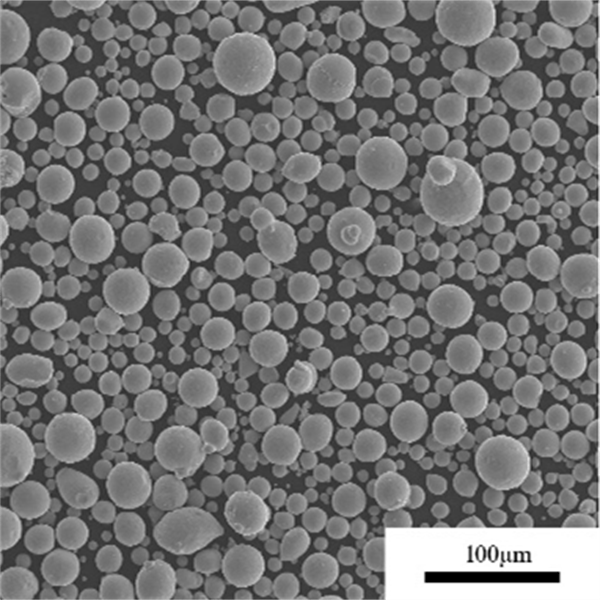
316L Stainless Steel Powder
Overview of 316L Stainless Steel Powder 316L is an austenitic stainless steel powder widely used in additive manufacturing to produce corrosion resistant parts with good mechanical properties and weldability. This article provides a detailed guide to 316L powder. Key aspects covered include composition, properties, AM process parameters, applications, specifications, suppliers, handling, inspection methods, comparisons to…
Small MOQ
Flexible sourcing for hundreds of products
Customization support
Customized powder according to industry
Rapid shipment
By DHL Express, safe and fast direct to your hands
Overview of 316L Stainless Steel Powder
316L is an austenitic stainless steel powder widely used in additive manufacturing to produce corrosion resistant parts with good mechanical properties and weldability. This article provides a detailed guide to 316L powder.
Key aspects covered include composition, properties, AM process parameters, applications, specifications, suppliers, handling, inspection methods, comparisons to alternatives, pros and cons, and FAQs. Tables are used to present information in an easy-to-reference format.
Composition of 316L Stainless Steel Powder
The composition of 316L stainless steel powder is:
Element | Weight % | Purpose |
---|---|---|
Iron | Balance | Principal matrix element |
Chromium | 16-18 | Corrosion resistance |
Nickel | 10-14 | Austenite stabilizer |
Molybdenum | 2-3 | Corrosion resistance |
Manganese | <2 | Deoxidizer |
Silicon | <1 | Deoxidizer |
Carbon | <0.03 | Avoid carbide precipitation |
The high chromium and nickel content provide corrosion resistance while the low carbon minimizes carbide precipitation.
Properties of 316L Stainless Steel Powder
Key properties of 316L powder include:
Property | Description |
---|---|
Corrosion resistance | Excellent resistance to pitting and crevice corrosion |
Strength | Tensile strength up to 620 MPa |
Weldability | Readily weldable and less prone to sensitization |
Fabricability | Easily formed into complex shapes |
Biocompatibility | Safe for contact with human body |
Temperature resistance | Resistant up to 900¡«C in oxidizing environments |
The properties make 316L suitable for harsh, corrosive environments.
AM Process Parameters for 316L Powder
Typical parameters for printing 316L powder include:
Parameter | Typical value | Purpose |
---|---|---|
Layer height | 20-100 Ã×m | Balance speed and resolution |
Laser power | 150-350 W | Melting condition without vaporization |
Scan speed | 200-1200 mm/s | Density versus build rate |
Hatch spacing | 100-200 Ã×m | Mechanical properties |
Supports | Minimal tree/lattice | Overhangs, internal channels |
Hot isostatic pressing | 1150¡«C, 100 MPa, 3 hrs | Eliminate porosity |
Parameters tailored for density, microstructure, production rate and post-processing needs.
Applications of 3D Printed 316L Parts
AM 316L components are used in:
Industry | Applications |
---|---|
Aerospace | Structural brackets, panels, housings |
Automotive | Turbine housings, impellers, valves |
Chemical | Pumps, valves, reaction vessels |
Oil and gas | Downhole tools, manifolds, flanges |
Biomedical | Dental, orthopedic implants, surgical tools |
Benefits versus wrought 316L include complex geometries, reduced part count, and accelerated product development.
Specifications of 316L Powder for AM
316L powder must meet strict specifications:
Parameter | Specification |
---|---|
Particle size range | 15-45 Ã×m typical |
Particle shape | Spherical morphology |
Apparent density | > 4 g/cc |
Tap density | > 6 g/cc |
Hall flow rate | > 23 sec for 50 g |
Purity | >99.9% |
Oxygen content | <1000 ppm |
Custom size distributions and controlled composition available.
Suppliers of 316L Stainless Steel Powder
Reputable 316L powder suppliers include:
Supplier | Location |
---|---|
Sandvik Osprey | UK |
Carpenter Additive | USA |
LPW Technology | UK |
Erasteel | Sweden |
Critical Materials | USA |
Praxair | USA |
Prices range from $50/kg to $120/kg based on quality considerations and order volumes.
Handling and Storage of 316L Powder
As a reactive material, careful 316L powder handling is essential:
- Store sealed containers away from moisture, acids, ignition sources
- Use inert gas padding during transportation and storage
- Ground equipment to dissipate static charges
- Avoid dust accumulation through extraction and ventilation
- Follow safety data sheet precautions
Proper techniques ensure optimal powder condition.
Inspection and Testing of 316L Powder
Quality testing methods include:
Method | Parameters Tested |
---|---|
Sieve analysis | Particle size distribution |
SEM imaging | Particle morphology |
EDX | Chemistry and composition |
XRD | Phases present |
Pycnometry | Density |
Hall flow rate | Powder flowability |
Testing per ASTM standards verifies powder quality and batch consistency.
Comparing 316L to Alternative Alloy Powders
316L compares to other alloys as:
Alloy | Corrosion Resistance | Strength | Cost | Printability |
---|---|---|---|---|
316L | Excellent | Medium | Medium | Excellent |
17-4PH | Good | High | Medium | Good |
IN718 | Good | Very high | High | Fair |
CoCr | Fair | Medium | Medium | Good |
With its balanced properties, 316L is very versatile for small to medium sized AM components needing corrosion resistance.
Pros and Cons of 316L Powder for AM
Pros | Cons |
---|---|
Excellent corrosion resistance and biocompatibility | Lower high temperature strength than alloys |
Readily weldable and machinable | Susceptible to porosity during printing |
Cost advantage over exotic alloys | Prone to thermal cracking |
Can match wrought material properties | Required post-processing like HIP |
Range of suppliers available | Lower hardness than precipitation hardening alloys |
316L provides versatile performance at moderate cost, albeit with controlled processing requirements.
Frequently Asked Questions about 316L Stainless Steel Powder
Q: What particle size range works best for printing 316L alloy?
A: A typical range is 15-45 microns. It provides good powder flowability combined with high resolution and density.
Q: What post-processing methods are used on 316L AM parts?
A: Hot isostatic pressing, heat treatment, surface machining, and electropolishing are common methods for achieving full densification and surface finish.
Q: Which metal 3D printing process is ideal for 316L alloy?
A: All major powder bed fusion processes including selective laser melting (SLM), direct metal laser sintering (DMLS) and electron beam melting (EBM) are regularly used.
Q: What industries use additively manufactured 316L components?
A: Aerospace, automotive, biomedical, marine hardware, chemical processing, and oil and gas industries benefit from 3D printed 316L parts.
Q: Does 316L require support structures during 3D printing?
A: Yes, support structures are essential on overhangs and bridged sections to prevent deformation and allow easy removal after printing.
Q: What defects can occur when printing 316L powder?
A: Potential defects are porosity, cracking, distortion, lack of fusion, and surface roughness. Most can be prevented with optimized parameters.
Q: What is the key difference between 316 and 316L alloys?
A: 316L has lower carbon content (0.03% max) which improves corrosion resistance and eliminates harmful carbide precipitation during welding.
Q: How are the properties of printed 316L compared to wrought alloy?
A: With optimized parameters, AM 316L components can achieve mechanical properties on par or exceeding conventionally processed wrought counterparts.
Q: What density can be expected with 3D printed 316L parts?
A: Density above 99% is achievable for 316L with ideal parameters tailored for the alloy, matching wrought material properties.
Q: What finishing is typically applied to 316L AM parts?
A: Abrasive flow machining, CNC machining, and electropolishing are common finishing processes for removing surface roughness and achieving the required tolerances.
Contact us now
Please contact us for recent product quotes and stock availability.