Welcome to the fascinating world of Molten Metal Deposition (MMD). In this article, we’ll delve deep into the nuances of MMD, exploring its applications, types, and much more. Whether you’re an engineering enthusiast, a seasoned professional, or just curious about the latest in manufacturing technology, this guide is for you.
Overview of Molten Metal Deposition (MMD)
Molten Metal Deposition (MMD) is a cutting-edge additive manufacturing process where metal is melted and deposited layer by layer to create intricate and robust structures. This technique stands at the forefront of modern manufacturing, offering unparalleled precision and flexibility.
Types of Metal Powders for MMD
Understanding the various types of metal powders used in MMD is crucial for selecting the right material for your project. Here’s a detailed look at some specific metal powder models:
Metal Powder Model | Composition | Properties | Characteristics |
---|---|---|---|
AlSi10Mg | Al, Si, Mg | Lightweight, Strong | Excellent for casting |
Inconel 718 | Ni, Cr, Fe | High Strength, Corrosion Resistant | Ideal for aerospace |
Ti6Al4V | Ti, Al, V | High Strength-to-Weight Ratio | Widely used in medical implants |
Stainless Steel 316L | Fe, Cr, Ni, Mo | Corrosion Resistant, Durable | Common in marine applications |
Maraging Steel | Fe, Ni, Mo, Co | Ultra-High Strength | Used in tooling and aerospace |
Copper C18150 | Cu, Cr, Zr | High Conductivity | Excellent for electrical applications |
Nickel Alloy 625 | Ni, Cr, Mo | High Temperature Resistance | Suitable for chemical industries |
Tool Steel H13 | Fe, Cr, Mo, V | High Wear Resistance | Perfect for die casting molds |
Cobalt Chrome Alloy | Co, Cr, Mo | High Wear and Corrosion Resistance | Utilized in dental and medical fields |
Aluminium 7075 | Al, Zn, Mg, Cu | High Strength | Used in aerospace and sports equipment |
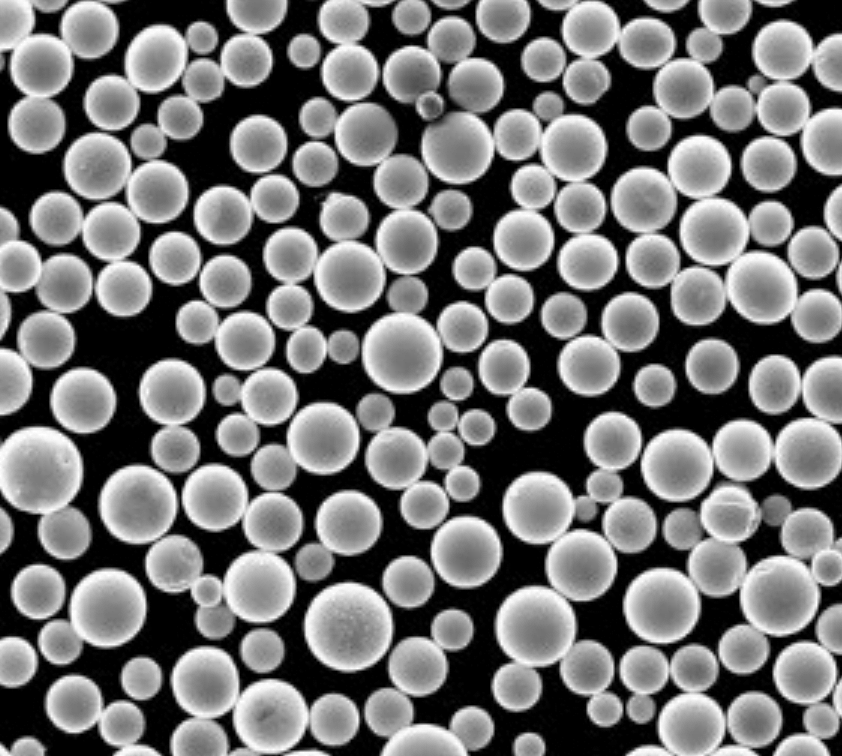
Composition of Molten Metal Deposition (MMD)
The composition of the metal powders significantly impacts the properties and performance of the final product. Each metal powder is engineered to meet specific needs:
- AlSi10Mg: Aluminum alloyed with Silicon and Magnesium, known for its lightweight and high strength.
- Inconel 718: A nickel-chromium alloy that offers high strength and resistance to corrosion and heat.
- Ti6Al4V: Titanium alloyed with Aluminum and Vanadium, celebrated for its superior strength-to-weight ratio.
- Stainless Steel 316L: Comprising Iron, Chromium, Nickel, and Molybdenum, it’s renowned for its corrosion resistance and durability.
- Maraging Steel: A mix of Iron, Nickel, Molybdenum, and Cobalt, noted for its ultra-high strength.
Characteristics of Molten Metal Deposition (MMD)
MMD’s unique characteristics make it suitable for various applications. Here are some key features:
- Precision: MMD allows for the creation of intricate and precise designs that traditional manufacturing methods cannot achieve.
- Flexibility: The ability to use a variety of metal powders means MMD can be tailored to specific applications.
- Efficiency: Reduced material waste compared to subtractive manufacturing methods.
- Strength: The layer-by-layer deposition process can produce components with superior mechanical properties.
Applications of Molten Metal Deposition (MMD)
MMD is revolutionizing many industries. Here’s how it’s being used across different sectors:
Industry | Applications |
---|---|
Aerospace | Turbine blades, structural components |
Automotive | Engine parts, custom tools |
Medical | Orthopedic implants, dental prosthetics |
Marine | Corrosion-resistant parts |
Electrical | Conductive components, connectors |
Tooling | Molds, dies, and jigs |
Consumer Goods | Customizable products, sports equipment |
Chemical Processing | High-temperature resistant components |
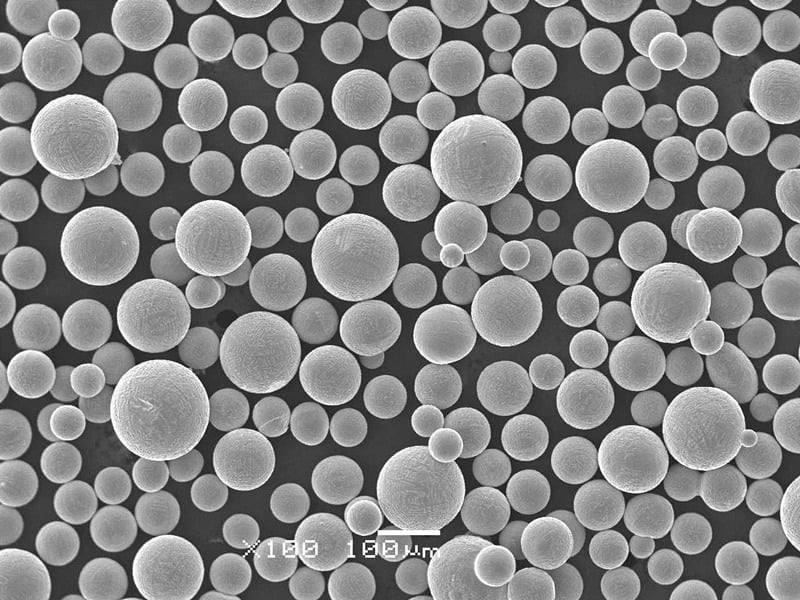
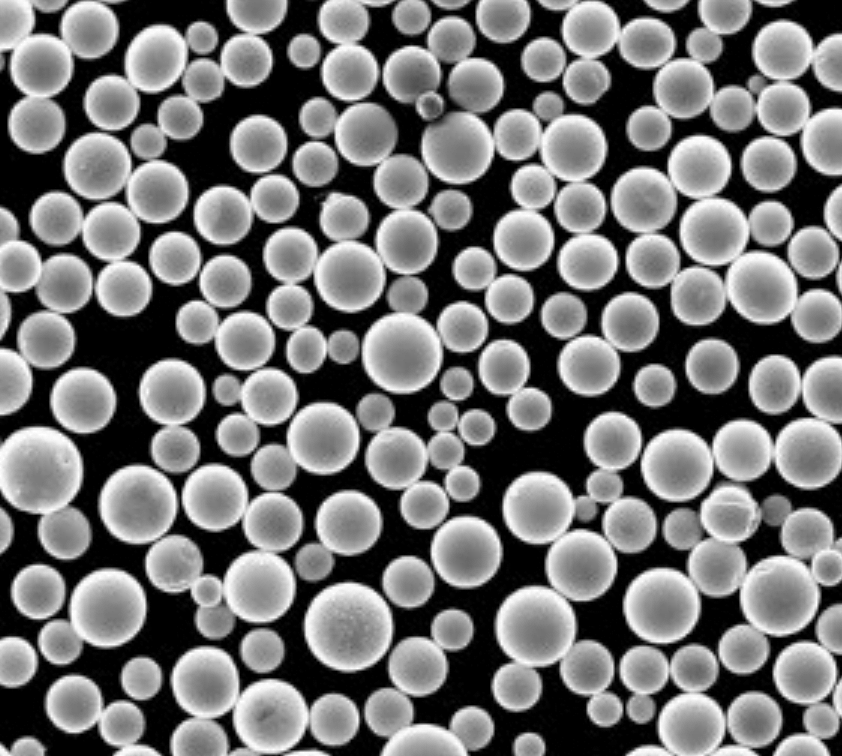
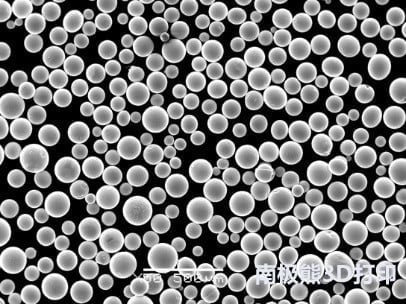
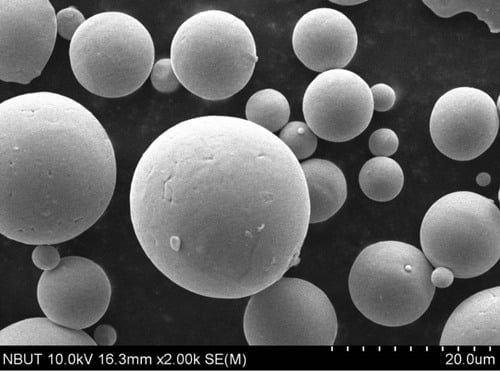
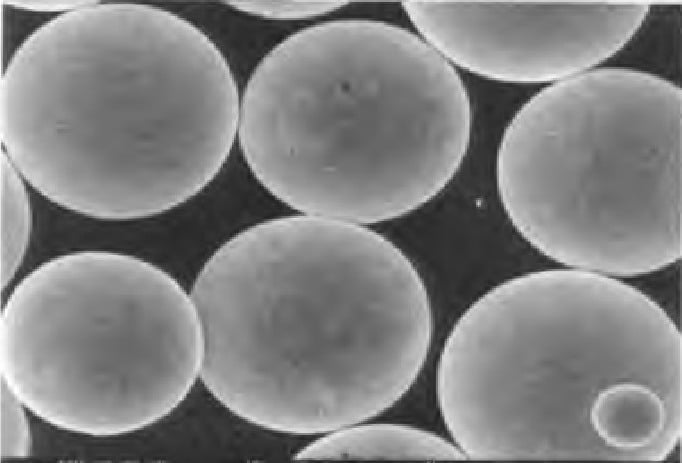
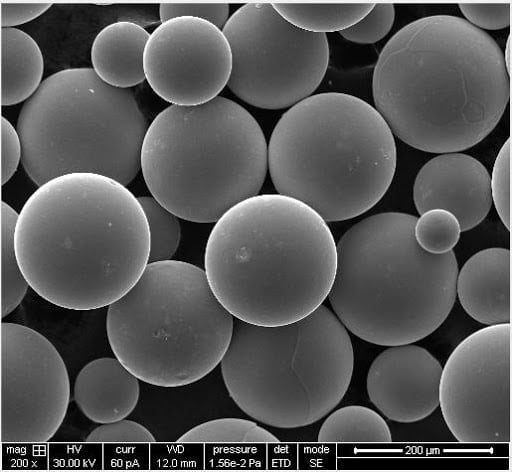
Specifications, Sizes, Grades, and Standards in MMD
When selecting materials for MMD, understanding the specifications, sizes, grades, and standards is essential. Here’s a detailed look:
Metal Powder Model | Specifications | Sizes (μm) | Grades | Standards |
---|---|---|---|---|
AlSi10Mg | ASTM B918 | 15-45 | Standard Grade | ISO 20902 |
Inconel 718 | AMS 5662 | 15-53 | Premium Grade | ASTM F3055 |
Ti6Al4V | ASTM F2924 | 10-45 | Medical Grade | ISO 5832-3 |
Stainless Steel 316L | ASTM A276 | 10-45 | Industrial Grade | ISO 5832-1 |
Maraging Steel | AMS 6514 | 15-53 | Tool Grade | DIN 1.2709 |
Copper C18150 | ASTM B124 | 15-45 | Electrical Grade | ISO 431 |
Nickel Alloy 625 | AMS 5666 | 15-53 | Industrial Grade | ASTM B443 |
Tool Steel H13 | ASTM A681 | 15-45 | Tool Grade | ISO 4957 |
Cobalt Chrome Alloy | ASTM F75 | 10-45 | Medical Grade | ISO 5832-4 |
Aluminium 7075 | ASTM B211 | 15-45 | Aerospace Grade | AMS 4045 |
Suppliers and Pricing Details
Navigating the market for metal powders involves understanding suppliers and pricing:
Supplier | Metal Powder Models Available | Pricing (USD/kg) |
---|---|---|
EOS | AlSi10Mg, Ti6Al4V, Inconel 718 | $300 – $500 |
Höganäs | Stainless Steel 316L, Maraging Steel | $200 – $400 |
Carpenter | Inconel 718, Tool Steel H13 | $250 – $450 |
GKN Additive | AlSi10Mg, Copper C18150 | $220 – $420 |
LPW Technology | Ti6Al4V, Nickel Alloy 625 | $270 – $470 |
Sandvik | Stainless Steel 316L, Cobalt Chrome | $230 – $430 |
AP&C | Aluminium 7075, Inconel 718 | $310 – $510 |
Renishaw | Ti6Al4V, Maraging Steel | $280 – $480 |
Praxair | Copper C18150, Tool Steel H13 | $240 – $440 |
Oerlikon | Nickel Alloy 625, Aluminium 7075 | $260 – $460 |
Advantages and Limitations of Molten Metal Deposition (MMD)
Every technology has its pros and cons. Here’s a comparative look at MMD:
Aspect | Advantages | Limitations |
---|---|---|
Precision | High precision and intricate details | Requires high-quality control |
Material Usage | Efficient material usage, less waste | Initial material cost can be high |
Flexibility | Can use a wide range of metal powders | Not all metals are compatible |
Production Speed | Faster prototyping and production cycles | Speed can vary based on complexity and material |
Strength | Superior mechanical properties | Potential for internal defects if not monitored carefully |
Customization | Easy customization for specific applications | Requires specialized equipment and expertise |
Cost | Lower operational costs over time | High initial setup and equipment cost |
Comparing Metal Powders for MMD
To make an informed choice, let’s compare some metal powders based on different parameters:
Parameter | AlSi10Mg | Inconel 718 | Ti6Al4V | Stainless Steel 316L | Maraging Steel |
---|---|---|---|---|---|
Strength | Medium | High | High | Medium | Very High |
Weight | Light | Medium | Light | Medium | Heavy |
Corrosion Resistance | Medium | Very High | High | Very High | Medium |
Thermal Resistance | Medium | Very High | High | High | Medium |
Cost | Low | High | High | Medium | High |
Insights and Examples
Imagine creating a custom automotive part. You’d want a material that’s both lightweight and strong. Here, AlSi10Mg is an excellent choice due to its impressive strength-to-weight ratio. For a high-temperature application, Inconel 718 would be more suitable due to its superior thermal resistance.
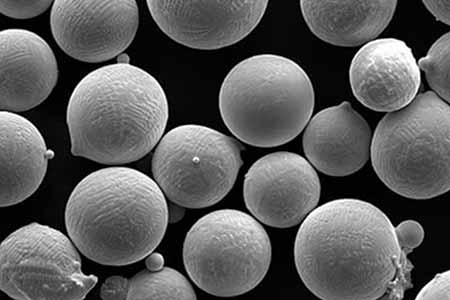
FAQ
Question | Answer |
---|---|
What is Molten Metal Deposition (MMD)? | MMD is an additive manufacturing process that deposits molten metal layer by layer to create detailed and robust structures. |
Which metals can be used in MMD? | Various metals including Aluminum alloys, Titanium alloys, Nickel alloys, Stainless steels, and more. |
What industries benefit most from MMD? | Aerospace, automotive, medical, marine, electrical, tooling, consumer goods, and chemical processing industries. |
How does MMD compare to traditional manufacturing methods? | MMD offers higher precision, flexibility, and efficiency with less material waste, but requires specialized equipment and expertise. |
What are the costs associated with MMD? | Initial setup and material costs can be high, but operational costs are lower over time. |
Can MMD produce complex shapes? | Yes, MMD can create intricate and complex shapes that are difficult or impossible with traditional methods. |
Is MMD environmentally friendly? | MMD is more environmentally friendly due to reduced material waste compared to subtractive manufacturing processes. |
What are the limitations of MMD? | Potential for internal defects, high initial costs, and the need for high-quality control and specialized knowledge. |
What is the typical size range of metal powders used in MMD? | Metal powders typically range from 10 to 53 micrometers in size. |
Who are some leading suppliers of metal powders for MMD? | Leading suppliers include EOS, Höganäs, Carpenter, GKN Additive, LPW Technology, Sandvik, AP&C, Renishaw, Praxair, and Oerlikon. |
Conclusion
Molten Metal Deposition (MMD) is transforming manufacturing with its precision, efficiency, and flexibility. By understanding the various metal powders, their compositions, and characteristics, you can leverage this technology to its fullest potential. Whether you’re crafting aerospace components or customizing medical implants, MMD offers solutions that are both innovative and practical.
So, what will you create next with MMD? The possibilities are as limitless as your imagination!
About 3DP mETAL
Product Category
CONTACT US
Any questions? Send us a message now! After receiving your message, we will process your request with a whole team.