Introduction
In the rapidly evolving world of additive manufacturing, multi-laser printing has emerged as a groundbreaking technique. It’s revolutionizing the production of metal parts by increasing efficiency, enhancing precision, and enabling the creation of complex geometries that were once considered impossible. But what truly fuels this technology? The answer lies in the powder used for multi-laser printing.
This article delves deep into the world of powders used in multi-laser printing, exploring various models, their compositions, characteristics, applications, and more. Whether you’re a seasoned engineer, a curious tech enthusiast, or someone exploring the potential of additive manufacturing, this guide is tailored to meet your needs. Let’s start our journey by understanding the basics.
Overview of Powders for Multi-Laser Printing
What is Multi-Laser Printing?
Multi-laser printing, also known as multi-laser powder bed fusion (PBF), is a type of additive manufacturing that uses multiple lasers to selectively melt powder materials layer by layer. This method is commonly used for metals and is prized for its ability to produce highly detailed and structurally sound parts.
Key Points:
- Multiple Lasers: Increases production speed and allows for the creation of more complex parts.
- Precision: Ensures high accuracy in part dimensions.
- Versatility: Can work with a wide range of metal powders.
Why the Choice of Powder Matters
The success of multi-laser printing heavily depends on the powder used. The quality, composition, and characteristics of the powder directly impact the final product’s strength, durability, and appearance. This section will explore the importance of choosing the right powder and the factors to consider when selecting one.
Factors to Consider:
- Particle Size and Shape: Affects flowability and packing density.
- Composition: Determines the material properties of the final product.
- Purity: Impacts the quality and consistency of the printed parts.
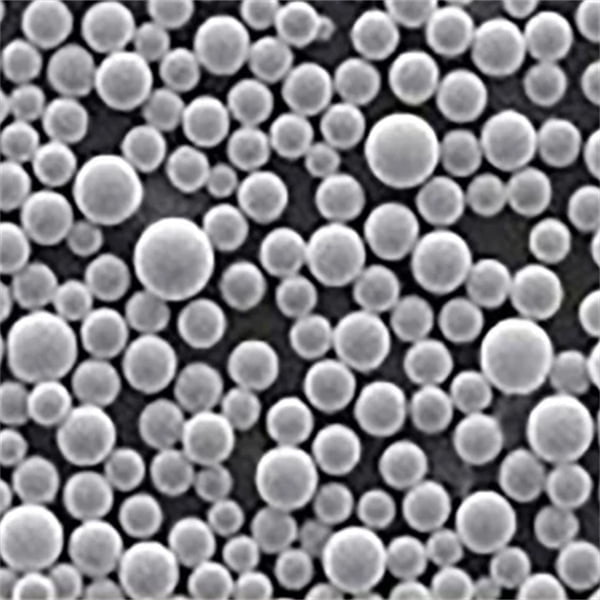
Types of Powders for Multi-Laser Printing
Understanding Different Powder Models
There are various powders available in the market for multi-laser printing, each tailored for specific applications. Let’s explore some of the most popular models.
Powder Model | Composition | Characteristics | Applications | Advantages | Limitations |
---|---|---|---|---|---|
Inconel 718 | Nickel-Chromium | High strength, corrosion resistance | Aerospace, turbines | Resistant to high temperatures | Expensive, difficult to process |
Ti-6Al-4V | Titanium alloy | Lightweight, strong | Medical implants, aerospace | Biocompatible, strong | Brittle under certain conditions |
316L Stainless Steel | Iron-Nickel-Chromium | Corrosion resistance, good weldability | Medical devices, food processing | Cost-effective, easy to work with | Lower strength compared to other metals |
AlSi10Mg | Aluminum alloy | Lightweight, good thermal properties | Automotive, aerospace | High conductivity, easy to process | Limited strength, not suitable for high-stress applications |
CoCrMo | Cobalt-Chrome-Molybdenum | High wear resistance, biocompatibility | Dental, orthopedic implants | Durable, long-lasting | Expensive, limited availability |
CuNi2SiCr | Copper-Nickel-Silicon-Chromium | Excellent electrical conductivity, corrosion resistance | Electrical components, heat exchangers | Conductive, easy to process | Expensive, limited mechanical strength |
Maraging Steel | Nickel-Cobalt-Molybdenum | High strength, toughness | Tooling, high-stress applications | Heat-treatable, durable | Limited corrosion resistance, expensive |
Hastelloy X | Nickel-Chromium-Molybdenum | High-temperature strength, oxidation resistance | Aerospace, chemical processing | Durable, strong under high temperatures | Expensive, difficult to process |
Al6061 | Aluminum alloy | High strength-to-weight ratio, corrosion resistance | Automotive, aerospace | Lightweight, easy to work with | Limited fatigue strength |
Tantalum | Pure Tantalum | High melting point, biocompatibility | Medical implants, electronics | Extremely durable, resistant to corrosion | Very expensive, limited availability |
Composition of Powder for Multi-Laser Printing
The composition of metal powders is crucial as it determines the material properties of the printed part. Each element in the alloy plays a specific role, influencing factors like strength, corrosion resistance, and thermal stability. Let’s dive into the composition of some key powders used in multi-laser printing.
Characteristics of Powder for Multi-Laser Printing
Particle Size and Shape
The particle size and shape of the powder are critical in ensuring smooth printing operations. Spherical particles, for example, offer better flowability, leading to more uniform layers during printing.
Powder Type | Particle Size (µm) | Particle Shape | Impact on Printing |
---|---|---|---|
Inconel 718 | 15-45 µm | Spherical | Good flowability, high packing density |
Ti-6Al-4V | 20-60 µm | Spherical | Consistent layer formation, less porosity |
316L Stainless Steel | 10-50 µm | Irregular | Varies in flowability, suitable for detailed work |
AlSi10Mg | 15-45 µm | Spherical | Excellent flow, easy to process |
CoCrMo | 20-60 µm | Spherical | Consistent layer formation, high density |
CuNi2SiCr | 15-45 µm | Irregular | Requires careful handling, moderate flow |
Maraging Steel | 10-50 µm | Spherical | Good packing, high strength |
Hastelloy X | 15-45 µm | Spherical | Excellent thermal stability, smooth printing |
Al6061 | 20-60 µm | Spherical | Lightweight, easy to handle |
Tantalum | 15-45 µm | Spherical | High melting point, challenging to process |
Applications of Powders in Multi-Laser Printing
Diverse Industry Applications
The versatility of multi-laser printing has opened doors to numerous industries, each benefiting from the specific properties of different metal powders. Let’s explore how these powders are used across various sectors.
Industry | Common Powders | Applications |
---|---|---|
Aerospace | Inconel 718, Ti-6Al-4V | Turbine blades, engine components |
Medical | Ti-6Al-4V, CoCrMo | Implants, surgical instruments |
Automotive | AlSi10Mg, Al6061 | Lightweight parts, structural components |
Tooling | Maraging Steel, Inconel 718 | Injection molds, cutting tools |
Electronics | CuNi2SiCr, Tantalum | Electrical connectors, heat sinks |
Chemical Processing | Hastelloy X, Inconel 718 | Valves, pumps, chemical reactors |
Food Processing | 316L Stainless Steel | Hygienic equipment, food contact surfaces |
Dental | CoCrMo, Ti-6Al-4V | Dental implants, orthodontic devices |
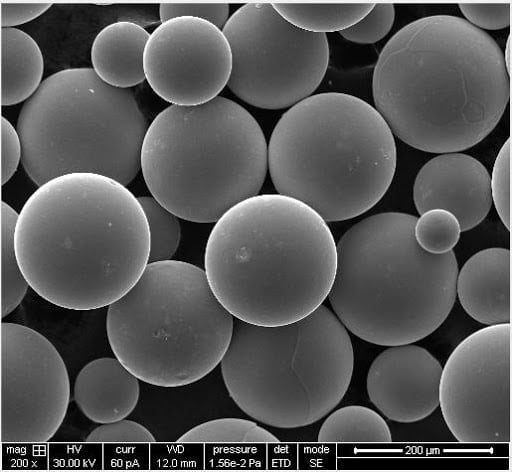
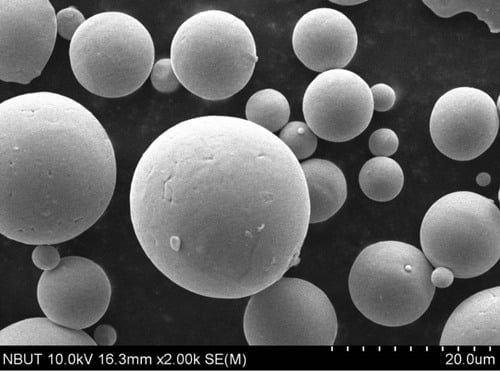
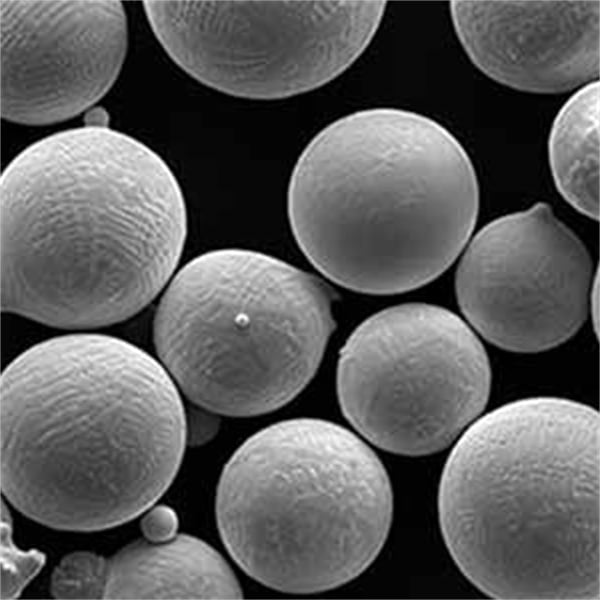
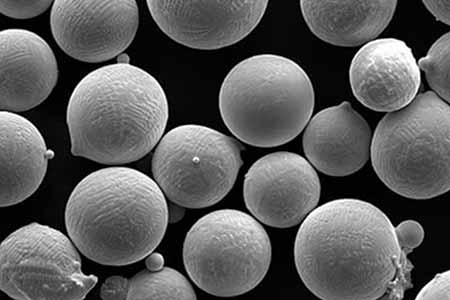
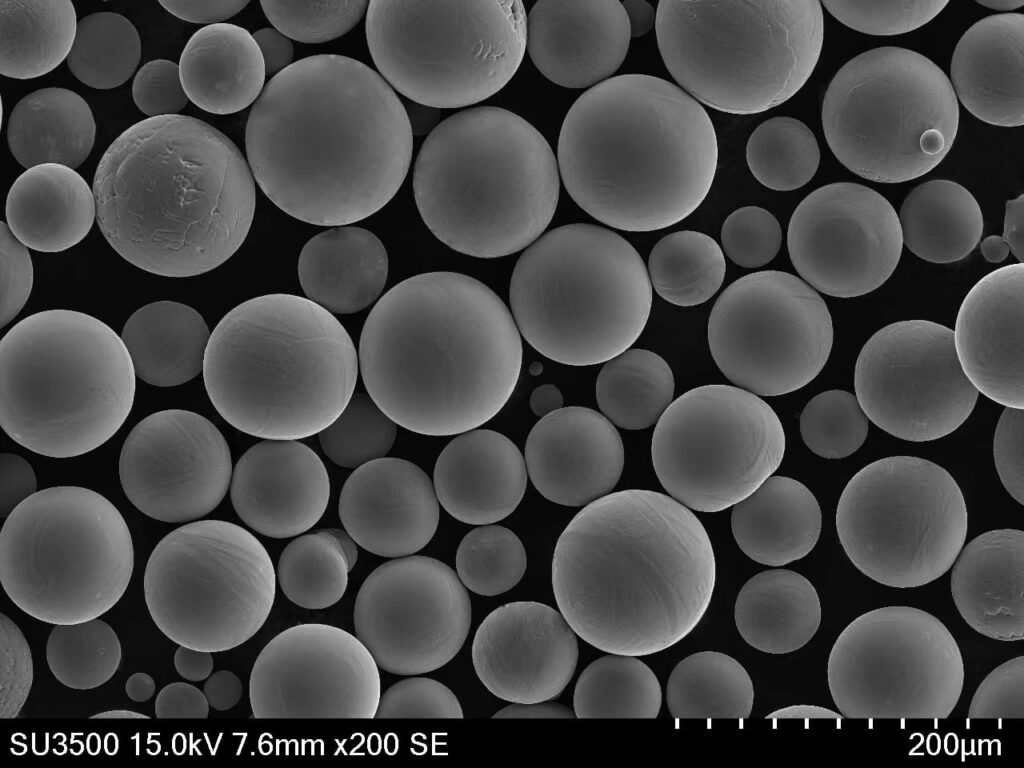
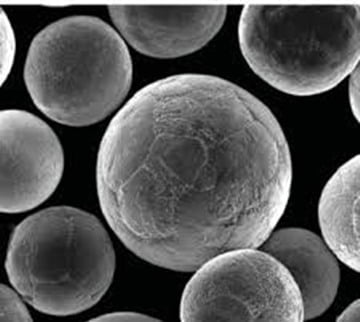
Specifications, Sizes, Grades, and Standards
Understanding Specifications and Standards
Each powder used in multi-laser printing adheres to specific standards and grades, ensuring consistency and quality. Here’s a breakdown of the specifications for some popular powders.
Powder Model | Size Range (µm) | Grade | Standards |
---|---|---|---|
Inconel 718 | 15-45 µm | AMS 5662, ASTM B637 | ASTM F3055-14a, ISO 15156 |
Ti-6Al-4V | 20-60 µm | Grade 5, Grade 23 | ASTM F2924, ISO 5832-3 |
316L Stainless Steel | 10-50 µm | UNS S31603 | ASTM A240, ASTM F138 |
AlSi10Mg | 15-45 µm | EN AW-6082 | ASTM B209, ISO 3522 |
CoCrMo | 20-60 µm | ASTM F75, ASTM F799 | ISO 5832-4, ISO 5832-12 |
CuNi2SiCr | 15-45 µm | UNS C18050 | ASTM B111, ASTM B171 |
Maraging Steel | 10-50 µm | 18Ni (300) | AMS 6514, ASTM A538 |
Hastelloy X | 15-45 µm | UNS N06002 | ASTM B435, AMS 5754 |
Al6061 | 20-60 µm | T6, T651 | ASTM B209, ASTM B221 |
Tantalum | 15-45 µm | ASTM F560 | ISO 13782, ASTM B708 |
Suppliers and Pricing Details
Where to Source Your Powders
The availability of metal powders for multi-laser printing is growing, with numerous suppliers offering various models. Below is a list of some reputable suppliers and approximate pricing for different powders.
Supplier | Powder Model | Price (per kg) | Availability |
---|---|---|---|
Höganäs | Inconel 718 | $150 – $200 | Worldwide |
Carpenter Additive | Ti-6Al-4V | $300 – $350 | Worldwide |
Sandvik Osprey | 316L Stainless Steel | $100 – $150 | Europe, North America |
AP&C (GE Additive) | AlSi10Mg | $80 – $120 | Worldwide |
EOS GmbH | CoCrMo | $250 – $300 | Europe, Asia |
GKN Additive | CuNi2SiCr | $200 – $250 | Worldwide |
Renishaw | Maraging Steel | $180 – $220 | Europe, North America |
Praxair Surface Technologies | Hastelloy X | $400 – $450 | Worldwide |
Metalysis | Al6061 | $90 – $130 | Europe, Asia |
Telex Metals | Tantalum | $500 – $600 | North America |
Advantages and Limitations of Using Specific Powders
Comparing Powder Models
When selecting a powder for multi-laser printing, it’s essential to weigh the advantages and limitations. Here’s a detailed comparison to help you make an informed decision.
Powder Model | Advantages | Limitations |
---|---|---|
Inconel 718 | High strength, excellent heat resistance | Expensive, challenging to process |
Ti-6Al-4V | Lightweight, biocompatible | Brittle, difficult to machine |
316L Stainless Steel | Corrosion resistant, easy to work with | Lower strength compared to other alloys |
AlSi10Mg | Lightweight, good thermal properties | Limited strength, not ideal for high-stress parts |
CoCrMo | Durable, biocompatible | Expensive, limited availability |
CuNi2SiCr | Excellent conductivity, corrosion resistance | High cost, limited mechanical strength |
Maraging Steel | High strength, heat-treatable | Limited corrosion resistance, expensive |
Hastelloy X | Outstanding high-temperature performance | Expensive, difficult to work with |
Al6061 | High strength-to-weight ratio, corrosion resistant | Lower fatigue strength |
Tantalum | Highly durable, biocompatible | Very expensive, difficult to source |
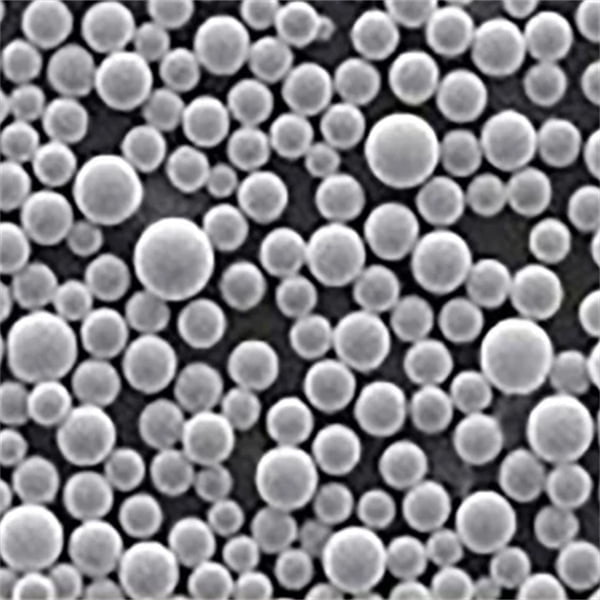
FAQs
Question | Answer |
---|---|
What is the best powder for high-temperature applications? | Inconel 718 and Hastelloy X are excellent choices due to their heat resistance. |
Is Ti-6Al-4V suitable for medical implants? | Yes, Ti-6Al-4V is biocompatible and widely used in medical implants. |
Which powder offers the best electrical conductivity? | CuNi2SiCr is highly conductive, making it ideal for electrical components. |
What are the most cost-effective powders? | 316L Stainless Steel and AlSi10Mg are more affordable options with good properties. |
Can I use multiple powders in a single print? | Generally, it’s best to stick with one powder per print to ensure consistency, though some advanced machines may allow blending. |
What is the typical particle size for powders? | Most powders range between 10-60 µm, with specific sizes depending on the application. |
How do I store metal powders? | Store them in a dry, cool place, away from any moisture to avoid oxidation or contamination. |
Conclusion
The world of multi-laser printing is as complex as it is fascinating, with metal powders at the heart of this technology. Whether you’re printing aerospace components, medical implants, or intricate tooling parts, the right powder can make all the difference. By understanding the types, compositions, characteristics, and applications of these powders, you can optimize your printing processes and achieve exceptional results.
About 3DP mETAL
Product Category
CONTACT US
Any questions? Send us a message now! After receiving your message, we will process your request with a whole team.