Imagine building complex metal parts layer by layer, like stacking molten Legos. That’s the magic of Molten Metal Deposition (MMD), a cutting-edge metal additive manufacturing (AM) process that’s transforming how we create functional and intricate metal components. But MMD is more than just a cool trick; it offers a powerful set of advantages that are shaking up the world of metal fabrication.
This comprehensive guide dives deep into the fascinating world of MMD. We’ll explore its operational principles, unveil its unique benefits, and delve into the exciting applications that are pushing the boundaries of what’s possible. So, buckle up and get ready to be amazed by the world of Molten Metal Deposition!
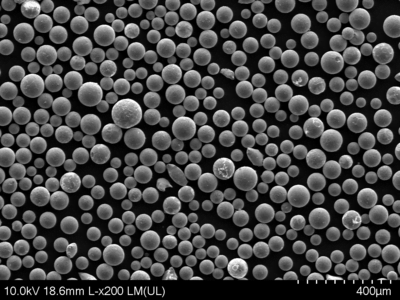
Operational Principle of Molten Metal Deposition (MMD)
At its core, MMD is a single-step metal AM process that utilizes a continuous strand of metal wire as its feedstock. Here’s a breakdown of the magic behind this innovative technology:
- Feeding the Beast: The process starts with a spool of metal wire, typically aluminum or titanium, that’s fed into a specialized feeder mechanism. Think of it as a high-tech spool holder that constantly pushes the wire forward.
- Heating Up the Action: The wire then travels into a heated chamber, where it gets blasted with intense heat. This heat, often generated by a plasma arc or resistance heating, melts the metal wire, transforming it from a solid strand into a molten pool.
- Precise Extrusion: The molten metal doesn’t get to relax in its liquid state for long. It’s pushed through a narrow nozzle at the bottom of the heating chamber, acting like a high-tech toothpaste tube for molten metal.
- Building Block by Block: As the molten metal exits the nozzle, it’s deposited layer by layer onto a pre-heated build platform. Imagine a tiny robot meticulously squeezing out dollops of molten metal, building the desired shape one layer at a time.
- Fusion Frenzy: The beauty of MMD lies in the fusion process. The extreme heat of the molten metal causes it to bond seamlessly with the previously deposited layer, creating a strong and continuous structure.
Think of it this way: Picture a skilled pastry chef meticulously piping out layer upon layer of molten chocolate to create a stunning and intricate chocolate sculpture. MMD operates on a similar principle, but with much higher temperatures and way cooler applications (no offense to chocolate!).
The key advantage of MMD lies in its single-step nature. Unlike other metal AM processes that involve complex laser melting or powder bed fusion, MMD relies on simple molten metal deposition, making it a more cost-effective and potentially faster option.
the Advantages: Why MMD is a Game Changer
MMD boasts a compelling set of advantages that make it a highly attractive option for various metal fabrication applications. Here are some of the key benefits that set MMD apart:
- Cost-Effectiveness: Compared to other metal AM processes like Laser Beam Melting (LBM) or Selective Laser Sintering (SLS), MMD can be significantly cheaper. This is primarily due to its simpler setup and the use of readily available metal wire as feedstock.
- Speed Demon: MMD can be a real speedster in the world of metal AM. The single-step deposition process and the continuous nature of the metal wire feedstock allow for faster build times compared to some powder-based AM techniques.
- Material Versatility: MMD isn’t picky when it comes to materials. It can handle a wide range of metal wires, including aluminum, titanium, steel, and even some exotic alloys. This versatility opens doors for creating components from various metals with unique properties.
- Large Build Volume: MMD systems often offer larger build volumes compared to some other metal AM technologies. This allows for the creation of bigger and more complex metal parts in a single build.
- Minimal Post-Processing: Unlike some other AM processes that require extensive post-processing steps like support removal, MMD often requires minimal post-processing, leading to faster turnaround times and lower overall production costs.
Think of it this way: MMD is like the Swiss Army knife of metal AM. It’s cost-effective, fast, versatile, and requires minimal fuss, making it a valuable tool for a wide range of applications.
However, like any technology, MMD does have some limitations to consider:
- Surface Finish: While MMD offers good dimensional accuracy, the surface finish of the parts can be slightly rougher compared to some other AM processes. This might necessitate additional post-processing steps for applications requiring a smoother finish.
- Material Properties: The rapid solidification of metal in MMD can sometimes lead to variations in the microstructure of the final part, potentially affecting its mechanical properties.
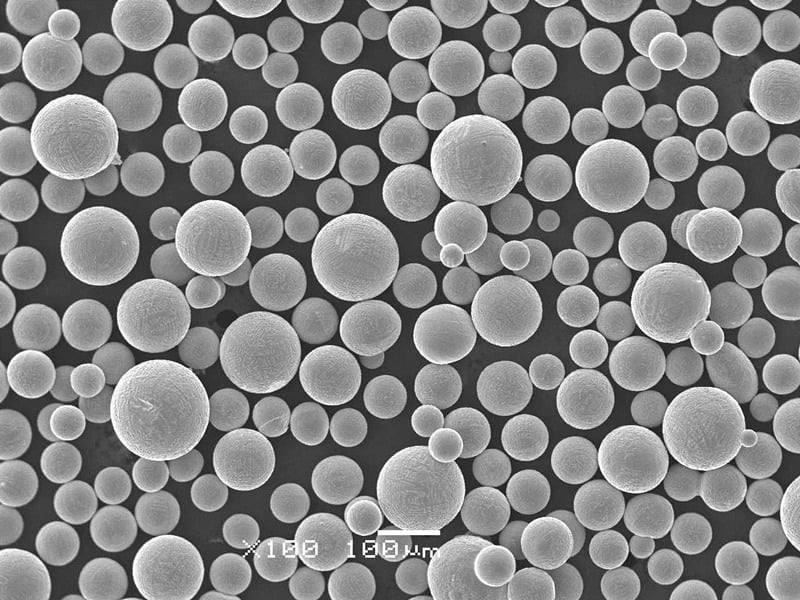
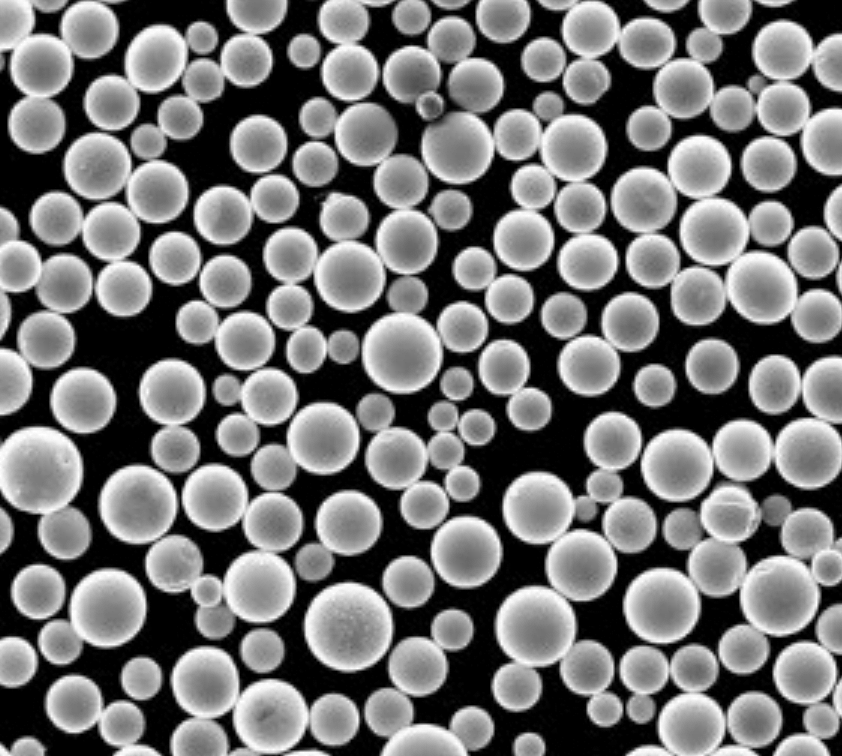
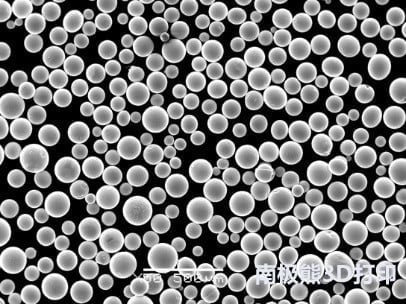
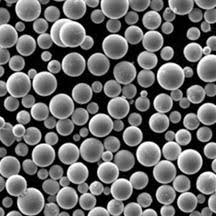
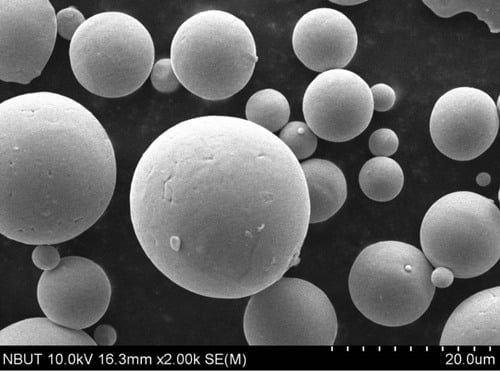
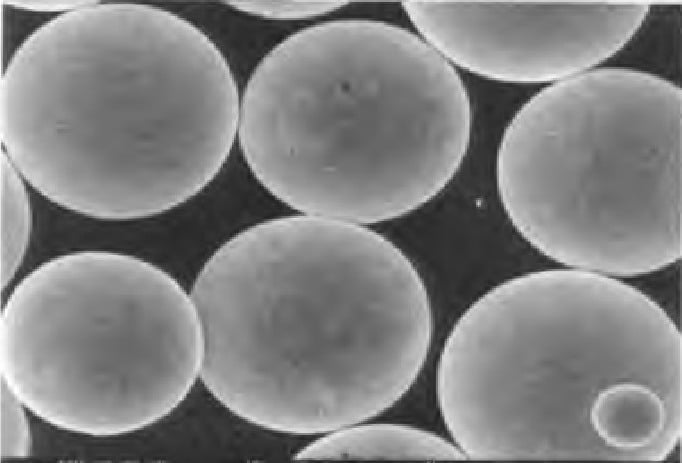
Applications of Molten Metal Deposition (MMD)
The exciting world of MMD extends far beyond the technical aspects. Let’s delve into the diverse applications where MMD is making a significant impact:
1. Aerospace and Defense: Soaring to New Heights
The aerospace and defense industries are constantly pushing the boundaries of design and functionality. MMD’s ability to create lightweight, high-strength metal components makes it a perfect fit for these demanding applications. Here are some specific examples:
- Aircraft Components: MMD can be used to create lightweight and strong aircraft components like wing parts, brackets, and even heat exchangers. The ability to use aluminum and titanium, both popular choices in aircraft construction, makes MMD even more attractive.
- Missile Components: The high-speed deposition and minimal post-processing of MMD make it ideal for creating complex and functional missile components.
- Spacecraft Parts: MMD’s ability to handle a wider range of materials, including exotic alloys, opens doors for creating specialized components for spacecraft that can withstand the harsh conditions of space.
The Impact: By using MMD, aerospace and defense companies can create lighter and stronger components, leading to improved fuel efficiency, increased payload capacity, and overall better performance for aircrafts, missiles, and spacecraft.
2. Automotive Industry: Revving Up Innovation
The automotive industry is constantly innovating to create lighter, more fuel-efficient vehicles. MMD is emerging as a game-changer in this arena:
- Engine Components: MMD can be used to create complex engine components like pistons, cylinder heads, and even intake manifolds. The ability to use high-strength aluminum alloys allows for weight reduction without compromising performance.
- Custom Parts: MMD’s flexibility and fast turnaround times make it ideal for creating custom parts for prototypes and low-volume production runs, accelerating the development of new automotive technologies.
- Electric Vehicle Parts: The lightweight and high-strength properties of MMD-created components are highly desirable for electric vehicles, where weight reduction is crucial for maximizing range.
The Impact: MMD is helping the automotive industry achieve lighter vehicles with improved fuel efficiency and performance. This translates to a more sustainable future for transportation.
3. Medical and Biomedical Applications: Healing Touches
The medical and biomedical fields are constantly seeking ways to improve patient care and develop innovative solutions. MMD is making its mark in this critical area:
- Prosthetic Limbs: MMD offers the potential to create custom-made prosthetic limbs with complex geometries and biocompatible materials like titanium. This can lead to improved functionality, comfort, and overall well-being for amputees.
- Medical Implants: MMD can be used to create intricate medical implants like spinal cages and dental implants with high precision and using biocompatible materials, leading to better patient outcomes.
- Surgical Tools: The ability to create complex and customized surgical tools with MMD opens doors for minimally invasive surgeries, potentially leading to faster recovery times and reduced patient discomfort.
The Impact: MMD is playing a vital role in advancing medical and biomedical technologies. By creating custom-made implants, prosthetics, and surgical tools, MMD is contributing to improved patient care and a healthier future.
4. Consumer Goods: Everyday Applications
The influence of MMD isn’t limited to high-tech industries. It’s gradually making its way into the world of consumer goods:
- Sporting Goods: MMD can be used to create lightweight and high-strength components for sporting goods like bicycle frames, golf clubs, and even baseball bats. This can lead to improved performance and a more dynamic user experience.
- Consumer Electronics: The ability to create complex and intricate shapes with MMD opens doors for developing innovative consumer electronics with unique designs and functionalities.
The Impact: MMD is transforming the world of consumer goods by enabling the creation of lighter, stronger, and more innovative products that enhance our everyday lives.
5. Rapid Prototyping and Low-Volume Production
MMD’s ability to quickly create functional prototypes makes it a valuable tool for various industries. Here’s why:
- Faster Design Iteration: Compared to traditional manufacturing methods, MMD allows for rapid creation of prototypes, speeding up the design iteration process and allowing for quicker product development cycles.
- Reduced Costs: For low-volume production runs, MMD can be a more cost-effective alternative to traditional manufacturing methods like machining or casting.
- Design Flexibility: MMD’s ability to handle complex geometries allows for the creation of intricate and innovative prototypes that might be difficult or expensive to produce using traditional methods.
The Impact: MMD is accelerating the pace of innovation across various industries by enabling faster and more cost-effective prototyping, leading to the development of better products in a shorter timeframe.
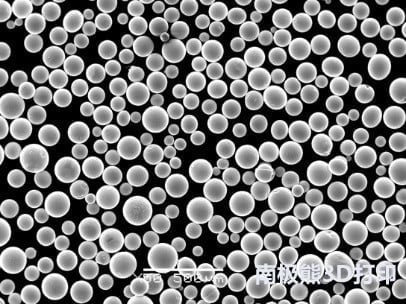
FAQ
What is Molten Metal Deposition (MMD)?
Molten Metal Deposition (MMD) is a type of 3D printing process that uses a continuous metal wire to create objects. The wire is fed into a heated chamber where it melts, and the molten metal is then extruded through a nozzle and deposited onto a build platform. A plasma jet preheats the area where the metal is being deposited, ensuring a strong bond with the previous layer.
What are the advantages of MMD?
- Faster and more affordable: Compared to other metal 3D printing methods like powder bed fusion, MMD is faster and uses cheaper materials like metal wire or even granulate. This makes it a more accessible option for metal 3D printing.
- Higher deposition rates: MMD boasts high deposition rates, meaning it can create objects quickly and efficiently.
- Reduced post-processing: MMD requires minimal post-processing steps compared to other methods, streamlining the production process.
What are some disadvantages of MMD?
- Surface finish: MMD-printed objects may have a rougher surface finish compared to other 3D printing methods.
- Limited material selection: While MMD is being developed for a wider range of metals, the current selection of materials is more limited compared to other methods.
What are some applications of MMD?
MMD is well-suited for creating large metal parts due to its speed and efficiency. Some potential applications include:
- Manufacturing structural components for aerospace or automotive industries
- Creating molds and tooling
- Building heat exchangers
Is MMD a new technology?
MMD is a developing technology, but it’s gaining traction in the field of additive manufacturing. Companies like ValCUN are receiving grants to further develop the process.
About 3DP mETAL
Product Category
CONTACT US
Any questions? Send us a message now! After receiving your message, we will process your request with a whole team.