Overview
Plasma quality powders are essential materials in various advanced manufacturing processes, particularly in additive manufacturing and coating applications. These powders are known for their high purity, excellent flowability, and consistent particle size distribution, making them ideal for producing high-quality parts with superior mechanical properties. In this comprehensive guide, we’ll dive deep into the world of plasma quality powders, exploring different models, their compositions, properties, applications, and much more.
Composition of Plasma Quality Powder
Plasma quality powders are composed of various metals and alloys, each offering unique properties and advantages. Here’s a detailed table summarizing the composition of some popular metal powder models:
Metal Powder Model | Composition | Description |
---|---|---|
Ti-6Al-4V | Ti (90%), Al (6%), V (4%) | Titanium alloy known for high strength, low density, and excellent corrosion resistance. |
316L Stainless Steel | Fe (70%), Cr (17%), Ni (12%), Mo (2%) | A low-carbon stainless steel offering excellent corrosion resistance and good mechanical properties. |
Inconel 718 | Ni (50-55%), Cr (17-21%), Fe (balance), Mo (2.8-3.3%) | Nickel-based superalloy with high strength and oxidation resistance at elevated temperatures. |
CoCrMo | Co (60-65%), Cr (27-30%), Mo (5-7%) | Cobalt-chromium-molybdenum alloy known for high wear resistance and biocompatibility. |
AlSi10Mg | Al (85-90%), Si (9-11%), Mg (0.2-0.5%) | Aluminum alloy with good strength, lightweight, and excellent casting properties. |
CuNi2SiCr | Cu (balance), Ni (2%), Si (1%), Cr (0.2%) | Copper-nickel-silicon-chromium alloy with high electrical conductivity and good mechanical strength. |
Maraging Steel (18Ni-300) | Fe (70-75%), Ni (18%), Co (8-12%), Mo (4-5%) | High-strength steel alloy with excellent toughness and weldability. |
Hastelloy X | Ni (47-52%), Cr (20-23%), Fe (17-20%), Mo (8-10%) | Nickel-chromium-iron-molybdenum alloy with high temperature strength and oxidation resistance. |
Tool Steel H13 | Fe (90%), Cr (5%), Mo (1.5%), V (1%), C (1%) | High-carbon steel known for excellent toughness and resistance to thermal fatigue. |
Niobium C-103 | Nb (89-95%), Hf (8-10%), Ti (2%) | Niobium-based alloy with high melting point and excellent corrosion resistance. |
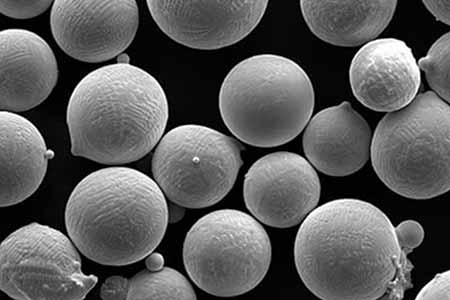
Characteristics of Plasma Quality Powder
Plasma quality powders boast a range of characteristics that make them suitable for high-performance applications. Here’s a closer look at these properties:
Property | Description |
---|---|
High Purity | Minimal impurities ensure consistent material performance and quality. |
Excellent Flowability | Smooth and consistent powder flow during manufacturing processes, reducing defects. |
Uniform Particle Size | Ensures uniform layer deposition and consistent mechanical properties in the final product. |
High Sphericity | Spherical particles promote better packing density and flow characteristics. |
Low Oxygen Content | Reduces oxidation and improves material properties and performance. |
Controlled Composition | Precise alloying elements lead to predictable and repeatable material behavior. |
Applications of Plasma Quality Powder
Plasma quality powders are used in a variety of high-tech applications due to their superior properties. Here’s a detailed table showcasing some common applications:
Application | Description |
---|---|
Additive Manufacturing (3D Printing) | Producing complex, high-performance parts with excellent mechanical properties and surface finish. |
Thermal Spray Coatings | Providing wear resistance, corrosion protection, and thermal barrier properties to various surfaces. |
Biomedical Implants | Manufacturing biocompatible implants with high strength and corrosion resistance. |
Aerospace Components | Creating lightweight, high-strength parts for aircraft and spacecraft. |
Automotive Industry | Producing durable and lightweight components for engines, transmissions, and other critical parts. |
Energy Sector | Fabricating parts for power generation, including turbine blades and heat exchangers. |
Tooling and Molds | Manufacturing durable tools and molds with high wear resistance. |
Electronic Devices | Creating components with high electrical conductivity and thermal stability. |
Defense and Military | Producing high-strength, corrosion-resistant parts for military applications. |
Jewelry and Fashion | Crafting intricate, high-quality pieces with unique material properties. |
Specifications, Sizes, Grades, and Standards
Plasma quality powders come in various specifications, sizes, grades, and standards to meet different application requirements. Here’s a detailed table summarizing these aspects:
Metal Powder Model | Size Range (µm) | Grade | Standard |
---|---|---|---|
Ti-6Al-4V | 15-45 | Grade 23 | ASTM F2924 |
316L Stainless Steel | 15-45 | Grade 316L | ASTM A240 |
Inconel 718 | 15-45 | Grade 718 | ASTM B637 |
CoCrMo | 15-45 | Grade F75 | ASTM F1537 |
AlSi10Mg | 20-63 | Grade 10 | EN 1706 |
CuNi2SiCr | 20-63 | Grade 1 | ASTM B422 |
Maraging Steel (18Ni-300) | 15-45 | Grade 300 | AMS 6514 |
Hastelloy X | 15-45 | Grade X | ASTM B435 |
Tool Steel H13 | 15-53 | Grade H13 | ASTM A681 |
Niobium C-103 | 20-63 | Grade C-103 | AMS 7852 |
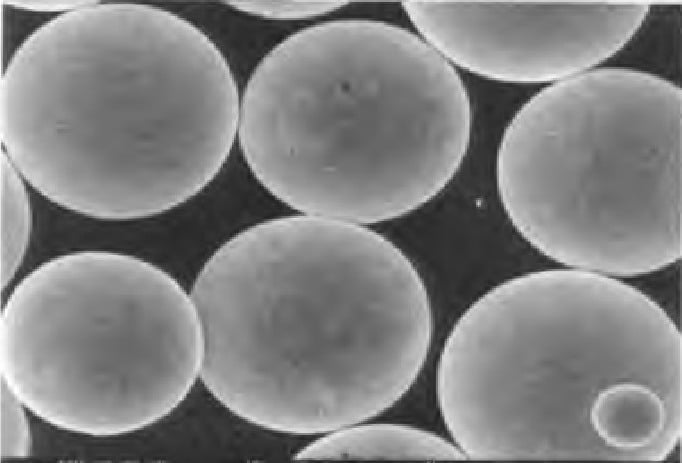
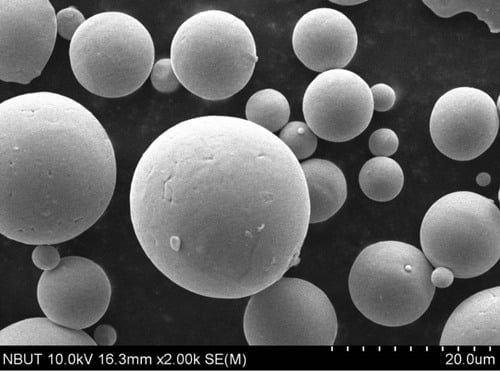
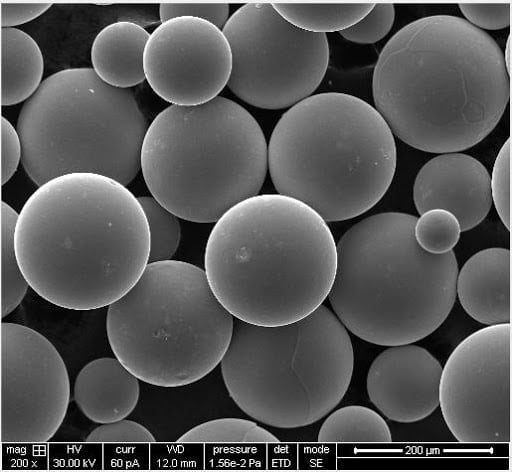
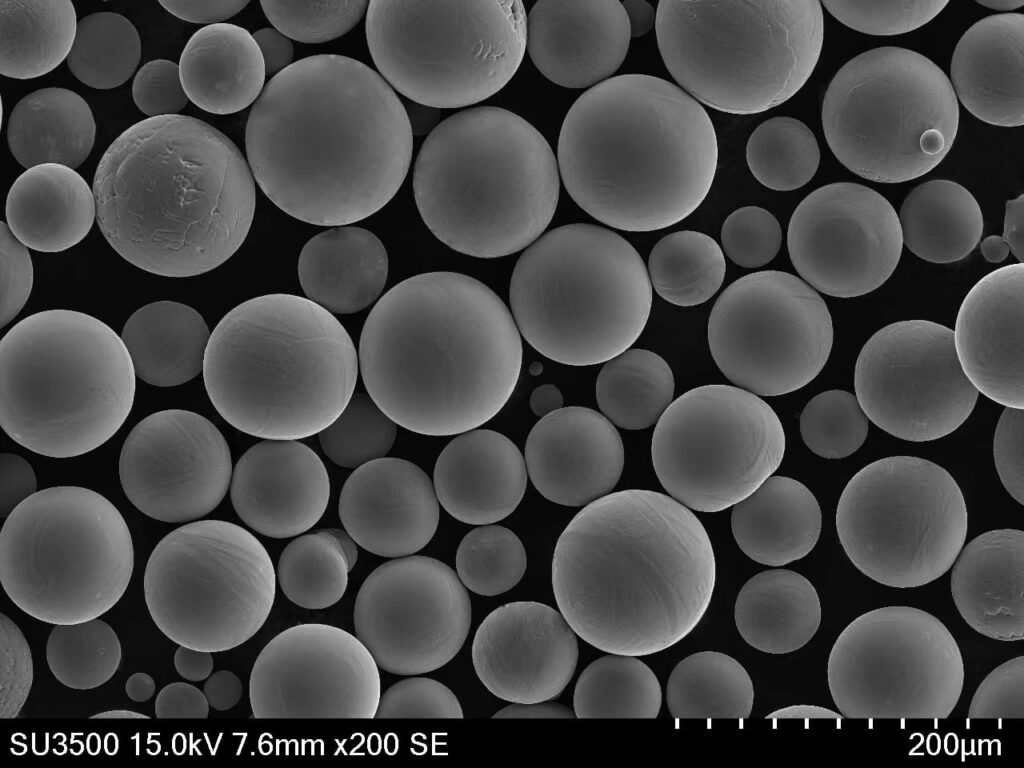
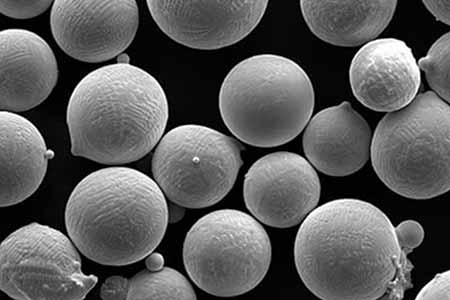
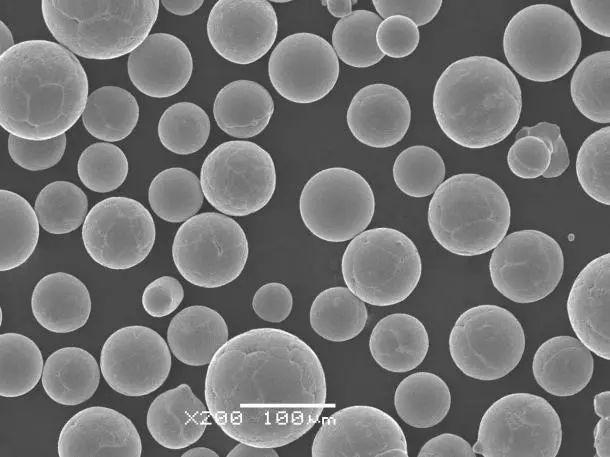
Suppliers and Pricing Details
When it comes to sourcing plasma quality powders, several reputable suppliers offer a range of options. Here’s a table with some notable suppliers and their pricing details:
Supplier | Metal Powder Model | Price (USD/kg) | Minimum Order Quantity (kg) |
---|---|---|---|
Carpenter Technology | Ti-6Al-4V | $400 | 10 |
Höganäs | 316L Stainless Steel | $150 | 5 |
Sandvik | Inconel 718 | $300 | 10 |
Arcam AB | CoCrMo | $250 | 5 |
GKN Hoeganaes | AlSi10Mg | $100 | 20 |
HC Starck | CuNi2SiCr | $200 | 5 |
LPW Technology | Maraging Steel (18Ni-300) | $350 | 10 |
Oerlikon Metco | Hastelloy X | $400 | 5 |
Bodycote | Tool Steel H13 | $200 | 10 |
Metalysis | Niobium C-103 | $500 | 5 |
Pros and Cons of Plasma Quality Powder
When choosing plasma quality powders for various applications, it’s essential to weigh the advantages and limitations. Here’s a table comparing the pros and cons of these powders:
Pros | Cons |
---|---|
High purity and consistent quality | Higher cost compared to other powders |
Excellent mechanical properties | Limited availability for some specific alloys |
Superior flowability and packing density | Requires specialized handling and storage |
Low oxygen content reduces oxidation | Sensitivity to moisture and contamination |
Wide range of compositions and alloys | Some powders may require post-processing |
Suitable for high-performance applications | Complex manufacturing process for some powders |
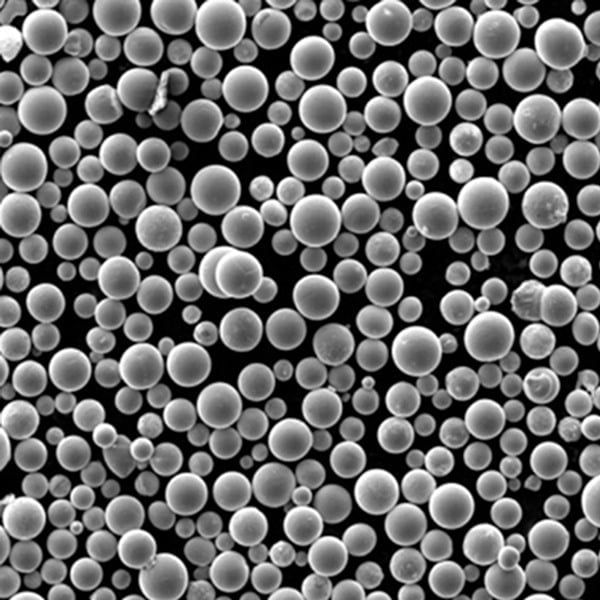
FAQs
What are plasma quality powders used for?
Plasma quality powders are used in a variety of applications, including additive manufacturing, thermal spray coatings, biomedical implants, aerospace components, automotive parts, energy sector components, tooling, electronic devices, defense applications, and even jewelry.
What is plasma quality powder?
Plasma quality powder is a specific type of metal or ceramic powder used in thermal spraying. Thermal spraying is a process that uses a plasma torch to melt and spray these powders onto a surface, creating a coating with desired properties like wear resistance, corrosion resistance, or thermal insulation.
What makes a good plasma quality powder?
Several factors contribute to a high-quality thermal spray powder:
- Chemistry: The powder’s exact composition plays a crucial role in the final coating’s properties. Manufacturers may offer powders with specific chemistries depending on the application.
- Particle size and distribution: Consistent particle size and distribution ensure proper melting, deposition efficiency, and coating quality.
- Particle shape: The shape of the powder particles can influence the flowability, packing density, and splat morphology (shape of the deposited material) in the coating.
- Flowability: Powders need to flow freely for proper feeding into the thermal spray equipment.
How does plasma quality powder differ from other types of metal powders?
Plasma quality powders are often finer and more precisely sized compared to welding powders or powders for additive manufacturing. They might also have tighter chemistry control to achieve specific properties in the final coating.
Where can I find information on specific plasma quality powders?
Reputable powder manufacturers typically provide detailed data sheets for their products. These data sheets will include information on the powder’s chemistry, particle size distribution, morphology, and other relevant specifications.
What are some factors to consider when choosing a plasma quality powder?
- Desired coating properties: What properties do you need the coating to have (e.g., wear resistance, corrosion resistance, thermal conductivity)?
- Substrate material: The type of material being coated will influence compatible powder selection.
- Thermal spray process: Different thermal spray processes may require powders with specific characteristics.
- Cost: Plasma quality powders can vary in price depending on the material, chemistry, and production method.
About 3DP mETAL
Product Category
CONTACT US
Any questions? Send us a message now! After receiving your message, we will process your request with a whole team.