steel Powder | Corrosion-resistant, strong | Expensive, harder to machine |
Cobalt Powder | High melting point, magnetic, wear-resistant | Expensive, toxic if not handled properly |
Zinc Powder | Anti-corrosion, good electrochemical behavior | Can react with moisture, handling hazards |
Tungsten Powder | High density, high melting point, wear-resistant | Very dense, hard to work with |
Magnesium Powder | Lightweight, high specific strength, machinable | Highly reactive, flammable in powder form |
Specifications, Sizes, Grades, Standards
Specifications and Sizes
Type | Size Range | Common Grades | Standards |
---|---|---|---|
Aluminum Powder | 1-100 µm | 1050, 1100, 2024 | ASTM B928, ISO 6361 |
Copper Powder | 0.5-45 µm | C11000, C10100 | ASTM B170,ISO 4503 |
Iron Powder | 1-200 µm | A1000, ASC100.29 | ASTM B783, ISO 4497 |
Titanium Powder | 10-500 µm | CP1, Ti6Al4V | ASTM B348, ISO 5832-2 |
Nickel Powder | 2-150 µm | Ni201, Ni205 | ASTM B330, ISO 6284 |
Stainless Steel Powder | 5-150 µm | 304L, 316L | ASTM A276, ISO 4954 |
Cobalt Powder | 1-100 µm | CoCrMo, CoCrFeNi | ASTM F75, ISO 5832-12 |
Zinc Powder | 0.5-50 µm | Zn22, Zn94 | ASTM B860, ISO 3549 |
Tungsten Powder | 0.1-200 µm | W1, W2 | ASTM B777, ISO 6848 |
Magnesium Powder | 1-500 µm | AZ31B, WE43 | ASTM B107, ISO 16220 |
Suppliers and Pricing Details
Supplier | Metallic Powders Available | Price Range (per kg) | Website |
---|---|---|---|
Advanced Materials | Aluminum, Titanium, Copper, Nickel | $20 – $200 | www.advancedmaterials.com |
Global Metal Powders | Iron, Stainless Steel, Zinc, Magnesium | $10 – $150 | www.globalmetalpowders.com |
Powder Alloy Corporation | Cobalt, Nickel, Tungsten | $50 – $300 | www.powderalloycorp.com |
AMETEK Specialty Metal Products | Aluminum, Iron, Stainless Steel | $30 – $250 | www.ametekmetals.com |
Makin Metal Powders | Copper, Zinc, Iron, Nickel | $15 – $180 | www.makinmetals.com |
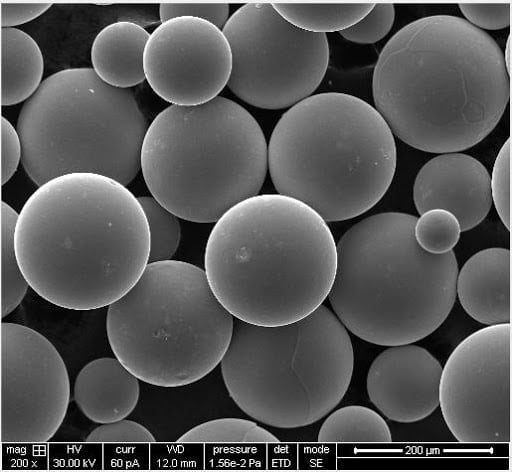
FAQ
Question | Answer |
---|---|
What are metallic powders? | Finely divided particles of metals used in various industrial applications. |
How are metallic powders produced? | Common methods include atomization, reduction, electrolysis, and mechanical alloying. |
What are the main uses of metallic powders? | Additive manufacturing, powder metallurgy, thermal spraying, metal injection molding, and more. |
What are the benefits of using metallic powders? | They allow for high precision, material efficiency, and the creation of complex shapes. |
Are there any disadvantages to using metallic powders? | They can be costly, pose handling hazards, and require consistent quality control. |
How should metallic powders be stored? | In a dry, cool place, away from any sources of ignition, and in tightly sealed containers. |
Can metallic powders be recycled? | Yes, many metallic powders can be recycled, depending on the metal and the application. |
What safety precautions are necessary when handling metallic powders? | Use protective gear, ensure proper ventilation, and follow all safety guidelines to prevent inhalation and fire hazards. |
What industries benefit most from metallic powders? | Aerospace, automotive, electronics, medical, and industrial manufacturing. |
How does the particle size of metallic powders affect their use? | Smaller particles offer higher surface area and reactivity, while larger particles may provide better flow characteristics. |
Conclusion
Metallic powders are a critical component in modern manufacturing, offering unique properties and capabilities that traditional bulk metals can’t match. From their use in innovative additive manufacturing processes to their essential role in everyday products, metallic powders continue to push the boundaries of what’s possible in material science. Understanding their types, properties, and applications can open up a world of possibilities, whether you’re looking to improve product performance, explore new manufacturing techniques, or simply expand your knowledge.
About 3DP mETAL
Product Category
CONTACT US
Any questions? Send us a message now! After receiving your message, we will process your request with a whole team.