Imagine a world where complex metal parts can be created layer by layer, on-demand, with minimal waste. This isn’t science fiction; it’s the reality of Fabrico aditivo de alumínio, also known as 3D printing, for aluminum. This technology is transforming industries, offering unparalleled design freedom, lightweight components, and a sustainable approach to metal fabrication.
the Power of Aluminum Powders
At the heart of AM for aluminum lies a crucial ingredient: metal powder. These fine, granular particles are meticulously crafted to ensure smooth flow during the printing process and achieve the desired mechanical properties in the final product. But not all aluminum powders are created equal. Different alloys and processing methods result in a diverse range of options, each with its own strengths and applications.
Here’s a glimpse into ten specific metal powder models that are driving innovation in Additive Manufacturing for aluminum:
- AlSi10Mg: A popular workhorse, AlSi10Mg (Aluminum Silicon Magnesium) offers a good balance of strength, castability, and weldability. It’s widely used for applications like ductwork, tools, and engine parts.
- F357: Renowned for its consistent printability, F357 is a favorite for production environments. This alloy excels in achieving uniform results across various scales, making it ideal for high-volume manufacturing. However, its specialized nature comes at a slightly higher cost compared to some other options.
- Liga de escamas: Imagine a metal that’s not only lightweight but also boasts exceptional strength. Enter Scalmalloy, an aluminum-scandium alloy known for its high strength-to-weight ratio. This makes it a prime candidate for aerospace components and applications demanding both weight reduction and structural integrity.
- AEROSPRINT: Developed specifically for Laser Beam Melting (LBM) – a popular AM technique – AEROSPRINT boasts superior mechanical properties compared to traditional cast aluminum. This translates to lighter, stronger parts for demanding applications in the aerospace and defense sectors.
- AMable Maraging 300: Maraging steels are renowned for their exceptional strength after a specific heat treatment. AMable Maraging 300 brings this advantage to the AM world. This alloy offers high strength and good ductility, making it suitable for applications requiring robust performance under pressure.
- AlSi7Mg0.3: A close cousin to AlSi10Mg, AlSi7Mg0.3 offers a good balance of properties with slightly lower silicon content. This can be beneficial for applications where dimensional accuracy is critical.
- Al2024: Widely used in the aerospace industry, Al2024 is known for its high strength-to-weight ratio and good machinability. However, its susceptibility to corrosion requires careful post-processing considerations for AM applications.
- Custom Alloys: The beauty of AM lies in its ability to accommodate custom alloys. By tweaking the composition of the metal powder, manufacturers can create materials with properties tailored to specific applications. This opens doors for cutting-edge advancements in various industries.
- Nano-Alumina: This innovative powder incorporates nanometer-sized alumina particles within the aluminum matrix. This unique structure enhances strength and wear resistance, making it suitable for components requiring exceptional durability.
- Recycled Aluminum Powders: Sustainability is a growing concern in manufacturing. Recycled aluminum powders offer an eco-friendly alternative to virgin materials. They can be used to create high-quality parts with a reduced environmental footprint.
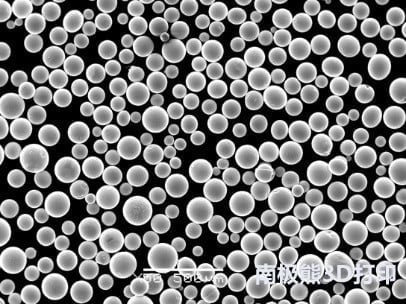
Composição, propriedades e características
Liga | Composition (wt%) | Propriedades principais | Características |
---|---|---|---|
AlSi10Mg | Si (9-11), Mg (0.3-0.6), Fe (<=0.5), Mn (<=0.5) | Good strength, castability, weldability | Excellent printability, good corrosion resistance |
F357 | Si (7-9), Mg (0.3-0.6), Cu (<=0.5), Fe (<=0.5) | Consistent printability, good mechanical properties | High cost compared to some alloys |
Scalmalloy | Al (balance), Sc (4.0-4.5), Mg (0.2-0.4), Zr (<=0.2) | Elevada relação força/peso, boa resistência à corrosão | Limited availability, requires specific printing parameters |
AEROSPRINT | Al (balance), Mg (Si < 0.2), Fe (< 0.2) | Superior mechanical properties, good fatigue resistance | Optimized for Laser Beam Melting |
AMable Maraging 300 | Fe (balance), Mo (18-19 |
Aplicações de Fabrico aditivo de alumínio
The true power of Additive Manufacturing for aluminum lies in its diverse range of applications. Unlike traditional manufacturing techniques that are limited by subtractive methods (removing material to create a shape), AM offers unparalleled design freedom. Complex geometries, internal channels, and lightweight structures become readily achievable, pushing the boundaries of what’s possible.
Here’s a breakdown of some key application areas for Additive Manufacturing Aluminum:
- Aeroespacial: The relentless pursuit of lightweight, high-strength components makes AM a perfect fit for the aerospace industry. From complex engine parts to intricate airframe components, aluminum alloys like Scalmalloy and AEROSPRINT are being used to create lighter, stronger aircraft, improving fuel efficiency and performance.
- Automotivo: Weight reduction is a top priority in the automotive industry, and AM for aluminum offers a compelling solution. Intricate components like cylinder heads, pistons, and even brake calipers can be additively manufactured using aluminum alloys like AlSi10Mg and custom alloys. This not only reduces weight but also enables the creation of complex cooling channels for improved thermal management.
- Dispositivos médicos: The ability to create custom prosthetics and implants with intricate lattice structures makes AM for aluminum valuable in the medical field. Biocompatible aluminum alloys are being explored for the creation of lightweight implants that better integrate with bone tissue.
- Bens de consumo: From custom-designed bike frames to intricate camera components, AM for aluminum is finding its way into consumer goods. The ability to create complex shapes and personalize products opens doors for innovative and aesthetically pleasing designs.
- Prototyping and Low-Volume Production: The rapid prototyping capabilities of AM make it ideal for creating functional prototypes quickly and efficiently. This allows for faster design iterations and reduces time-to-market for new products. Additionally, AM can be used for low-volume production runs, catering to niche markets or customized products.
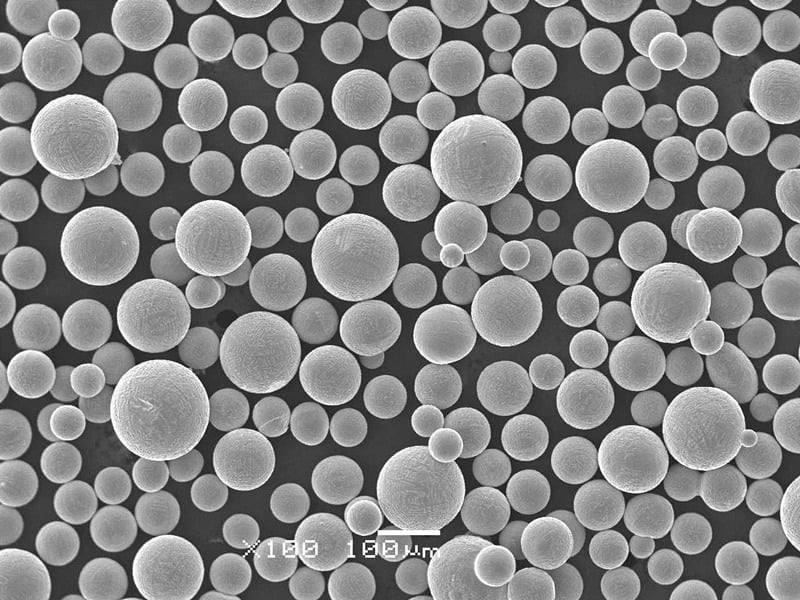
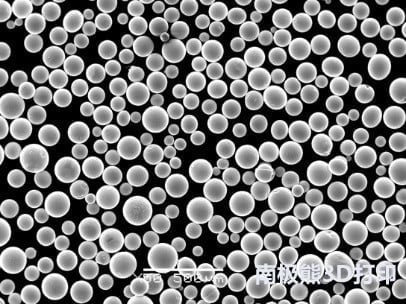
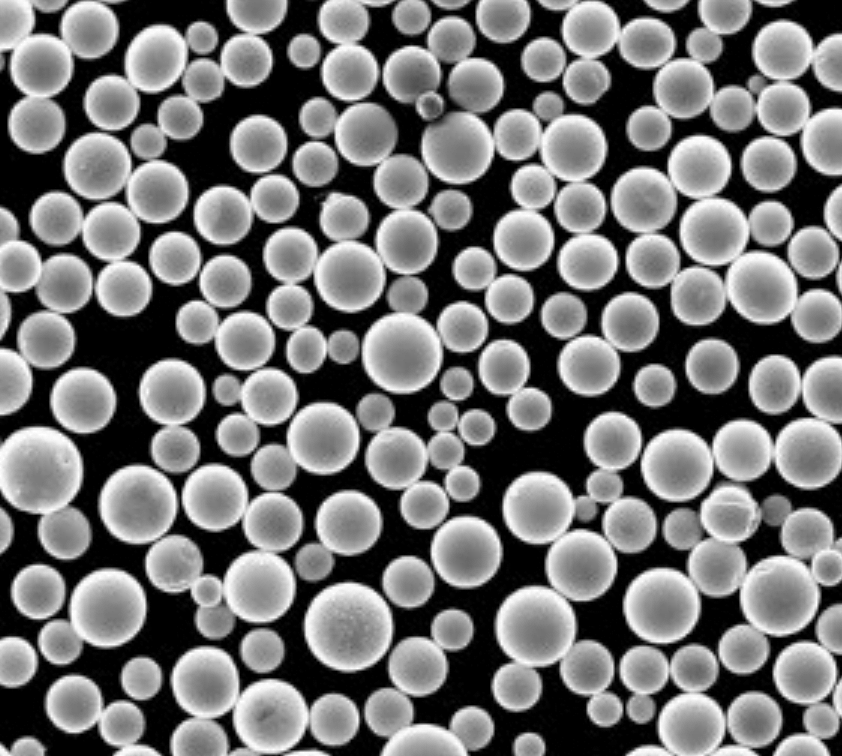
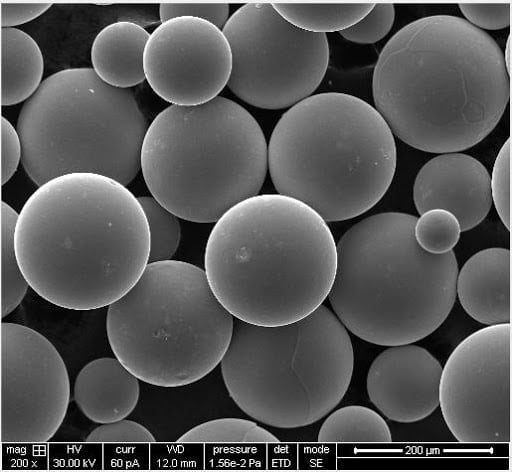
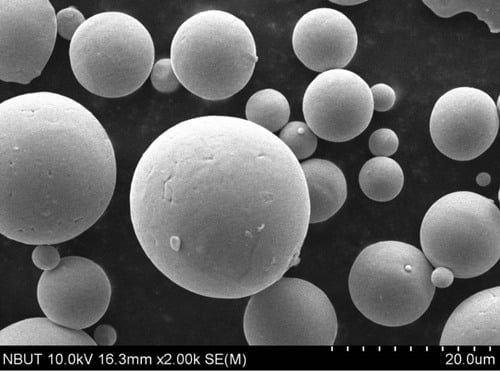
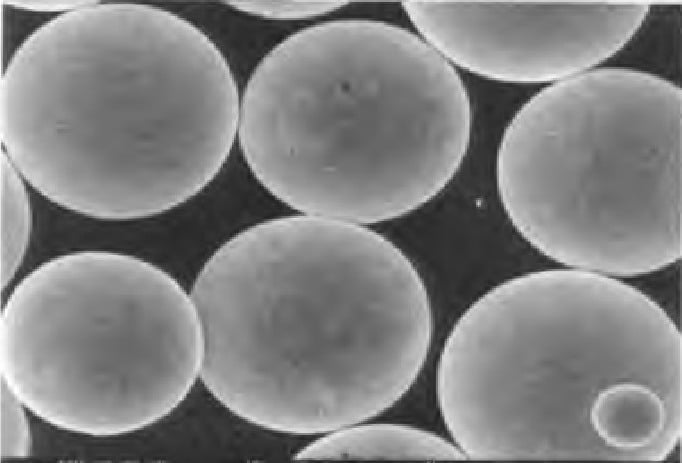
Aplicações de Fabrico aditivo de alumínio
Área de aplicação | Benefícios | Exemplos |
---|---|---|
Aeroespacial | Lightweight, high-strength components | Engine parts, airframe components, landing gear |
Automotivo | Weight reduction, complex cooling channels | Cylinder heads, pistons, brake calipers |
Dispositivos médicos | Custom prosthetics, lightweight implants | Bone plates, joint replacements |
bens de consumo | Complex shapes, personalized products | Bike frames, camera components, jewelry |
Prototyping & Low-Volume Production | Rapid prototyping, low-volume production runs | Functional prototypes, custom-designed products |
Advantages of Additive Manufacturing Aluminum: A Game Changer
Additive Manufacturing for aluminum offers a multitude of advantages over traditional subtractive manufacturing methods. Here’s a closer look at some of the key benefits:
- Liberdade de conceção: Unleash your creativity! AM allows for the creation of complex geometries, internal channels, and lightweight structures that are simply impossible with traditional methods. This opens doors for innovative designs and improved functionality.
- Lightweight Components: Aluminum’s inherent lightness, combined with the ability to create intricate lattice structures, makes AM ideal for weight reduction. This is particularly beneficial in industries like aerospace and automotive, where every gram saved translates to improved fuel efficiency and performance.
- Redução de resíduos: Traditional manufacturing often generates significant scrap material. AM, on the other hand, is a more sustainable approach. Material is only used where needed, minimizing waste and reducing environmental impact.
- Prototipagem rápida: The ability to quickly create functional prototypes allows for faster design iterations and reduces time-to-market for new products. This agility gives businesses a competitive edge in today’s fast-paced market.
- Fabrico a pedido: AM enables the creation of parts on-demand, eliminating the need for large inventories and reducing storage requirements. This is particularly beneficial for spare parts or customized products.
- Personalização em massa: The ability to create complex geometries with ease makes AM ideal for mass customization. Products can be tailored to individual needs and preferences, opening doors for a new era of personalized manufacturing.
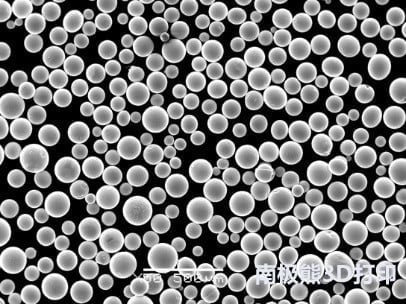
Disadvantages of Additive Manufacturing Aluminum
While Additive Manufacturing for aluminum offers a plethora of advantages, it’s important to acknowledge the limitations and considerations involved:
- Custo: Currently, AM for aluminum can be more expensive than traditional manufacturing methods, especially for high-volume production runs. The cost of metal powders, machine operation, and post-processing can add up. However, as technology advances and adoption increases, costs are expected to come down.
- Build Size Limitations: The size of components that can be additively manufactured is currently limited by the build volume of the machines. While advancements are being made, it may not be suitable for large-scale projects yet.
- Acabamento da superfície: The surface finish of additively manufactured parts can be rougher compared to those produced with traditional methods. Post-processing techniques like machining or polishing may be required to achieve a desired surface finish.
- Propriedades do material: The mechanical properties of additively manufactured aluminum parts can differ slightly from those produced with traditional methods. This is due to the inherent nature of the AM process, such as the layer-by-layer build and potential for residual stresses. However, ongoing research and development are continuously improving the properties of AM parts.
- Complexidade do processo: Additive Manufacturing for aluminum requires specialized equipment, skilled operators, and careful process control. Compared to traditional methods, AM has a steeper learning curve and may require additional expertise to ensure successful implementation.
- Qualificação parcial: For certain industries, like aerospace or medical, parts need to meet stringent qualification standards. Qualification processes for additively manufactured parts are still evolving, and specific protocols may need to be developed for each application.
Vantagens e desvantagens de Fabrico aditivo de alumínio
Vantagem | Descrição | Desvantagem | Descrição |
---|---|---|---|
Liberdade de conceção | Create complex geometries, internal channels, lightweight structures | Custo | Currently more expensive than traditional methods for high-volume production |
Lightweight Components | Reduce weight for improved performance | Limitações de tamanho de construção | Restricted by machine build volume |
Redução de resíduos | Sustainable approach with minimal material waste | Acabamento da superfície | May require post-processing for desired finish |
Prototipagem Rápida | Faster design iterations and reduced time-to-market | Propriedades do material | Slight differences compared to traditional methods |
On-Demand Manufacturing | Create parts as needed, eliminate large inventories | Complexidade do processo | Requires specialized equipment, skilled operators, and control |
Mass Customization | Tailor products to individual needs | Qualificação parcial | Evolving standards, specific protocols may be needed |
Specifications, Sizes, Grades, and Standards for Additive Manufacturing Aluminum Powders
The specifications, sizes, grades, and standards for aluminum powders used in Additive Manufacturing are crucial factors for achieving desired results. Here’s a breakdown of these key considerations:
- Especificações: Aluminum powder specifications typically include chemical composition, particle size distribution, flowability, and apparent density. These parameters influence the printability, mechanical properties, and surface finish of the final additively manufactured part.
- Tamanhos: Aluminum powder for AM is typically available in a range of particle sizes, from micrometers to tens of micrometers. The choice of particle size depends on the specific AM technology being used and the desired properties of the final part. For example, finer powders offer better surface finish but may be less flowable, while coarser powders can be more flowable but may result in a rougher surface finish.
- Graus: A wide range of aluminum grades are available for AM, including wrought alloys, cast alloys, and even custom alloys. The choice of grade depends on the desired mechanical properties, corrosion resistance, and other application-specific requirements. Some popular grades used in AM for aluminum include AlSi10Mg, F357, Scalmalloy, and AEROSPRINT (as mentioned previously).
- Normas: Several standards are being developed to ensure the quality and consistency of aluminum powders for AM. These standards address factors like chemical composition, particle size distribution, and flowability. Some relevant standards include ASTM International (ASTM) standards and standards from industry organizations like the Aluminum Association (AA).
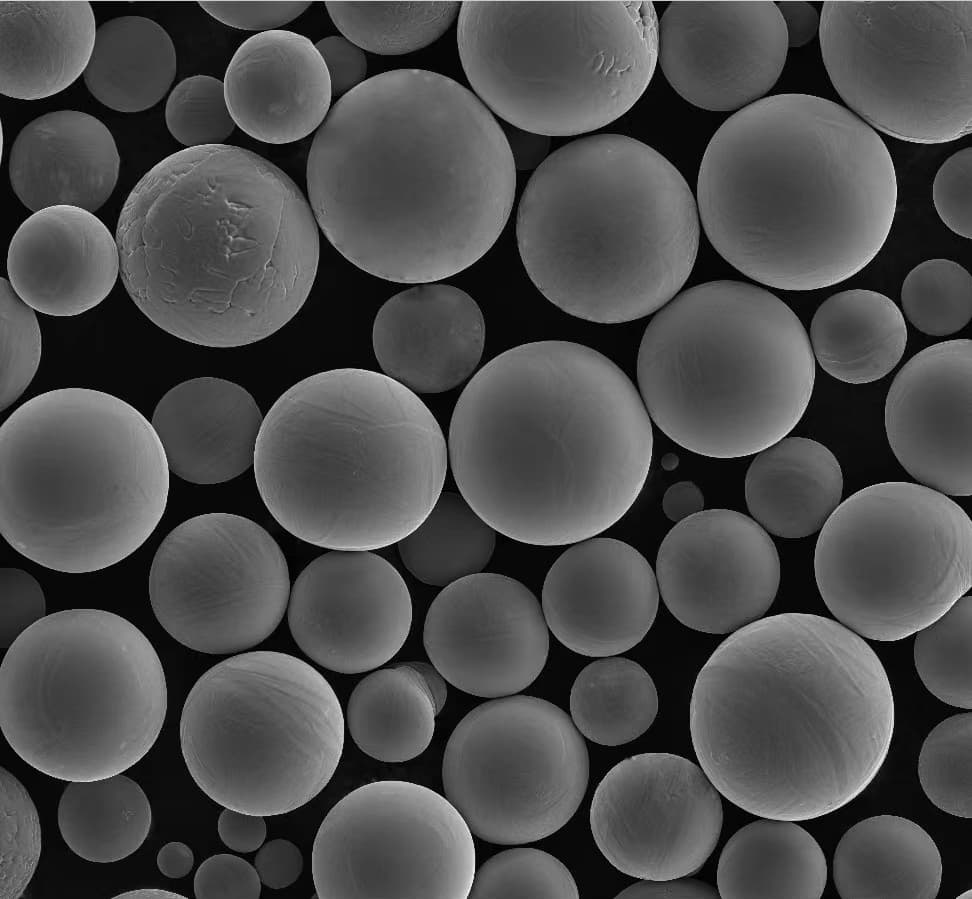
Suppliers and Pricing of Aluminum Powders for Additive Manufacturing
The availability and pricing of aluminum powders for Additive Manufacturing can vary depending on the specific alloy, particle size, and supplier. Here’s a general overview:
- Fornecedores: Several companies specialize in supplying aluminum powders for AM. These suppliers offer a range of alloys and particle sizes to cater to diverse printing applications. Some prominent names include AP Powder, Höganäs, SLM Solutions, and AMEX additiv.
- Preço: The pricing of aluminum powders for AM can vary significantly. Generally, finer powders and high-performance alloys tend to be more expensive. It’s important to consider the total cost of ownership, including material cost, machine operation costs, and post-processing requirements, when evaluating the economic viability of AM for a particular application.
O futuro da Fabrico aditivo de alumínio
Additive Manufacturing for aluminum is a rapidly evolving technology with immense potential. As costs decrease, machine capabilities improve, and material properties continue to be optimized, AM is poised to revolutionize various industries. Here are some exciting possibilities on the horizon:
- Wider adoption in high-volume production: Advancements in technology and cost reduction are expected to make AM for aluminum more competitive for high-volume production runs. This could open doors for the creation of lighter, more complex components across various sectors.
- Development of new aluminum alloys specifically for AM: Research is ongoing to develop new aluminum alloys specifically optimized for the AM process. These alloys will offer superior mechanical properties, printability, and performance, pushing the boundaries of what’s possible with AM.
- Integration of AM with other technologies: The future holds promise for the integration of Additive Manufacturing with other technologies. Imagine combining AM with machining or other post-processing techniques to achieve even more complex and high-quality parts. Additionally, the potential integration of AM with other digital manufacturing technologies, like simulation and design software, could create a seamless workflow for designing and producing optimized components.
- Sustainability advancements: Additive Manufacturing for aluminum offers inherent sustainability benefits due to reduced waste. As the technology matures and the use of recycled aluminum powders becomes more widespread, the environmental impact can be further minimized.
Overall, Additive Manufacturing for aluminum is a transformative technology with the potential to disrupt various industries. By unlocking design freedom, enabling lightweight components, and offering a sustainable approach to manufacturing, AM paves the way for a future filled with innovation and progress.
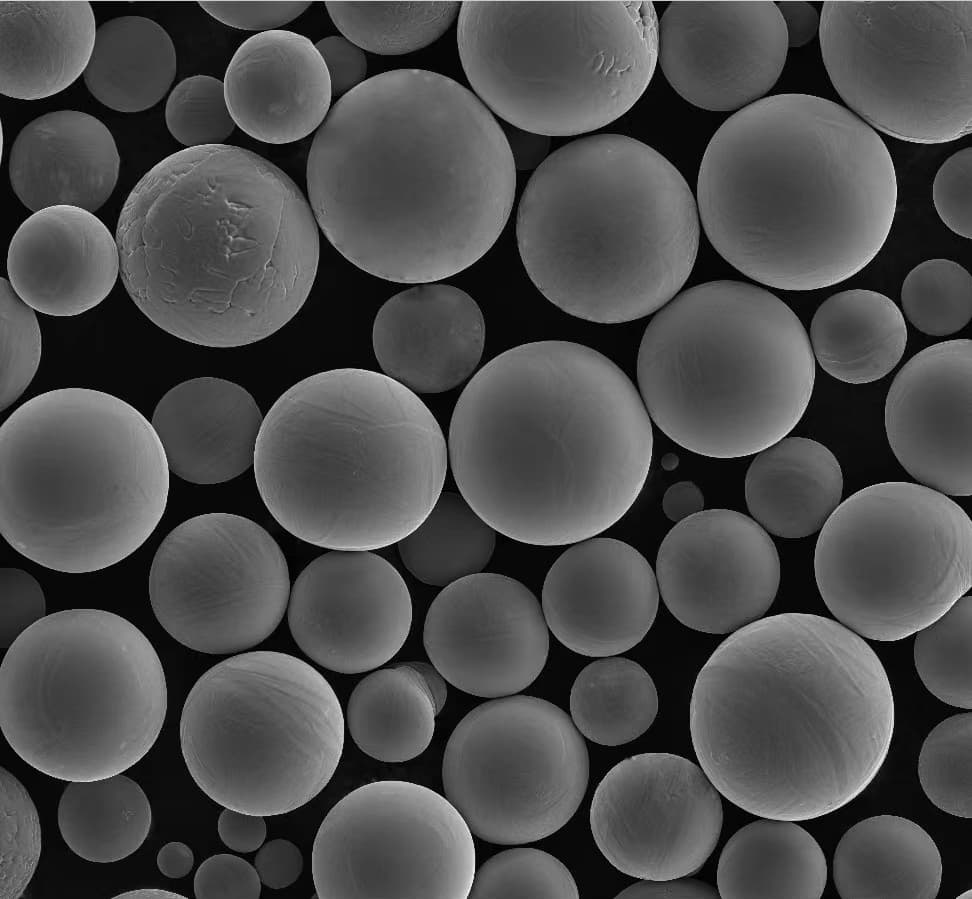
Perguntas Frequentes
Q: What are the benefits of using aluminum powders for Additive Manufacturing?
A: Aluminum powders offer several advantages for AM, including:
- Good printability: Aluminum powders generally flow well, making them suitable for various AM technologies.
- Componentes leves: Aluminum’s inherent lightness translates to lighter additively manufactured parts, improving performance in weight-sensitive applications.
- Diverse range of alloys: A wide variety of aluminum alloys are available for AM, catering to different needs in terms of strength, corrosion resistance, and other properties.
Q: What are some of the challenges associated with Additive Manufacturing Aluminum?
A: While AM for aluminum offers numerous benefits, there are also some challenges to consider:
- Custo: Currently, AM can be more expensive than traditional methods for high-volume production.
- Build size limitations: The size of parts that can be additively manufactured is currently limited by machine build volume.
- Complexidade do processo: AM requires specialized equipment, skilled operators, and careful process control.
Q: What are some typical applications for Additive Manufacturing Aluminum?
A: AM for aluminum finds applications in various sectors, including:
- Aeroespacial: Lightweight, high-strength components for aircraft.
- Automotivo: Weight reduction and complex cooling channels in engine parts and other components.
- Dispositivos médicos: Custom prosthetics and implants with intricate lattice structures.
- Bens de consumo: Complex shapes and personalized products like bike frames and camera components.
- Prototyping & Low-Volume Production: Rapid prototyping for faster design iterations and low-volume production runs for customized products.
Q: Where can I find suppliers of aluminum powders for Additive Manufacturing?
A: Several companies specialize in supplying aluminum powders for AM. Some prominent names include AP Powder, Höganäs, SLM Solutions, and AMEX additiv. It’s recommended to research and compare offerings from various suppliers to find the best fit for your specific needs and budget.
Sobre a 3DP mETAL
Categoria do produto
CONTACTE-NOS
Tem dúvidas ? Envie uma mensagem para nós agora mesmo! Após o recebimento de sua mensagem, nós processaremos sua solicitação com toda a equipe.