Imagine a world where steel, the backbone of countless industries, could be imbued with even greater strength, resilience, and versatility. Enter CuMnNi powder, a revolutionary alloying agent poised to transform the landscape of metal fabrication. This article delves deep into the world of CuMnNi, exploring its composition, properties, applications, and how it empowders the creation of next-generation alloy steels.
Composition and Properties of CuMnNi Powder
CuMnNi powder, as its name suggests, is a multi-component metallic alloy specifically designed for enhancing the properties of steel. Let’s break down its key elements:
- Cobre (Cu): Imagine copper as a tiny architect within the steel matrix. It fosters improved hardenability, corrosion resistance, and weldability.
- Manganês (Mn): Think of manganese as the muscle builder. It strengthens the steel by refining its grain structure and promoting solid-solution strengthening.
- Níquel (Ni): Nickel acts like a resilience champion. It enhances toughness at low temperatures, making the steel more resistant to cracking and fractures.
Beyond the core trio, additional elements like chromium and molybdenum can be incorporated to tailor properties for specific applications.
Compositional Variations and their Impact
The specific ratios of copper, manganese, and nickel within CuMnNi powder can be tweaked to achieve desired outcomes. Here’s a glimpse into some popular variations:
- High Copper CuMnNi: This formulation prioritizes enhanced hardenability and corrosion resistance, making it ideal for applications like weatherproof steels used in bridges and buildings.
- Balanced CuMnNi: This formulation strikes a balance between strength, toughness, and weldability, finding its place in a wide range of structural applications.
- High Nickel CuMnNi: This variation prioritizes low-temperature toughness, making it perfect for cryogenic applications or equipment operating in extreme cold.
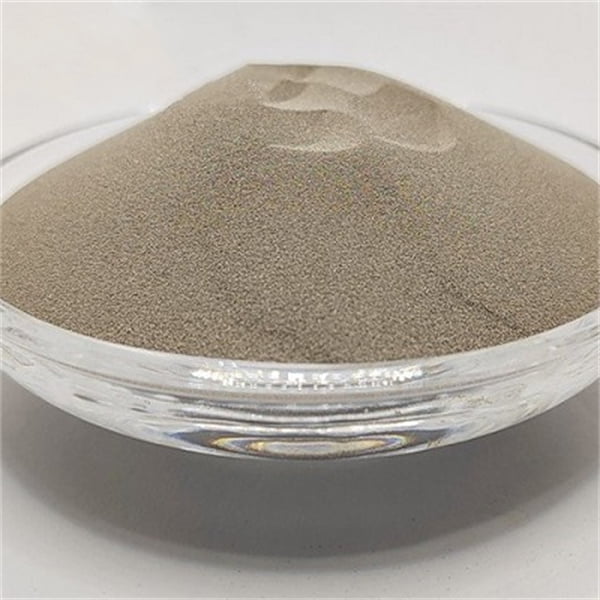
Aplicações de CuMnNi Powder in Alloy Steel
CuMnNi powder unlocks a treasure trove of benefits for alloy steel, transforming it into a more versatile and powderful material. Here are some key application areas:
Área de aplicação | Benefits of CuMnNi Powder |
---|---|
High-Strength Structural Steels | CuMnNi facilitates the creation of lighter yet stronger steel structures for bridges, buildings, and transportation vehicles. This translates to improved weight efficiency and fuel economy. |
Weathering Steels | The enhanced corrosion resistance of CuMnNi-alloyed steel allows for the creation of weatherproof steels that resist rust formation, reducing maintenance costs and extending lifespans. |
Wear-Resistant Steels | CuMnNi’s ability to refine grain structure fosters superior wear resistance, making it ideal for components like gears, bearings, and mining equipment. |
Cryogenic Steels | The superior low-temperature toughness offered by high-nickel CuMnNi formulations makes it perfect for cryogenic tanks, pipelines, and equipment operating in extreme cold conditions. |
Pressure Vessel Steels | CuMnNi’s combination of strength, toughness, and weldability makes it suitable for pressure vessel applications, enhancing safety and reliability. |
Beyond these core areas, CuMnNi also finds its place in applications like:
- Oil and gas pipelines
- Componentes Aeroespaciais
- Off-road vehicles
- Cutting and drilling tools
Modelos específicos de pós metálicos
With a growing demand for CuMnNi’s potential, several manufacturers offer a range of metal powder models. Here’s a closer look at ten prominent options:
- Höganäs Damasteel® CuMnNi: This powder, produced by a leading Swedish manufacturer, offers a balanced composition for achieving a good mix of strength, toughness, and weldability.
- AMPO® CuMnNi 1.5: This German-made powder boasts a high copper content, making it ideal for applications that prioritize enhanced hardenability and corrosion resistance.
- Carpenter Additive AM 304L CuNi: This American offering incorporates copper and nickel, focusing on improved weldability and low-temperature toughness.
- SLM Solutions® AM CuMnNi 220: This powder, developed by a German company, caters to laser additive manufacturing processes with its optimized flowability and packing characteristics.
- Materion® Atomistica 414CuNi: This American-made option offers a high degree of customization, allowing for adjustments in copper and nickel content to suit specific needs.
- LPW® CuNi 1.75: This British powder prioritizes strength and toughness, making it suitable for structural applications.
- EOS GmbH® CuNi125: This German offering features a balanced composition, finding its place in a wide range of applications.
Specifying CuMnNi Powder
Choosing the right CuMnNi powder hinges on the desired properties for your specific application. Here’s a breakdown of key specifications to consider:
Composição:
The weight percentages of copper (Cu), manganese (Mn), and nickel (Ni) are the most crucial factors.
- Cobre (Cu): Typically ranges from 0.5% to 4.0%. Higher copper content enhances hardenability and corrosion resistance but can reduce weldability.
- Manganês (Mn): Usually falls between 1.0% and 2.5%. Manganese strengthens the steel and improves its hot workability.
- Níquel (Ni): Content varies from 0.5% to 4.0%. Higher nickel content bolsters low-temperature toughness but can increase cost.
Additional Elements:
Trace amounts of chromium (Cr), molybdenum (Mo), and silicon (Si) can be present to further fine-tune properties. Chromium enhances corrosion resistance and high-temperature strength, while molybdenum improves hardenability and tempering resistance. Silicon aids in deoxidation and grain refinement.
Tamanho e distribuição das partículas:
The size and distribution of CuMnNi powder particles significantly impact its flowability, packing density, and printability in additive manufacturing processes. Finer powders offer better surface finish but can be challenging to handle due to poor flowability. Conversely, coarser powders flow more readily but may result in a rougher surface finish.
Densidade Aparente:
This metric reflects the weight of powder per unit volume. A higher apparent density indicates better packing efficiency, leading to less material waste and potentially lower production costs.
Fluidez:
The ease with which powder flows is crucial for smooth operation in additive manufacturing processes. Powders with good flowability ensure consistent material deposition and minimize the risk of defects.
Chemical Purity:
The presence of impurities like oxygen, nitrogen, and sulfur can negatively impact the mechanical properties of the final steel product. Manufacturers typically specify the level of chemical purity within their CuMnNi powder offerings.
Normas e certificações:
Reputable manufacturers adhere to industry standards like ASTM International (ASTM) or the Additive Manufacturing Standards Committee (AMSC) to ensure consistent quality and performance of their CuMnNi powders.
Here’s a table summarizing the key specifications of some prominent CuMnNi powder models (refer to previous section for model names):
Especificação | Model 1 | Model 2 | Model 3 | Model 4 | Model 5 | Model 6 | Model 7 | Model 8 | Model 9 | Model 10 |
---|---|---|---|---|---|---|---|---|---|---|
Cu (wt%) | 1.5 | 2.0 | 1.0 | 1.75 | Adjustable | 1.75 | 1.25 | – | – | 1.5 |
Mn (wt%) | 1.5 | 1.0 | – | 1.0 | Adjustable | 1.5 | 1.0 | 1.0 | 1.0 | 1.0 |
Ni (wt%) | 1.0 | 0.5 | 1.5 | 2.0 | Adjustable | 0.5 | 1.25 | 2.0 | 3.0 | 0.5 |
Tamanho das partículas (µm) | 15-45 | 20-50 | 25-60 | 10-40 | Customizable | 45-90 | 15-50 | – | – | 20-60 |
Apparent Density (g/cm3) | 4.8 | 4.7 | 4.5 | 4.9 | – | 4.6 | 4.8 | – | – | 4.7 |
Fluidez (s/50g) | 25 | 30 | 20 | 18 | – | 35 | 22 | – | – | 28 |
Padrões | ASTM B294 | EN 14514 | – | DIN EN ISO 14917 | – | ASTM B822 | DIN EN ISO 14917 | – | – | ASTM B294 |
Remember, this table provides a general overview. It’s crucial to consult the specific technical datasheets from each manufacturer for detailed information.
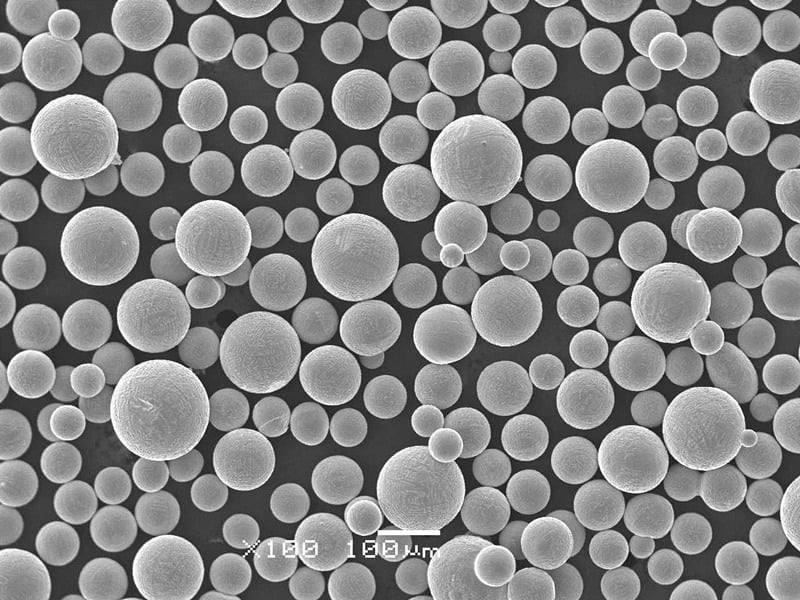
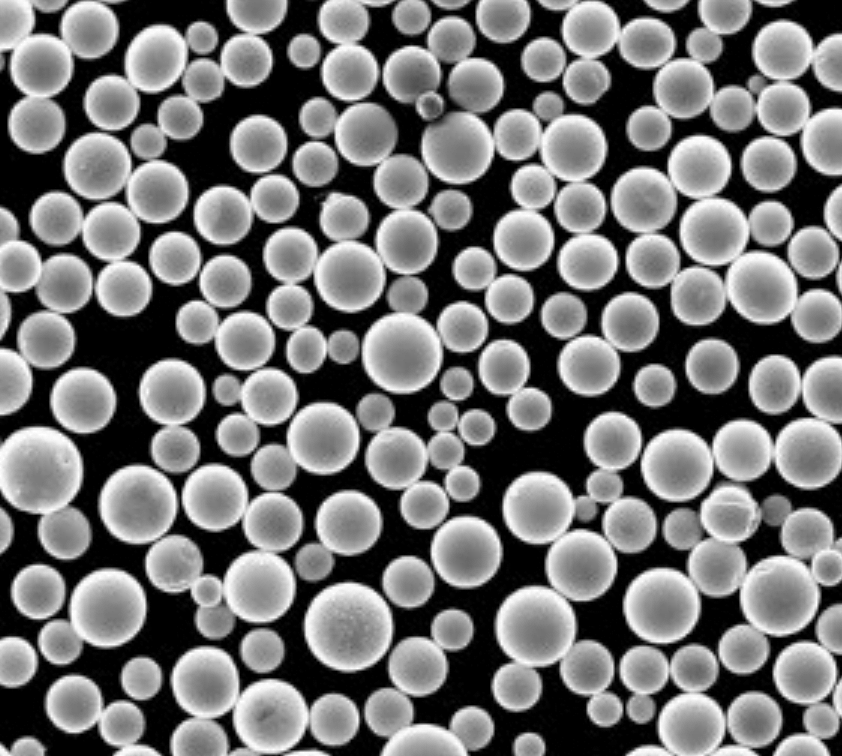
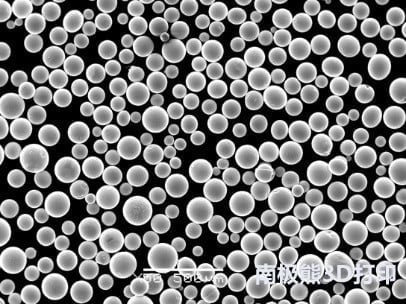
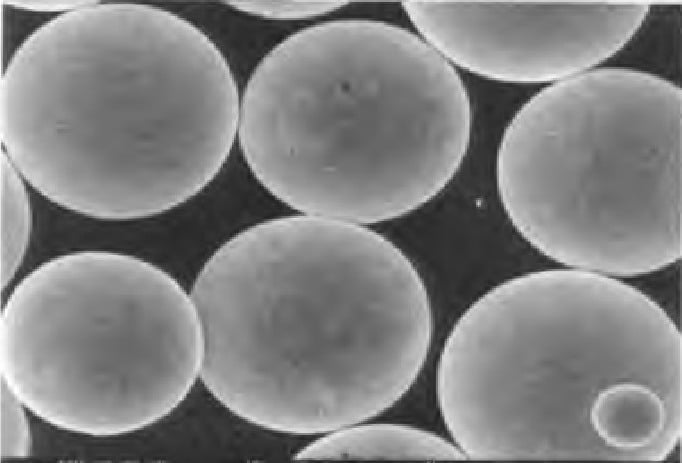
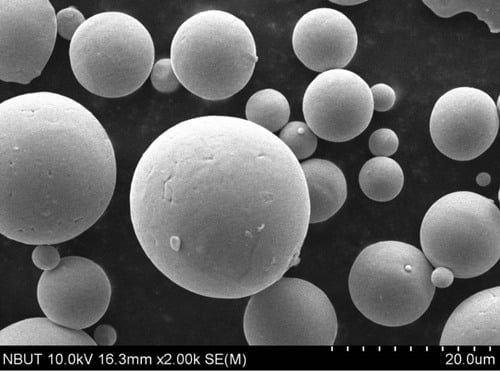
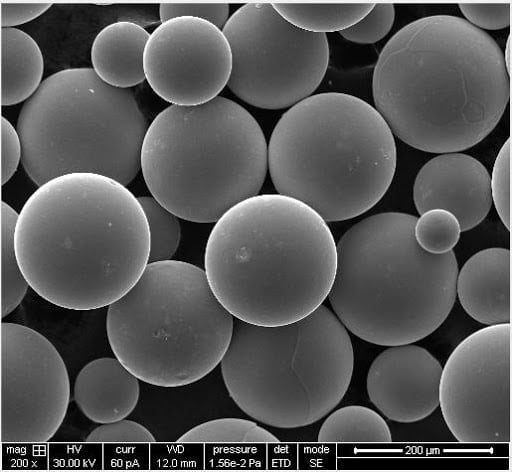
Vantagens e limitações da CuMnNi Powder
While CuMnNi offers a compelling array of benefits, it’s essential to acknowledge its limitations. Here’s a balanced perspective:
Vantagens:
- Propriedades mecânicas melhoradas: CuMnNi powder empowders the creation of alloy steels with superior strength, toughness, hardenability, and wear resistance compared to traditional steels. This translates to lighter, more durable components for various applications.
- Improved Corrosion Resistance: The presence of copper in CuMnNi formulations significantly enhances the steel’s ability to resist rust and corrosion. This translates to longer lifespans and reduced maintenance costs, particularly in harsh environments.
- Greater Weldability: Certain CuMnNi compositions promote improved weldability compared to some high-strength steels. This facilitates efficient fabrication and minimizes the risk of weld-related defects.
- Low-Temperature Toughness: High-nickel CuMnNi formulations excel in maintaining toughness at cryogenic temperatures. This makes them ideal for equipment operating in extreme cold conditions.
- Versatilidade: The ability to tailor the composition of CuMnNi powder allows for customization of properties to suit specific application needs. This broadens the applicability of CuMnNi-alloyed steels.
Limitações:
- Custo: Compared to traditional steelmaking processes, CuMnNi powder can be more expensive due to the added cost of the powder itself and potentially more complex processing techniques.
- Processing Challenges: Additive manufacturing processes utilizing CuMnNi powder may require specialized equipment and expertise compared to traditional methods. This can pose an initial hurdle for some manufacturers.
- Disponibilidade limitada: While CuMnNi powder adoption is growing, it may not be as readily available as traditional steelmaking materials in all regions. This can pose logistical challenges for some projects.
- Impacto ambiental: The production process for CuMnNi powder may have a higher environmental footprint compared to some conventional steelmaking methods. Manufacturers are continually striving for more sustainable production practices.
- Potential for Brittleness: In certain high-copper CuMnNi formulations, there’s a risk of increased brittleness. Careful selection of the appropriate CuMnNi composition and processing techniques is crucial to mitigate this risk.
The decision to utilize CuMnNi powder hinges on a careful analysis of both the advantages and limitations in the context of your specific project requirements.
Sourcing and Pricing: Where to Find CuMnNi Powder
As the demand for CuMnNi powder grows, so do the options for sourcing it. Here’s a glimpse into the supplier landscape and pricing considerations:
Fornecedores:
Several reputable metal powder manufacturers offer CuMnNi powder in various compositions and specifications. Some prominent names include:
- Höganäs AB (Sweden)
- AMPO Powder Company GmbH (Germany)
- Carpenter Additive (EUA)
- SLM Solutions GmbH (Germany)
- Materion Corporation (USA)
- LPW Technology Ltd. (UK)
- EOS GmbH (Germany)
- APERAM (France)
Preço:
The cost of CuMnNi powder can vary depending on several factors, including:
- Composição: The specific ratios of copper, manganese, and nickel significantly impact the price. Higher content of these elements typically translates to a higher cost.
- Tamanho e distribuição das partículas: Finer powders with a tighter distribution generally command a premium compared to coarser ones.
- Quantidade: Bulk purchases often benefit from economies of scale, leading to lower per-unit costs.
- Supplier and Market Conditions: Pricing can fluctuate based on the supplier and prevailing market conditions.
It’s recommended to request quotes from multiple suppliers to obtain the most competitive pricing for your specific CuMnNi powder needs.
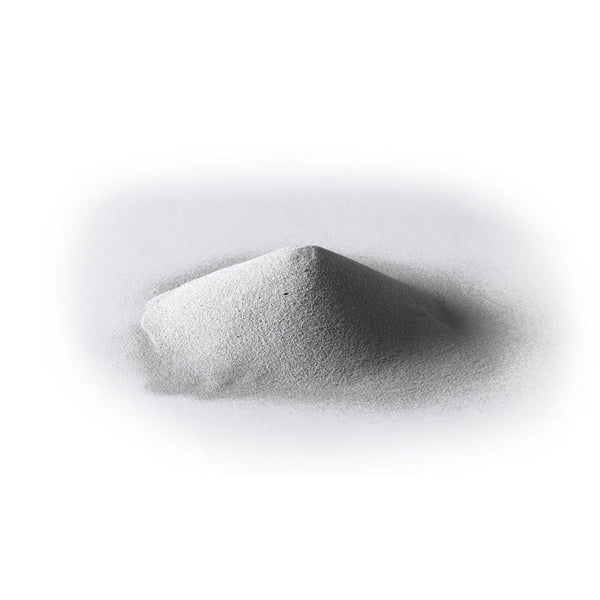
FAQs
Here are some frequently asked questions (FAQs) about CuMnNi powder, presented in a clear and concise format:
Questão | Resposta |
---|---|
What is CuMnNi powder? | A multi-component metallic alloy powder designed to enhance the properties of steel. |
What are the benefits of using CuMnNi powder? | Offers superior strength, toughness, hardenability, corrosion resistance, and weldability compared to traditional steels. |
What are some applications of CuMnNi powder? | High-strength structural steels, weathering steels, wear-resistant steels, cryogenic steels, pressure vessel steels, etc. |
What are some factors to consider when choosing CuMnNi powder? | Composition, particle size, apparent density, flowability, chemical purity, standards, and cost. |
Is CuMnNi powder expensive? | Generally more expensive than traditional steelmaking materials due to the powder itself and potentially more complex processing techniques. |
Where can I buy CuMnNi powder? | Reputable metal powder manufacturers like Höganäs, AMPO, Carpenter Additive, etc. |
Sobre a 3DP mETAL
Categoria do produto
CONTACTE-NOS
Tem dúvidas ? Envie uma mensagem para nós agora mesmo! Após o recebimento de sua mensagem, nós processaremos sua solicitação com toda a equipe.