Overview
In today’s rapidly evolving technological landscape, the demand for advanced materials that offer a blend of different properties is skyrocketing. Enter multi-material structures. These innovative compositions combine two or more distinct materials to create products with superior performance characteristics. Think of it like a symphony orchestra where each instrument plays a vital role in creating a harmonious and powerful outcome. From aerospace to automotive industries, multi-material structures are paving the way for stronger, lighter, and more efficient designs. But what exactly are these materials, and why are they so revolutionary? Let’s dive into the world of multi-material structures, exploring their types, compositions, properties, applications, and more.
Types and Composition of Multi-Material Structures
Multi-material structures are created by integrating different materials, each contributing its unique properties to the final product. The combination can involve metals, polymers, ceramics, and composites. Here, we’ll focus on some popular metal powders used in multi-material structures.
Metal Powder | Composition | Properties |
---|---|---|
Aluminum 6061 | Al, Mg, Si, Fe, Cu, Mn, Cr, Zn, Ti | Lightweight, corrosion-resistant, strong |
Titanium Ti-6Al-4V | Ti, Al, V | High strength, lightweight, corrosion-resistant |
Stainless Steel 316L | Fe, Cr, Ni, Mo | High corrosion resistance, good weldability |
Inconel 718 | Ni, Cr, Fe, Mo, Nb, Ti, Al | Heat resistance, high strength |
Copper C11000 | Cu | Excellent conductivity, corrosion resistance |
Nickel 200 | Ni | Good mechanical properties, corrosion-resistant |
Cobalt Chrome | Co, Cr, Mo | Wear resistance, high-temperature strength |
Tungsten W | W | High density, high melting point |
Tool Steel H13 | Fe, Cr, Mo, V, Si | High toughness, heat resistance |
Bronze CuSn12 | Cu, Sn | Wear resistance, good machinability |
Each of these powders brings its own set of strengths to a multi-material structure, enabling engineers to design components that meet specific performance criteria.
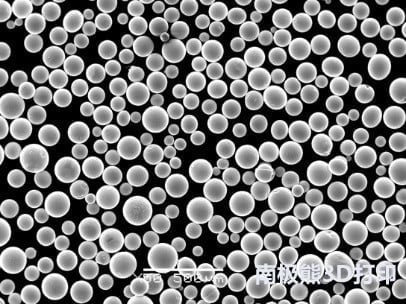
Characteristics of Multi-Material Structures
Multi-material structures stand out due to their unique blend of properties. Here’s a closer look at the characteristics that make them so valuable.
Characteristic | Description |
---|---|
Enhanced Strength | Combining materials can significantly increase the overall strength. |
Lightweight | Materials like aluminum and titanium reduce weight without sacrificing durability. |
Corrosion Resistance | Materials like stainless steel and Inconel enhance corrosion resistance. |
Thermal Stability | Multi-materials can maintain performance in extreme temperatures. |
Electrical Conductivity | Copper and nickel-based materials offer excellent electrical properties. |
Wear Resistance | Cobalt chrome and tool steel enhance wear resistance. |
By merging different materials, engineers can tailor multi-material structures to achieve specific performance goals that single-material structures cannot provide.
Applications of Multi-Material Structures
Multi-material structures are revolutionizing various industries by offering improved performance and efficiency. Here are some of the key applications.
Application | Description |
---|---|
Aerospace | Lightweight and strong components for aircraft and spacecraft. |
Automotive | Enhanced performance and fuel efficiency in vehicle parts. |
Medical Devices | Biocompatible materials for implants and prosthetics. |
Electronics | Improved conductivity and heat dissipation in electronic components. |
Construction | Durable and lightweight materials for building structures. |
Energy | Efficient and corrosion-resistant materials for power generation and storage. |
Defense | Strong and lightweight materials for armor and military equipment. |
Sports Equipment | High-performance materials for better durability and performance in sports gear. |
Robotics | Lightweight and durable materials for robotic components. |
Marine | Corrosion-resistant materials for underwater applications. |
These applications showcase the versatility and advantages of multi-material structures across different sectors.
Grades of Multi-Material Structures
Different grades of multi-material structures are used depending on the specific requirements of an application. Let’s explore some of these grades and their standards.
Grade | Composition | Standard | Application |
---|---|---|---|
Aluminum 6061-T6 | Al, Mg, Si, Fe, Cu, Mn, Cr, Zn, Ti | ASTM B221 | Aerospace, automotive |
Titanium Grade 5 | Ti, Al, V | ASTM B348 | Aerospace, medical devices |
Stainless 316L | Fe, Cr, Ni, Mo | ASTM A240 | Medical devices, marine |
Inconel 718 | Ni, Cr, Fe, Mo, Nb, Ti, Al | AMS 5662 | Aerospace, energy |
Copper C11000 | Cu | ASTM B152 | Electrical components |
Nickel 200 | Ni | ASTM B160 | Chemical processing, electronics |
Cobalt Chrome | Co, Cr, Mo | ASTM F75 | Medical implants, aerospace |
Tungsten W | W | ASTM B777 | Defense, aerospace |
Tool Steel H13 | Fe, Cr, Mo, V, Si | ASTM A681 | Tooling, molding |
Bronze CuSn12 | Cu, Sn | ASTM B505 | Bearings, bushings |
These grades ensure that multi-material structures meet the required performance standards for their intended applications.
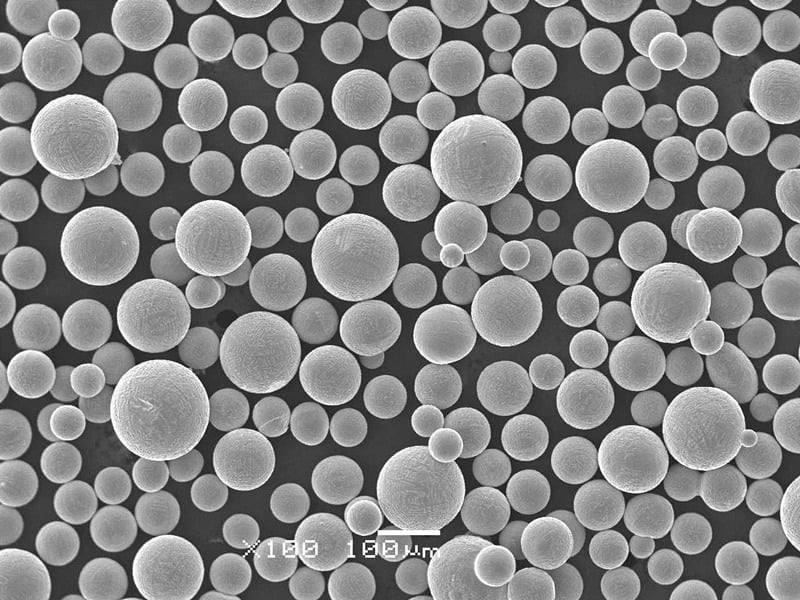
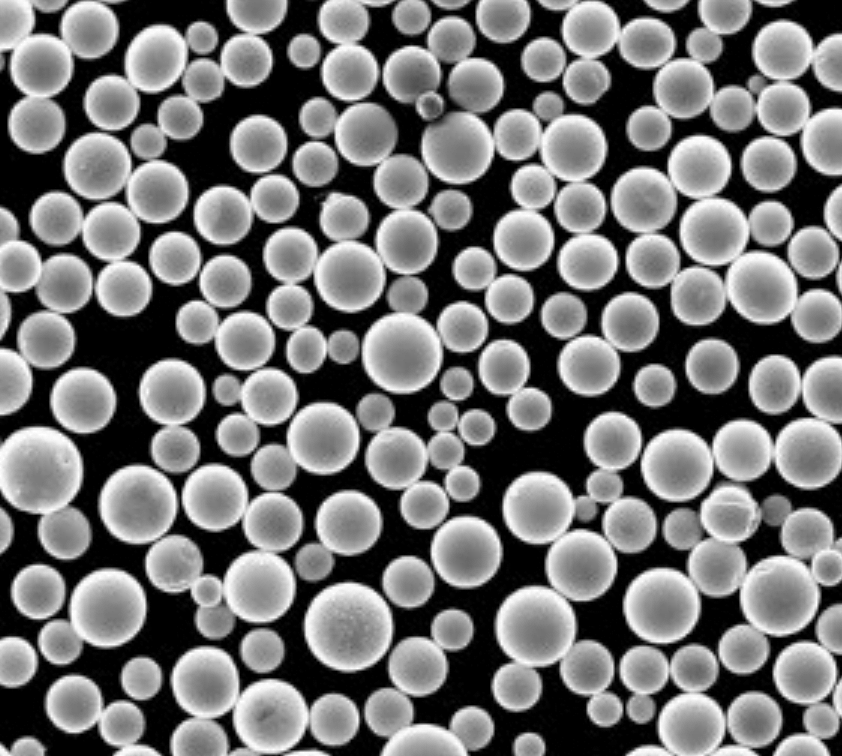
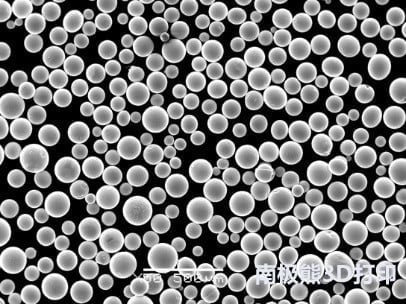
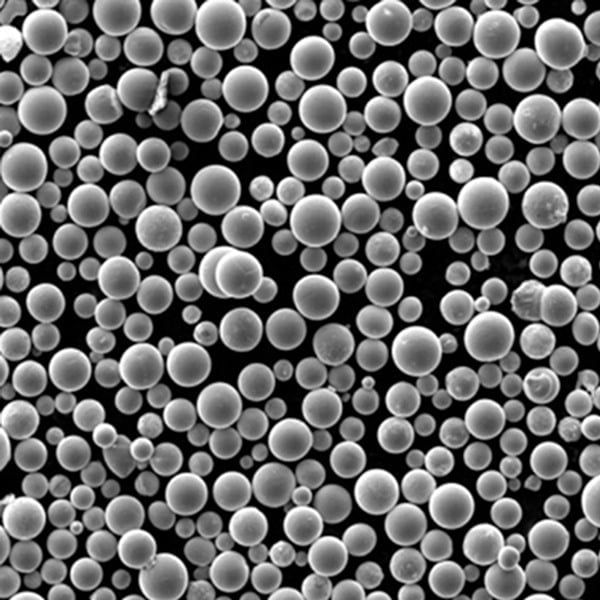
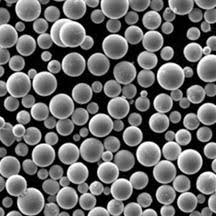
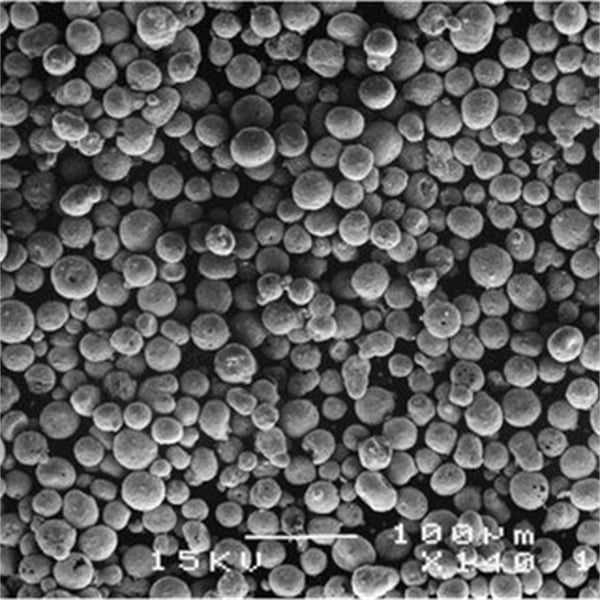
Suppliers and Pricing Details
Finding the right supplier and understanding the pricing details are crucial for sourcing multi-material structures. Here’s a breakdown of some leading suppliers and their offerings.
Supplier | Materials Offered | Pricing (Approx.) | Region |
---|---|---|---|
Carpenter Technology | Stainless Steel, Titanium, Inconel | $50 – $200 per kg | Global |
Sandvik Materials | Stainless Steel, Titanium | $60 – $180 per kg | Global |
Allegheny Technologies | Stainless Steel, Nickel Alloys | $70 – $250 per kg | North America, Europe |
Oerlikon Metco | Metal Powders (Various) | $80 – $220 per kg | Global |
Höganäs | Metal Powders (Various) | $90 – $230 per kg | Global |
Arcam AB | Titanium, Stainless Steel | $100 – $300 per kg | Global |
EOS GmbH | Metal Powders (Various) | $110 – $320 per kg | Global |
LPW Technology | Metal Powders (Various) | $120 – $340 per kg | Global |
Renishaw | Stainless Steel, Titanium | $130 – $360 per kg | Global |
Praxair Surface Technologies | Metal Powders (Various) | $140 – $380 per kg | Global |
These suppliers offer a range of metal powders used in multi-material structures, and their pricing varies based on material type and quantity.
Advantages and Limitations of Multi-Material Structures
While multi-material structures offer numerous benefits, they also come with certain limitations. Here’s a comparative look.
Advantages | Limitations |
---|---|
Enhanced mechanical properties | Complexity in manufacturing |
Lightweight designs | Higher production costs |
Improved corrosion resistance | Potential for galvanic corrosion |
Tailored thermal properties | Joining dissimilar materials |
Versatility in applications | Limited by material compatibility |
Increased product lifespan | Challenges in recycling |
Understanding these pros and cons can help engineers make informed decisions when designing multi-material structures.
Composition of Multi-Material Structures
The composition of multi-material structures is meticulously engineered to achieve specific performance characteristics. Let’s delve into the details.
Material Combination | Description |
---|---|
Aluminum and Carbon Fiber | Combines lightweight and high strength properties for aerospace applications. |
Titanium and PEEK | Merges biocompatibility with structural strength for medical implants. |
Stainless Steel and Polymer | Enhances corrosion resistance and flexibility for electronic enclosures. |
Copper and Graphite | Offers superior electrical conductivity and thermal management. |
Nickel Alloy and Ceramic | Provides high-temperature stability and wear resistance for industrial use. |
Magnesium and Glass Fiber | Lightweight and strong, ideal for automotive components. |
Cobalt Chrome and UHMWPE | Combines wear resistance with low friction for joint replacements. |
Tungsten and Aluminum Oxide | High density and thermal stability for radiation shielding. |
Tool Steel and Diamond | Offers extreme hardness and durability for cutting tools. |
Bronze and PTFE | Provides low friction and wear resistance for bearing applications. |
These combinations are carefully selected to exploit the best properties of each material, resulting in superior multi-material structures.
Specifications, Sizes, and Standards
Ensuring the right specifications and adherence to standards is crucial for the performance of multi-material structures. Here are some common specifications.
Specification | Size Range | Standard |
---|---|---|
Aluminum 6061 Sheet | 0.5mm to 200mm thickness | ASTM B209 |
Titanium Ti-6Al-4V Rod | 10mm to 150mm diameter | ASTM B348 |
Stainless Steel 316L Plate | 1mm to 100mm thickness | ASTM A240 |
Inconel 718 Bar | 5mm to 100mm diameter | AMS 5662 |
Copper C11000 Foil | 0.01mm to 2mm thickness | ASTM B152 |
Nickel 200 Wire | 0.1mm to 10mm diameter | ASTM B160 |
Cobalt Chrome Powder | 10µm to 150µm particle size | ASTM F75 |
Tungsten Sheet | 0.5mm to 50mm thickness | ASTM B777 |
Tool Steel H13 Block | 20mm to 300mm thickness | ASTM A681 |
Bronze CuSn12 Rod | 5mm to 200mm diameter | ASTM B505 |
These specifications ensure that multi-material structures meet the necessary quality and performance standards for their intended applications.
Comparing Multi-Material Structures
When choosing between different multi-material structures, it’s essential to compare their properties and performance. Here’s a comparison of some common options.
Material Combination | Strength | Weight | Corrosion Resistance | Thermal Stability | Electrical Conductivity | Cost |
---|---|---|---|---|---|---|
Aluminum and Carbon Fiber | High | Low | Moderate | High | Low | Medium |
Titanium and PEEK | Very High | Low | High | High | Low | High |
Stainless Steel and Polymer | Moderate | Moderate | Very High | Moderate | Moderate | Low |
Copper and Graphite | Low | High | Low | High | Very High | High |
Nickel Alloy and Ceramic | High | High | Very High | Very High | Low | Very High |
Magnesium and Glass Fiber | High | Very Low | Low | Moderate | Low | Medium |
Cobalt Chrome and UHMWPE | High | Moderate | Very High | High | Low | High |
Tungsten and Aluminum Oxide | Very High | Very High | High | Very High | Low | Very High |
Tool Steel and Diamond | Extremely High | High | High | High | Low | Very High |
Bronze and PTFE | Moderate | Moderate | Moderate | Low | Low | Medium |
This comparison helps identify the best material combination for specific requirements based on various performance metrics.
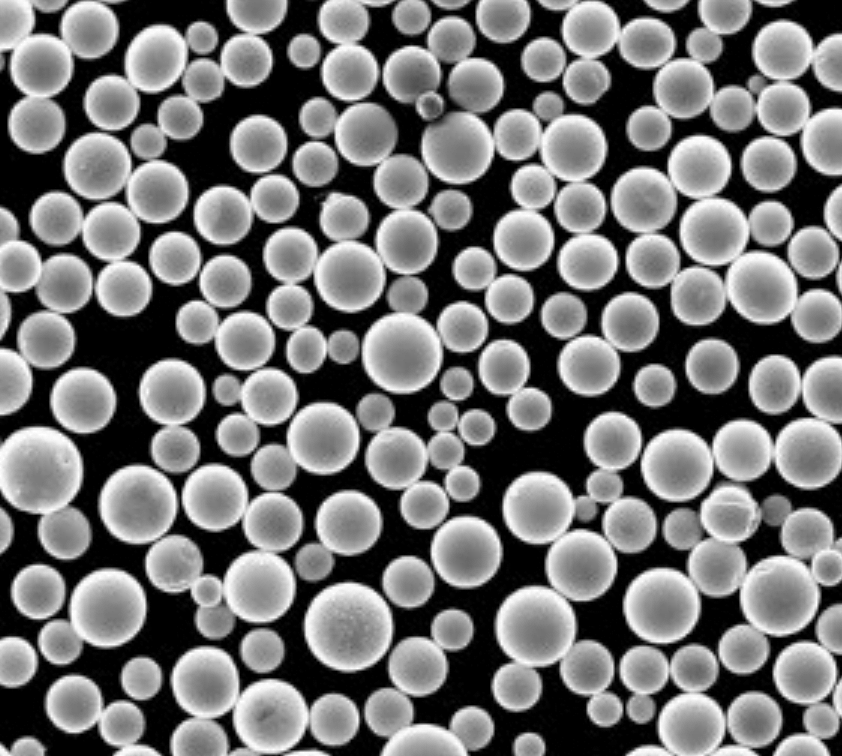
FAQs
Question | Answer |
---|---|
What are multi-material structures? | Structures made from two or more different materials to achieve superior properties. |
Why use multi-material structures? | They offer enhanced strength, reduced weight, and improved performance in various applications. |
What industries benefit from multi-material structures? | Aerospace, automotive, medical devices, electronics, and more. |
How are multi-material structures manufactured? | Techniques include additive manufacturing, welding, and adhesive bonding. |
What are the challenges in using multi-material structures? | Joining dissimilar materials and potential galvanic corrosion. |
Are multi-material structures recyclable? | Recycling can be challenging due to the different materials involved. |
What is the cost of multi-material structures? | Costs vary based on material combinations and manufacturing processes. |
Can multi-material structures be customized? | Yes, they can be tailored to meet specific performance requirements. |
What standards govern multi-material structures? | Standards include ASTM, AMS, and ISO depending on the materials and applications. |
How do multi-material structures compare to single-material structures? | They often provide better performance but can be more complex and costly to produce. |
About 3DP mETAL
Product Category
CONTACT US
Any questions? Send us a message now! After receiving your message, we will process your request with a whole team.