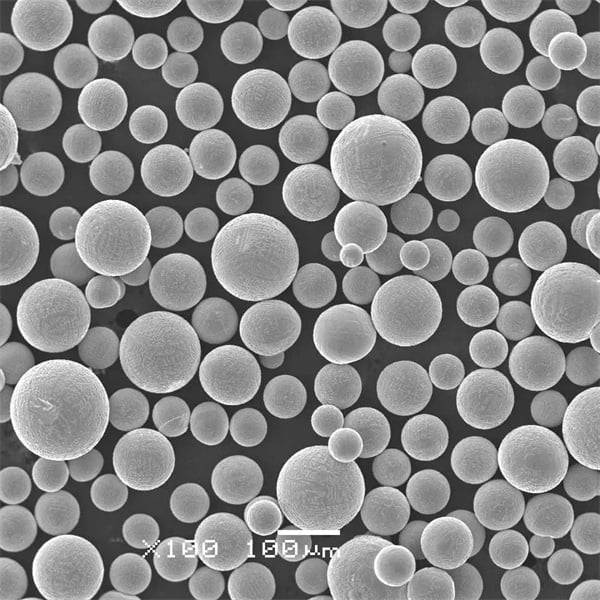
H13 tool steel powder
H13 Tool Steel Powder: Overview H13 tool steel powder is a high-performance steel powder known for its exceptional hot hardness, wear resistance, and toughness. It is widely utilized in tooling and die applications where high-temperature strength and resistance to thermal fatigue are essential. Composition The composition of H13 tool steel powder is meticulously designed to…
Small MOQ
Flexible sourcing for hundreds of products
Customization support
Customized powder according to industry
Rapid shipment
By DHL Express, safe and fast direct to your hands
H13 Tool Steel Powder: Overview
H13 tool steel powder is a high-performance steel powder known for its exceptional hot hardness, wear resistance, and toughness. It is widely utilized in tooling and die applications where high-temperature strength and resistance to thermal fatigue are essential.
Composition
The composition of H13 tool steel powder is meticulously designed to optimize its mechanical properties and performance:
Element | Weight % |
---|---|
Carbon (C) | 0.32-0.45 |
Chromium (Cr) | 4.75-5.50 |
Molybdenum (Mo) | 1.10-1.75 |
Vanadium (V) | 0.80-1.20 |
Silicon (Si) | 0.80-1.20 |
Manganese (Mn) | ≤0.50 |
Phosphorus (P) | ≤0.03 |
Sulfur (S) | ≤0.03 |
Iron (Fe) | Balance |
These alloying elements impart excellent hardenability, strength, and heat resistance to H13 tool steel powder.
Properties
H13 tool steel powder boasts impressive mechanical properties, ensuring its suitability for various industrial applications:
Property | Value |
---|---|
Density | 7.8-8.0 g/cm³ |
Hardness | 45-50 HRC |
Tensile Strength | 1000-1100 MPa |
Yield Strength | 850-900 MPa |
Elongation | 10-15% |
Thermal Conductivity | 23.8 W/m-K |
Coefficient of Thermal Expansion | 11.5 µm/m-K |
Melting Point | 1427-1475°C |
These properties make H13 tool steel powder an ideal choice for components requiring high strength, lightweight design, and resistance to harsh environments.
Applications
Typical applications for H13 tool steel powder include:
- Die casting dies
- Extrusion dies
- Forging dies
- Plastic molds
- Hot work tooling
- Injection molds
- Metal forming tools
Its combination of high hardness, toughness, and heat resistance makes it indispensable for tooling applications in manufacturing processes.
Additive Manufacturing Process
H13 tool steel powder is typically produced through gas atomization or water atomization processes. Gas atomization involves the rapid solidification of molten metal by high-pressure gas streams, resulting in spherical powder particles suitable for additive manufacturing. Water atomization produces irregular-shaped particles, requiring post-processing for additive manufacturing applications.
Powder Specifications
H13 tool steel powder is available in various specifications to meet specific application requirements:
Attribute | Details |
---|---|
Particle sizes | 15-45 µm, 10-100 µm |
Morphology | Spherical, irregular |
Apparent density | 3.5-4.5 g/cm³ |
Tap density | 4-5 g/cm³ |
Purity | ≥99.5% |
Oxygen content | <300 ppm |
Moisture content | <0.2% |
These specifications ensure the quality and consistency of H13 tool steel powder for additive manufacturing processes.
Standards and Grades
H13 tool steel powder complies with relevant industry standards, including ASTM A681 and AISI H13. Equivalent grades include DIN 1.2344 and JIS SKD61.
Quality Control
Quality control measures for H13 tool steel powder include:
- Chemical analysis: Verifying the correct composition of alloying elements.
- Particle size analysis: Ensuring the desired particle size distribution.
- Powder morphology assessment: Checking for spherical or irregular particle shapes.
- Density testing: Measuring apparent and tap densities for powder packing efficiency.
- Purity assessment: Verifying the purity level to ensure desired properties.
- Oxygen and moisture content analysis: Monitoring to prevent contamination.
Cost Analysis
Costs for H13 tool steel powder vary depending on factors such as order volume, particle size range, powder morphology, purity levels, and manufacturer/distributor margins.
Powder Storage And Handling
Proper storage and handling practices are crucial to maintain the integrity of H13 tool steel powder:
- Store in sealed containers in a cool, dry environment.
- Use inert gas purging or vacuum to prevent moisture pickup.
- Ground all powder handling and transfer equipment.
- Use appropriate personal protective equipment (PPE) when handling powder.
Health And Safety
H13 tool steel powder poses minimal health risks with proper handling:
- Wear appropriate PPE when handling powder.
- Use HEPA-filtered vacuum for clean-up of dust and powder.
- Avoid breathing any welding or melting fumes.
- Dispose according to local environmental regulations.
FAQ
- Is H13 tool steel powder suitable for aerospace applications? Yes, H13 tool steel powder is commonly used in aerospace for structural parts, aircraft frames, and rocket motor casings due to its high strength and toughness.
- What are the main advantages of H13 tool steel powder for defense applications? H13 tool steel powder offers excellent strength and toughness, making it ideal for missile components and armor plating in defense applications.
- Can H13 tool steel powder be used in additive manufacturing processes? Yes, H13 tool steel powder is suitable for additive manufacturing processes such as selective laser melting (SLM) and electron beam melting (EBM) to produce complex components with high strength and corrosion resistance.
- What are the typical costs associated with H13 tool steel powder? Costs for H13 tool steel powder vary based on factors such as volume, particle size range, purity levels, and market conditions.
- Is H13 tool steel powder recyclable? Yes, H13 tool steel powder can be recycled and reused in additive manufacturing processes, provided it meets quality standards and is free from contamination.
Contact us now
Please contact us for recent product quotes and stock availability.