Pó CuSnPNi, a captivating blend of copper (Cu), tin (Sn), phosphorus (P), and nickel (Ni), has emerged as a revolutionary force within the realm of Powder Metallurgy (PM). Imagine crafting intricate metal components not by traditional subtractive methods like machining, but by building them layer by layer from a magical metallic dust – that’s the essence of PM. CuSnPNi powder steps into this arena, offering a unique set of properties that make it a game-changer for countless applications.
Composição, propriedades e características
Componente | Peso % | Propriedades principais |
---|---|---|
Cobre (Cu) | Equilíbrio | – Excellent thermal and electrical conductivity <br> – High ductility and workability |
Estanho (Sn) | 6-8 | – Improves wettability and sintering characteristics <br> – Enhances corrosion resistance |
Fósforo (P) | 0.5-1.5 | – Promotes solid-state sintering at lower temperatures <br> – Strengthens grain boundaries |
Níquel (Ni) | 0.5-2.0 | – Increases strength and hardness <br> – Enhances wear resistance |
This synergistic blend of elements imbues CuSnPNi powder with a remarkable cocktail of properties:
- Superior Sinterability: Compared to pure copper powder, CuSnPNi achieves exceptional density and mechanical strength at significantly lower sintering temperatures (around 750-850°C). This translates to energy savings, reduced distortion in complex shapes, and the ability to integrate heat-sensitive components into the PM process.
- Enhanced Mechanical Performance: The presence of nickel boosts the strength and hardness of CuSnPNi parts, making them ideal for applications demanding robustness and wear resistance. Imagine intricate gears, bearings, and electrical contacts crafted from CuSnPNi, withstanding the rigors of daily operation.
- Excellent Conductivity: Copper remains the dominant element, ensuring that CuSnPNi retains its impressive thermal and electrical conductivity. This makes it a perfect choice for heat sinks, electrical connectors, and electromagnetic components, where efficient heat dissipation and current flow are critical.
- Resistência à corrosão: The addition of tin bolsters CuSnPNi’s resistance to corrosion, particularly in environments where oxidation and degradation pose a threat. Think of intricate components used in marine applications, plumbing systems, or even architectural elements facing harsh weather conditions.
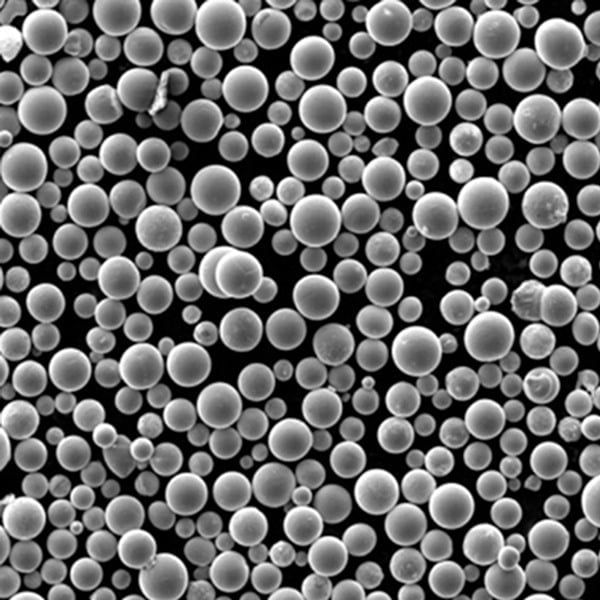
Aplicações de Pó CuSnPNi
The versatility of CuSnPNi powder translates into a vast array of applications across diverse industries:
Indústria | APLICAÇÕES | Considerações fundamentais |
---|---|---|
Automotivo | – Bushings, bearings, gears, and electrical connectors | – High wear resistance and fatigue strength are crucial. – Conductivity for efficient heat dissipation in engine components is essential. |
Eletrônica | – Heat sinks, EMI/RFI shielding components, and electrical connectors | – Excellent thermal conductivity and electrical conductivity are paramount. – Precise control of electrical properties might be required for specific applications. |
Aeroespacial e Defesa | – Structural components, waveguides, and heat sinks | – Lightweight yet robust materials are preferred. – High strength and excellent conductivity are often critical. |
bens de consumo | – Gears for appliances, plumbing components, and connectors | – Durability, corrosion resistance, and affordability are key factors. – Formability might be important for creating intricate shapes. |
Specific CuSnPNi Powder Models
While CuSnPNi powder boasts a core composition, various manufacturers offer specific models with slight variations in their make-up and properties. Let’s delve into a few prominent examples:
- Höganäs AMPCOLOY™ 460: This popular model boasts a well-balanced composition (Cu-6Sn-0.5P-1.0Ni) and is renowned for its exceptional sinterability and high mechanical strength. It’s a versatile choice for a wide range of PM applications.
- Carpenter Brother CTP™ 100: This model (Cu-7Sn-0.7P-1.5Ni) prioritizes strength and wear resistance with a slightly higher nickel content. It excels in applications demanding robust performance, such as gears and bearings.
- GKN Hoeganaes AMLS™ 92: This copper-tin-phosphorus alloy (Cu-8Sn-1.0P) prioritizes excellent sinterability and conductivity at even lower temperatures (around 700°C). It’s ideal for applications requiring intricate shapes or integration with heat-sensitive components.
- AMPCOLOY™ 415M: This model (Cu-4Sn-0.5P-1.5Ni) from Höganäs offers a slightly lower tin content compared to the 460 model. This translates to improved conductivity while maintaining good sinterability and mechanical strength. It’s a suitable choice for applications where both electrical performance and robustness are important.
- AMPCOLOY™ C7500: This specialty model from Höganäs (Cu-4Sn-0.7P-2.0Ni) prioritizes superior strength and wear resistance with a higher nickel content. Think of demanding applications like high-performance gears or wear pads.
- Arcop™ 1200: This model from Carpenter Brother (Cu-8Sn-1.0P-1.0Ni) offers a good balance between sinterability, strength, and conductivity. It’s a versatile choice for various PM applications, particularly those requiring a balance of properties.
- SCu-4Sn-1P: This model from BASF (Cu-4Sn-1.0P) prioritizes excellent conductivity with a lower nickel content compared to other models. It’s ideal for applications where electrical performance is paramount, such as high-frequency connectors or electromagnetic components.
- AMPCOLOY™ CB025: This specialty model from Höganäs (Cu-0.5Sn-0.5P-0.5Ni) boasts a very low tin content. While its sinterability might be slightly lower compared to other models, it offers exceptional conductivity, making it perfect for applications demanding the highest electrical performance, such as high-speed electronics or microwave components.
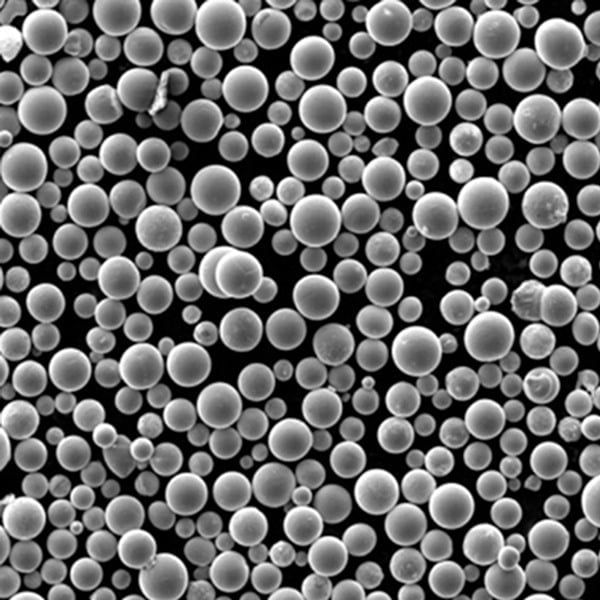
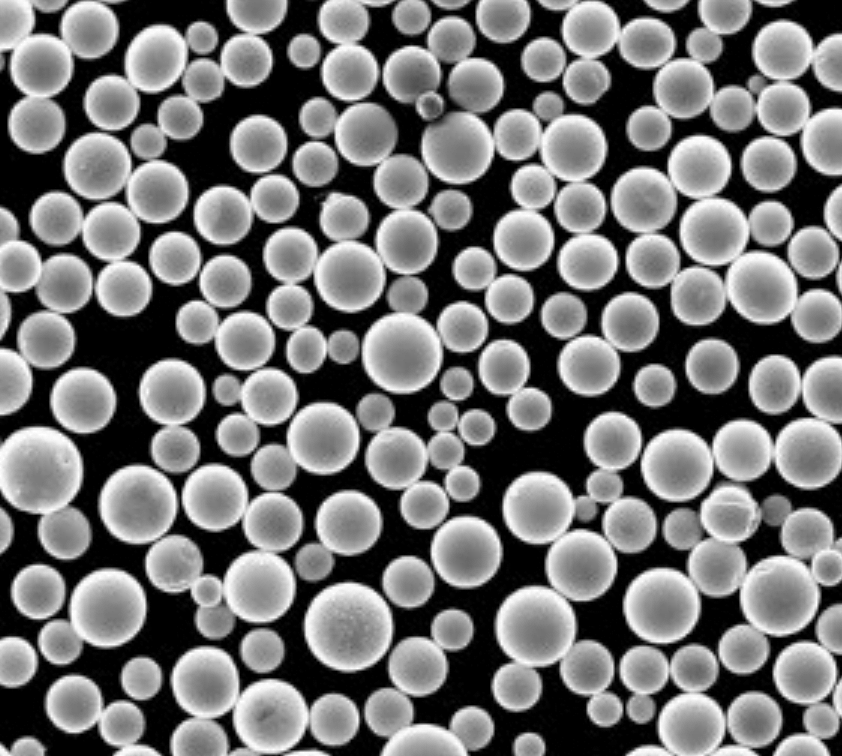
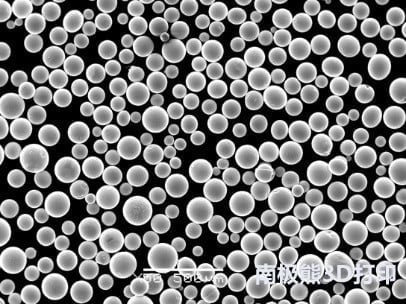
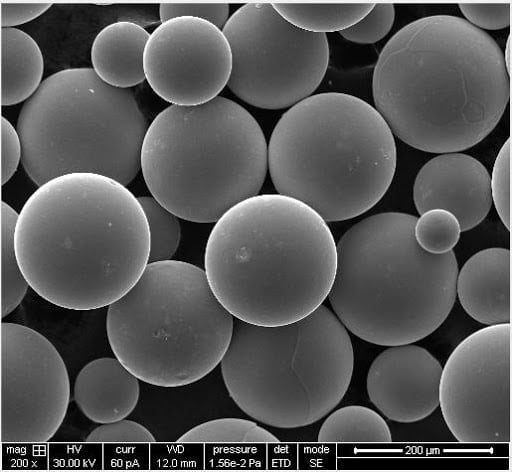
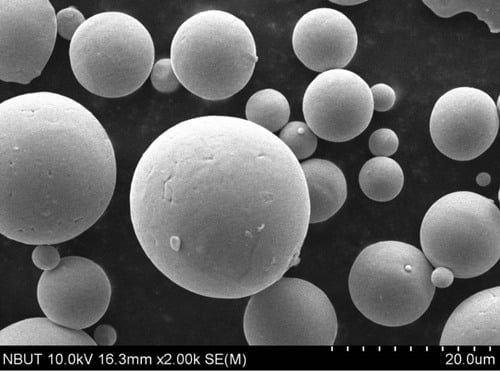
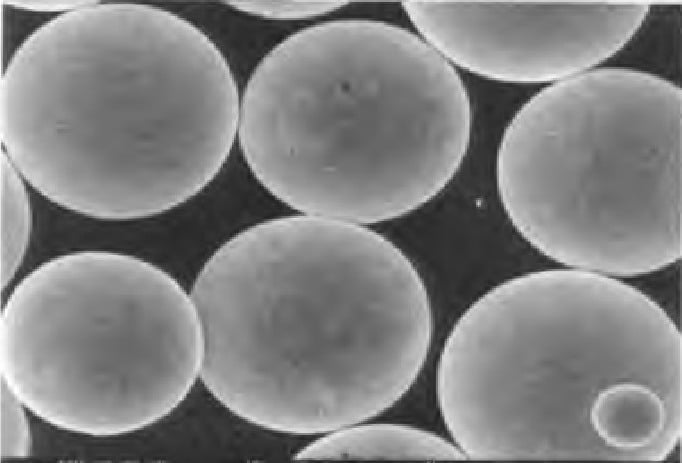
os prós e contras de CuSnPNi Powder
Like any material, CuSnPNi powder comes with its own set of advantages and limitations:
Vantagens:
- Superior Sinterability: Lower sintering temperatures translate to energy savings, reduced distortion, and broader compatibility with heat-sensitive components.
- Enhanced Mechanical Performance: Increased strength, hardness, and wear resistance make it ideal for demanding applications.
- Excellent Conductivity: Retained conductivity from copper makes it perfect for heat dissipation and electrical applications.
- Resistência à corrosão: Improved resistance to corrosion extends the lifespan of components.
- Versatilidade: A wide range of applications across various industries.
Desvantagens:
- Custo: Compared to pure copper powder, CuSnPNi can be slightly more expensive due to the additional elements.
- Maquinabilidade: While generally good, machinability might be slightly lower compared to pure copper, requiring adjustments in machining processes for some applications.
- Oxidation Potential: At very high temperatures, the copper component can oxidize. Careful process control during PM is necessary to minimize this effect.
The Final Verdict: A Material for the Future
CuSnPNi powder stands as a testament to the power of material science. Its unique combination of properties and versatility positions it as a game-changer in the realm of Powder Metallurgy. From robust gears in automobiles to intricate heat sinks in electronics, CuSnPNi is shaping the future of countless industries. As research and development continue, we can expect even more refined Pó CuSnPNi models with tailored properties, further expanding its reach and impact.
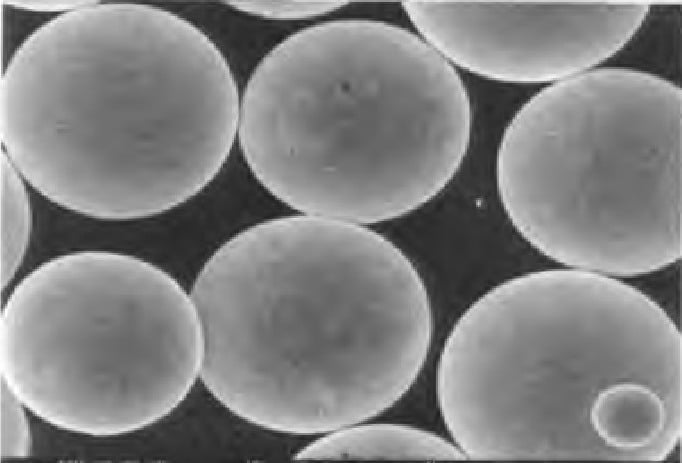
Perguntas Frequentes
Questão | Resposta |
---|---|
What are the typical particle sizes of CuSnPNi powder? | CuSnPNi powder typically comes in a range of particle sizes, from around 10 to 150 microns. The specific size chosen depends on the desired properties and application. Finer particles generally promote better sinterability but might require higher processing pressures. |
Can CuSnPNi powder be recycled? | Yes, CuSnPNi powder exhibits excellent recyclability. Scrap parts or excess powder can be reintroduced into the PM process, minimizing waste and promoting sustainability. |
How does CuSnPNi powder compare to other copper-based PM materials? | CuSnPNi offers a significant advantage in terms of sinterability compared to pure copper powder. It achieves higher density and mechanical strength at lower temperatures. Compared to other copper alloys used in PM, CuSnPNi offers a good balance between properties like strength, conductivity, and corrosion resistance. The specific choice depends on the application’s priorities. |
Where can I find suppliers of CuSnPi powder? | Several leading metal powder manufacturers offer CuSnPNi powder. Some prominent examples include Höganäs, Carpenter Brother, and BASF. |
Sobre a 3DP mETAL
Categoria do produto
CONTACTE-NOS
Tem dúvidas ? Envie uma mensagem para nós agora mesmo! Após o recebimento de sua mensagem, nós processaremos sua solicitação com toda a equipe.