Welcome to the fascinating world of MIM metal powder! If you’re diving into this topic, chances are you’re either an enthusiast, a professional, or someone curious about the intricacies of metal injection molding (MIM). Well, you’re in the right place. In this comprehensive guide, we’ll unravel the complexities of MIM metal powder, discuss its various models, delve into its applications, and weigh its pros and cons. So, grab a cup of coffee, sit back, and let’s embark on this informative journey.
Overview of MIM Metal Powder
Metal Injection Molding (MIM) is a manufacturing process that combines the versatility of plastic injection molding with the strength and integrity of powdered metallurgy. This process is perfect for producing complex, high-volume metal parts with intricate shapes and tight tolerances. The secret sauce here is the MIM metal powder—a finely powdered form of metal that serves as the raw material in this process.
MIM metal powder is typically less than 20 micrometers in diameter and comes in various compositions, tailored for specific applications. The powder’s fine nature allows it to be molded into precise shapes, which are then sintered to produce solid metal components.
Key Details of MIM Metal Powder
Aspect | Details |
---|---|
Definition | Fine metal powder used in Metal Injection Molding |
Particle Size | Typically < 20 micrometers |
Applications | Automotive, aerospace, medical devices, electronics |
Advantages | High precision, complex shapes, cost-effective |
Disadvantages | Limited to small parts, initial setup cost |
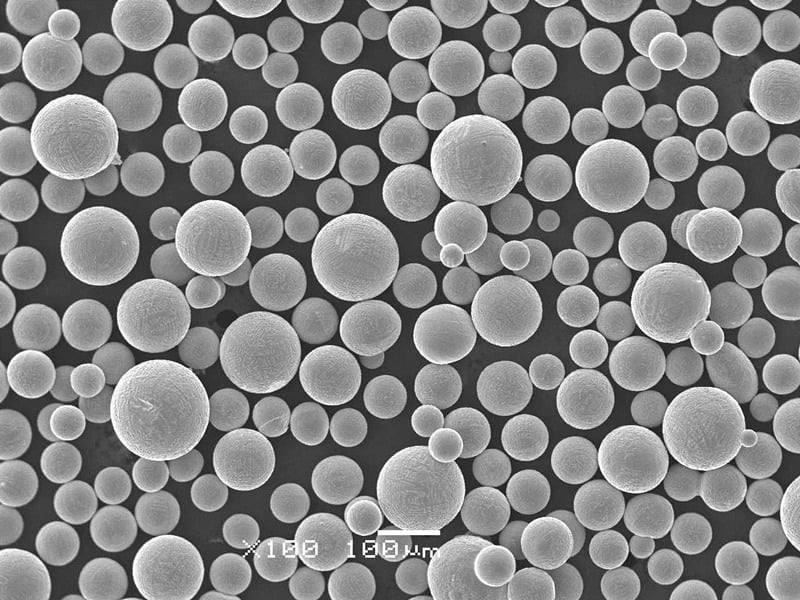
Types of MIM Metal Powder
MIM metal powders come in various types, each suited for different applications and performance requirements. Let’s explore some specific models:
1. Stainless Steel Powder (316L)
316L stainless steel powder is a popular choice in MIM due to its excellent corrosion resistance and mechanical properties. It’s widely used in medical devices, watches, and marine applications.
Composition:
- Chromium: 16-18%
- Nickel: 10-14%
- Molybdenum: 2-3%
- Carbon: ≤ 0.03%
Properties:
- High corrosion resistance
- Good strength and ductility
- Non-magnetic
2. Carbonyl Iron Powder
Carbonyl iron powder is known for its high purity and uniform particle size, making it ideal for high-density and high-strength parts. Common applications include automotive components and electronics.
Composition:
- Iron: > 97%
- Carbon: < 0.02%
- Oxygen: < 0.5%
Properties:
- High density
- Excellent magnetic properties
- High purity
3. Tool Steel Powder (M2)
M2 tool steel powder offers exceptional hardness and wear resistance, making it suitable for cutting tools and high-stress applications.
Composition:
- Tungsten: 5-6%
- Molybdenum: 5%
- Chromium: 4%
- Vanadium: 2%
- Carbon: 0.85-1.05%
Properties:
- High hardness
- Excellent wear resistance
- Good toughness
4. Titanium Alloy Powder (Ti-6Al-4V)
Ti-6Al-4V is a widely used titanium alloy powder known for its high strength-to-weight ratio and excellent biocompatibility, making it ideal for aerospace and medical implants.
Composition:
- Titanium: 90%
- Aluminum: 6%
- Vanadium: 4%
Properties:
- High strength-to-weight ratio
- Excellent corrosion resistance
- Biocompatible
5. Nickel Alloy Powder (IN718)
IN718 is a nickel-chromium alloy powder renowned for its high strength and oxidation resistance at high temperatures. It’s commonly used in aerospace and power generation.
Composition:
- Nickel: 50-55%
- Chromium: 17-21%
- Iron: 17%
- Molybdenum: 2.8-3.3%
Properties:
- High temperature resistance
- Good oxidation resistance
- High strength
6. Cobalt-Chrome Alloy Powder (CoCr)
Cobalt-chrome alloy powder is known for its exceptional wear resistance and biocompatibility, often used in dental and orthopedic implants.
Composition:
- Cobalt: 55-65%
- Chromium: 26-30%
- Molybdenum: 5-7%
Properties:
- High wear resistance
- Excellent corrosion resistance
- Biocompatible
7. Aluminum Alloy Powder (AlSi10Mg)
AlSi10Mg is an aluminum alloy powder with good thermal properties and strength, commonly used in lightweight structural components and automotive parts.
Composition:
- Aluminum: 85-90%
- Silicon: 9-11%
- Magnesium: 0.2-0.5%
Properties:
- Lightweight
- Good thermal conductivity
- High strength
8. Copper Powder
Copper powder is valued for its excellent electrical and thermal conductivity, making it suitable for electrical components and heat exchangers.
Composition:
- Copper: > 99%
- Oxygen: < 0.5%
Properties:
- High electrical conductivity
- Good thermal conductivity
- High ductility
9. Bronze Powder (CuSn10)
CuSn10 bronze powder combines good mechanical properties with corrosion resistance, often used in bearings and bushings.
Composition:
- Copper: 88-92%
- Tin: 8-12%
Properties:
- Good wear resistance
- High strength
- Excellent corrosion resistance
10. Inconel Powder (IN625)
IN625 is a nickel-chromium alloy powder with outstanding fatigue and thermal-fatigue properties, commonly used in aerospace and chemical processing.
Composition:
- Nickel: 58%
- Chromium: 20-23%
- Molybdenum: 8-10%
- Niobium: 3.15-4.15%
Properties:
- High fatigue resistance
- Excellent oxidation resistance
- High strength
Applications of MIM Metal Powder
MIM metal powder finds its way into a multitude of industries, thanks to its versatility and the unique advantages it brings to manufacturing. Here’s a look at some of the key applications:
Industry | Application | Benefits |
---|---|---|
Automotive | Fuel injectors, turbocharger components, gears | High precision, complex shapes, durability |
Aerospace | Engine components, fasteners, brackets | Lightweight, high strength, heat resistance |
Medical Devices | Surgical instruments, implants, orthodontic parts | Biocompatibility, intricate designs, corrosion resistance |
Electronics | Connectors, sensor housings, EMI shielding | Miniaturization, electrical conductivity |
Consumer Goods | Watch cases, eyeglass frames, writing instruments | Aesthetic quality, durability |
Industrial | Cutting tools, machinery parts, fittings | Wear resistance, mechanical strength |
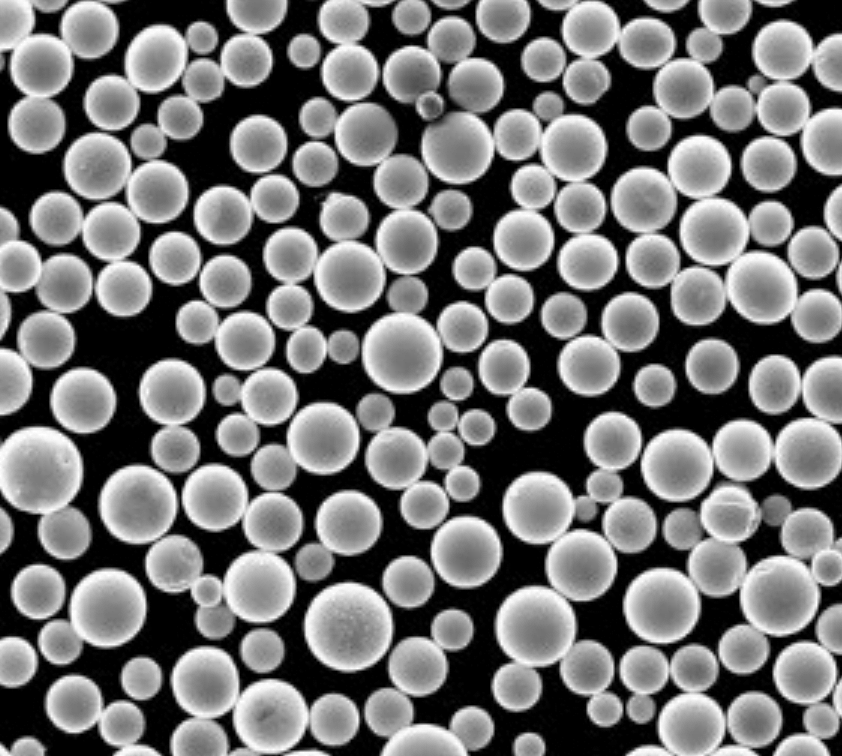
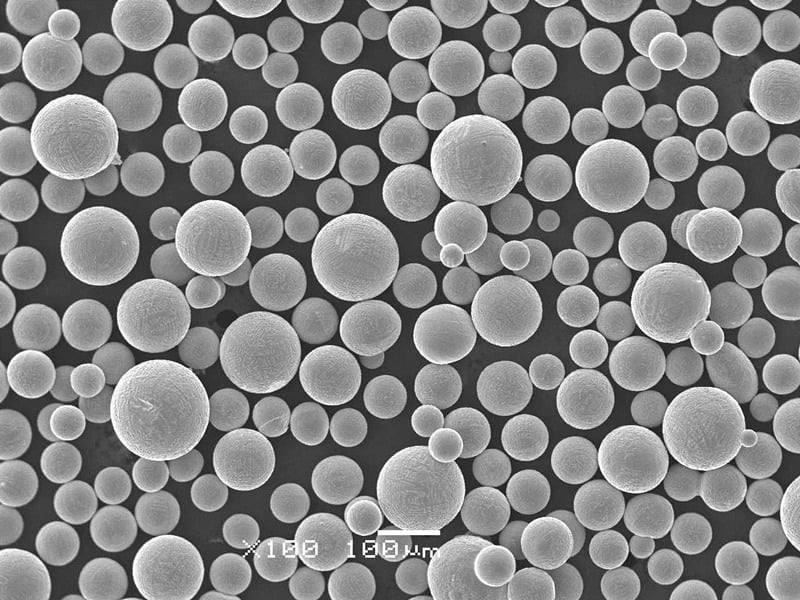
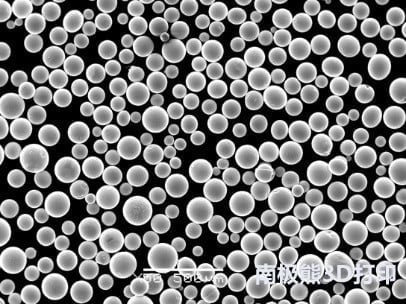
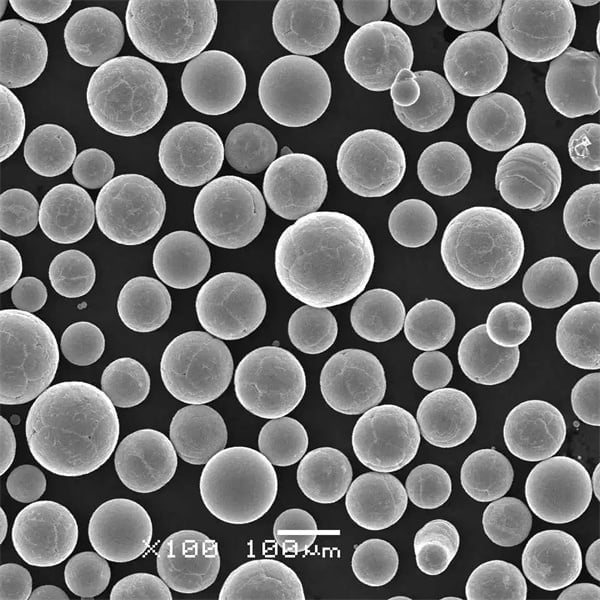
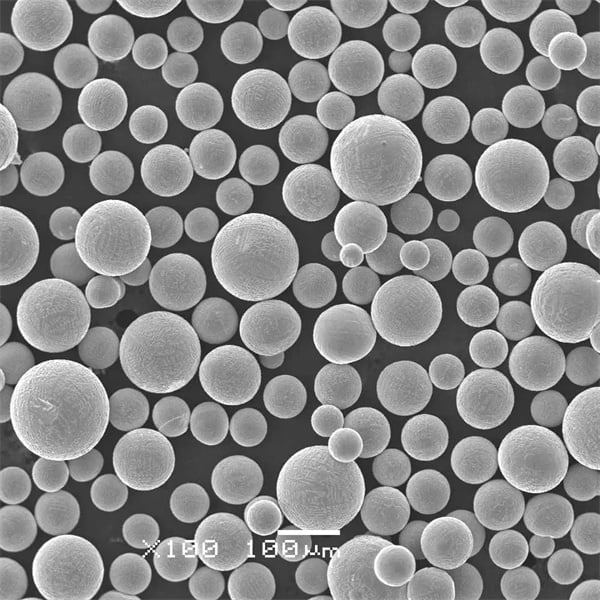
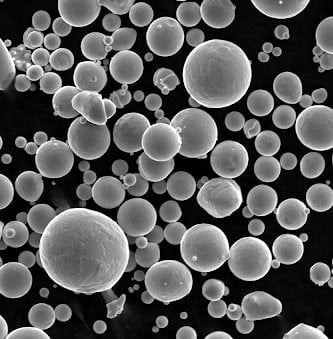
Specifications, Sizes, Grades, and Standards
Understanding the specifications, sizes, grades, and standards of MIM metal powder is crucial for selecting the right material for your application. Here’s a detailed look:
Material | Size Range (µm) | Grade | Standard |
---|---|---|---|
316L Stainless Steel | 5-15 | AISI 316L | ASTM F138, ISO 5832-1 |
Carbonyl Iron | 2-10 | Fe | ASTM B426 |
M2 Tool Steel | 10-20 | M2 | ASTM A600 |
Ti-6Al-4V Titanium | 15-45 | Grade 5 | ASTM B348, AMS 4911 |
IN718 Nickel Alloy | 15-53 | IN718 | ASTM B637, AMS 5662 |
CoCr Alloy | 10-25 | F75 | ASTM F75, ISO 5832-4 |
AlSi10Mg Aluminum | 20-63 | AlSi10Mg | ISO 3522 |
Copper | 10-50 | C11000 | ASTM B170, ASTM B152 |
Bronze (CuSn10) | 10-45 | CuSn10 | ASTM B505 |
IN625 Nickel Alloy | 15-45 | IN625 | ASTM B443, AMS 5666 |
Suppliers and Pricing Details
When sourcing MIM metal powder, it’s important to consider reliable suppliers and compare pricing to get the best deal. Here’s a snapshot:
Supplier | Location | Material | Pricing (per kg) |
---|---|---|---|
Höganäs AB | Sweden | 316L, Ti-6Al-4V, Carbonyl Iron | $80 – $200 |
Sandvik Materials Technology | Sweden | M2 Tool Steel, IN718 | $100 – $250 |
GKN Powder Metallurgy | Global | CoCr, IN625, AlSi10Mg | $90 – $220 |
Advanced Technology & Materials Co., Ltd. | China | Copper, Bronze (CuSn10) | $50 – $150 |
Carpenter Technology Corporation | USA | 316L, Ti-6Al-4V, IN625 | $120 – $300 |
Pros and Cons of MIM Metal Powder
Like any technology, MIM metal powder has its advantages and limitations. Let’s break them down:
Aspect | Advantages | Limitations |
---|---|---|
Cost | Cost-effective for high-volume production | High initial setup cost |
Precision | Can produce complex shapes with tight tolerances | Limited to small parts |
Material Properties | Maintains excellent material properties | Potential for slight porosity |
Versatility | Applicable to a wide range of metals and alloys | Powder handling and storage requirements |
Production Speed | Faster than traditional machining methods | Longer cycle time for large parts |
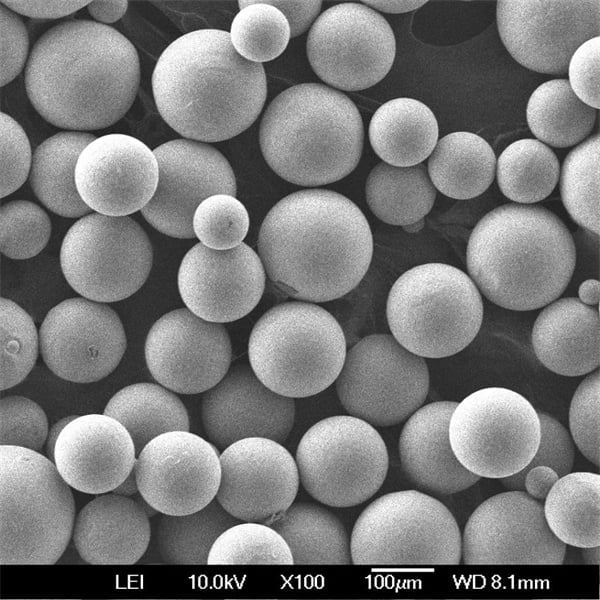
FAQs
What is MIM Metal Powder?
MIM metal powder is a finely powdered form of metal used in Metal Injection Molding. It’s used to create complex, high-precision metal parts by injecting the powder mixed with a binder into a mold, which is then sintered to form solid metal components.
What are the main benefits of using MIM metal powder?
The main benefits include high precision, the ability to produce complex shapes, cost-effectiveness for high-volume production, and maintaining excellent material properties.
What industries commonly use MIM metal powder?
MIM metal powder is commonly used in the automotive, aerospace, medical devices, electronics, consumer goods, and industrial sectors.
How does the particle size of MIM metal powder affect its performance?
Smaller particle sizes typically result in better flowability and packing density, leading to higher precision and strength in the final product. However, very fine powders can be more challenging to handle and may pose health risks if not managed properly.
What are some common types of MIM metal powders?
Common types include 316L stainless steel, carbonyl iron, M2 tool steel, Ti-6Al-4V titanium alloy, IN718 nickel alloy, CoCr alloy, AlSi10Mg aluminum alloy, copper, bronze (CuSn10), and IN625 nickel alloy.
How do I choose the right MIM metal powder for my application?
Choosing the right MIM metal powder depends on your specific application requirements, including mechanical properties, corrosion resistance, thermal properties, and biocompatibility. Consulting with a supplier or materials engineer can help in making an informed decision.
What are the challenges associated with MIM metal powder?
Challenges include managing the powder handling and storage, ensuring uniform particle size distribution, controlling the sintering process to avoid porosity, and the high initial setup cost.
Can MIM metal powder be used for large parts?
MIM metal powder is typically used for small to medium-sized parts due to the limitations in mold size and the complexity of the sintering process for larger components.
What is the cost range for MIM metal powders?
The cost of MIM metal powders varies widely depending on the material and supplier, typically ranging from $50 to $300 per kilogram.
Are there any health risks associated with handling MIM metal powder?
Yes, fine metal powders can pose inhalation risks and should be handled with appropriate safety measures, including protective equipment and adequate ventilation.
About 3DP mETAL
Product Category
CONTACT US
Any questions? Send us a message now! After receiving your message, we will process your request with a whole team.