Imagine a world where metal can be transformed into tiny, perfect spheres – the building blocks for revolutionary technologies like 3D printing. This world is not science fiction, and the process behind it is called the Plasma Rotating Electrode Process, or PREP for short. Buckle up, because we’re about to embark on a journey into the heart of this fascinating technology.
Characteristics of the Plasma Rotating Electrode Process
PREP is a method for creating high-quality metal powders. But what makes it special? Here are some key characteristics that set it apart:
- Spherical Powders: PREP excels at producing near-perfect spheres. This is crucial for 3D printing, as these uniform shapes flow smoothly during the printing process, leading to better quality final products.
- High Purity: The entire process occurs within an inert gas environment, minimizing contamination with oxygen or other unwanted elements. This translates to stronger, more reliable metal parts.
- Tailored Properties: By tweaking various parameters in the process, manufacturers can control the size, morphology, and even the internal structure of the powder particles. This allows for fine-tuning the properties of the final product.
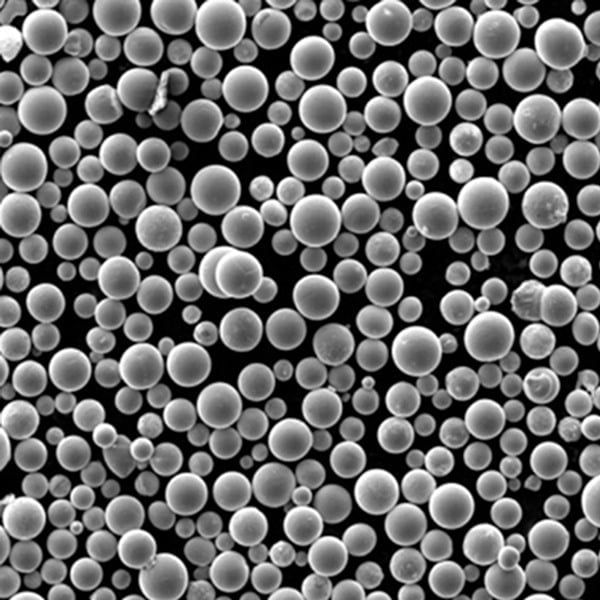
The Process Flow of Plasma Rotating Electrode Process
Now, let’s delve into the captivating dance that occurs within a PREP system:
- The Stage is Set: The raw material, typically a metal rod, is secured onto a rapidly spinning spindle. Imagine a potter’s wheel on overdrive, but instead of clay, we have a metal bar ready to be transformed.
- Plasma Takes Center Stage: A plasma torch, a tool that generates intensely hot, ionized gas, is directed at the rotating rod. Think of it as a super-powered blowtorch that melts metal with ease.
- Centrifugal Force Takes Over: As the rod spins at high speeds (think thousands of revolutions per minute!), the molten metal experiences a powerful centrifugal force. Imagine a kid swinging a ball on a string – the faster they spin, the harder it is to hold onto the ball. In PREP, this force flings tiny droplets of molten metal outwards.
- Solidification Symphony: These molten droplets rapidly cool and solidify into perfect spheres as they travel through the inert gas chamber. It’s like watching raindrops solidify mid-air, only these drops are made of molten metal!
- Curtain Call – Collection and Inspection: The finished metal powder is collected, and its size, shape, and purity are meticulously inspected to ensure it meets the desired specifications.
The Application Areas of Plasma Rotating Electrode Process
PREP’s ability to produce high-quality metal powders unlocks a treasure trove of applications:
- Additive Manufacturing (3D Printing): As mentioned earlier, PREP powders are ideal for 3D printing. They flow smoothly, create strong bonds, and can be used to print complex metal objects for aerospace, automotive, and medical industries.
- Metal Injection Molding (MIM): PREP powders are also instrumental in MIM, where metal powder is mixed with a binder to create a moldable feedstock. This allows for the creation of intricate metal parts with high precision.
- Thermal Spraying: PREP powders can be used to coat surfaces with a layer of metal. This technique improves wear resistance, corrosion resistance, and thermal properties, making it valuable for components in power plants, turbines, and engines.
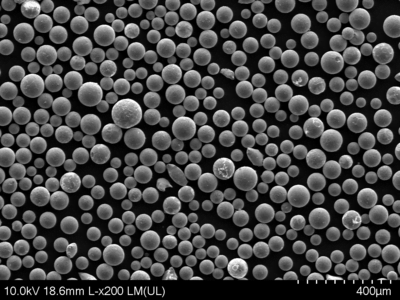
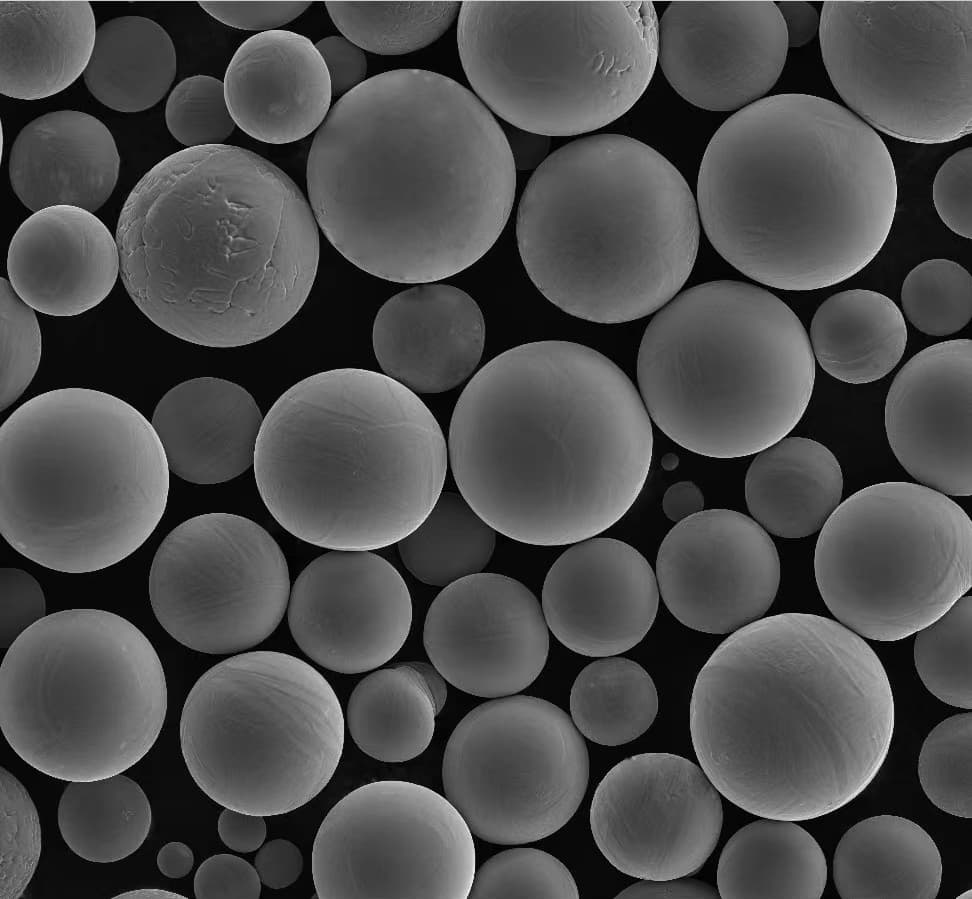
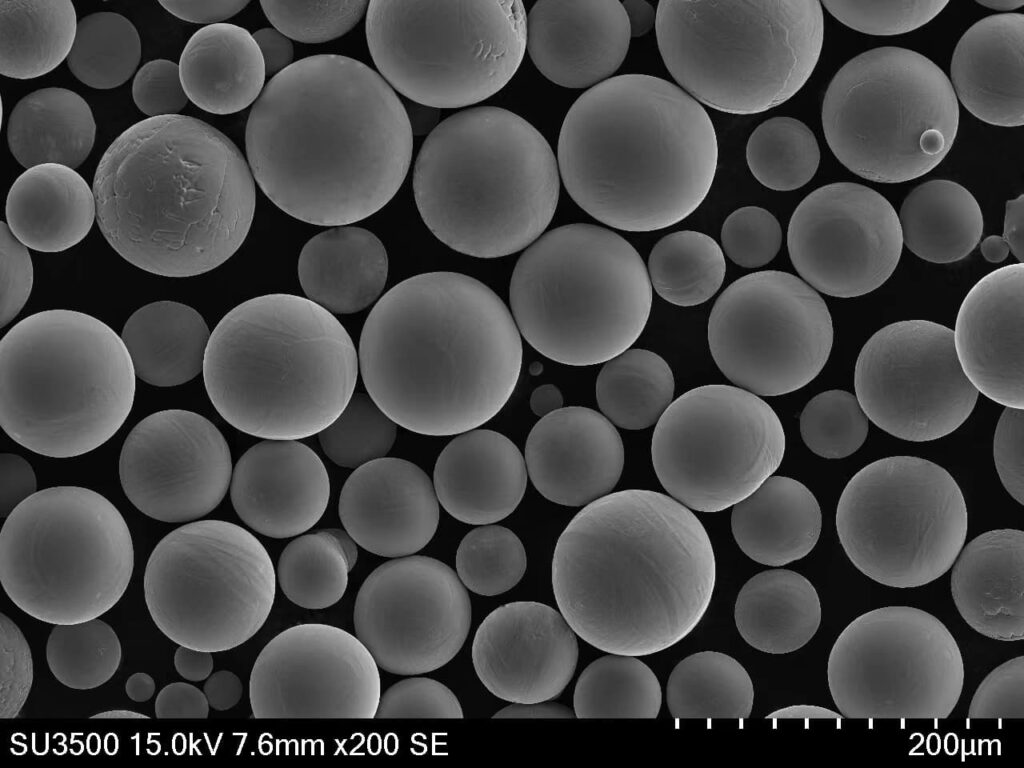
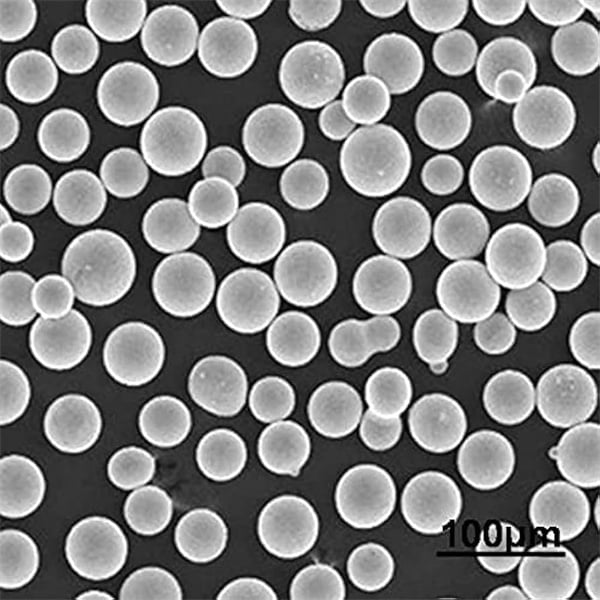
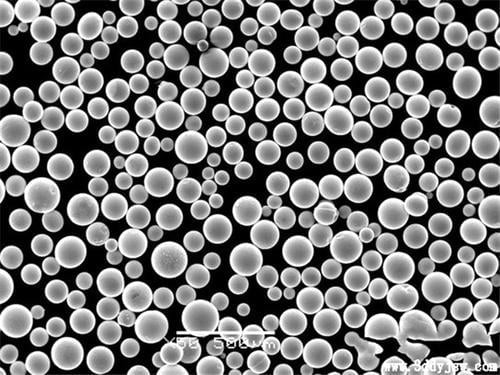
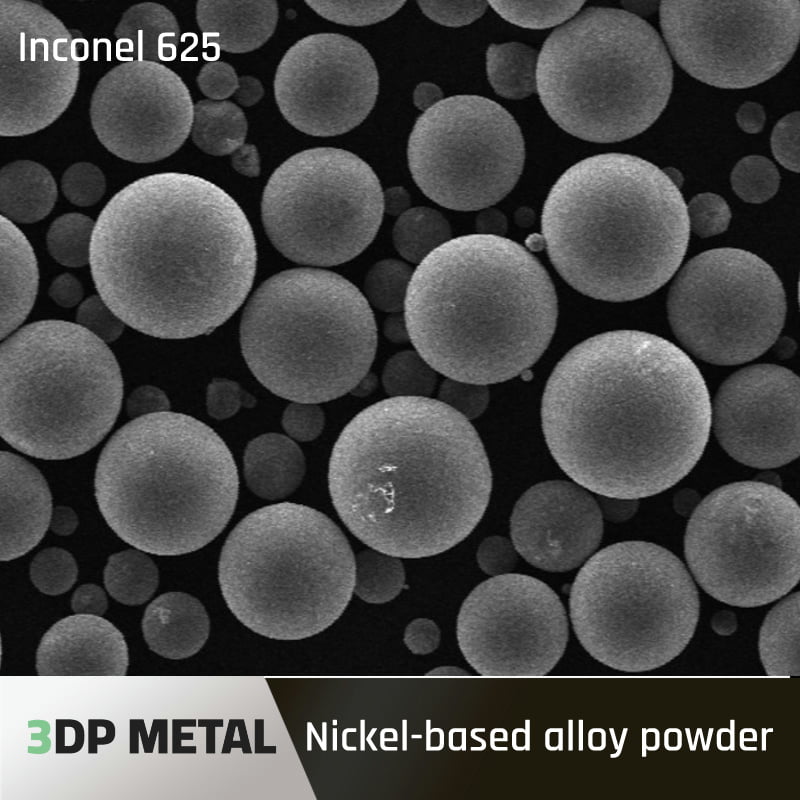
Advantages and Considerations of PREP
PREP boasts several advantages:
- High-Quality Powders: The near-perfect spherical shape and minimized contamination lead to superior quality metal parts when compared to other powder production methods.
- Wide Material Compatibility: PREP can handle a vast array of metals, from common ones like aluminum and titanium to more exotic materials like nickel superalloys. This versatility opens doors for innovative applications.
However, there are also some considerations:
- Complexity: Setting up and operating a PREP system requires specialized equipment and expertise. It’s not a simple process for a home workshop!
- Cost: PREP systems can be expensive to set up and maintain. This can translate into higher costs for the resulting powders compared to some simpler methods.
Advantages and Considerations of PREP
Comparison with Other Metal Powder Production Methods
While PREP excels in specific areas, it’s valuable to understand how it stacks up against other methods for creating metal powders:
- Atomization: This broad category encompasses various techniques, including gas atomization and water atomization. Both involve molten metal being broken up into droplets through a pressurized gas or water stream. Compared to PREP: Atomization can be a less expensive and more straightforward process. However, the resulting powders may have less consistent shapes and potentially higher levels of internal porosity (tiny air bubbles trapped within the particles). This can impact the final product’s strength and performance.
- Electrodeposition: This method involves using electricity to deposit metal ions onto a cathode (a negatively charged electrode). Compared to PREP: Electrodeposition offers high control over the size and morphology of the particles. However, it’s typically limited to producing powders of specific metals and often results in more irregularly shaped particles compared to PREP’s near-perfect spheres.
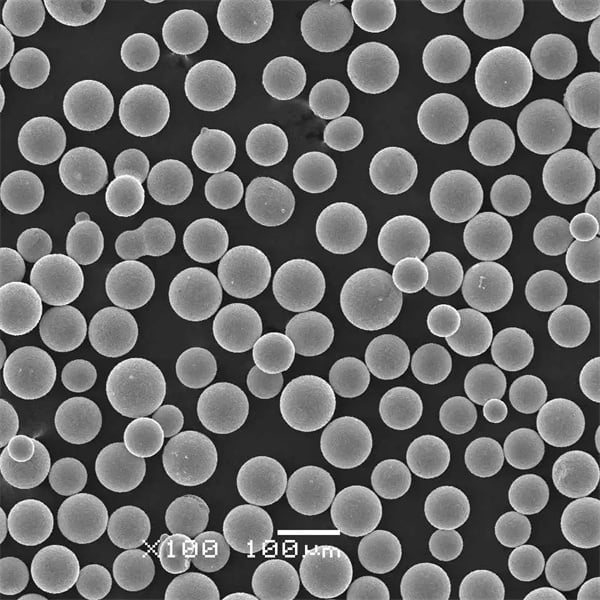
The Future of PREP
The future of PREP is bright! Researchers are constantly innovating and improving the process. Here are some exciting trends to watch:
- Increased Efficiency: Optimizing equipment and process parameters will lead to faster production times and lower costs, making PREP powders more accessible.
- Nanoparticle Production: The ability to produce even smaller, nanoscale powders using PREP could open doors for entirely new applications in areas like electronics and bioprinting.
- Novel Materials: Exploring the use of PREP with new and exotic materials could unlock possibilities for groundbreaking technologies in fields like aerospace and energy generation.
FAQ
Here’s a breakdown of some frequently asked questions about PREP:
Question | Answer |
---|---|
What are the size ranges of powders produced by PREP? | PREP offers a high degree of control over particle size. The process can typically produce powders with a wide range ranging from 10 microns (about the width of a red blood cell) to several hundred microns (roughly the thickness of a human hair). |
Can PREP be used to create alloys? | Absolutely! By feeding a rod made from a pre-alloyed material into the system, PREP can create metal powders with a specific and consistent composition. This allows for the creation of high-performance alloy parts through techniques like 3D printing and metal injection molding. |
How does PREP compare to other metal powder production methods? | PREP has its own set of advantages and disadvantages compared to other methods: |
Conclusion
The Plasma Rotating Electrode Process is a fascinating and powerful tool for creating high-quality metal powders. While it has its complexities and considerations, PREP’s ability to produce near-perfect spheres with minimal impurities positions it as a key player in the future of additive manufacturing, metal injection molding, and other advanced applications. As research and development continue, PREP promises to be at the forefront of shaping the metallic world of tomorrow.
About 3DP mETAL
Product Category
CONTACT US
Any questions? Send us a message now! After receiving your message, we will process your request with a whole team.