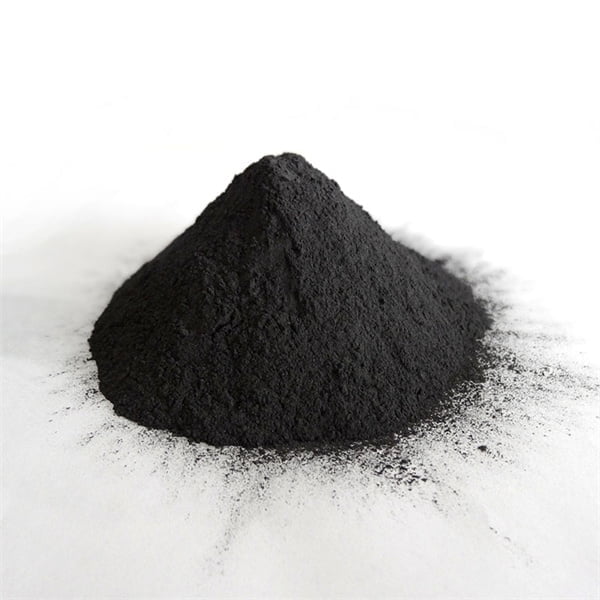
CoCrMo Powder
Overview of CoCrMo Powder CoCrMo is a cobalt-chromium-molybdenum alloy powder widely used in metal additive manufacturing for biomedical, dental, aerospace, and industrial applications needing wear resistance and biocompatibility. This article provides a detailed guide to CoCrMo powder covering composition, properties, AM process parameters, applications, specifications, suppliers, handling, inspection, comparisons, pros and cons, and FAQs. Key…
Small MOQ
Flexible sourcing for hundreds of products
Customization support
Customized powder according to industry
Rapid shipment
By DHL Express, safe and fast direct to your hands
Overview of CoCrMo Powder
CoCrMo is a cobalt-chromium-molybdenum alloy powder widely used in metal additive manufacturing for biomedical, dental, aerospace, and industrial applications needing wear resistance and biocompatibility.
This article provides a detailed guide to CoCrMo powder covering composition, properties, AM process parameters, applications, specifications, suppliers, handling, inspection, comparisons, pros and cons, and FAQs. Key information is presented in easy-to-reference tables.
Composition of CoCrMo Powder
The composition of CoCrMo alloy powder is:
Element | Weight % | Purpose |
---|---|---|
Cobalt | 58-69 | Matrix element, biocompatibility |
Chromium | 26-30 | Corrosion resistance, wear resistance |
Molybdenum | 5-7 | Strength, wear resistance |
Carbon | 0.05-0.35 | Carbide former |
Silicon | 1 max | Deoxidizer |
Manganese | 1 max | Deoxidizer |
Iron | 0.75 max | Contamination limit |
The high cobalt content provides biocompatibility while chromium and molybdenum impart strength and wear resistance.
Properties of CoCrMo Powder
Key properties of CoCrMo powder include:
Property | Description |
---|---|
Biocompatibility | Excellent compatibility with human body tissues |
Wear resistance | High abrasion and sliding wear resistance |
Corrosion resistance | Resistant to body fluids and many chemicals |
Strength | Tensile strength up to 1310 MPa when work hardened |
Hardness | Up to 54 HRC when age hardened |
Fatigue strength | Suitable for cyclical dynamic loading |
The properties enable use for load-bearing implants and devices.
AM Process Parameters for CoCrMo Powder
Typical parameters for printing CoCrMo powder include:
Parameter | Typical value | Purpose |
---|---|---|
Layer height | 20-50 Ã×m | Resolution vs build speed |
Laser power | 150-400 W | Melting condition without vaporization |
Scan speed | 400-1200 mm/s | Density versus production rate |
Hatch spacing | 80-120 Ã×m | Mechanical properties |
Supports | Tree or lattice | Overhangs, internal channels |
Hot isostatic pressing | 1220¡«C, 100 MPa, 3 hrs | Eliminate porosity |
Parameters tailored for density, microstructure, build rate and post-processing requirements.
Applications of 3D Printed CoCrMo Parts
AM CoCrMo components are used in:
Industry | Applications |
---|---|
Medical | Knee/hip implants, dental crowns, surgical tools |
Aerospace | Turbine blades, engine components |
Automotive | Valve seats, turbocharger wheels |
Industrial | Wear-resistant tooling, flanges, seals |
Oil and gas | Valve parts, pumps |
Benefits versus wrought CoCrMo include complex geometries, customized implants, reduced costs and lead times.
Specifications of CoCrMo Powder for AM
CoCrMo powder must meet strict specifications:
Parameter | Specification |
---|---|
Particle size range | 15-45 Ã×m typical |
Particle shape | Spherical morphology |
Apparent density | > 4 g/cc |
Tap density | > 6 g/cc |
Hall flow rate | > 23 sec for 50 g |
Purity | >99.9% |
Oxygen content | <1000 ppm |
Custom size distributions and controlled moisture levels available.
Suppliers of CoCrMo Powder
Reputable CoCrMo powder suppliers include:
Supplier | Location |
---|---|
Carpenter Additive | USA |
Sandvik Osprey | UK |
Erasteel | Sweden |
AP&C | Canada |
LPW Technology | UK |
Arcam AB | Sweden |
Pricing ranges from $50/kg to $120/kg based on quality considerations and order volume.
Handling and Storage of CoCrMo Powder
As a reactive material, careful CoCrMo powder handling is essential:
- Store sealed containers away from moisture, acids, ignition sources
- Prevent exposure to air and use inert gas padding
- Ground equipment to dissipate static charges
- Avoid dust accumulation and use dust extraction
- Local exhaust ventilation recommended
- Follow safety data sheet precautions
Proper techniques ensure optimal powder condition.
Inspection and Testing of CoCrMo Powder
Quality testing methods include:
Method | Parameters Tested |
---|---|
Sieve analysis | Particle size distribution |
SEM imaging | Particle morphology |
EDX | Chemistry and composition |
XRD | Phases present |
Pycnometry | Density |
Hall flow rate | Powder flowability |
Testing per ASTM standards verifies powder quality and batch consistency.
Comparing CoCrMo to Alternative Alloy Powders
CoCrMo compares to other alloys as:
Alloy | Biocompatibility | Strength | Cost | Printability |
---|---|---|---|---|
CoCrMo | Excellent | Medium | Medium | Good |
Titanium Ti64 | Good | Low | High | Fair |
Stainless steel 316L | Good | Medium | Medium | Excellent |
Inconel 718 | Poor | High | High | Good |
CoCrMo provides the best combination of biocompatibility, strength, and printability for many applications.
Pros and Cons of CoCrMo Powder for AM
Pros | Cons |
---|---|
Excellent biocompatibility and corrosion resistance | Limited high temperature capability |
Very good wear and abrasion resistance | Susceptible to porosity during printing |
Readily 3D printable and weldable | Requires controlled atmosphere handling |
Cost advantage versus titanium alloys | Post-processing often needed |
Can match wrought material properties | Lower fracture toughness than stainless steels |
CoCrMo enables functional metal implants and components, albeit with controlled processing requirements.
Frequently Asked Questions about CoCrMo Powder
Q: What particle size range works best for 3D printing CoCrMo alloy?
A: A typical range is 15-45 microns. It provides good powder flowability combined with high resolution and density.
Q: What post-processing methods are used on CoCrMo AM parts?
A: Hot isostatic pressing, heat treatment, surface machining, and polishing are commonly used post-processes for achieving full density and surface finish.
Q: Which metal 3D printing processes are compatible with CoCrMo alloy?
A: Selective laser melting (SLM), direct metal laser sintering (DMLS) and electron beam melting (EBM) can all process CoCrMo powder.
Q: What industries use additively manufactured CoCrMo components?
A: Medical, dental, aerospace, automotive, oil and gas, and industrial sectors benefit from 3D printed CoCrMo parts.
Q: Does CoCrMo require support structures during 3D printing?
A: Yes, supports are needed on overhangs and internal channels to prevent deformation and allow easy removal after printing.
Q: What defects can occur when printing CoCrMo powder?
A: Potential defects are porosity, cracking, distortion, incomplete fusion, and surface roughness. Most can be prevented with optimized parameters.
Q: What type of biocompatibility testing is done on CoCrMo alloys?
A: Cytotoxicity, sensitization, irritation, systemic toxicity, genotoxicity, and implantation testing per standards like ISO 10993 are conducted.
Q: How are the properties of printed CoCrMo compared to cast alloy?
A: AM CoCrMo components can achieve mechanical properties on par or better than cast and annealed counterparts when optimized.
Q: What are the main differences between CoCr F75 and SP2 alloys?
A: F75 has higher carbon for better machinability while SP2 has lower carbon plus niobium for improved particle melting behavior during printing.
Q: What density can be expected with 3D printed CoCrMo components?
A: Density above 99% is achievable for CoCrMo with ideal parameters tailored for the alloy, matching wrought material properties.
Contact us now
Please contact us for recent product quotes and stock availability.