When you think of advanced materials, your mind might wander to the latest gadgets or high-tech innovations. But what about the raw materials that make these advancements possible? One such material that’s making waves in the engineering world is Nickel Aluminide Powder. So, let’s dive into the fascinating world of this powerhouse alloy.
Overview of Nickel Aluminide Powder
Nickel aluminide (NiAl) is a type of intermetallic compound known for its exceptional high-temperature strength and resistance to oxidation. It’s a material that combines the best of both worlds: the robustness of nickel and the lightweight characteristics of aluminum. The result? A high-performance powder that can withstand extreme conditions while maintaining structural integrity.
Why Nickel Aluminide Powder?
Nickel aluminide powder stands out due to its unique properties:
- High Melting Point: It retains its strength at temperatures where other materials would falter.
- Oxidation Resistance: This material is less likely to corrode, even when exposed to harsh environments.
- Lightweight: Despite its strength, it’s lighter than many other metals, making it ideal for applications where weight is a concern.
Types of Nickel Aluminide Powder
There are various types of Nickel Aluminide Powder, each with specific compositions and properties tailored for different applications. Here are some of the most notable ones:
Type | Composition | Properties | Applications |
---|---|---|---|
NiAl | Nickel (50%), Aluminum (50%) | High-temperature strength, oxidation resistance | Aerospace components, turbine blades |
Ni3Al | Nickel (75%), Aluminum (25%) | Superior mechanical properties, ductility | High-performance coatings, electrical contacts |
NiAl + Cr | Nickel (40-50%), Aluminum (40-50%), Chromium (10%) | Enhanced corrosion resistance, durability | Industrial gas turbines, jet engines |
NiAl + Mo | Nickel (40-50%), Aluminum (40-50%), Molybdenum (5-10%) | Improved wear resistance, hardness | Cutting tools, wear-resistant coatings |
NiAl + B | Nickel (40-50%), Aluminum (40-50%), Boron (trace amounts) | Grain refinement, increased strength | Structural components, automotive parts |
NiAl + Ti | Nickel (40-50%), Aluminum (40-50%), Titanium (5-10%) | High-temperature stability, toughness | Aerospace fasteners, high-stress components |
NiAl + Hf | Nickel (40-50%), Aluminum (40-50%), Hafnium (5-10%) | Enhanced creep resistance, stability | Turbine disks, high-temperature applications |
NiAl + W | Nickel (40-50%), Aluminum (40-50%), Tungsten (5-10%) | Increased density, thermal stability | Rocket nozzles, heat shields |
NiAl + SiC | Nickel (40-50%), Aluminum (40-50%), Silicon Carbide (10-15%) | High stiffness, reduced thermal expansion | High-precision machinery, electronic packaging |
NiAl + Y2O3 | Nickel (40-50%), Aluminum (40-50%), Yttrium Oxide (5-10%) | Enhanced oxidation resistance, longevity | High-temperature coatings, industrial catalysts |
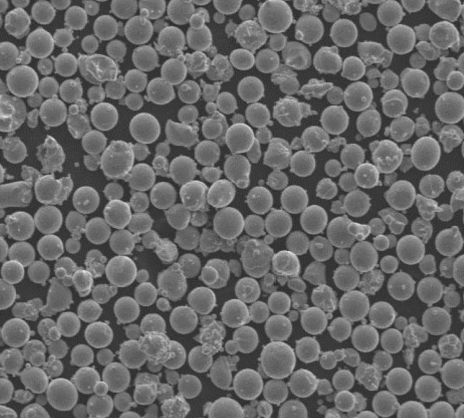
Applications of Nickel Aluminide Powder
Nickel aluminide powder is a game-changer across numerous industries due to its versatility and superior properties. Here’s a closer look at where and how it’s being used:
Application | Details |
---|---|
Aerospace | Used in turbine blades, engine components, and structural parts due to its high strength-to-weight ratio and resistance to extreme temperatures. |
Automotive | Ideal for high-stress components, improving fuel efficiency and performance. |
Industrial Gas Turbines | Enhances the efficiency and longevity of turbines, reducing maintenance costs. |
Electronics | Utilized in high-performance coatings and electrical contacts, ensuring durability and reliability. |
Medical Devices | Provides wear-resistant and biocompatible coatings for implants and surgical tools. |
Cutting Tools | Offers improved wear resistance and hardness, extending the tool life. |
Power Generation | Used in components that require high-temperature stability and oxidation resistance. |
Construction Machinery | Provides strength and durability for heavy-duty applications. |
High-Precision Machinery | Reduces thermal expansion, ensuring accuracy and stability in sensitive equipment. |
Rocket Nozzles and Heat Shields | Withstands extreme thermal and mechanical stress, essential for space applications. |
Specifications, Sizes, Grades, Standards
Choosing the right Nickel Aluminide Powder involves understanding its specifications, sizes, grades, and standards. Here’s a detailed look at these factors:
Specification | Details |
---|---|
Particle Size | Ranges from 5 micrometers to 50 micrometers, depending on the application. |
Purity | Typically above 99.5%, ensuring high performance and consistency. |
Grades | Varies based on the alloying elements and their concentrations. |
Standards | Conforms to industry standards such as ASTM, ISO, and AMS for quality and reliability. |
Suppliers and Pricing Details
Finding the right supplier for Nickel Aluminide Powder is crucial for ensuring quality and performance. Here are some key suppliers and their pricing details:
Supplier | Location | Pricing | Specialization |
---|---|---|---|
Advanced Powder Tech | USA | $500 – $700 per kg | High-purity powders for aerospace and industrial applications. |
Metal Powder Co. | Germany | €450 – €650 per kg | Custom alloy formulations and large-scale production. |
Powder Metallurgy Ltd. | UK | £400 – £600 per kg | Specialized in high-performance coatings and electronics. |
Asia Metals | China | $450 – $600 per kg | Competitive pricing with a focus on automotive and medical industries. |
Euro Powder Works | EU | €500 – €750 per kg | High-precision powders for aerospace and high-precision machinery. |
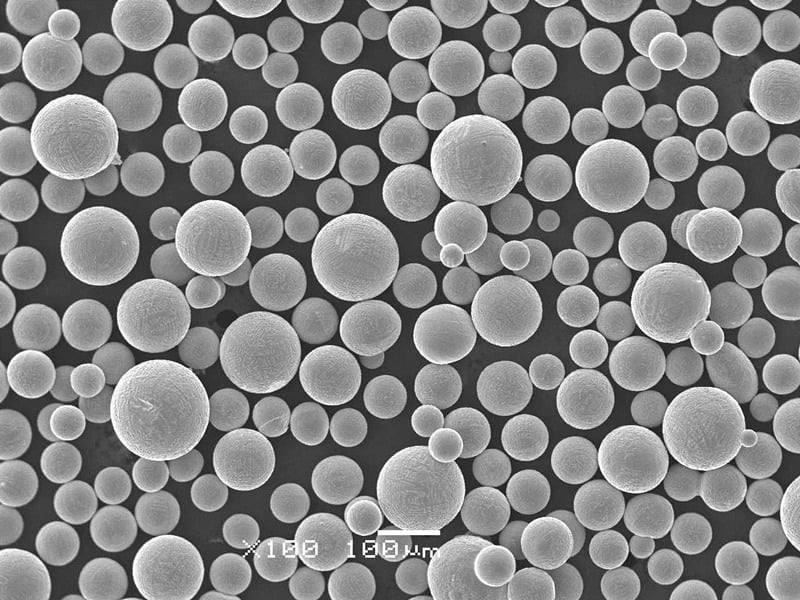
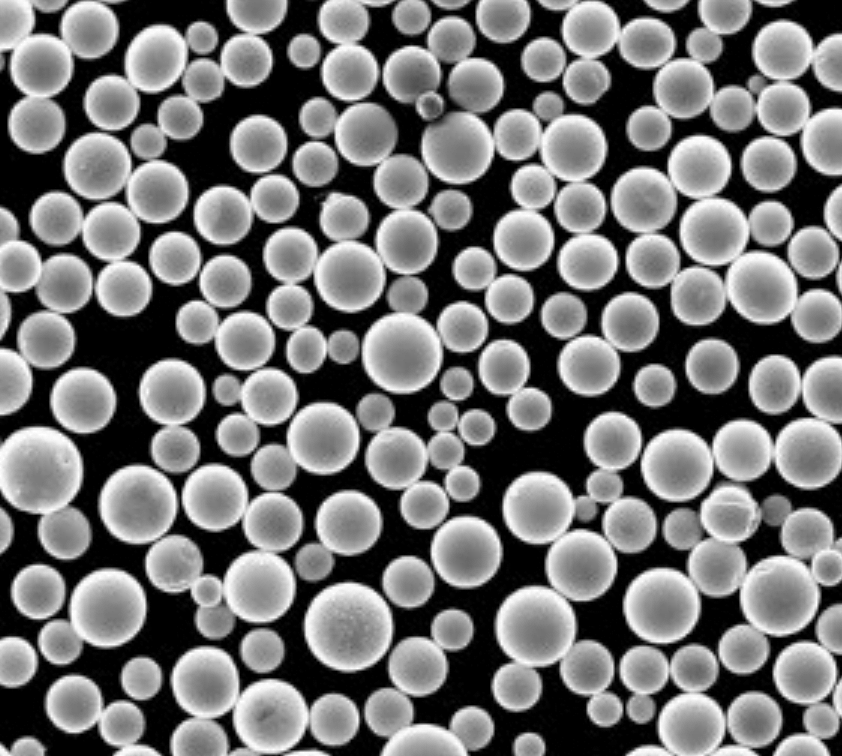
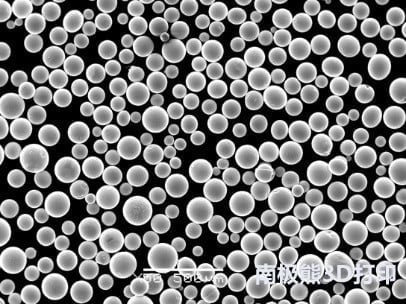
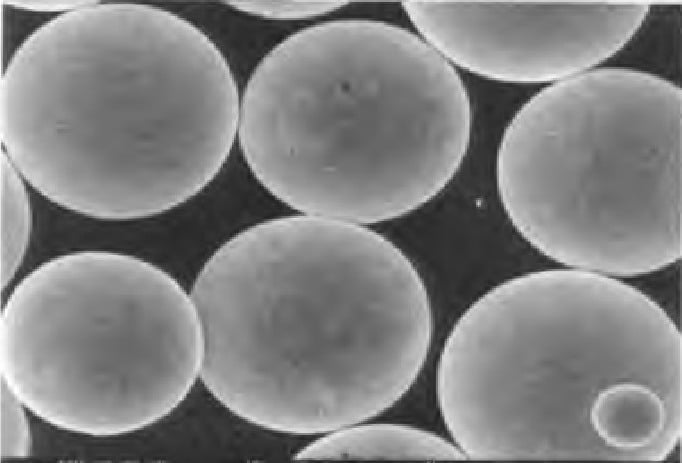
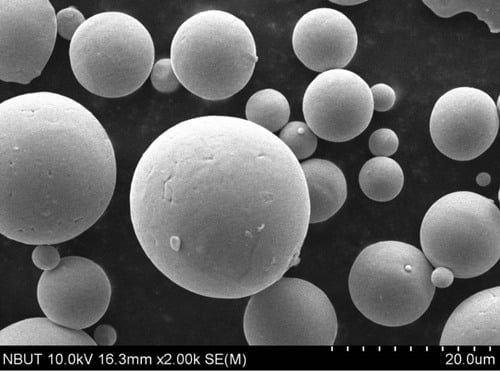
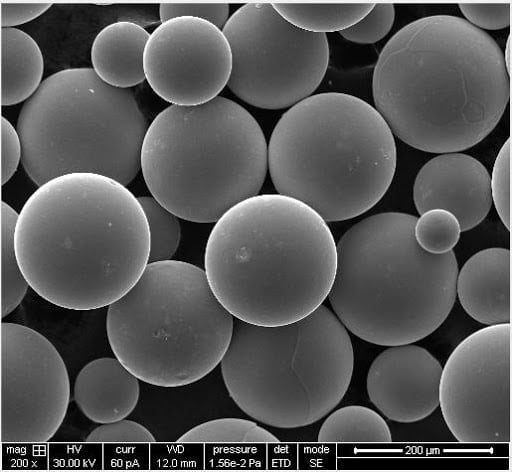
Advantages and Disadvantages of Nickel Aluminide Powder
Nickel Aluminide Powder offers numerous benefits, but it’s not without its drawbacks. Let’s compare the pros and cons:
Aspect | Advantages | Disadvantages |
---|---|---|
Strength | High strength-to-weight ratio, excellent high-temperature strength | Can be brittle in certain conditions, requires careful handling |
Oxidation Resistance | Exceptional resistance to oxidation and corrosion | High cost compared to some traditional materials |
Weight | Lightweight, ideal for aerospace and automotive applications | Limited ductility in some alloy compositions |
Thermal Stability | Maintains properties at high temperatures | Complex manufacturing process, requiring specialized equipment |
Wear Resistance | High hardness and wear resistance | May require alloying with other elements to optimize properties |
Versatility | Suitable for various industries and applications | May not be the best choice for applications requiring high ductility |
In-Depth Look: Specific Nickel Aluminide Powder Models
Understanding specific models of Nickel Aluminide Powder can help you make an informed decision. Here are detailed descriptions of ten notable models:
1. NiAl Model 101
Composition: Nickel (50%), Aluminum (50%)
Properties: Basic nickel aluminide with excellent high-temperature strength and oxidation resistance.
Applications: Turbine blades, aerospace components.
2. Ni3Al Model 202
Composition: Nickel (75%), Aluminum (25%)
Properties: Superior mechanical properties and ductility.
Applications: High-performance coatings, electrical contacts.
3. NiAl + Cr Model 303
Composition: Nickel (40-50%), Aluminum (40-50%), Chromium (10%)
Properties: Enhanced corrosion resistance and durability.
Applications: Industrial gas turbines, jet engines.
4. NiAl + Mo Model 404
Composition: Nickel (40-50%), Aluminum (40-50%), Molybdenum (5-10%)
Properties: Improved wear resistance and hardness.
Applications: Cutting tools, wear-resistant coatings.
5. NiAl + B Model 505
Composition: Nickel (40-50%), Aluminum (40-50%), Boron (trace amounts)
Properties: Grain refinement, increased strength.
Applications: Structural components, automotive parts.
6. NiAl + Ti Model 606
Composition: Nickel (40-50%), Aluminum (40-50%), Titanium (5-10%)
Properties: High-temperature stability and toughness.
Applications: Aerospace fasteners, high-stress components.
7. NiAl + Hf Model 707
Composition: Nickel (40-50%), Aluminum (40-50%), Hafnium (5-10%)
Properties: Enhanced creep resistance and stability.
Applications: Turbine disks, high-temperature applications.
8. NiAl + W Model 808
Composition: Nickel (40-50%), Aluminum (40-50%), Tungsten (5-
10%)
Properties: Increased density and thermal stability.
Applications: Rocket nozzles, heat shields.
9. NiAl + SiC Model 909
Composition: Nickel (40-50%), Aluminum (40-50%), Silicon Carbide (10-15%)
Properties: High stiffness and reduced thermal expansion.
Applications: High-precision machinery, electronic packaging.
10. NiAl + Y2O3 Model 1010
Composition: Nickel (40-50%), Aluminum (40-50%), Yttrium Oxide (5-10%)
Properties: Enhanced oxidation resistance and longevity.
Applications: High-temperature coatings, industrial catalysts.
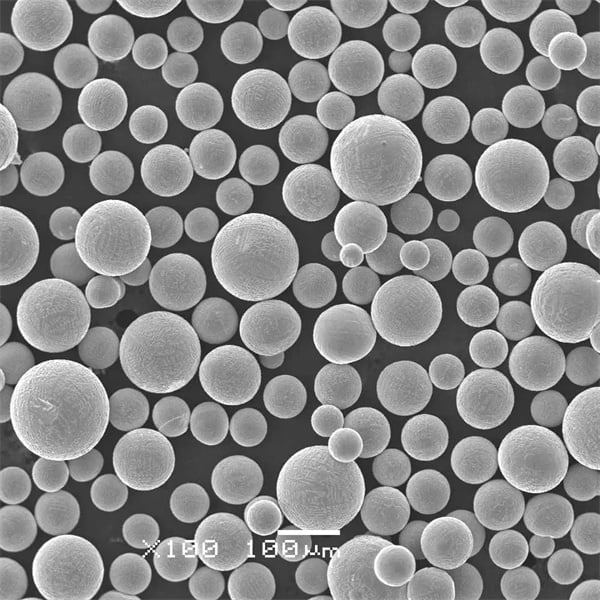
FAQ
Here’s a handy FAQ section to address common questions about Nickel Aluminide Powder:
Question | Answer |
---|---|
What is Nickel Aluminide Powder? | It’s an intermetallic compound combining nickel and aluminum, known for its high-temperature strength and oxidation resistance. |
Where is it used? | It finds applications in aerospace, automotive, industrial gas turbines, electronics, medical devices, and more. |
What are its key properties? | High melting point, lightweight, excellent oxidation resistance, and high strength-to-weight ratio. |
How is it manufactured? | Typically through advanced powder metallurgy techniques, ensuring high purity and consistency. |
What are the common alloying elements? | Chromium, molybdenum, boron, titanium, hafnium, tungsten, silicon carbide, and yttrium oxide. |
How do I choose the right grade? | Consider the specific application requirements, such as temperature resistance, mechanical strength, and environmental conditions. |
Is it expensive? | Generally more costly than traditional materials, but its performance benefits often justify the price. |
Can it be customized? | Yes, different compositions can be tailored to meet specific needs and applications. |
What are the limitations? | Brittle under certain conditions, high cost, and complex manufacturing process. |
Why is it preferred in aerospace? | Its high strength-to-weight ratio and ability to withstand extreme temperatures make it ideal for aerospace applications. |
Conclusion
Nickel Aluminide Powder is a revolutionary material that bridges the gap between traditional metals and high-performance demands of modern industries. From its various types and compositions to its wide range of applications, it stands out as a robust, versatile, and essential component in cutting-edge technology. Whether you’re in aerospace, automotive, or any field that demands top-tier materials, Nickel Aluminide Powder is a contender worth considering.
About 3DP mETAL
Product Category
CONTACT US
Any questions? Send us a message now! After receiving your message, we will process your request with a whole team.