In the realm of spray coating, where durability and precision reign supreme, H13 tool steel power emerges as a champion. This robust material isn’t just another pretty face in the machine shop; it’s a workhorse, consistently delivering exceptional performance for a wide range of coating applications. But what exactly makes H13 such a powerful ally in the world of sprayed-on protection? Buckle up, because we’re about to delve into the fascinating world of H13 and its dominance in spray coating.
Composição de Potência do aço ferramenta H13
Imagine a material forged from a blend of iron, chromium, molybdenum, and vanadium. That’s the essence of H13 tool steel. This potent combination imbues H13 with a cocktail of desirable properties:
- Superior Hot Hardness: Think of a knight’s armor, withstanding the scorching heat of battle. H13 boasts similar resilience, retaining its strength and shape even when temperatures soar. This makes it ideal for applications involving hot work processes, like thermal spraying.
- Excellent Wear Resistance: Picture a shield deflecting blows time and again. H13 mirrors this tenacity, resisting wear and tear with remarkable fortitude. This translates to longer tool life and reduced downtime in spray coating operations.
- Good Dimensional Stability: Imagine a ruler maintaining its perfect lines despite pressure. H13 exhibits similar dimensional stability, minimizing distortion during the spray coating process. This ensures precise coating thickness and consistent results.
- Decent Toughness: Think of a willow branch bending without breaking in a strong wind. H13 possesses a degree of toughness, allowing it to absorb some impact without succumbing to fractures.
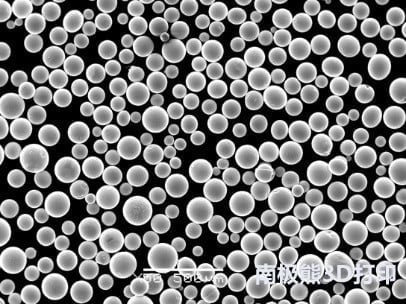
A Look Inside the H13 Powerhouse: A Compositional Breakdown
Let’s delve deeper into the specific elements that make H13 tool steel power such a powerhouse:
Elemento | Composição (%) | Função |
---|---|---|
Ferro (Fe) | Base (balance) | Provides the foundation for the steel’s structure |
Crómio (Cr) | 4.0 – 5.0 | Aumenta a temperabilidade, a resistência à corrosão e a resistência ao desgaste |
Molibdênio (Mo) | 1.3 – 1.5 | Improves hot hardness and high-temperature strength |
Vanádio (V) | 0.3 – 0 | Refines grain size, further enhancing wear resistance |
the Top 10 Pós metálicos for Spray Coating
H13 isn’t the only star in the spray coating galaxy. Here are 10 other top contenders in the realm of metal powders, each with its unique strengths:
- Aço inoxidável 316L: A versatile champion, offering excellent corrosion resistance for applications in harsh environments.
- Inconel 625: The high-temperature hero, boasting exceptional oxidation resistance and strength at elevated temperatures.
- Nickel Aluminum: A lightweight warrior, ideal for applications requiring a balance of strength and weight reduction.
- Carboneto de tungsténio: The ultimate wear fighter, renowned for its unmatched wear resistance in abrasive environments.
- Chrome Carbide: A close cousin to tungsten carbide, offering exceptional wear resistance at a slightly lower cost.
- Cobalt Chrome: The biocompatible champion, perfect for medical implants due to its excellent biocompatibility.
- Titanium: The lightweight and strong contender, prized for its high strength-to-weight ratio and corrosion resistance.
- Cobre: The thermal conductor extraordinaire, ideal for applications requiring efficient heat transfer.
- Alumínio: The lightweight and affordable option, perfect for applications where weight and cost are primary concerns.
- Metco 17: A specialized alloy designed for exceptional wear resistance and high-temperature performance in hot forging applications.
The H13 Advantage
When it comes to spray coating, H13 tool steel power offers a plethora of advantages that make it a compelling choice:
- Exceptional Wear Resistance: As mentioned earlier, H13 excels in resisting wear and tear. This translates to longer-lasting coatings, reduced maintenance costs, and improved overall equipment life for spray coating equipment.
- Superior Hot Hardness: H13’s ability to maintain its strength at high temperatures makes it ideal for thermal spraying processes. This ensures the integrity of the coating even when subjected to extreme heat.
- Good Dimensional Stability: H13 minimizes distortion during the spray coating process, leading to precise coating thickness and consistent results. This is crucial for applications where dimensional accuracy is paramount.
- Maquinabilidade: While not its most defining feature, H13 offers decent machinability compared to other tool steels.
Applications of H13 tool steel power in Spray Coating
H13’s impressive repertoire of properties translates into a diverse range of applications in the world of spray coating. Here, we’ll explore some of the most common battlegrounds where H13 shines:
- Mold Cores and Cavity Inserts: Imagine the intricate shapes of plastic parts. Molds used to create these parts often have cores and cavity inserts made from H13. The material’s wear resistance ensures these inserts maintain their precise shapes over extended production runs, leading to high-quality plastic parts.
- Dies and Punches: Think of cookie cutters stamping out delicious treats. Dies and punches used in metal forming processes often benefit from H13’s strength and wear resistance. This allows them to withstand the constant pressure and friction involved in shaping metal sheets.
- Wear Plates and Liners: Picture chutes guiding materials down a processing line. These chutes are often lined with wear plates made from H13. The material’s exceptional wear resistance protects the underlying structure from damage caused by abrasive materials.
- Thermal Spraying Applications: This is where H13 truly shines. In thermal spraying, molten metal particles are propelled onto a substrate to create a protective coating. H13’s hot hardness makes it ideal for use as nozzles, feedstock material, and even substrates for thermal spray coatings.
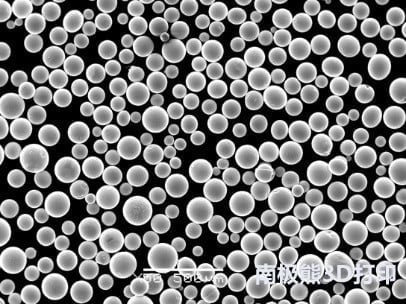
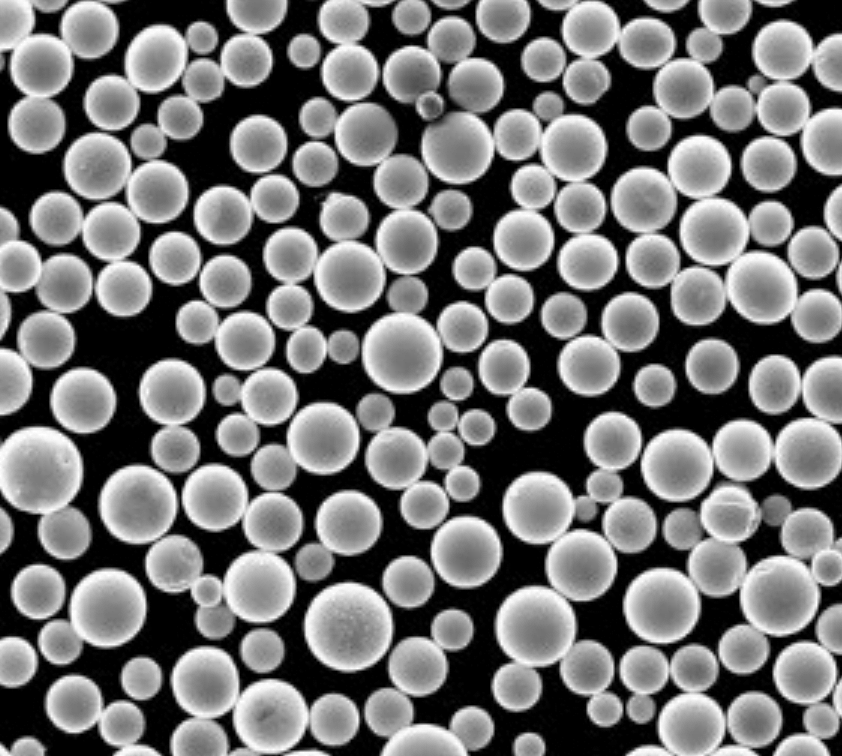
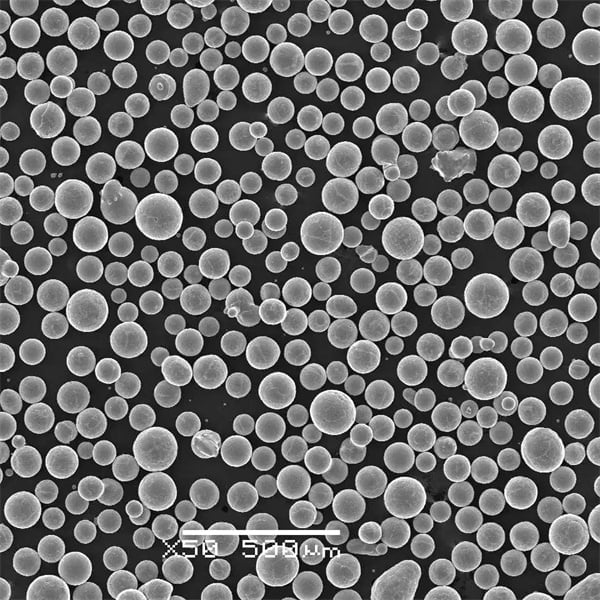
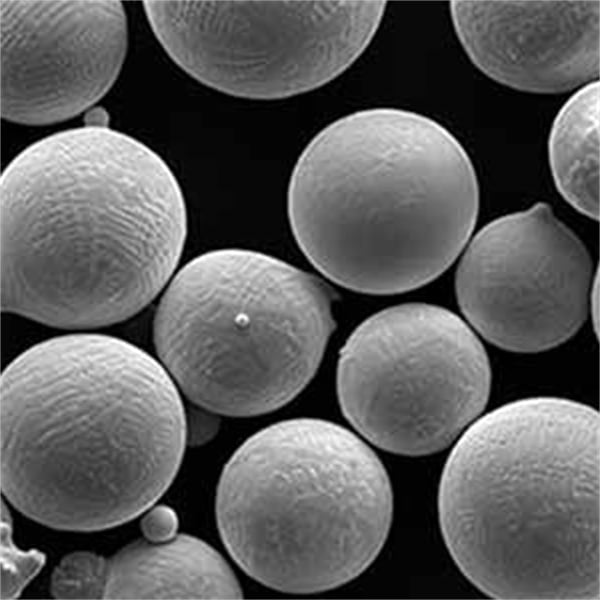
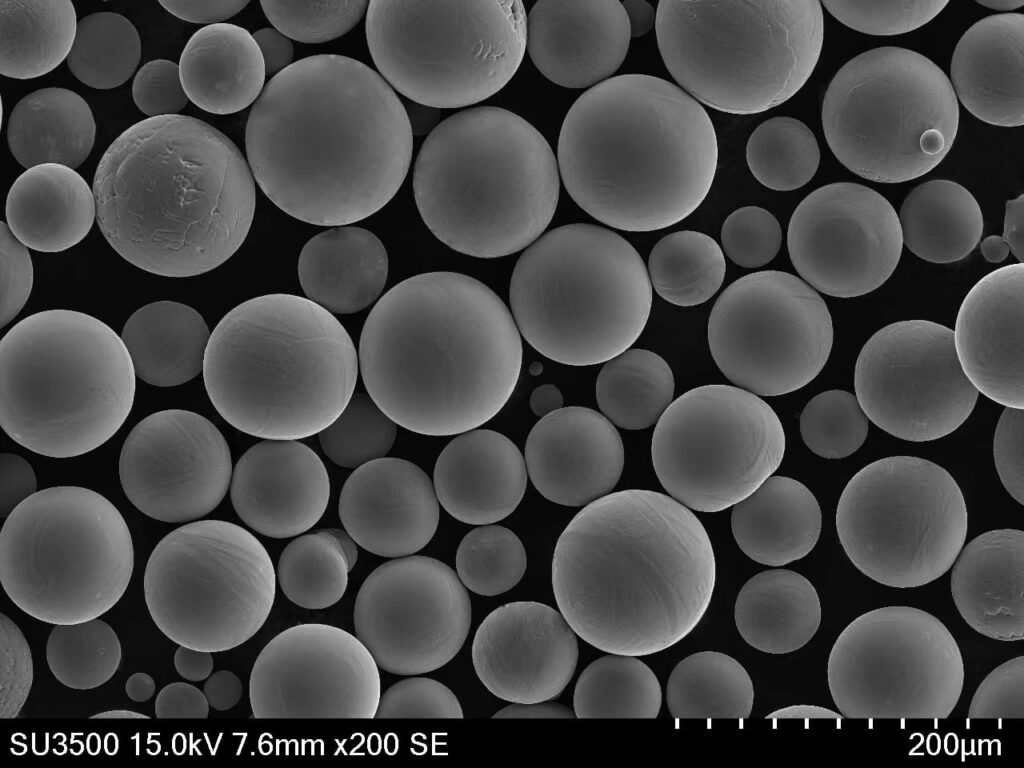
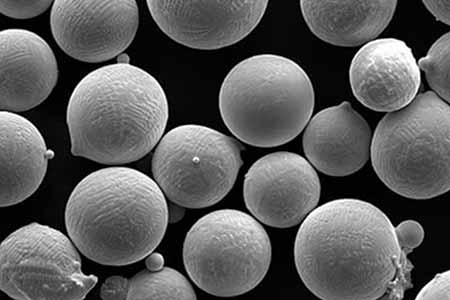
Specialized Applications of H13 tool steel power
While the aforementioned applications represent the core battlegrounds for H13 in spray coating, its versatility extends beyond the ordinary:
- Hot Working Tools: Think of forging hammers shaping red-hot metal. H13’s hot hardness makes it suitable for such hot working tools, ensuring they maintain their shape and deliver precise blows even at elevated temperatures.
- Shear Blades: Imagine cutting through thick sheets of metal with ease. Shear blades used in metal cutting operations can benefit from H13’s wear resistance, leading to cleaner cuts and longer blade life.
- Gears and Cams: Picture the intricate dance of gears in a machine. Gears and cams subjected to high contact stress can leverage H13’s strength and wear resistance to ensure smooth operation and extended life.
H13 vs. The Competition: A Comparative Analysis
While H13 reigns supreme in many spray coating applications, it’s not the only contender in the arena. Let’s compare it to some of its closest rivals:
- H11 Tool Steel: A close cousin, H11 offers similar properties but with slightly lower hot hardness and wear resistance. It’s often a more budget-friendly option for less demanding applications.
- Aço inoxidável 316L: This champion boasts superior corrosion resistance, making it ideal for applications in harsh environments where H13 might succumb to corrosion. However, its wear resistance is lower compared to H13.
- Inconel 625: The high-temperature king surpasses H13 in terms of oxidation resistance at extreme temperatures. However, its higher cost and lower machinability make it a less versatile option for some applications.
Advantages and Disadvantages of H13 tool steel power
Every hero has their limitations, and H13 is no exception. Let’s delve into both sides of the coin:
Vantagens:
- Exceptional Wear Resistance: As highlighted repeatedly, H13’s wear resistance is a game-changer, leading to longer-lasting coatings and reduced maintenance costs.
- Superior Hot Hardness: The ability to maintain strength at high temperatures makes H13 ideal for thermal spray applications and hot working tools.
- Good Dimensional Stability: H13 minimizes distortion during spray coating, ensuring precise coating thickness and consistent results.
- Decent Machinability: While not its most defining feature, H13 offers workable machinability compared to other tool steels.
Desvantagens:
- Custo mais elevado: Compared to some other options like H11, H13 comes with a slightly higher price tag.
- Frágil a baixas temperaturas: While strong at high temperatures, H13 can become brittle at low temperatures. This needs to be considered when selecting the material for specific applications.
- Susceptible to Corrosion: In highly corrosive environments, H13 might not be the optimal choice. Stainless steels offer superior corrosion resistance.
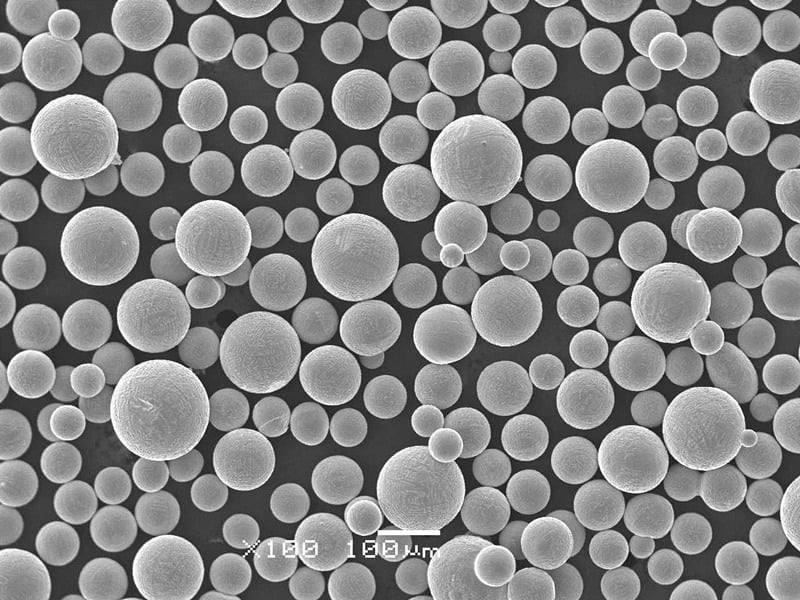
Perguntas Frequentes
Q: What are some alternatives to H13 tool steel for spray coating applications?
A: Depending on the specific requirements, alternatives include H11 tool steel (more budget-friendly for less demanding applications), stainless steel 316L (superior corrosion resistance), and Inconel 625 (exceptional oxidation resistance at extreme temperatures).
Q: Is H13 tool steel a good substrate for thermal spray coating?
A: Yes, H13 is generally considered a good substrate for thermal spray coating. Its properties, such as good dimensional stability and hardenability, make it a suitable base for adding a wear-resistant or corrosion-resistant coating.
Q: What are the benefits of thermal spray coating H13 tool steel?
A: Thermal spray coating can improve the performance of H13 tool steel in several ways, including:
- Increased wear resistance: A coating can protect the H13 substrate from wear and tear, extending the life of the tool.
- Improved corrosion resistance: A coating can protect the H13 substrate from corrosion, especially if the tool will be exposed to harsh chemicals or environments.
- Reduced friction: A coating can reduce friction between the tool and the workpiece, which can improve efficiency and reduce heat generation.
Q: What are some things to consider before spray coating H13 tool steel?
A: There are several factors to consider before spray coating H13 tool steel, including:
- The type of coating: Different coatings offer different benefits. It’s important to choose a coating that is compatible with the intended application and will provide the desired properties.
- The surface preparation of the H13 substrate: The surface of the H13 must be properly cleaned and prepared to ensure good adhesion of the coating.
- The heat treatment of the H13 substrate: H13 is often heat treated to improve its properties. The heat treatment process may need to be adjusted to account for the spray coating process.
Q: What are some resources where I can learn more about spray coating H13 tool steel?
- Several resources are available online and in libraries that discuss thermal spray coating of tool steel, including H13.
- Professional organizations such as the American Society for Materials Testing (ASTM) publish standards and specifications for thermal spray coatings.
Sobre a 3DP mETAL
Categoria do produto
CONTACTE-NOS
Tem dúvidas ? Envie uma mensagem para nós agora mesmo! Após o recebimento de sua mensagem, nós processaremos sua solicitação com toda a equipe.