Visão geral do fabrico aditivo de cobre
Welcome to the world of additive manufacturing with copper! This incredible process is revolutionizing how we create complex and intricate parts, allowing for designs that were once impossible with traditional manufacturing techniques. In this guide, we’ll dive deep into the specifics of additive manufacturing with copper, from the types of metal powders used to the pros and cons of this method. We’ll also explore the various applications, technical specifications, and suppliers in this burgeoning field.
Copper, known for its excellent electrical and thermal conductivity, has found a new life in the realm of additive manufacturing. The ability to create parts with high precision and complexity opens up a wide range of possibilities in industries such as aerospace, automotive, electronics, and beyond. But what exactly is additive manufacturing, and how does copper fit into the picture? Let’s explore!
What is Additive Manufacturing?
Additive manufacturing, often referred to as 3D printing, is a process where materials are joined layer by layer to form a three-dimensional object. Unlike traditional subtractive manufacturing, which involves cutting away material from a solid block, additive manufacturing builds objects from the ground up based on digital models. This method offers unparalleled design freedom, allowing for the creation of complex geometries that are both lightweight and strong.
Types of Additive Manufacturing Processes
- Fusão Seletiva a Laser (SLM)
- Fusao por Feixe de Electron (EBM)
- Jato de ligante
- Direct Energy Deposition (DED)
- Material Extrusion
Each of these processes has its unique advantages and applications, making them suitable for different types of materials and end-use products.
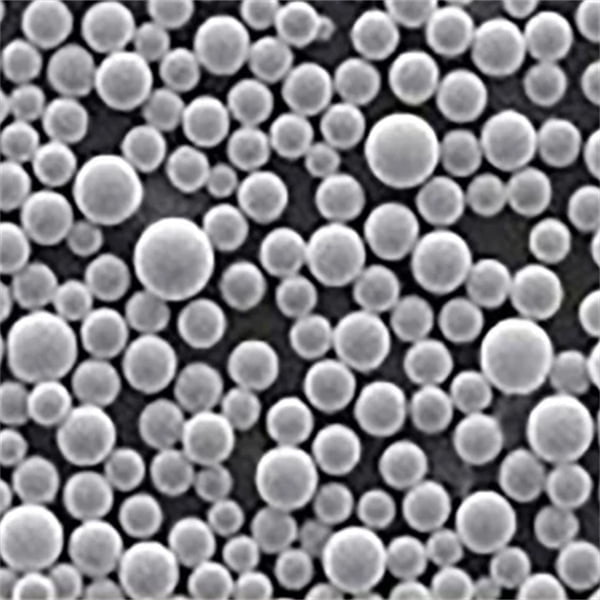
Why Use Copper in Additive Manufacturing?
Copper is highly valued for its electrical and thermal properties, making it a critical material in various industries. When it comes to additive manufacturing, copper’s ability to be printed into complex shapes without losing its intrinsic properties makes it an excellent choice. Let’s break down the reasons why copper is a game-changer in this field.
Principais benefícios da Fabrico aditivo Cobre
- Elevada condutividade eléctrica: Ideal for electrical components and circuits.
- Condutividade térmica: Perfect for heat exchangers and cooling systems.
- Antimicrobial Properties: Useful in medical devices and healthcare applications.
- Resistência à corrosão: Suitable for harsh environments and industrial applications.
Specific Metal Powder Models for Additive Manufacturing Copper
When it comes to additive manufacturing with copper, choosing the right metal powder is crucial. Here are ten specific models of copper powder that are widely used:
- CuCrZr (Copper-Chromium-Zirconium)
- Composição: Copper, Chromium, Zirconium
- Propriedades: High strength, good thermal stability
- APLICAÇÕES: Aerospace, automotive, electrical components
- CuNi2SiCr (Copper-Nickel-Silicon-Chromium)
- Composição: Copper, Nickel, Silicon, Chromium
- Propriedades: High hardness, excellent wear resistance
- APLICAÇÕES: Tooling, molds, electronic connectors
- CuSn10 (Copper-Tin)
- Composição: Copper, Tin
- Propriedades: Good corrosion resistance, decent strength
- APLICAÇÕES: Bearings, bushings, marine components
- Cu-OF (Oxygen-Free Copper)
- Composição: Pure copper with minimal oxygen content
- Propriedades: High conductivity, superior ductility
- APLICAÇÕES: Electrical wiring, high-purity applications
- CuNi10 (Copper-Nickel)
- Composição: Copper, Nickel
- Propriedades: Excellent corrosion resistance, good mechanical properties
- APLICAÇÕES: Marine engineering, chemical processing
- CuCr1Zr (Copper-Chromium-Zirconium)
- Composição: Copper, Chromium, Zirconium
- Propriedades: High strength, good conductivity
- APLICAÇÕES: Resistance welding electrodes, heat sinks
- CuNi30 (Copper-Nickel)
- Composição: Copper, Nickel
- Propriedades: High resistance to corrosion and erosion
- APLICAÇÕES: Shipbuilding, offshore technology
- CuBe2 (Copper-Beryllium)
- Composição: Copper, Beryllium
- Propriedades: High strength, non-magnetic
- APLICAÇÕES: Aerospace, oil and gas, telecommunications
- CuZn30 (Copper-Zinc)
- Composição: Copper, Zinc
- Propriedades: Good strength, excellent corrosion resistance
- APLICAÇÕES: Decorative items, industrial applications
- CuNi44 (Copper-Nickel)
- Composição: Copper, Nickel
- Propriedades: High electrical resistivity, good thermal conductivity
- APLICAÇÕES: Thermocouples, electrical resistors
Detailed Comparison of Copper Powders for Additive Manufacturing
Tipos, composição, propriedades e características
Pó de cobre | Composição | Propriedades | Características | APLICAÇÕES |
---|---|---|---|---|
CuCrZr | Cu, Cr, Zr | Alta resistência, estabilidade térmica | Good weldability | Aerospace, automotive, electrical |
CuNi2SiCr | Cu, Ni, Si, Cr | Elevada dureza, resistência ao desgaste | Good machinability | Tooling, molds, electronics |
CuSn10 | Cu, Sn | Corrosion resistance, moderate strength | Good castability | Bearings, bushings, marine |
Cu-OF | Cu puro | High conductivity, ductility | Low impurity levels | Electrical wiring, high-purity applications |
CuNi10 | Cu, Ni | Corrosion resistance, mechanical properties | Excelente soldabilidade | Marine engineering, chemical processing |
CuCr1Zr | Cu, Cr, Zr | High strength, conductivity | Good heat dissipation | Welding electrodes, heat sinks |
CuNi30 | Cu, Ni | Corrosion and erosion resistance | Good durability | Shipbuilding, offshore |
CuBe2 | Cu, Be | High strength, non-magnetic | Excellent fatigue resistance | Aerospace, oil and gas |
CuZn30 | Cu, Zn | Strength, corrosion resistance | Aesthetic appeal | Decorative, industrial |
CuNi44 | Cu, Ni | Electrical resistivity, thermal conductivity | Stable at high temperatures | Thermocouples, resistors |
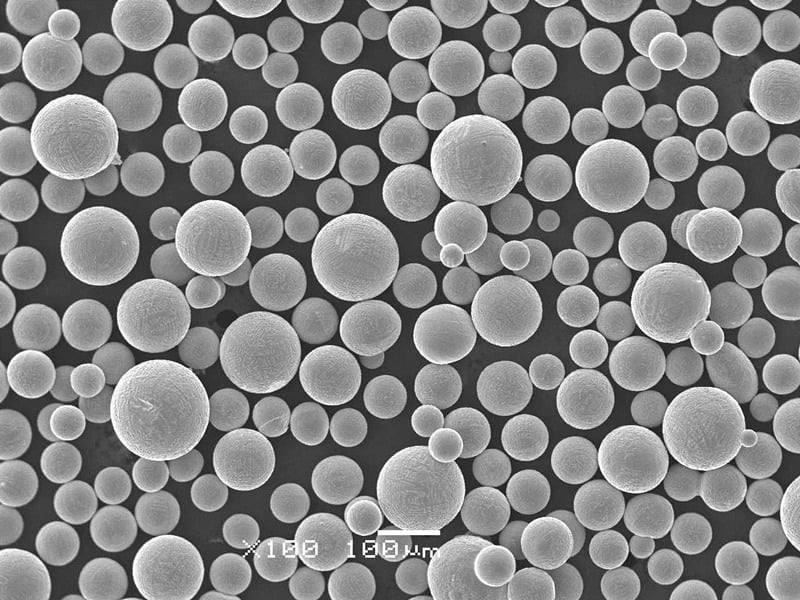
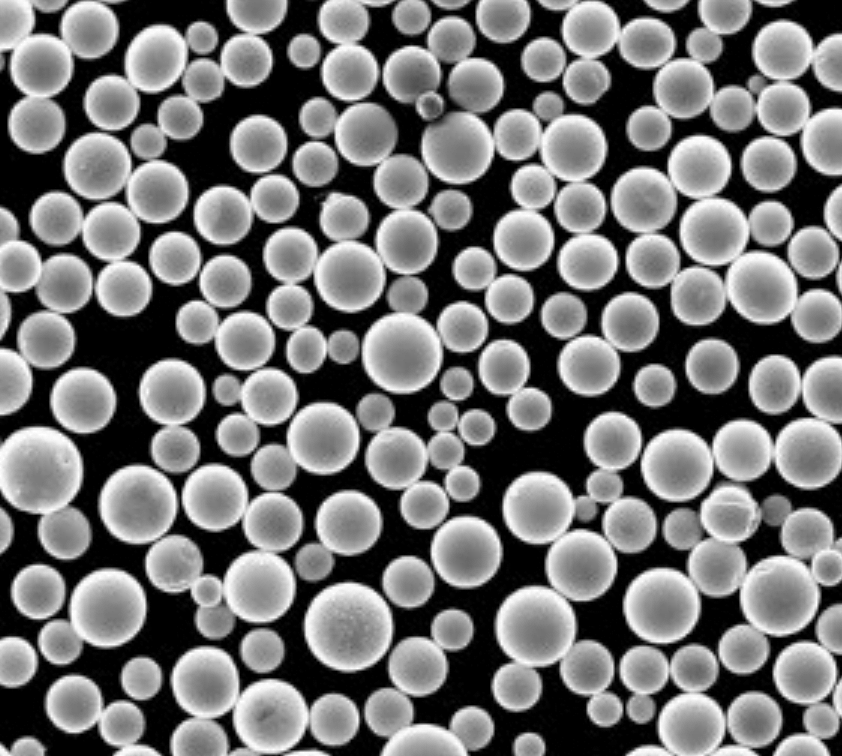
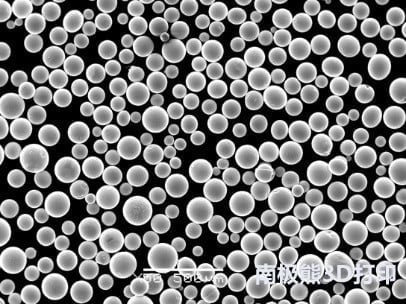
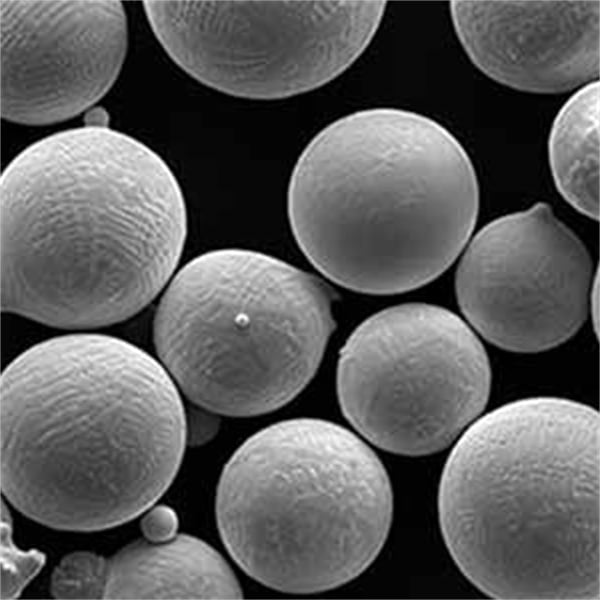
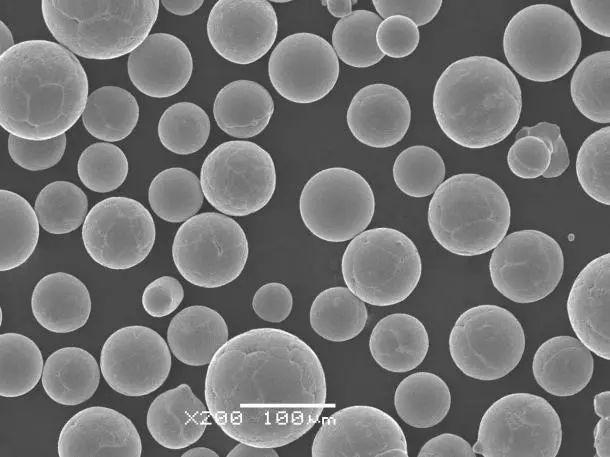
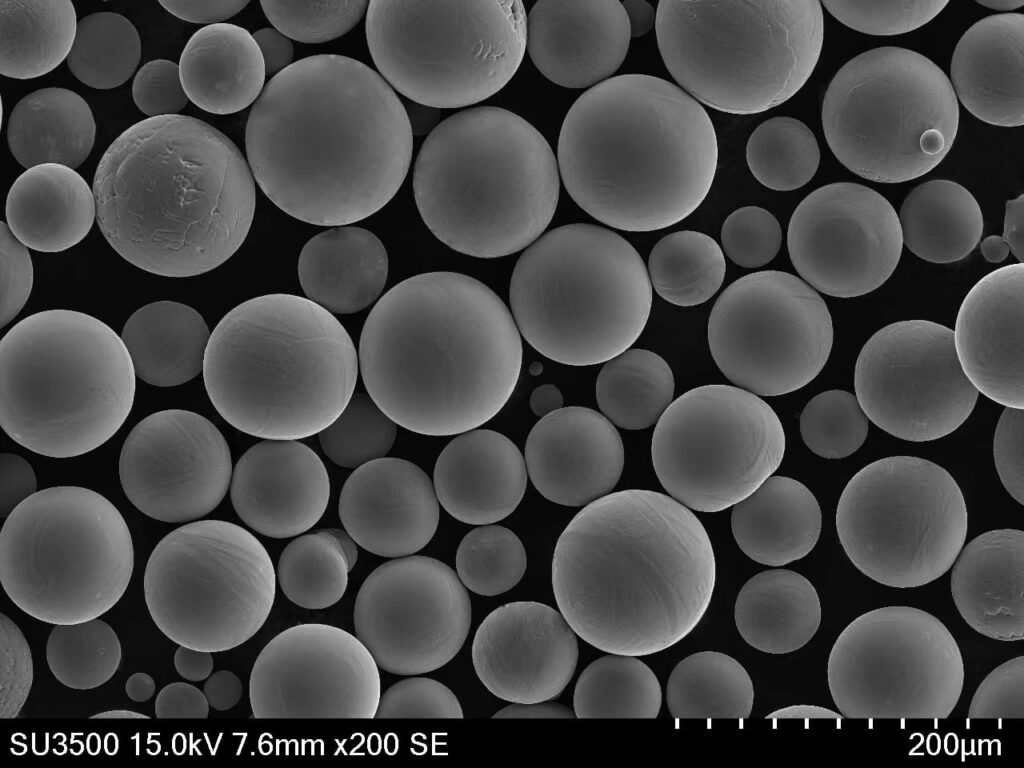
Applications of Additive Manufacturing Copper
Indústria | Aplicativo | Benefícios |
---|---|---|
Aeroespacial | Heat exchangers, fuel nozzles, structural components | Lightweight, durable, complex geometries |
Automotivo | Engine components, electrical connectors | Enhanced performance, reduced weight |
Eletrônica | Circuit boards, heat sinks, antennas | High conductivity, miniaturization |
Médico | Surgical tools, implants, prosthetics | Customization, biocompatibility |
Marinha | Propellers, hull fittings, heat exchangers | Resistência à corrosão, durabilidade |
Industrial | Molds, dies, wear-resistant parts | Improved lifespan, precision |
Produtos de consumo | Jewelry, decorative items | Aesthetic appeal, intricate designs |
Telecomunicações | Waveguides, connectors, heat dissipation components | Efficient signal transmission, reliability |
Especificações, tamanhos, graus e normas
Pó de cobre | Especificações | Tamanhos | Notas | Padrões |
---|---|---|---|---|
CuCrZr | ASTM B187, EN 12167 | 10-100 µm | C18150 | ASTM, EN |
CuNi2SiCr | ASTM B99, DIN 17666 | 15-120 µm | C70250 | ASTM, DIN |
CuSn10 | ASTM B505, EN 1982 | 20-150 µm | C90700 | ASTM, EN |
Cu-OF | ASTM B224, EN 13601 | 5-50 µm | C10100 | ASTM, EN |
CuNi10 | ASTM B151, EN 1653 | 25-200 µm | C70600 | ASTM, EN |
CuCr1Zr | ASTM B422, EN 12449 | 10-100 µm | C18160 | ASTM, EN |
CuNi30 | ASTM B359, EN 12451 | 30-250 µm | C71500 | ASTM, EN |
CuBe2 | ASTM B194, EN 1652 | 5-100 µm | C17200 | ASTM, EN |
CuZn30 | ASTM B36, EN 12163 | 15-100 µm | C26000 | ASTM, EN |
CuNi44 | ASTM B344, DIN 17670 | 20-150 µm | C71500 | ASTM, DIN |
Comparação dos prós e contras de Fabrico aditivo Cobre
Aspeto | **Prós** | Contras |
---|---|---|
Condutividade Elétrica | Superior conductivity | Complex post-processing |
Condutividade térmica | Excellent heat dissipation | High reflectivity issues during laser melting |
Flexibilidade de conceção | Enables complex geometries | Potential for residual stresses |
Utilização de materiais | Efficient use of materials | Higher cost of metal powders |
Propriedades Mecânicas | Alta relação resistência-peso | Anisotropic properties |
Personalização | Tailored solutions for specific needs | Limited scalability for large volumes |
Speed of Production | Faster prototyping and production | Slower compared to traditional methods for large batches |
Parâmetros técnicos e limiares
Parâmetros | Range/Threshold | Significance |
---|---|---|
Distribuição de Tamanho de Partículas | 5-250 µm | Affects powder flow and packing density |
Espessura da Camada | 20-100 µm | Influences surface finish and build time |
Potência do Laser | 200-400 W | Determines melting and sintering efficiency |
Taxa de construção | 10-50 cm³/h | Impacts production speed |
Densidade | 8.92 g/cm³ (pure copper) | Affects mechanical properties and performance |
Porosidade | < 0,5% | Impacts strength and durability |
Rugosidade da superfície | 5-15 µm | Influences post-processing requirements |
Advantages of Additive Manufacturing Copper
Additive manufacturing with copper presents numerous benefits that are driving its adoption across various industries. Let’s break down these advantages in detail.
High Electrical and Thermal Conductivity
Copper’s natural properties make it an excellent choice for components that require high electrical and thermal conductivity. This is particularly beneficial in the electronics and electrical industries, where copper is used for wiring, connectors, and heat sinks.
Flexibilidade de conceção
One of the biggest advantages of additive manufacturing is the ability to create complex geometries that are impossible with traditional methods. This design freedom allows for the creation of lightweight structures, intricate internal channels, and optimized shapes that enhance performance.
Eficiência dos materiais
Additive manufacturing is inherently more material-efficient than traditional subtractive methods. Since parts are built layer by layer, there is minimal waste, making the process more sustainable and cost-effective in the long run.
Customization and Rapid Prototyping
The ability to produce custom parts quickly is a significant advantage of additive manufacturing. This is particularly useful for prototyping, allowing for rapid iteration and testing of designs. Custom medical implants and specialized tooling are also key applications.
Propriedades Mecânicas Aprimoradas
Additively manufactured copper parts can exhibit excellent mechanical properties, such as high strength and durability. By optimizing the printing parameters, manufacturers can produce parts with superior performance characteristics tailored to specific applications.
Desvantagens de Fabrico aditivo Cobre
While additive manufacturing with copper offers many benefits, there are also challenges and limitations to consider.
Custos elevados
The cost of copper powders and additive manufacturing equipment can be high. This initial investment can be a barrier for small and medium-sized enterprises. Additionally, the cost per part can be higher compared to traditional manufacturing methods for large volume production.
Technical Challenges
Copper’s high reflectivity and thermal conductivity pose challenges in laser-based additive manufacturing processes. These properties can lead to issues with energy absorption and heat distribution, affecting the quality of the printed parts.
Requisitos de pós-processamento
Additively manufactured parts often require post-processing to achieve the desired surface finish and mechanical properties. This can include machining, heat treatment, and surface treatments, adding to the overall production time and cost.
Anisotropic Properties
Parts produced through additive manufacturing can exhibit anisotropic properties, meaning their mechanical properties can vary depending on the build direction. This can be a critical consideration in applications where uniform strength and performance are required.
Limited Scalability
While additive manufacturing is excellent for producing small to medium-sized parts, scaling up for larger production volumes can be challenging. The build size of additive manufacturing equipment is also limited, restricting the size of parts that can be produced.
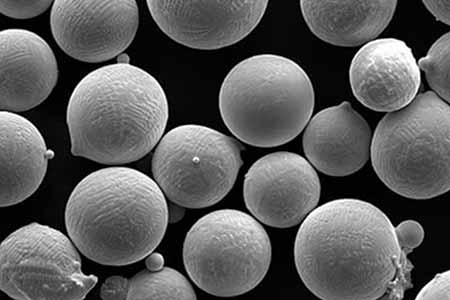
Perguntas Frequentes
Questão | Resposta |
---|---|
What is additive manufacturing with copper? | Additive manufacturing with copper involves creating parts layer by layer using copper metal powders. |
What are the benefits of using copper in additive manufacturing? | High electrical and thermal conductivity, design flexibility, material efficiency, and customization. |
What are the challenges of additive manufacturing with copper? | High costs, technical challenges with reflectivity, post-processing requirements, and limited scalability. |
Which industries benefit from copper additive manufacturing? | Aerospace, automotive, electronics, medical, marine, industrial, consumer products, and telecommunications. |
What are some common copper powders used in additive manufacturing? | CuCrZr, CuNi2SiCr, CuSn10, Cu-OF, CuNi10, CuCr1Zr, CuNi30, CuBe2, CuZn30, CuNi44. |
How does additive manufacturing compare to traditional methods? | Additive manufacturing offers design flexibility and material efficiency but can be more expensive for large volumes. |
What post-processing steps are required for additively manufactured copper parts? | Machining, heat treatment, and surface treatments to achieve desired finish and properties. |
Can additive manufacturing produce large copper parts? | Currently, the build size is limited, and scalability for large volumes is a challenge. |
Are additively manufactured copper parts as strong as traditionally manufactured ones? | They can be, depending on the process and post-processing, but may exhibit anisotropic properties. |
What is the future of additive manufacturing with copper? | The future looks promising with ongoing advancements in technology and materials improving capabilities and applications. |
Conclusão
Additive manufacturing with copper is a transformative technology that offers numerous benefits for a wide range of industries. From its excellent electrical and thermal properties to its design flexibility and material efficiency, copper is a valuable material in the world of 3D printing. However, it is essential to consider the challenges, such as high costs and technical difficulties, to fully leverage its potential.
As technology continues to advance, the applications and capabilities of additive manufacturing with copper are expected to grow, paving the way for innovative solutions and enhanced performance in various sectors. Whether you are in aerospace, automotive, electronics, or any other industry, understanding the intricacies of this process can help you make informed decisions and stay ahead in the rapidly evolving landscape of manufacturing.
Sobre a 3DP mETAL
Categoria do produto
CONTACTE-NOS
Tem dúvidas ? Envie uma mensagem para nós agora mesmo! Após o recebimento de sua mensagem, nós processaremos sua solicitação com toda a equipe.