Imagine a world where complex metal parts materialize layer-by-layer from a digital blueprint. This isn’t science fiction; it’s the reality of fabrico aditivo de alumínio (AM), also known as 3D printing for metals. This disruptive technology is transforming how we design, develop, and produce aluminum components, pushing the boundaries of what’s possible.
The Advantages of Aluminum Additive Manufacturing
Aluminum, prized for its lightweight strength and versatility, finds applications across countless industries. But traditional subtractive manufacturing, where material is removed from a solid block, has limitations. Aluminum AM overcomes these limitations in several exciting ways:
- Liberdade de conceção: Unleash your creativity! AM allows for intricate geometries, internal channels, and lattice structures impossible with conventional methods. This opens doors for lighter, stronger, and more efficient parts.
- Redução de resíduos: Traditional methods generate significant scrap metal. AM builds parts layer-by-layer, minimizing waste and promoting sustainability. Imagine the environmental impact of using less material!
- Prototipagem rápida: Gone are the days of lengthy and expensive prototypes. AM lets you create functional prototypes quickly and iterate on designs efficiently, accelerating the development process.
- Personalização em massa: AM excels at producing one-off or small-batch parts with minimal setup costs. Imagine customizing components for individual needs or creating specialized tools for specific applications.
- Complex Internal Features: AM allows for intricate internal features like channels and lattices within a single piece. This eliminates the need for complex assembly processes and reduces part count.
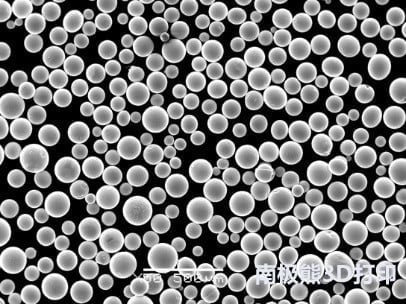
As aplicações de Fabrico aditivo de alumínio
The potential applications of aluminum AM are vast and constantly expanding. Here are some key areas where it’s making a significant impact:
- Aeroespacial: Weight reduction is paramount in airplanes. AM is enabling the creation of lightweight, high-strength aluminum components for airframes, reducing fuel consumption and increasing flight range.
- Automotivo: From lightweight chassis components to intricate engine parts, AM is helping automakers design next-generation vehicles with improved performance and fuel efficiency.
- Dispositivos médicos: Custom implants, prosthetics, and surgical tools tailored to individual patients are becoming a reality with AM. This technology is leading to personalized medical care with improved patient outcomes.
- Bens de consumo: Imagine custom bike frames, lightweight running shoes with built-in cushioning, or intricate jewelry designs – AM is opening doors for innovative and personalized consumer products.
Beyond these sectors, aluminum AM has applications in:
- Robotics: Creating customized grippers, lightweight robotic arms, and complex end-of-arm tooling.
- Defense: Manufacturing lightweight armor components, heat sinks, and other functional parts.
- Construction: Developing customized building components and architectural elements.
As the technology matures and costs decrease, we can expect even more groundbreaking applications of aluminum AM across various industries.
As características de Fabrico aditivo de alumínio
Understanding the process behind aluminum AM is crucial to appreciating its capabilities. Here’s a breakdown of the key aspects:
- Printing Techniques: Several AM techniques can be used with aluminum, with the most common being:
- Laser Powder Bed Fusion (LPBF): A high-powered laser melts aluminum powder layer-by-layer to build the desired part. Offers high accuracy and detail but can be expensive.
- Fusão por feixe de electrões (EBM): Similar to LPBF but uses an electron beam for melting, enabling processing of reactive materials like aluminum. Offers high strength but has a limited build volume.
- Jato de ligante: A binder material is deposited on a powder bed, selectively bonding the aluminum particles. Offers lower cost but with limitations in part strength and surface finish.
- Ligas de alumínio: Not all aluminum alloys are created equal for AM. Specific alloys are developed with good printability, meaning they flow well and minimize cracking during the printing process. Common choices include AlSi10Mg, AA2024, and Scalmalloy.
- Pós-processamento: Similar to traditional manufacturing, AM parts often require post-processing steps like heat treatment, support structure removal, and surface finishing to achieve the desired mechanical properties and aesthetics.
Here’s an analogy to understand the process: Imagine building a structure with tiny Lego bricks. Each brick represents a layer of aluminum powder, and the laser acts like a magic wand that selectively fuses these layers together, following a digital blueprint, to create the desired 3D object.
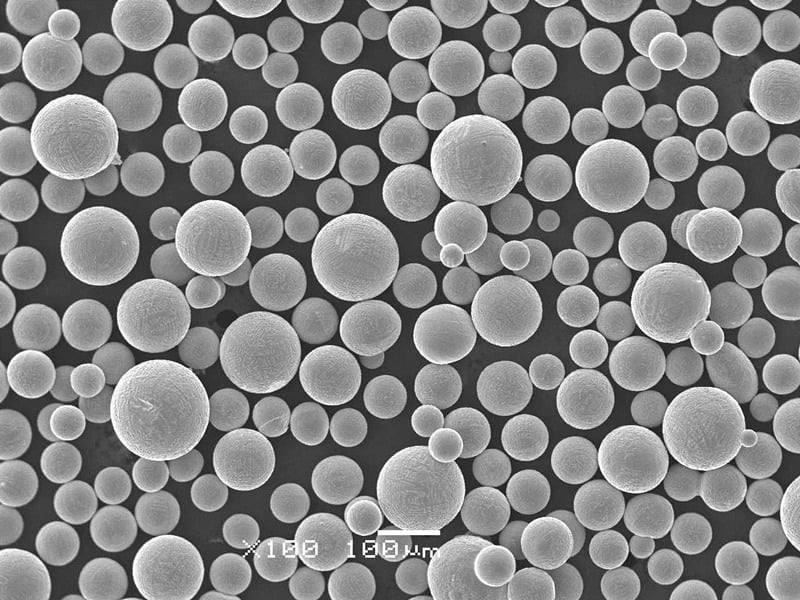
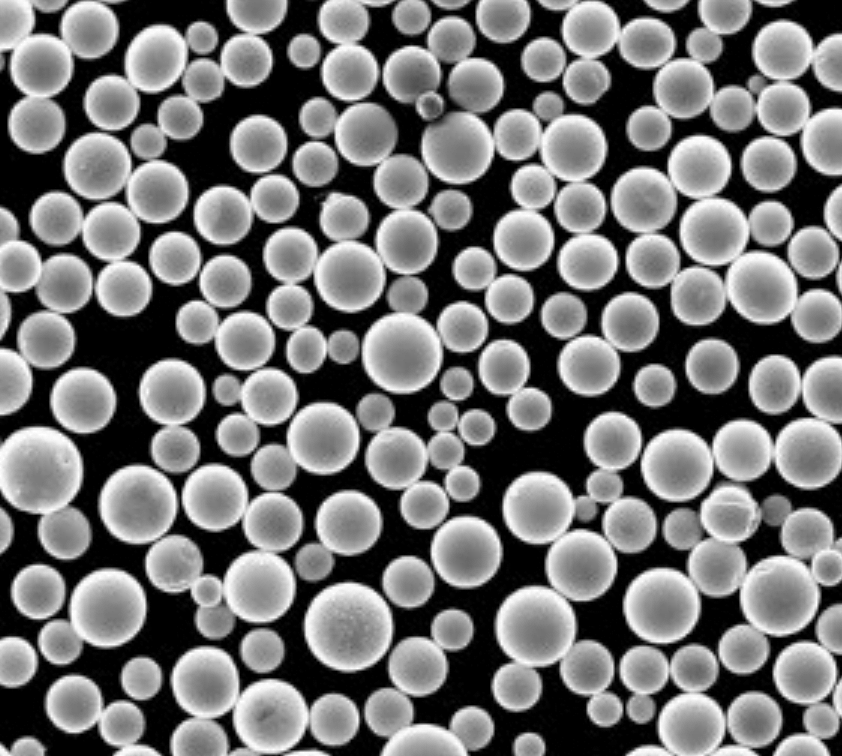
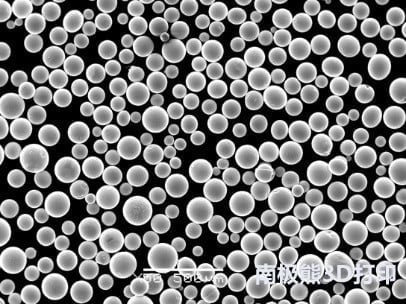
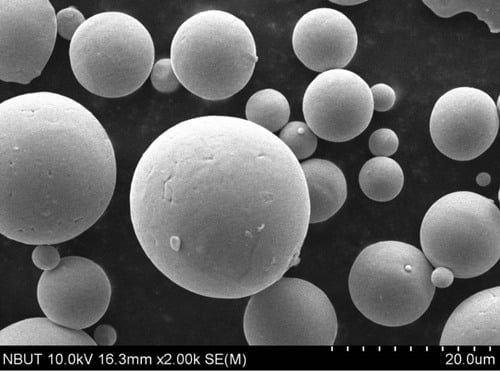
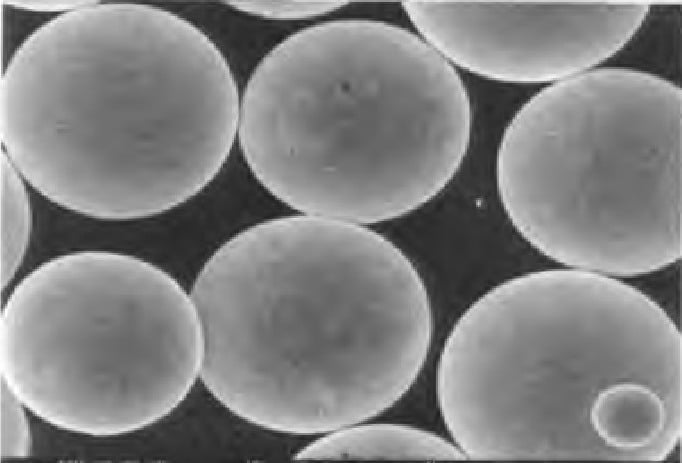
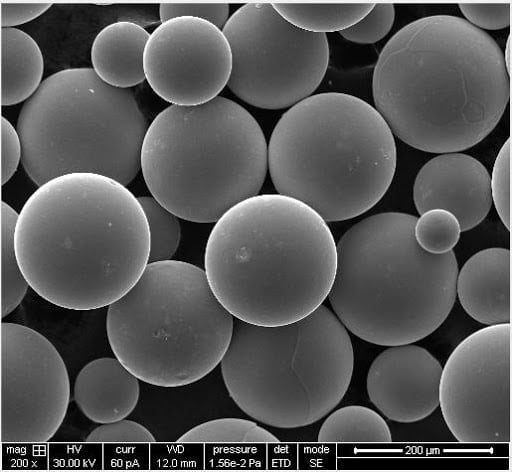
Challenges and Considerations in Fabrico aditivo de alumínio
Despite its immense potential, aluminum AM isn’t without its challenges:
- Custo: AM machines and aluminum powders can be expensive compared to traditional manufacturing methods. However, as the technology matures, costs are expected to decrease.
- Rugosidade da superfície: Parts produced through AM can have a rougher surface finish compared to traditionally machined components. This might require additional post-processing steps like polishing or machining for certain applications.
- Residual Stress: The rapid heating and cooling cycles during the printing process can introduce residual stress within the part. This can affect its mechanical properties and needs to be managed through proper process control and potentially, heat treatment.
- Limitações de tamanho da peça: Current AM machines have limitations on the size of parts they can produce. This might not be suitable for large-scale industrial applications yet.
- Especialização em design: Designing for AM requires a different mindset compared to traditional methods. Engineers need to understand the capabilities and limitations of the technology to optimize designs for successful printing.
However, these challenges are being actively addressed by researchers and manufacturers. Advancements in printing techniques, material science, and post-processing methods are continuously improving the capabilities and cost-effectiveness of aluminum AM.
Material Considerations for Aluminum Additive Manufacturing
The choice of aluminum alloy is crucial for successful printing and achieving the desired part properties. Here are some key factors to consider:
- Imprimibilidade: The powder needs to flow well and have good laser or electron beam absorption for proper melting and bonding.
- Propriedades mecânicas: Different alloys offer varying strengths, ductility, and fatigue resistance. Selecting the right alloy depends on the application’s specific requirements.
- Tratamento térmico: Some alloys benefit from heat treatment after printing to optimize their mechanical properties.
Here’s a table summarizing some commonly used aluminum alloys for AM, along with their key characteristics:
Alloy Designation | Capacidade de impressão | Força | Ductilidade | Heat Treatable | APLICAÇÕES |
---|---|---|---|---|---|
AlSi10Mg | Excelente | Bom | Moderada | Sim | Aerospace components, automotive parts, general-purpose applications |
AA2024 | Bom | Alto | Baixo | Sim | Aerospace components, high-strength parts |
Scalmalloy | Excelente | Muito alto | Baixo | Sim | High-performance applications, demanding aerospace and motorsports components |
AlSi7Mg0.6 | Bom | Moderada | Bom | Sim | Automotive parts, heat exchangers |
Remember, this table is not exhaustive, and new alloys are constantly being developed specifically for AM. Consulting with a materials expert is crucial for selecting the optimal aluminum alloy for your specific project requirements.
O futuro da Fabrico aditivo de alumínio
The future of aluminum AM is bright and brimming with possibilities. Here are some exciting trends to watch for:
- Custos reduzidos: Advancements in technology and wider adoption are expected to drive down the cost of AM machines and aluminum powders, making it more accessible for a broader range of applications.
- Impressão multi-material: The ability to print parts with multiple materials within a single build is on the horizon. This opens doors for components with unique combinations of properties, like a lightweight core structure with a high-strength outer shell.
- Hybrid Manufacturing: Integrating AM with traditional subtractive manufacturing techniques allows for combining the best of both worlds. Imagine creating a complex internal structure through AM and then machining the outer surface for a precise finish.
- Standardization: As the industry matures, we can expect increased standardization of printing processes and materials, improving quality control and repeatability.
Aluminum AM is not just a new technology; it’s a paradigm shift in manufacturing. It empowers designers and engineers to push the boundaries of creativity and functionality. As these trends unfold, we can expect even more revolutionary applications of aluminum AM that will shape the future of various industries.
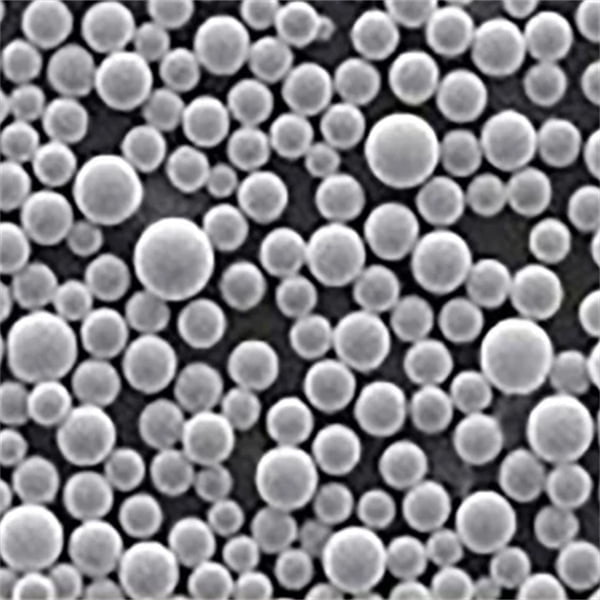
Perguntas Frequentes
Eis algumas perguntas frequentes sobre fabrico aditivo de alumínio:
P: Quais são as vantagens da AM de alumínio em comparação com o fabrico tradicional?
A: Aluminum AM offers several advantages, including design freedom, reduced waste, rapid prototyping, mass customization, and the ability to create complex internal features.
Q: What are the different types of aluminum AM processes?
A: The most common techniques are Laser Powder Bed Fusion (LPBF), Electron Beam Melting (EBM), and Binder Jetting. Each technique has its own advantages and limitations.
Q: What are some of the challenges associated with aluminum AM?
A: Challenges include cost, surface roughness, residual stress, part size limitations, and the need for design expertise specific to AM.
Q: What factors should be considered when choosing an aluminum alloy for AM?
A: Printability, mechanical properties, and heat treatment options are all crucial factors to consider when selecting an aluminum alloy for AM.
Q: What does the future hold for aluminum AM?
A: The future is bright! We can expect reduced costs, multi-material printing, hybrid manufacturing.
Sobre a 3DP mETAL
Categoria do produto
CONTACTE-NOS
Tem dúvidas ? Envie uma mensagem para nós agora mesmo! Após o recebimento de sua mensagem, nós processaremos sua solicitação com toda a equipe.