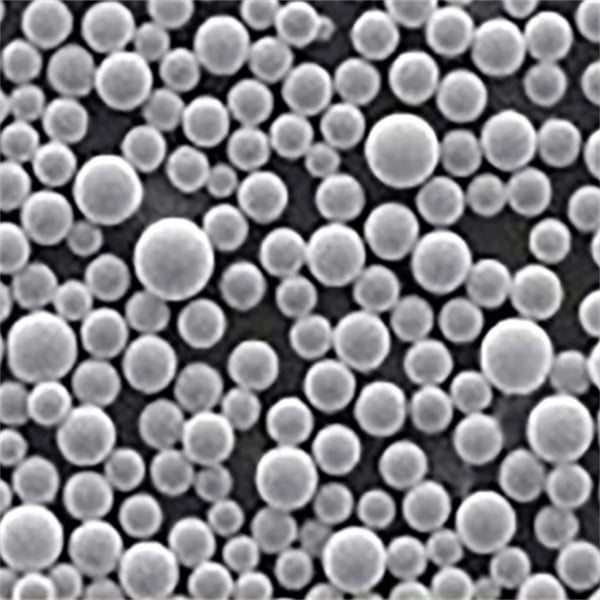
Alloy X-750 Powder
Alloy X-750 Powder: Overview Alloy X-750 Powder is highly esteemed for its exceptional high-temperature strength, oxidation resistance, and corrosion resistance, making it indispensable in various demanding applications. Its unique combination of properties makes it suitable for environments where extreme temperatures and aggressive atmospheres are prevalent. Composition Alloy X-750 Powder is meticulously crafted with precise alloying…
Small MOQ
Flexible sourcing for hundreds of products
Customization support
Customized powder according to industry
Rapid shipment
By DHL Express, safe and fast direct to your hands
Alloy X-750 Powder: Overview
Alloy X-750 Powder is highly esteemed for its exceptional high-temperature strength, oxidation resistance, and corrosion resistance, making it indispensable in various demanding applications. Its unique combination of properties makes it suitable for environments where extreme temperatures and aggressive atmospheres are prevalent.
Composition
Alloy X-750 Powder is meticulously crafted with precise alloying elements:
Element | Weight % |
---|---|
Nickel (Ni) | 70.0 min |
Chromium (Cr) | 14.0-17.0 |
Iron (Fe) | 5.0-9.0 |
Aluminum (Al) | 2.25-2.75 |
Titanium (Ti) | 0.7-1.2 |
Cobalt (Co) | 1.0 max |
Molybdenum (Mo) | 0.7-1.2 |
Copper (Cu) | 0.5-1.0 |
Silicon (Si) | 0.5 max |
Sulfur (S) | 0.01 max |
Carbon (C) | 0.08 max |
Properties
Alloy X-750 Powder boasts outstanding properties:
Property | Value |
---|---|
Density | 8.27 g/cm³ |
Tensile Strength | 1034 MPa (min) |
Yield Strength | 689 MPa (min) |
Elongation | 30% (min) |
Hardness (HRB) | 96 HRB |
Melting Point | 1393-1427°C |
Thermal Conductivity | 11.0 W/m·K |
Electrical Resistivity | 1.22 µΩ·m |
Applications
Alloy X-750 Powder finds extensive applications in the aerospace, gas turbine, and nuclear industries for components like turbine blades, rocket engines, and reactor vessels.
Additive Manufacturing Process
Produced through gas or plasma atomization processes, Alloy X-750 Powder is suitable for additive manufacturing techniques such as powder bed fusion and directed energy deposition.
Powder Specifications
Available in various size ranges, morphologies, and quality levels, Alloy X-750 Powder meets specific application requirements.
Standards and Grades
Alloy X-750 Powder complies with industry standards like AMS 5667, ensuring quality and suitability for diverse applications.
Quality Control
Stringent quality control measures, including chemical and particle size analysis, ensure the consistency and reliability of Alloy X-750 Powder.
Cost Analysis
The cost of Alloy X-750 Powder varies depending on factors such as volume, particle size range, and market conditions.
Powder Storage And Handling
Proper storage in sealed containers and adherence to handling protocols are essential to maintain the integrity of Alloy X-750 Powder.
Health And Safety
Alloy X-750 Powder poses minimal health risks but requires the use of personal protective equipment during handling and processing.
FAQ
- What are the main advantages of Alloy X-750 Powder? Alloy X-750 Powder offers exceptional high-temperature strength, oxidation resistance, and corrosion resistance, making it ideal for applications in aerospace, gas turbine, and nuclear industries.
- Can Alloy X-750 Powder be used in additive manufacturing? Yes, Alloy X-750 Powder is commonly used in additive manufacturing techniques such as powder bed fusion and directed energy deposition to produce components with superior high-temperature properties.
- Is Alloy X-750 Powder suitable for turbine blade applications? Yes, Alloy X-750 Powder is widely used in turbine blades due to its excellent high-temperature strength and oxidation resistance.
- What are the typical costs associated with Alloy X-750 Powder? Costs for Alloy X-750 Powder vary based on factors such as volume, particle size range, powder morphology, purity levels, and market conditions.
Contact us now
Please contact us for recent product quotes and stock availability.