When diving into the world of advanced metal powders, one aspect that often raises eyebrows is the concept of minor gas-trapped pores. These microscopic voids within metal powders can significantly impact the performance and application of the final product. But what exactly are minor gas-trapped pores powders, and how do they affect various industries? Let’s explore this fascinating subject, unraveling the complexities and nuances of these powders, their properties, and their applications.
Overview of Minor Gas-Trapped Pores Powders
Minor gas-trapped pores powders are specialized metal powders that contain small, gas-filled voids within their structure. These pores are typically formed during the production process, where gases like hydrogen, nitrogen, or oxygen become trapped within the molten metal before it solidifies. The presence of these pores can influence the mechanical properties, density, and overall performance of the powder when used in manufacturing processes such as 3D printing, sintering, and powder metallurgy.
Key Details of Minor Gas-Trapped Pores Powders
Feature | Description |
---|---|
Primary Components | Metal powders (e.g., stainless steel, titanium, aluminum) with gas-filled voids |
Typical Gas Inclusions | Hydrogen, Nitrogen, Oxygen |
Primary Manufacturing Process | Atomization, sintering, and 3D printing |
Impact on Properties | Affects density, mechanical strength, thermal conductivity, and electrical resistance |
Common Applications | Aerospace, automotive, medical devices, additive manufacturing, and energy industries |
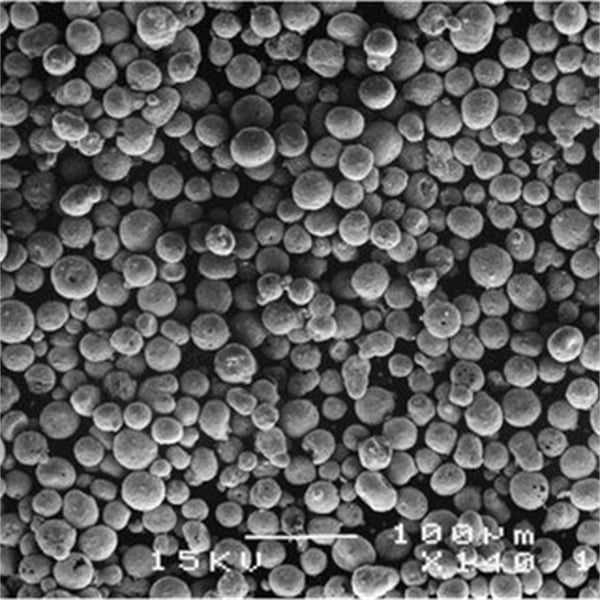
Composition of Minor Gas-Trapped Pores Powders
The composition of these powders plays a crucial role in their final properties and applications. Let’s take a closer look at some of the specific metal powder models, their compositions, and what makes them unique.
Popular Minor Gas-Trapped Pores Powder Models
- 316L Stainless Steel Powder
- Composition: Iron (Fe) > 60%, Chromium (Cr) 16-18%, Nickel (Ni) 10-14%, Molybdenum (Mo) 2-3%
- Description: Known for its corrosion resistance, this powder is commonly used in harsh environments like marine and chemical industries. The minor gas-trapped pores reduce density slightly but offer improved malleability.
- Ti-6Al-4V (Titanium Alloy) Powder
- Composition: Titanium (Ti) ~90%, Aluminum (Al) 6%, Vanadium (V) 4%
- Description: A high-strength, lightweight alloy with excellent biocompatibility, making it ideal for medical implants. Gas-trapped pores can enhance its fatigue resistance.
- Inconel 718 Powder
- Composition: Nickel (Ni) ~50-55%, Chromium (Cr) 17-21%, Iron (Fe) 18-22%, Niobium (Nb) 4.75-5.5%
- Description: This superalloy is used in aerospace for its high temperature and corrosion resistance. Minor pores improve its thermal insulation properties.
- AlSi10Mg Aluminum Powder
- Composition: Aluminum (Al) ~85-90%, Silicon (Si) 9-11%, Magnesium (Mg) 0.2-0.5%
- Description: Lightweight and strong, this powder is ideal for automotive parts. Gas-trapped pores can reduce its weight further, making it more efficient in energy applications.
- Hastelloy X Powder
- Composition: Nickel (Ni) 47-50%, Chromium (Cr) 20-23%, Iron (Fe) 18-20%, Molybdenum (Mo) 8-10%
- Description: Known for its resistance to oxidation and high temperatures, Hastelloy X is used in gas turbines. Gas-trapped pores enhance its thermal shock resistance.
- 316Ti Stainless Steel Powder
- Composition: Iron (Fe) > 60%, Chromium (Cr) 16-18%, Nickel (Ni) 10-14%, Titanium (Ti) 0.5-0.7%
- Description: This variant of 316L includes titanium for improved heat resistance. Gas-trapped pores provide better stress distribution during high-temperature applications.
- Cobalt-Chrome (CoCr) Powder
- Composition: Cobalt (Co) ~60-65%, Chromium (Cr) 25-30%, Molybdenum (Mo) 5-7%
- Description: Used primarily in medical implants, the minor pores in this powder help improve its fatigue life and biocompatibility.
- Tool Steel H13 Powder
- Composition: Iron (Fe) > 80%, Chromium (Cr) 4-5.5%, Molybdenum (Mo) 1.2-1.5%, Vanadium (V) 0.8-1.2%
- Description: Ideal for high-strength, wear-resistant tools. Gas-trapped pores can enhance toughness by absorbing impact energy.
- Copper (Cu) Powder
- Composition: Copper (Cu) > 99%
- Description: With excellent thermal and electrical conductivity, minor gas-trapped pores in copper powder can reduce its density, making it more efficient for heat exchangers.
- Nickel 200 Powder
- Composition: Nickel (Ni) > 99%
- Description: This high-purity nickel powder is used in electronics and aerospace for its excellent corrosion resistance. Gas-trapped pores can improve its electrical insulation properties.
Characteristics of Minor Gas-Trapped Pores Powders
Understanding the characteristics of minor gas-trapped pores powders is essential for selecting the right material for specific applications. These powders exhibit unique traits that can either be advantageous or detrimental, depending on the intended use.
Key Characteristics
- Density Reduction: The presence of gas-trapped pores typically leads to a lower overall density, which can be beneficial in applications requiring lightweight materials.
- Improved Malleability: Minor pores can make the material more malleable, allowing for easier shaping and forming processes.
- Thermal and Electrical Conductivity: Depending on the type of metal, gas-trapped pores can either enhance or reduce conductivity. For example, copper with minor pores may have reduced thermal conductivity, which can be beneficial in certain heat-resistant applications.
- Mechanical Strength: While the reduction in density can sometimes lead to a decrease in mechanical strength, the distribution of stress around the pores can improve the material’s toughness and fatigue resistance.
- Surface Finish: The presence of pores can affect the surface finish of components, particularly in additive manufacturing, where smooth surfaces are often desired.
Comparative Characteristics of Different Powder Models
Powder Model | Density | Thermal Conductivity | Electrical Conductivity | Mechanical Strength | Surface Finish |
---|---|---|---|---|---|
316L Stainless Steel | Moderate | Moderate | Moderate | High | Good |
Ti-6Al-4V | Low | Low | Low | Very High | Excellent |
Inconel 718 | High | Moderate | Low | Very High | Good |
AlSi10Mg Aluminum | Very Low | High | High | Moderate | Excellent |
Hastelloy X | High | Low | Low | Very High | Moderate |
316Ti Stainless Steel | Moderate | Moderate | Moderate | High | Good |
Cobalt-Chrome | Moderate | Low | Low | Very High | Excellent |
Tool Steel H13 | High | Low | Low | Very High | Moderate |
Copper (Cu) | Very High | Very High | Very High | Moderate | Excellent |
Nickel 200 | High | Moderate | High | Moderate | Good |
Applications of Minor Gas-Trapped Pores Powders
The applications of minor gas-trapped pores powders are diverse and span across several industries. Each application leverages the unique properties of these powders to achieve specific performance outcomes.
Key Applications Across Industries
Industry | Application | Powder Model | Benefits of Gas-Trapped Pores |
---|---|---|---|
Aerospace | Turbine Blades, Structural Components | Inconel 718, Hastelloy X | Improved thermal shock resistance, reduced weight |
Automotive | Engine Parts, Lightweight Structures | AlSi10Mg, 316L Stainless Steel | Reduced weight, improved fuel efficiency |
Medical Devices | Implants, Prosthetics | Ti-6Al-4V, Cobalt-Chrome | Enhanced biocompatibility, fatigue resistance |
Energy | Heat Exchangers, Power Generation Equipment | Copper, Nickel 200 | Improved thermal insulation, reduced weight |
Tooling | Molds, Cutting Tools | Tool Steel H13 | Enhanced toughness, better stress distribution |
Electronics | Conductive Components, Connectors | Copper, Nickel 200 | Improved electrical insulation, reduced density |
Additive Manufacturing | Complex Geometries, Prototypes | 316L Stainless Steel, AlSi10Mg | Improved malleability, better surface finish |
Marine | Corrosion-Resistant Structures | 316Ti Stainless Steel | Enhanced corrosion resistance, reduced weight |
Chemical Processing | High-Temperature Equipment | Hastelloy X, Inconel 718 | Better oxidation resistance, improved thermal insulation |
Defense | Armor, Structural Components | Ti-6Al-4V, Inconel 718 | Lightweight, improved impact resistance |
Specifications, Sizes, Grades, and Standard
Selecting the appropriate minor gas-trapped pores powder requires understanding the available specifications, sizes, grades, and standards. Here’s a detailed look at what’s on offer:
Specifications and Standards
Powder Model | Available Sizes (µm) | Common Grades | Standards Compliance |
---|---|---|---|
316L Stainless Steel | 15-45, 45-105 | AM (Additive Manufacturing), PM (Powder Metallurgy) | ASTM A276, ISO 5832-1 |
Ti-6Al-4V | 15-45, 45-105 | Grade 23, Grade 5 | ASTM F136, ISO 5832-3 |
Inconel 718 | 15-45, 45-105 | AMS 5662, AMS 5663 | ASTM B637, AMS 5662 |
AlSi10Mg Aluminum | 15-45, 45-90 | EN AC-43000 | ASTM B85, ISO 3522 |
Hastelloy X | 15-45, 45-105 | AMS 5536, AMS 5754 | ASTM B619, ASME SB619 |
316Ti Stainless Steel | 15-45, 45-105 | AM, PM | ASTM A276, ISO 5832-1 |
Cobalt-Chrome | 15-45, 45-105 | ASTM F75, F799 | ISO 5832-4, ASTM F1537 |
Tool Steel H13 | 15-45, 45-105 | AISI H13 | ASTM A681, ISO 4957 |
Copper (Cu) | 15-45, 45-105 | C10100, C10200 | ASTM B170, ISO 1338 |
Nickel 200 | 15-45, 45-105 | UNS N02200 | ASTM B160, ASME SB160 |
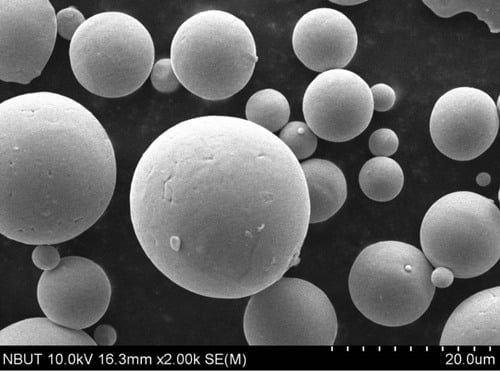
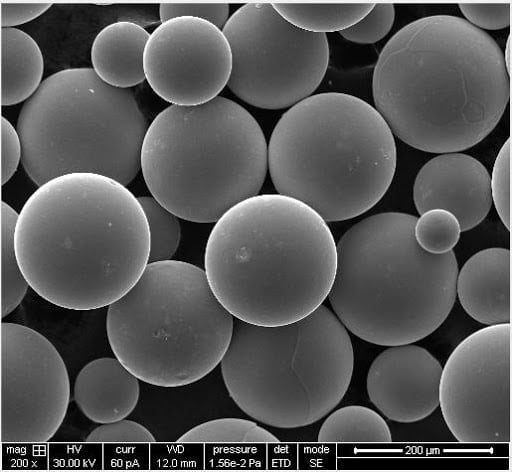
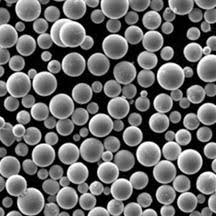
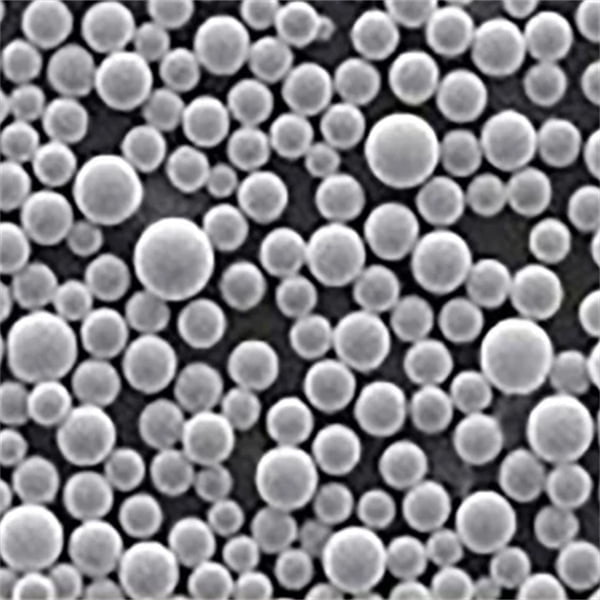
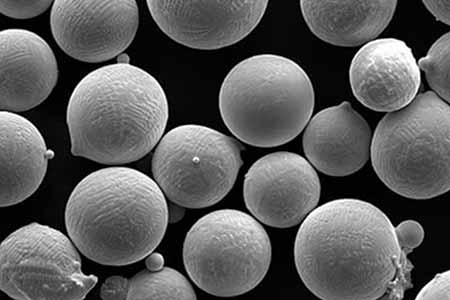
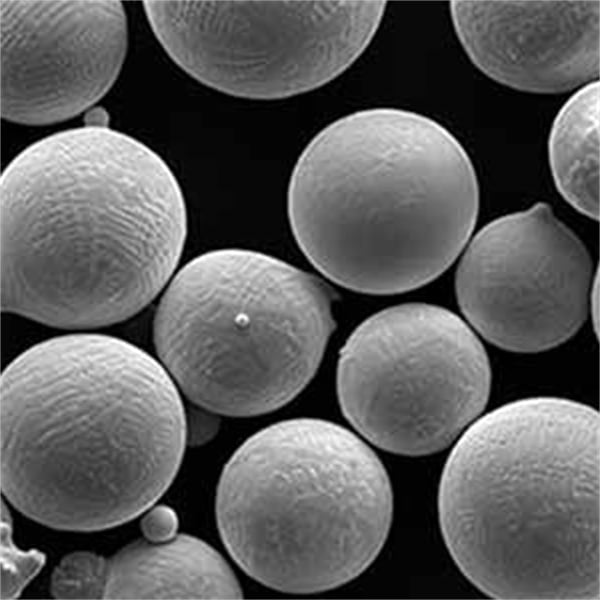
Suppliers and Pricing Details
To provide the best possible products for your needs, it’s essential to consider various suppliers and their offerings. Below is a comparative table of some leading suppliers of minor gas-trapped pores powders along with approximate pricing details.
Comparison of Suppliers and Pricing
Supplier | Powder Model | Price per kg (USD) | Lead Time | Minimum Order Quantity (kg) |
---|---|---|---|---|
AP&C (Advanced Powders & Coatings) | Ti-6Al-4V, Inconel 718 | $250-$400 | 2-4 weeks | 10 |
GKN Hoeganaes | 316L Stainless Steel, AlSi10Mg | $100-$200 | 3-6 weeks | 20 |
LPW Technology | Hastelloy X, Cobalt-Chrome | $300-$500 | 1-3 weeks | 5 |
Carpenter Technology | Tool Steel H13, Nickel 200 | $150-$300 | 4-8 weeks | 10 |
Sandvik Osprey | 316Ti Stainless Steel, Copper | $200-$350 | 3-5 weeks | 15 |
Advantages and Limitations of Minor Gas-Trapped Pores Powders
When choosing materials for any project, it’s important to weigh the pros and cons. Here’s how minor gas-trapped pores powders stack up:
Pros and Cons
Advantage | Details |
---|---|
Weight Reduction | Minor gas-trapped pores decrease overall density, making components lighter. |
Improved Malleability | Easier to shape and form during manufacturing processes. |
Enhanced Toughness | Pores can help distribute stress, reducing the likelihood of failure. |
Thermal Insulation | Gas-trapped pores can provide better thermal insulation for high-temperature applications. |
Cost-Effective for Lightweight Components | Lower material density can lead to cost savings in weight-sensitive industries. |
Limitation | Details |
---|---|
Potential Reduction in Strength | Lower density might compromise mechanical strength in some applications. |
Surface Finish Issues | Minor pores can affect the surface quality, requiring additional processing. |
Variable Conductivity | Pores may reduce thermal or electrical conductivity, depending on the material. |
Complex Manufacturing Requirements | Specialized processes are needed to manage and optimize pore characteristics. |
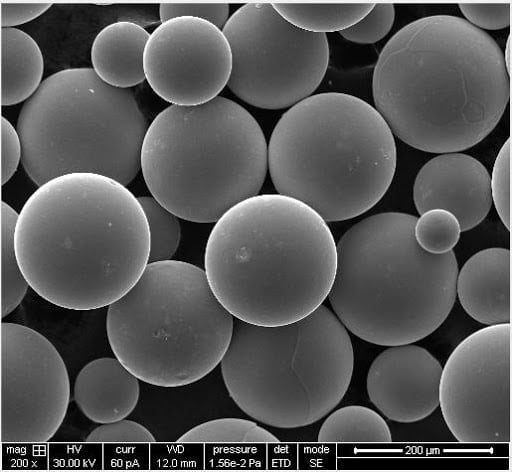
FAQ
To address common queries about minor gas-trapped pores powders, here’s an FAQ section that provides clear and concise answers.
Common Questions About Minor Gas-Trapped Pores Powders
Question | Answer |
---|---|
What are minor gas-trapped pores in metal powders? | These are small voids filled with gas that become trapped within the metal during the production process. |
How do gas-trapped pores affect the density of metal powders? | Gas-trapped pores reduce the overall density of the powder, making the final product lighter. |
Can the presence of pores improve material toughness? | Yes, in some cases, the pores can help distribute stress more evenly, enhancing the toughness of the material. |
What are the typical gases found in these pores? | Common gases include hydrogen, nitrogen, and oxygen. |
Are there any industries where gas-trapped pores are particularly beneficial? | Yes, industries like aerospace, automotive, and medical devices benefit from the reduced weight and improved toughness of these powders. |
Do these powders require special handling or storage conditions? | Generally, they should be stored in dry, temperature-controlled environments to prevent oxidation and maintain their quality. |
How do gas-trapped pores affect the surface finish of parts? | Pores can create a rougher surface finish, which might require additional polishing or smoothing processes. |
Can minor gas-trapped pores powders be used in 3D printing? | Absolutely! These powders are commonly used in additive manufacturing for creating complex geometries with specific material properties. |
Are there any environmental concerns related to these powders? | As with any metal powder, proper handling and disposal are necessary to minimize environmental impact, but the pores themselves are not harmful. |
What factors should be considered when selecting a supplier for these powders? | Consider factors like material quality, pricing, lead times, and the supplier’s reputation for consistency and reliability. |
Conclusion
Minor gas-trapped pores powders represent a fascinating intersection of material science and advanced manufacturing technology. Their unique properties make them invaluable in industries ranging from aerospace to medical devices. By understanding the composition, characteristics, and applications of these powders, manufacturers can better tailor their products to meet specific performance requirements.
Whether you’re looking for lightweight, high-strength components or materials with specialized thermal properties, minor gas-trapped pores powders offer a wide array of possibilities. When choosing the right powder, it’s crucial to consider the balance between advantages and limitations, ensuring the best possible outcome for your project.
Explore these materials further, experiment with different compositions, and discover how minor gas-trapped pores powders can revolutionize your manufacturing processes.
About 3DP mETAL
Product Category
CONTACT US
Any questions? Send us a message now! After receiving your message, we will process your request with a whole team.