Imagine a world where intricate, near-net-shape metal components can be mass-produced with high precision and intricate details. This isn’t science fiction; it’s the reality of Metal Injection Molding (MIM), a revolutionary manufacturing process that relies on a secret weapon: MIM metal powder.
But what exactly is MIM metal powder, and how does it transform tiny particles into complex metal parts? Buckle up, because we’re diving deep into the fascinating world of MIM powders, exploring their types, properties, applications, and the intricate dance they perform to create the metal components that power our everyday lives.
the Composition and Properties of MIM Metal Powder
MIM metal powders are like microscopic building blocks, meticulously crafted to meet the specific demands of the desired final product. Here’s a breakdown of their key characteristics:
Property | Description |
---|---|
Composition | MIM powders primarily consist of metal particles, often alloyed with other elements for enhanced properties. Common base metals include steel (stainless steel, tool steel), nickel, copper, and titanium. |
Particle Size and Distribution | The size and distribution of the metal particles play a crucial role. Typically, MIM powders range from 5 to 30 microns in diameter, with a narrow size distribution ensuring uniform packing and minimizing defects in the final part. Imagine a playground filled with children; for smooth playtime, you’d want them all to be roughly the same size. It’s the same principle with MIM powders. |
Morphology | The shape of the metal particles also matters. Spherical particles are preferred for optimal flow and packing density during the molding process. Think of ball bearings; they roll smoothly and fill spaces efficiently, just like spherical MIM powders. |
Flowability | Good flowability is essential for even distribution within the mold cavity. Powders with excellent flow characteristics prevent segregation (uneven distribution) and ensure consistent part quality. |
Sinterability | MIM powders need to readily bond together during the sintering stage, where heat transforms the loose powder into a solid metal part. Imagine tiny hands reaching out and holding onto each other; good sinterability ensures strong inter-particle bonding. |
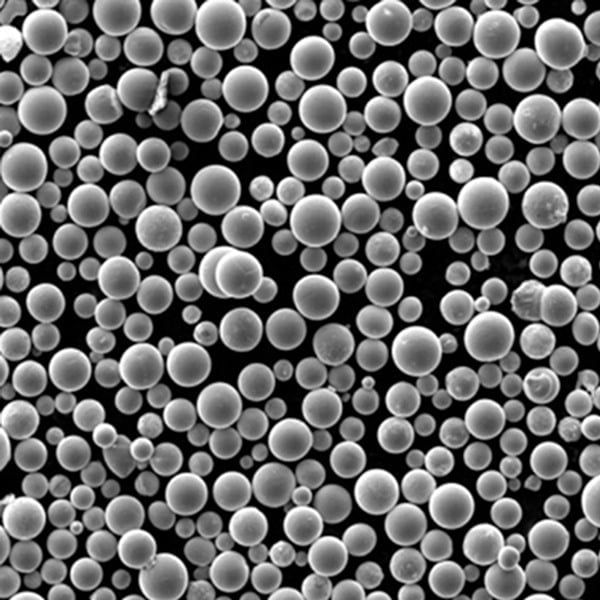
Popular MIM Metal Powder Models
- 316L Stainless Steel: A versatile, corrosion-resistant workhorse, particularly popular for medical devices, automotive components, and electronic parts.
- 17-4PH Stainless Steel: Offering high strength and good hardness, this model shines in applications demanding wear resistance, like gears and fasteners.
- Carbon Steel: Cost-effective and readily available, carbon steel MIM powders find their way into structural components, gears, and tools.
- Nickel Alloy 201: Known for its excellent corrosion resistance and high-temperature performance, this powder is ideal for chemical processing equipment and aerospace components.
- Copper: Offering high thermal and electrical conductivity, copper MIM powders are perfect for heat sinks, electrical connectors, and electronic packaging.
- Titanium Grade 2: This lightweight and biocompatible powder is a star player in the medical device industry, particularly for implants and prosthetics.
- Inconel 625: Renowned for its exceptional high-temperature strength and corrosion resistance, Inconel 625 MIM powders are used in demanding applications like jet engine components and chemical processing equipment.
- Kovar: With a thermal expansion coefficient that closely matches glass, Kovar MIM powders are ideal for creating glass-to-metal seals in electronic devices.
- Tungsten Carbide: Incredibly hard and wear-resistant, tungsten carbide MIM powders are used for cutting tools, wear parts, and molds.
These are just a few examples, and the variety of MIM metal powders available continues to expand, catering to an ever-growing range of applications.
Additional Considerations: Besides the base metal composition, MIM powders can be infused with various additives to enhance specific properties. Lubricants improve flow during molding, while binders hold the particles together before sintering. Specialty additives can also be introduced to achieve desired magnetic or electrical properties.
Applications of MIM Metal Powder
The true magic of MIM metal powder lies in its ability to breathe life into intricate and near-net-shape metal components. Here’s a glimpse into the diverse applications of these microscopic marvels:
Industry | Applications |
---|---|
Medical Devices | Surgical instruments, implants, and prosthetics benefit from the biocompatible nature of certain MIM powders. |
Automotive | Gears, fasteners, and intricate engine components can be mass-produced with high precision using MIM. |
Electronics | Connectors, heat sinks, and miniaturized electronic components leverage the excellent electrical and thermal properties of some MIM powders. |
Consumer Goods | From intricate watch parts and camera components to complex locks and firearm components, MIM allows for precise and cost-effective manufacturing. |
Aerospace & Defense | High-strength and lightweight MIM parts find their way into aircraft components, weapon systems, and demanding aerospace applications. |
Firearms | MIM powders are used to create intricate firearm components like triggers, safeties, and internal mechanisms. |
Telecommunications | Miniaturized connectors and RF components for mobile devices and telecommunication infrastructure often utilize MIM technology. |
the Hidden Gems of MIM Applications
MIM’s reach extends far beyond these traditional applications. Here are some fascinating, lesser-known uses of MIM metal powder:
- Microfluidics: The ability to create intricate channels and micro-features makes MIM powders ideal for microfluidic devices used in medical diagnostics and lab-on-a-chip technologies.
- Jewelry: MIM can create intricate and detailed jewelry pieces with sharp features and intricate designs, offering a cost-effective alternative to traditional casting methods.
- Sporting Goods: MIM finds its way into components like bicycle shifters and lightweight golf club heads, where strength, weight reduction, and intricate details are crucial.
The possibilities with MIM metal powders are truly endless, and as technology advances, we can expect even more innovative applications to emerge.
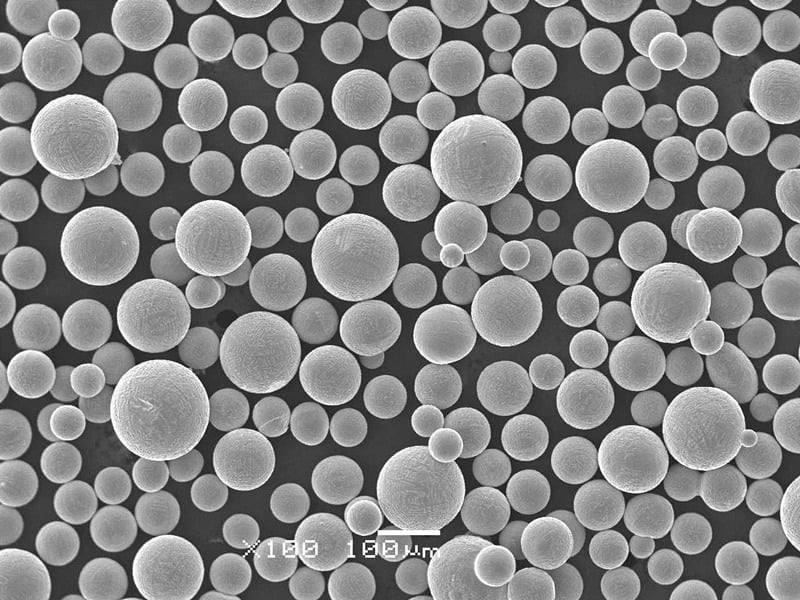
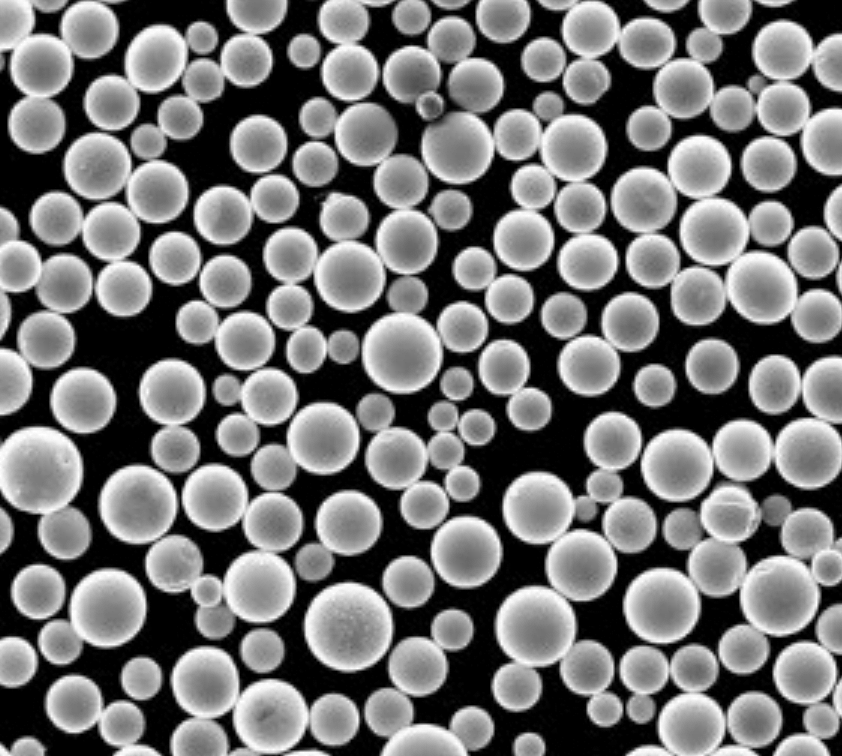
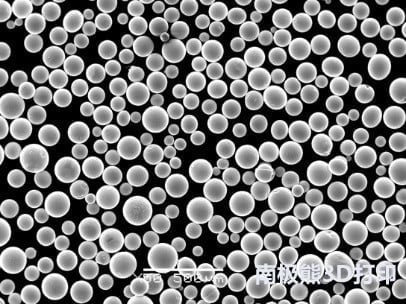
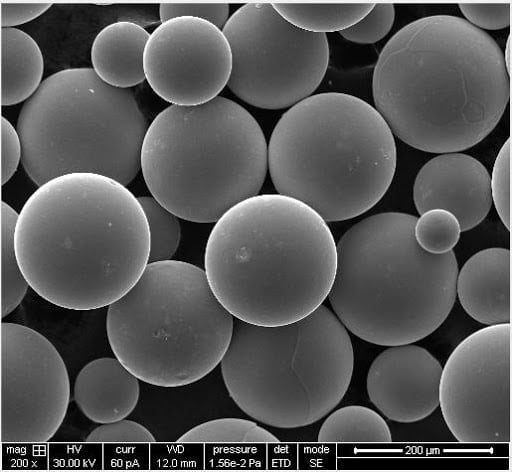
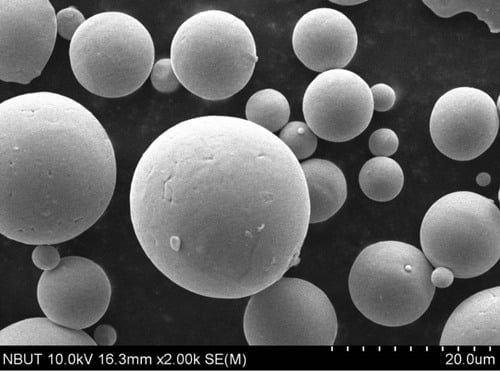
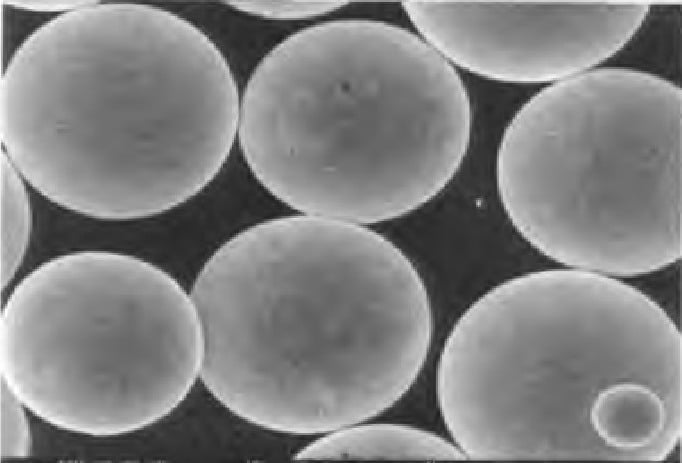
Advantages and Disadvantages of MIM Metal Powder
MIM metal powder offers a compelling proposition for manufacturers, but like any technology, it has its own set of advantages and limitations. Let’s delve into both sides of the coin:
Advantages of MIM Metal Powder:
- High Precision and Intricate Details: MIM allows for the creation of near-net-shape parts with intricate details and tight tolerances, surpassing the capabilities of traditional machining methods. Think of crafting a snowflake out of metal; with MIM, even the delicate, intricate branches can be formed with precision.
- Mass Production: MIM excels at producing large quantities of identical parts with consistent quality, making it ideal for high-volume production runs. Imagine baking hundreds of identical cookies simultaneously; that’s the power of MIM for metal components.
- Material Versatility: A wide variety of MIM metal powders are available, catering to a broad spectrum of material properties. This allows manufacturers to choose the perfect powder for the specific needs of the application.
- Cost-Effectiveness: For complex parts with high volumes, MIM can be a cost-effective alternative to traditional machining or casting methods. While the initial tooling costs might be higher, the savings in material waste and production time often outweigh them. Imagine building a complex mold just once to create thousands of identical parts; that’s the cost-saving advantage of MIM.
- Design Freedom: MIM allows for the creation of intricate geometries that wouldn’t be possible with other manufacturing methods. This opens doors for innovative and functional designs. Imagine designing a gear with internal channels for lubrication; MIM makes such designs a reality.
Disadvantages of MIM Metal Powder:
- Limited Part Size: While MIM can create intricate parts, there are limitations on the overall size of the component. This is due to the challenges of ensuring even powder distribution and proper sintering throughout a very large part.
- Material Porosity: MIM parts can have a slight level of porosity (tiny air pockets) due to the nature of the powder-based process. For applications requiring complete impermeability, MIM might not be the ideal choice. Imagine building a house of bricks; there will always be some air gaps between the bricks, similar to the porosity in MIM parts.
- Upfront Tooling Costs: Developing the molds for MIM can be expensive, especially for complex parts. This upfront cost can be a barrier for low-volume production runs. Imagine the cost of building a custom mold for baking a single, intricate cookie; that’s the initial investment consideration for MIM tooling.
- Post-Processing Requirements: MIM parts might require some post-processing steps like deburring (removing excess material) or heat treatment to achieve the desired final properties. Imagine baking cookies and then needing to trim off any uneven edges before packaging them.
Making the Right Choice:
The decision to use MIM metal powder depends on the specific application and its requirements. For high-volume production of complex parts where intricate details and tight tolerances are crucial, MIM can be a game-changer. However, for very large parts, applications requiring absolute impermeability, or low-volume production runs, other manufacturing methods might be better suited.
Specifications, Sizes, Grades, and Standards of MIM Metal Powder
Choosing the right MIM metal powder requires a deeper dive into its technical specifications. Here’s a breakdown of the key factors to consider:
Particle Size and Distribution:
- Typical Range: As mentioned earlier, MIM powders typically range from 5 to 30 microns in diameter. However, the specific size and distribution can vary depending on the desired final part properties.
- Impact on Properties: Finer powders (smaller particle size) can create parts with smoother surfaces and potentially higher strength. However, they can also be more challenging to flow and pack efficiently during molding, leading to potential defects. Conversely, coarser powders offer better flowability but might result in a slightly rougher surface finish and potentially lower strength.
Apparent Density:
- Definition: This refers to the weight of powder per unit volume, taking into account the spaces between particles.
- Importance: Apparent density influences the amount of powder needed to fill the mold cavity and ultimately affects the final part’s density and properties. Higher apparent density generally translates to less shrinkage during sintering and a denser final part.
Flowability:
- Measurement: Measured in seconds/50g, flowability indicates how easily the powder flows under gravity.
- Significance: Good flowability ensures even distribution within the mold, minimizing segregation and leading to consistent part quality.
Sinterability:
- Description: This refers to the powder’s ability to bond together during the sintering stage.
- Testing: Sinterability is often evaluated through tests that measure the strength of a sintered compact made from the powder. Good sinterability is crucial for achieving strong and functional final parts.
Chemical Composition:
- Beyond Base Metal: The specific composition of the MIM powder plays a vital role in the final part’s properties. Alloying elements and additional additives can be incorporated to achieve desired characteristics like strength, corrosion resistance, or electrical conductivity.
Standards and Certifications:
- Importance: Several industry standards and certifications govern the quality and performance of MIM powders. These standards ensure consistency and reliability for manufacturers. Some common standards include MPIF (Metal Powder Industries Federation) standards and ASTM International specifications.
Suppliers and Pricing
A multitude of global suppliers offer MIM metal powders in various compositions, sizes, and grades. Pricing can vary depending on the specific powder material, its complexity, and the volume purchased. Here’s a table (without specific pricing details due to constant fluctuations) to provide a general understanding:
MIM Metal Powder Type | Typical Applications | Considerations |
---|---|---|
Stainless Steel (316L, 17-4PH) | Medical devices, automotive components, electronic parts | Versatile, good corrosion resistance, wide range of grades available |
Nickel Alloy 201 | Chemical processing equipment, aerospace components | Excellent corrosion resistance, high-temperature performance |
Copper | Heat sinks, electrical connectors, electronic packaging | High thermal and electrical conductivity |
Titanium Grade 2 | Medical implants, prosthetics | Lightweight, biocompatible |
Tungsten Carbide | Cutting tools, wear parts, molds | Extremely hard and wear-resistant |
Choosing the Right Powder:
Selecting the optimal MIM metal powder requires careful consideration of the desired final part properties, application requirements, and production economics. Consulting with a reputable MIM powder supplier and leveraging their expertise can be invaluable in making the right choice.
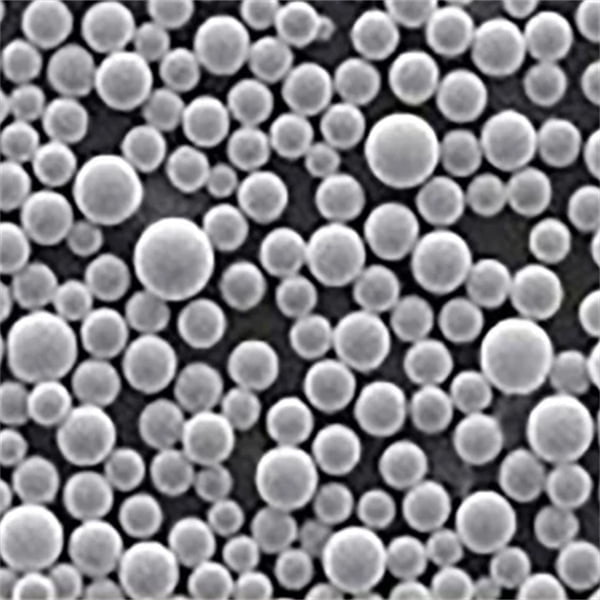
MIM Metal Powder
The future of MIM metal powder is brimming with exciting possibilities. Here are some trends to watch:
- Development of New Powder Materials: The constant innovation in material science is leading to the development of novel MIM powders with enhanced properties like even higher strength, improved conductivity, or biocompatibility tailored for specific applications.
- Advancements in Additive Manufacturing: The convergence of MIM technology with additive manufacturing techniques like 3D printing holds immense potential for creating even more complex and intricate metal parts with unprecedented design freedom.
- Focus on Sustainability: As environmental concerns grow, the focus will shift towards developing sustainable MIM powders with minimal environmental impact. This could involve exploring recycled materials or utilizing greener manufacturing processes.
MIM metal powder is a transformative technology that has revolutionized the way complex metal parts are manufactured. With its unique ability to create intricate shapes, achieve high precision, and offer cost-effective mass production, MIM is poised to play an even more significant role in shaping the future of metal components across diverse industries.
FAQ
Q: What are the advantages of using MIM metal powder?
A: MIM offers several advantages, including high precision for intricate details, mass production capabilities, material versatility, cost-effectiveness for complex parts, and design freedom for innovative geometries.
Q: What are the limitations of MIM metal powder?
A: MIM has limitations including restrictions on part size due to challenges with powder distribution and sintering, potential for slight porosity in the final part, high upfront tooling costs, and the need for post-processing steps like deburring or heat treatment.
Q: Is MIM metal powder environmentally friendly?
A: The environmental impact of MIM depends on various factors. The use of virgin materials and energy consumption during the process can raise concerns. However, advancements are being made towards:
- Recycled Powders: Exploring the use of recycled metal powders in MIM to minimize environmental footprint.
- Greener Processes: Researching alternative methods for powder production and sintering that reduce energy consumption and utilize less harmful chemicals.
Q: How does MIM metal powder compare to other metal manufacturing methods?
A: Here’s a comparison of MIM with some common metal manufacturing methods:
Feature | MIM | Machining | Casting |
---|---|---|---|
Complexity | High | Limited | Moderate |
Precision | Very high | High | Moderate |
Production Volume | High (mass production) | Low to moderate | High |
Cost (per part) | Cost-effective for complex parts | High for complex parts | Cost-effective for simple parts |
Material Waste | Low | High | Moderate |
Q: What are some emerging applications of MIM metal powder?
A: Beyond traditional applications, MIM is finding its way into exciting new areas like:
- Microfluidics: Creating intricate channels for medical diagnostics and lab-on-a-chip technologies.
- Jewelry: Manufacturing intricate and detailed jewelry pieces with sharp features and intricate designs.
- Sporting Goods: Developing lightweight components like bicycle shifters and golf club heads with intricate details.
Q: Where can I find more information about MIM metal powder?
A reputable source for information on MIM is the Metal Powder Industries Federation (MPIF) website: https://www.mpif.org/. Additionally, many MIM powder suppliers offer detailed information and resources on their websites.
About 3DP mETAL
Product Category
CONTACT US
Any questions? Send us a message now! After receiving your message, we will process your request with a whole team.