Overview of Preparing High Purity Powders
When it comes to manufacturing high-tech materials and advanced engineering products, the importance of high purity powders cannot be overstated. These powders serve as foundational components in various industries, from electronics to aerospace, where precision, consistency, and quality are paramount. But what exactly are high purity powders? How are they prepared, and why are they so crucial?
High purity powders are finely ground particles of metals, alloys, or ceramics that possess a high degree of chemical purity, typically 99.9% or higher. The preparation of these powders involves meticulous processes designed to eliminate impurities and achieve uniform particle sizes. The result is a material that meets stringent industry standards and ensures the reliability and performance of the end product.
In this comprehensive guide, we’ll delve into the intricacies of preparing high purity powders, exploring the different methods, materials, and applications. We’ll also discuss the specific metal powder models available, their compositions, properties, and use cases. Whether you’re an engineer, a manufacturer, or simply curious about the science behind these materials, this article will provide you with the insights you need.
Understanding High Purity Metal Powders
What Are High Purity Powders?
High purity powders are specialized materials with exceptional levels of chemical purity. They are typically produced from metals, ceramics, or alloys and are essential in applications where even the slightest contamination can lead to significant performance issues. These powders are used in a wide range of industries, including:
- Electronics: For manufacturing semiconductors, capacitors, and other electronic components.
- Aerospace: In the production of lightweight, high-strength materials for aircraft and spacecraft.
- Medical Devices: For creating biocompatible implants and other medical equipment.
- 3D Printing: As feedstock for additive manufacturing processes that require precise material properties.
Why Is Purity So Important?
Purity in metal powders is crucial because impurities can negatively affect the material’s performance. For example, in electronics, impurities can lead to electrical conductivity issues, while in aerospace, they can compromise the strength and durability of the material. High purity ensures that the material performs as expected, providing reliability and consistency in critical applications.
Common Methods for Preparing High Purity Powders
1. Atomization
Atomization is one of the most widely used methods for producing metal powders. It involves breaking up molten metal into fine droplets, which then solidify into powder particles. There are several types of atomization processes:
- Gas Atomization: Involves using a high-pressure gas to disintegrate molten metal.
- Water Atomization: Uses high-pressure water jets to break up molten metal.
- Centrifugal Atomization: Employs centrifugal forces to create fine powder particles.
Advantages: Produces spherical particles with good flowability and is suitable for a wide range of metals and alloys.
Disadvantages: Can be costly due to the need for specialized equipment and inert atmospheres to prevent oxidation.
2. Mechanical Alloying
Mechanical alloying is a solid-state powder processing technique involving repeated welding, fracturing, and rewelding of powder particles in a high-energy ball mill. This method is particularly effective for producing alloy powders with fine microstructures.
Advantages: Allows for the production of homogeneous alloy powders and can create materials with unique properties.
Disadvantages: Time-consuming and requires significant energy input.
3. Chemical Reduction
Chemical reduction is a process in which metal oxides are reduced to their metallic form using a reducing agent, such as hydrogen or carbon. The resulting metal is then ground into fine powder.
Advantages: Produces high-purity powders with fine particle sizes and is relatively low-cost.
Disadvantages: Limited to metals that can be easily reduced, such as copper, nickel, and tungsten.
4. Electrolytic Processes
Electrolytic processes involve the deposition of metal onto a cathode during electrolysis, followed by the removal and grinding of the deposited metal to form powder. This method is commonly used for metals like copper, silver, and nickel.
Advantages: Produces extremely high-purity powders with uniform particle sizes.
Disadvantages: Limited to metals that can be easily deposited electrolytically, and the process can be slow.
5. Sol-Gel Processing
Sol-gel processing is a chemical method that involves the transition of a solution into a solid gel phase. The gel is then dried and calcined to produce fine ceramic powders with high purity.
Advantages: Allows for precise control over the composition and microstructure of the powders.
Disadvantages: Generally limited to ceramic materials and can be complex to scale up.
6. Vapor Phase Synthesis
Vapor phase synthesis involves the condensation of metal vapors into fine powder particles. This method is used for producing ultra-fine powders, often with nanometer-sized particles.
Advantages: Produces powders with very high purity and fine particle sizes.
Disadvantages: Expensive and requires specialized equipment to handle metal vapors.
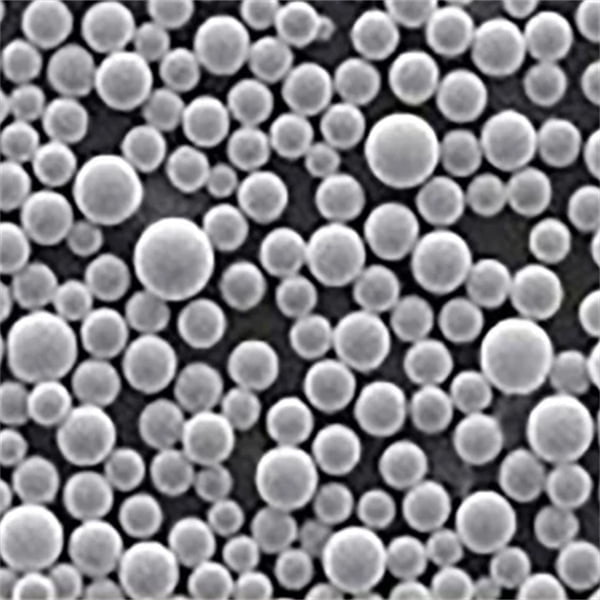
Specific Metal Powder Models and Their Properties
To give you a clearer picture of the range of high purity powders available, let’s explore some specific metal powder models, their compositions, and properties.
Metal Powder | Composition | Purity | Particle Size | Characteristics | Applications |
---|---|---|---|---|---|
Copper Powder | Cu | 99.9% | 10-50 microns | Excellent electrical conductivity | Electronics, 3D printing |
Nickel Powder | Ni | 99.9% | 5-20 microns | Corrosion-resistant, magnetic properties | Aerospace, electronics |
Tungsten Powder | W | 99.95% | 1-10 microns | High density, high melting point | Aerospace, radiation shielding |
Aluminum Powder | Al | 99.8% | 10-45 microns | Lightweight, high strength-to-weight ratio | Aerospace, automotive, 3D printing |
Titanium Powder | Ti | 99.5% | 20-60 microns | Biocompatible, high strength, corrosion-resistant | Medical devices, aerospace, 3D printing |
Cobalt Powder | Co | 99.9% | 5-20 microns | Magnetic properties, wear resistance | Electronics, hard alloys |
Silver Powder | Ag | 99.99% | 1-10 microns | High electrical and thermal conductivity | Electronics, conductive inks |
Gold Powder | Au | 99.99% | 1-10 microns | Excellent conductivity, corrosion-resistant | Electronics, jewelry, high-end coatings |
Platinum Powder | Pt | 99.95% | 2-15 microns | High chemical resistance, catalytic properties | Catalysts, electronics, medical devices |
Iron Powder | Fe | 99.5% | 10-100 microns | Magnetic properties, good machinability | Magnetic materials, powder metallurgy |
Characteristics and Uses
- Copper Powder: Known for its excellent electrical conductivity, copper powder is widely used in electronics for applications such as conductive inks and 3D printing. Its fine particle size allows for precise component fabrication.
- Nickel Powder: With its corrosion resistance and magnetic properties, nickel powder is a key material in aerospace applications, particularly in turbine blades and other high-performance components.
- Tungsten Powder: Tungsten’s high density and melting point make it ideal for radiation shielding and aerospace applications where extreme temperatures are encountered.
- Aluminum Powder: Aluminum powder’s lightweight nature and high strength-to-weight ratio are why it is frequently used in the aerospace and automotive industries, as well as in additive manufacturing.
- Titanium Powder: Titanium is known for its biocompatibility and corrosion resistance, making it a prime candidate for medical implants and aerospace components.
- Cobalt Powder: Cobalt’s magnetic properties and wear resistance make it essential for high-performance alloys and electronic components.
- Silver Powder: Silver powder’s superior electrical and thermal conductivity make it indispensable in electronics, particularly for conductive inks used in printed circuit boards.
- Gold Powder: Gold’s excellent conductivity and resistance to corrosion make it ideal for high-end electronics and coatings, as well as in jewelry making.
- Platinum Powder: Platinum is valued for its catalytic properties and chemical resistance, making it essential in catalytic converters and medical devices.
- Iron Powder: Iron powder is widely used in magnetic materials and powder metallurgy, where its machinability and magnetic properties are highly valued.
Comparison of Preparation Methods for High Purity Powders
Different methods for preparing high purity powders come with their own set of advantages and limitations. Let’s compare these methods to help you understand which one might be best suited for specific applications.
Preparation Method | Advantages | Disadvantages | Best For |
---|---|---|---|
Atomization | Produces spherical particles, good flowability | Expensive, risk of oxidation | Metals and alloys with a need for consistent particle size |
Mechanical Alloying | Homogeneous alloy powders, unique properties | Time-consuming, high energy consumption | Custom alloys, nanocomposites |
Chemical Reduction | High purity, fine particle sizes | Limited to easily reducible metals | Tungsten, copper, nickel |
Electrolytic Processes | Extremely high purity, uniform particle sizes | Slow, limited to electrolytically deposited metals | Copper, silver, nickel |
Sol-Gel Processing | Precise control over composition and microstructure | Complex, primarily for ceramics | Ceramic powders, advanced composites |
Vapor Phase Synthesis | Ultra-fine powders, high purity | Expensive, requires specialized equipment | Nanoparticles, specialized coatings |
Applications of High Purity Powders
High purity powders are utilized in a variety of cutting-edge applications, each requiring specific material properties. Here’s a look at some of the key applications:
Industry | Application | Required Powder Characteristics |
---|---|---|
Electronics | Conductive inks, semiconductors | High electrical conductivity, fine particle size |
Aerospace | Turbine blades, structural components | High strength, corrosion resistance, lightweight |
Medical Devices | Implants, surgical instruments | Biocompatibility, corrosion resistance |
3D Printing | Prototyping, complex geometries | Consistent particle size, flowability, high purity |
Automotive | Lightweight structural parts | High strength-to-weight ratio, corrosion resistance |
Catalysis | Catalytic converters, chemical processes | High surface area, chemical resistance |
Jewelry | Fine jewelry, luxury coatings | Aesthetic appeal, corrosion resistance, high purity |
Magnetic Materials | Magnetic storage, sensors | Magnetic properties, machinability |
Electronics
In the electronics industry, high purity powders are crucial for manufacturing components that require excellent electrical conductivity, such as conductive inks for printed circuit boards and semiconductors. Materials like silver and copper powders are particularly valued for their ability to conduct electricity efficiently.
Aerospace
The aerospace industry demands materials that are both lightweight and strong, with excellent corrosion resistance. High purity powders like titanium and aluminum are essential in producing turbine blades, structural components, and other critical parts that must withstand extreme conditions.
Medical Devices
For medical applications, biocompatibility and corrosion resistance are of utmost importance. High purity titanium powders are widely used in the production of implants and surgical instruments, ensuring that these devices are safe and effective for long-term use in the human body.
3D Printing
Additive manufacturing, or 3D printing, relies heavily on high purity powders to produce precise and complex geometries. Consistent particle size and flowability are key characteristics for powders used in this industry, making materials like aluminum and cobalt ideal for creating strong, lightweight structures.
Automotive
In the automotive sector, the focus is on materials that offer a high strength-to-weight ratio and corrosion resistance. High purity aluminum powders are often used in the production of lightweight structural parts, helping to improve fuel efficiency without compromising safety.
Catalysis
Catalytic converters and chemical processing applications require powders with high surface areas and chemical resistance. Platinum and other high purity powders are used as catalysts to speed up reactions and improve efficiency in these processes.
Jewelry
In the world of fine jewelry, materials like gold and silver powders are prized for their aesthetic appeal and resistance to tarnishing. These high purity powders are used to create intricate designs and luxurious coatings that stand the test of time.
Magnetic Materials
Magnetic materials are essential in various technologies, from data storage to sensors. High purity iron and cobalt powders are used to produce components with the necessary magnetic properties and machinability, ensuring reliable performance in critical applications.
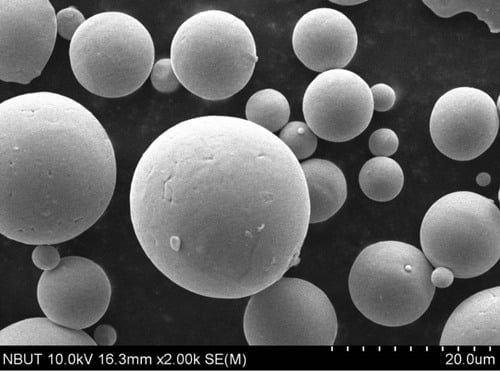
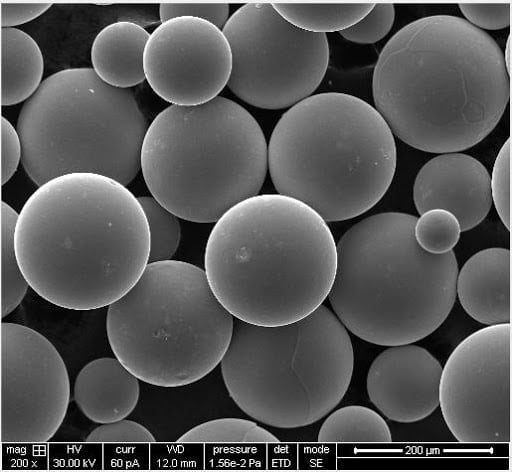
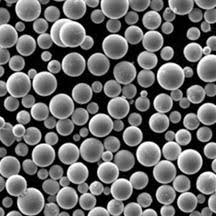
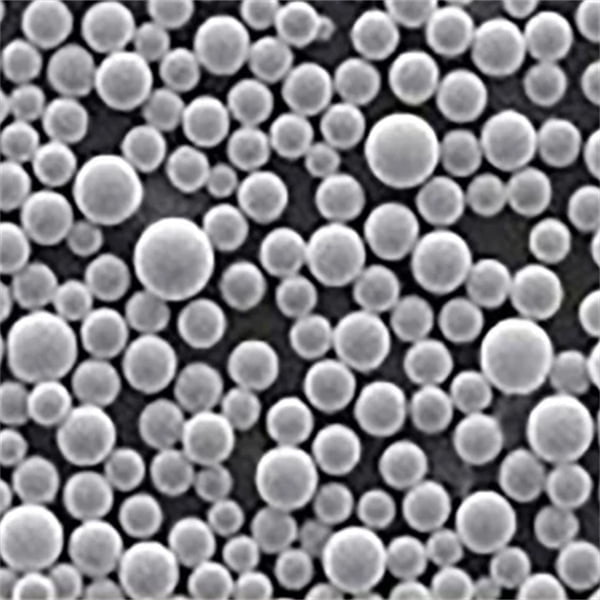
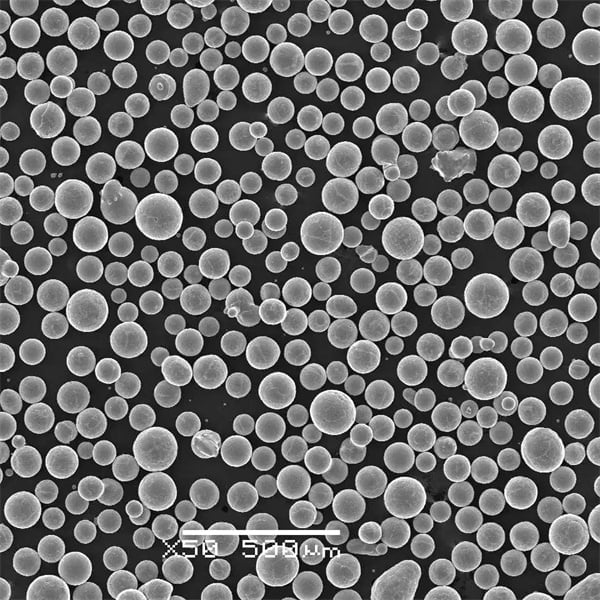
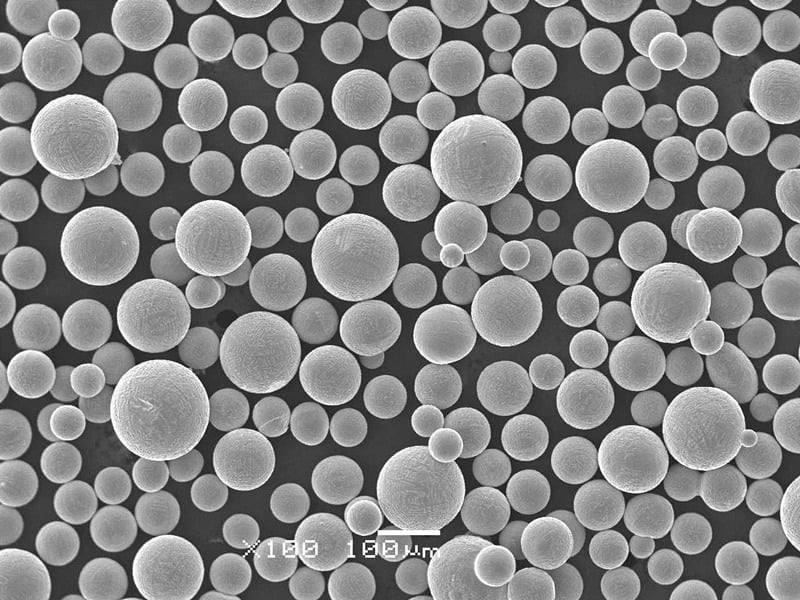
Specifications, Sizes, Grades, and Standards for High Purity Powders
When selecting high purity powders for specific applications, it’s important to consider the specifications, sizes, grades, and standards that govern their use. Here, we’ll outline some of the key parameters you should be aware of.
Material | Grade | Purity | Particle Size Range | Standards |
---|---|---|---|---|
Copper Powder | Electrolytic | 99.9% | 10-50 microns | ASTM B170, ISO 4288 |
Nickel Powder | Type 123 | 99.9% | 5-20 microns | ASTM B330, ISO 4499 |
Tungsten Powder | Grade W1 | 99.95% | 1-10 microns | ASTM B777, ISO 4499 |
Aluminum Powder | Grade 1100 | 99.8% | 10-45 microns | ASTM B209, ISO 6361 |
Titanium Powder | Grade 5 | 99.5% | 20-60 microns | ASTM F67, ISO 5832-2 |
Cobalt Powder | High Purity | 99.9% | 5-20 microns | ASTM B330, ISO 4499 |
Silver Powder | High Purity | 99.99% | 1-10 microns | ASTM B833, ISO 4506 |
Gold Powder | High Purity | 99.99% | 1-10 microns | ASTM B562, ISO 7302 |
Platinum Powder | High Purity | 99.95% | 2-15 microns | ASTM B841, ISO 11210 |
Iron Powder | Grade ASC100.29 | 99.5% | 10-100 microns | ASTM B822, ISO 3923 |
Understanding Grades and Standards
- Grades: These indicate the quality and suitability of the powder for specific applications. For instance, Titanium Grade 5 is known for its high strength and is commonly used in aerospace and medical applications.
- Purity: This is a measure of the chemical composition of the powder. High purity levels (e.g., 99.99%) are critical for applications where even trace amounts of impurities can affect performance.
- Particle Size Range: The size of the powder particles is crucial for ensuring proper flowability and packing density in applications like 3D printing and powder metallurgy.
- Standards: These are industry-specific guidelines that ensure the powder meets the necessary quality and safety requirements. For example, ASTM and ISO standards are widely recognized in the materials industry.
Suppliers and Pricing Details for High Purity Powders
Acquiring high purity powders requires sourcing from reputable suppliers who can provide consistent quality and meet industry standards. Here’s an overview of some leading suppliers and pricing details for high purity powders.
Supplier | Metal Powder | Grade | Price (per kg) | Minimum Order Quantity |
---|---|---|---|---|
American Elements | Copper Powder | Electrolytic | $100 | 1 kg |
Höganäs AB | Nickel Powder | Type 123 | $200 | 5 kg |
Global Tungsten & Powders Corp. | Tungsten Powder | Grade W1 | $500 | 1 kg |
Valimet Inc. | Aluminum Powder | Grade 1100 | $80 | 10 kg |
Advanced Powders & Coatings | Titanium Powder | Grade 5 | $350 | 5 kg |
Umicore | Cobalt Powder | High Purity | $300 | 2 kg |
Metalor Technologies | Silver Powder | High Purity | $1500 | 1 kg |
Ames Goldsmith | Gold Powder | High Purity | $60,000 | 100 g |
Johnson Matthey | Platinum Powder | High Purity | $25,000 | 100 g |
Rio Tinto Metal Powders | Iron Powder | Grade ASC100.29 | $50 | 25 kg |
Key Considerations When Choosing a Supplier
- Quality Assurance: Ensure that the supplier provides detailed material certifications and adheres to industry standards.
- Pricing: Pricing can vary significantly based on the metal, grade, and purity level. It’s important to balance cost with quality to meet your specific application needs.
- Minimum Order Quantity: This can vary from supplier to supplier. Smaller orders may be more expensive per unit, so consider your project’s scale when placing orders.
- Lead Times: Depending on the supplier and the specific metal powder, lead times can vary. Make sure to factor this into your production schedule.
Comparing Pros and Cons of Different High Purity Powders
Selecting the right high purity powder involves weighing the pros and cons of each option. Here’s a comparison to help you make an informed decision.
Metal Powder | Advantages | Disadvantages |
---|---|---|
Nickel Powder | Corrosion-resistant, magnetic properties | Expensive, limited to specific applications |
Tungsten Powder | High density, high melting point, excellent for radiation shielding | Very expensive, difficult to process |
Aluminum Powder | Lightweight, high strength-to-weight ratio, cost-effective | Can be prone to oxidation, requires special handling |
Titanium Powder | Biocompatible, high strength, corrosion-resistant | Expensive, challenging to process |
Cobalt Powder | Good magnetic properties, wear-resistant | Expensive, less commonly used in some applications |
Silver Powder | Superior electrical and thermal conductivity, aesthetic appeal | High cost, can tarnish over time |
Gold Powder | Excellent conductivity, high corrosion resistance, prestigious | Very high cost, primarily used in luxury applications |
Platinum Powder | High chemical resistance, catalytic properties | Extremely high cost, limited availability |
Iron Powder | Good machinability, magnetic properties, cost-effective | Lower purity compared to other metals, less corrosion-resistant |
Deciding Factors
When choosing a high purity powder for your specific application, consider these deciding factors:
- Application Requirements: Different applications demand different properties. For example, electronics require high electrical conductivity, while aerospace needs materials with high strength and low weight.
- Cost vs. Performance: Higher purity and specialized powders come with higher costs. Balance your budget with the performance requirements of your application.
- Processing and Handling: Some powders, like tungsten and titanium, are challenging to process and handle. Ensure that you have the necessary infrastructure and expertise to work with these materials.
- Supplier Reliability: Ensure your supplier can consistently provide high-quality powders and meet your order requirements.
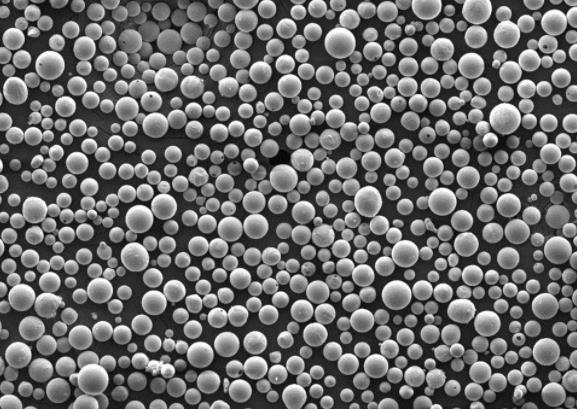
FAQs
What Is the Most Commonly Used High Purity Powder in Electronics?
Silver Powder is the most commonly used high purity powder in electronics due to its superior electrical and thermal conductivity. It is used in applications like conductive inks, solder pastes, and high-performance connectors.
How Does the Purity of Metal Powders Affect Their Performance?
The purity of metal powders is crucial for their performance. Higher purity powders have fewer impurities, which ensures better performance in applications requiring high precision, such as electronics and aerospace. Impurities can affect conductivity, strength, and overall reliability.
What Are the Key Considerations When Preparing High Purity Powders?
Key considerations include:
- Control of Contaminants: Ensuring the process minimizes contamination to maintain high purity.
- Particle Size: Achieving the desired particle size for optimal performance in the intended application.
- Processing Conditions: Utilizing appropriate methods and conditions to ensure the desired properties are achieved.
How Do Different Preparation Methods Compare in Terms of Cost?
- Atomization is often more expensive due to the need for specialized equipment and inert atmospheres.
- Mechanical Alloying and Chemical Reduction can be less costly but may have limitations based on the material and desired properties.
- Electrolytic Processes and Vapor Phase Synthesis are generally more expensive due to the complexity and cost of equipment.
Where Can I Find High Purity Powders for My Project?
High purity powders can be sourced from specialized suppliers such as American Elements, Höganäs AB, and Global Tungsten & Powders Corp. These suppliers provide a range of metal powders and offer detailed product specifications and support.
What Are the Safety Considerations When Handling High Purity Powders?
Handling high purity powders requires careful attention to safety due to the potential for dust inhalation and chemical reactivity. Always use appropriate personal protective equipment (PPE), handle powders in controlled environments, and follow safety guidelines provided by suppliers.
Conclusion
Preparing high purity powders involves a detailed and precise process to ensure that the final product meets stringent standards of purity and performance. Understanding the different preparation methods, properties of various metal powders, and their applications can help you make informed decisions for your specific needs.
From the basics of high purity powders to the intricacies of different preparation methods and applications, this guide provides a comprehensive overview of what you need to know. Whether you’re involved in electronics, aerospace, medical devices, or any other high-tech industry, high purity powders play a critical role in ensuring the reliability and efficiency of advanced materials.
By considering factors such as purity, preparation methods, and specific requirements of your application, you can select the right powder and supplier to meet your needs. With the right knowledge and resources, you can leverage high purity powders to achieve superior performance in your projects.
If you have any more questions or need further clarification on any of the topics covered, feel free to reach out or consult with industry experts for additional guidance.
About 3DP mETAL
Product Category
CONTACT US
Any questions? Send us a message now! After receiving your message, we will process your request with a whole team.