When it comes to advanced manufacturing techniques, Hot Isostatic Pressing (HIP) technology stands out as a pivotal process in various industries. In this comprehensive guide, we will delve into the intricacies of HIP technology, discussing everything from its fundamental principles to specific metal powder models, their properties, applications, and suppliers. Buckle up for a detailed yet engaging journey through the world of HIP technology!
Visão geral de Tecnologia HIP
Hot Isostatic Pressing (HIP) is a manufacturing process that improves the properties of metals and ceramics through the application of high pressure and high temperature. This technique is essential in producing components with superior density, strength, and fatigue resistance.
Key Details of HIP Technology
- Processo: Application of high pressure and temperature to eliminate porosity in metals and ceramics.
- Benefícios: Enhanced material properties like density, strength, and durability.
- APLICAÇÕES: Aerospace, automotive, medical implants, and more.
- Materiais: Various metals and ceramics, often in powder form.
How Does HIP Work?
The HIP process involves placing the material inside a high-pressure vessel, heating it to the required temperature, and applying isostatic pressure using an inert gas, typically argon. The combined heat and pressure eliminate internal voids and defects, resulting in a fully dense material.
Why Is HIP Important?
HIP technology is crucial because it allows manufacturers to produce parts with near-perfect material properties. This process significantly enhances mechanical properties, making it indispensable in high-stress applications like aerospace components and medical implants.
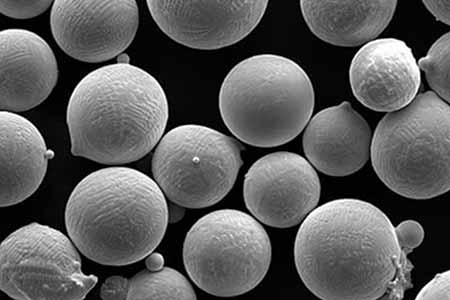
Modelos específicos de pós metálicos para Tecnologia HIP
Choosing the right metal powder is vital for the HIP process. Below, we detail ten specific metal powder models, their compositions, properties, and typical applications.
1. Inconel 718 Powder
Composição: Nickel-Chromium-Molybdenum alloy
Propriedades: High strength, corrosion resistance, and excellent weldability.
APLICAÇÕES: Aerospace engines, gas turbines, and nuclear reactors.
2. Titanium Grade 5 Powder (Ti-6Al-4V)
Composição: Titanium alloyed with 6% aluminum and 4% vanadium.
Propriedades: High strength-to-weight ratio, excellent corrosion resistance.
APLICAÇÕES: Aerospace components, medical implants, and automotive parts.
3. Maraging Steel Powder (18Ni-300)
Composição: Nickel, cobalt, molybdenum, and titanium alloy.
Propriedades: Ultra-high strength, toughness, and good machinability.
APLICAÇÕES: Tooling, aerospace structures, and high-performance engineering parts.
4. 316L Stainless Steel Powder
Composição: Iron, chromium, nickel, and molybdenum alloy.
Propriedades: Excellent corrosion resistance, high ductility, and weldability.
APLICAÇÕES: Medical devices, food processing equipment, and chemical industry.
5. Hastelloy X Powder
Composição: Nickel, chromium, iron, and molybdenum alloy.
Propriedades: High-temperature strength, oxidation resistance.
APLICAÇÕES: Gas turbines, aircraft engines, and industrial furnace applications.
6. Aluminum Alloy 6061 Powder
Composição: Aluminum with magnesium and silicon.
Propriedades: Good mechanical properties, excellent weldability, and corrosion resistance.
APLICAÇÕES: Aerospace components, automotive parts, and structural applications.
7. Cobalt-Chrome Alloy Powder (CoCr)
Composição: Cobalt, chromium, molybdenum alloy.
Propriedades: High wear resistance, biocompatibility.
APLICAÇÕES: Medical implants, dental prosthetics, and turbine blades.
8. Tantalum Powder
Composição: Pure tantalum.
Propriedades: High melting point, excellent corrosion resistance.
APLICAÇÕES: Medical implants, electronics, and chemical processing equipment.
9. Tungsten Carbide Powder
Composição: Tungsten and carbon.
Propriedades: Extremely high hardness, wear resistance.
APLICAÇÕES: Cutting tools, mining equipment, and wear-resistant parts.
10. Nickel Alloy 625 Powder
Composição: Nickel, chromium, molybdenum, and niobium alloy.
Propriedades: High strength, excellent fatigue, and thermal-fatigue resistance.
APLICAÇÕES: Aerospace, marine, and chemical processing industries.
Properties and Characteristics of Metal Powders for HIP
To provide a clearer understanding of the metal powders used in HIP technology, here is a detailed table summarizing their properties and characteristics.
Pó metálico | Composição | Propriedades | APLICAÇÕES |
---|---|---|---|
Inconel 718 | Ni-Cr-Mo alloy | High strength, corrosion resistance, weldability | Aerospace, gas turbines, nuclear reactors |
Titânio de grau 5 (Ti-6Al-4V) | Ti-6% Al-4% V | Elevada relação força/peso, resistência à corrosão | Aeroespacial, implantes médicos, automóvel |
Aço Maraging (18Ni-300) | Ni-Co-Mo-Ti alloy | Ultra-high strength, toughness, machinability | Tooling, aerospace structures |
Aço inoxidável 316L | Fe-Cr-Ni-Mo alloy | Corrosion resistance, high ductility, weldability | Medical devices, food processing, chemical industry |
Hastelloy X | Ni-Cr-Fe-Mo alloy | Resistência a altas temperaturas, resistência à oxidação | Gas turbines, aircraft engines, industrial furnaces |
Liga de alumínio 6061 | Al-Mg-Si | Mechanical properties, weldability, corrosion resistance | Aerospace, automotive, structural applications |
Cobalto-crómio (CoCr) | Co-Cr-Mo alloy | Resistência ao desgaste, biocompatibilidade | Medical implants, dental prosthetics, turbine blades |
Tântalo | Pure Ta | Elevado ponto de fusão, resistência à corrosão | Medical implants, electronics, chemical processing |
Carboneto de tungsténio | W-C | Elevada dureza, resistência ao desgaste | Cutting tools, mining equipment, wear-resistant parts |
Liga de níquel 625 | Ni-Cr-Mo-Nb alloy | Strength, fatigue resistance, thermal-fatigue resistance | Aerospace, marine, chemical processing industries |
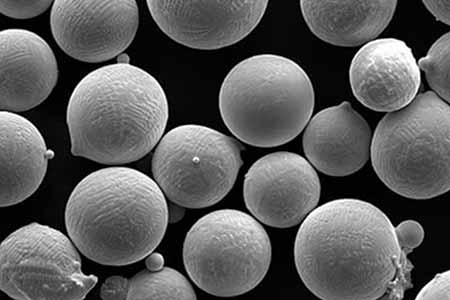
Aplicações de Tecnologia HIP
HIP technology is utilized across various industries due to its ability to enhance the mechanical properties of materials. Let’s explore some of the key applications.
Aeroespacial
In the aerospace industry, the demand for high-performance, lightweight, and durable components is ever-growing. HIP technology plays a crucial role in producing components such as turbine blades, engine parts, and structural elements with superior strength and fatigue resistance.
Implantes médicos
Medical implants require materials with excellent biocompatibility, corrosion resistance, and mechanical strength. HIP technology is used to manufacture implants like hip joints, dental prosthetics, and spinal implants, ensuring they meet the stringent requirements of the medical field.
Automotivo
In the automotive sector, components need to withstand high stress and harsh environments. HIP technology enhances the properties of engine parts, transmission components, and structural elements, improving their performance and longevity.
Energia e produção de eletricidade
HIP technology is essential in the energy sector for manufacturing components used in gas turbines, nuclear reactors, and power generation equipment. The process ensures these parts can withstand extreme conditions and maintain high performance.
Tooling and Dies
The tooling industry benefits from HIP technology by producing high-strength, wear-resistant tools and dies. These components are essential in manufacturing processes that require precision and durability.
Especificações, tamanhos, graus e normas
Understanding the specifications, sizes, grades, and standards of metal powders used in HIP technology is crucial for selecting the right material for a specific application. Below is a detailed table highlighting these aspects.
Pó metálico | Especificações | Tamanhos (Microns) | Notas | Padrões |
---|---|---|---|---|
Inconel 718 | AMS 5662, ASTM B637 | 15-45 | Prémio | ASTM, SAE, AMS |
Titânio de grau 5 (Ti-6Al-4V) | ASTM B348, AMS 4928 | 20-63 | Grade 5, ELI | ASTM, SAE, AMS |
Aço Maraging (18Ni-300) | AMS 6520, ASTM A538 | 10-53 | 250, 300, 350 | ASTM, SAE, AMS |
Aço inoxidável 316L | ASTM A240, AMS 5507 | 15-45 | 316L | ASTM, SAE, AMS |
Hastelloy X | ASTM B435, AMS 5536 | 20-63 | Prémio | ASTM, SAE, AMS |
Liga de alumínio 6061 | ASTM B221, AMS 4150 | 10-45 | 6061-T6, 6061-O | ASTM, SAE, AMS |
Cobalto-crómio (CoCr) | ASTM F1537, ISO 5832-4 | 15-63 | F75, F1537 | ASTM, ISO |
Tântalo | ASTM B708, ISO 13782 | 10-45 | RO5200, RO5400 | ASTM, ISO |
Carboneto de tungsténio | ASTM B777, ISO 4483 | 5-25 | WC-Co, WC-Ni | ASTM, ISO |
Fornecedores e informações sobre preços
Selecting the right supplier is crucial for obtaining high-quality metal powders for HIP technology. Below is a table of some reputable suppliers along with their pricing details.
Fornecedor | Pós metálicos oferecidos | Preço (por kg) | Região |
---|---|---|---|
Tecnologia Carpinteiro | Inconel 718, Titanium Grade 5, Maraging Steel | $100 – $300 | América do Norte, Europa |
Tecnologia de materiais da Sandvik | 316L Stainless Steel, Hastelloy X, CoCr | $80 – $250 | Mundial |
Tecnologias de Superfície da Praxair | Aluminum Alloy 6061, Nickel Alloy 625 | $90 – $200 | América do Norte, Europa |
ATI Materiais Especiais | Tantalum, Tungsten Carbide | $150 – $500 | Mundial |
Pós e Revestimentos Avançados | Vários pós metálicos | $70 – $400 | Mundial |
Advantages and Disadvantages of HIP Technology
Every technology comes with its own set of advantages and disadvantages. Here, we compare the pros and cons of HIP technology to help you understand its impact on manufacturing processes.
Advantages of HIP Technology
- Enhanced Material Properties: HIP significantly improves the density, strength, and durability of materials.
- Defect Elimination: The process effectively removes internal voids and defects, ensuring superior quality components.
- Versatilidade: Applicable to a wide range of metals and ceramics.
- Improved Performance: Components produced using HIP perform better under high stress and extreme conditions.
- Rentável: Reduces the need for secondary processing, saving time and costs.
Desvantagens de Tecnologia HIP
- Investimento inicial elevado: The equipment and setup costs for HIP technology can be substantial.
- Processo complexo: Requires precise control of pressure and temperature, making it complex to operate.
- Limited Size of Components: The size of the HIP vessel limits the size of the components that can be processed.
- Consumo de energia: The process can be energy-intensive, leading to higher operational costs.
Comparison of Metal Powders: Pros and Cons
Let’s compare some of the key metal powders used in HIP technology to highlight their specific advantages and disadvantages.
Pó metálico | Vantagens | Desvantagens |
---|---|---|
Inconel 718 | High strength, corrosion resistance, weldability | Custo elevado |
Titânio de grau 5 (Ti-6Al-4V) | Elevada relação força/peso, resistência à corrosão | Caro, difícil de maquinar |
Aço Maraging (18Ni-300) | Ultra-high strength, toughness, machinability | Requires heat treatment, can be brittle if not treated properly |
Aço inoxidável 316L | Corrosion resistance, high ductility, weldability | Menor resistência em comparação com outras ligas |
Hastelloy X | Resistência a altas temperaturas, resistência à oxidação | Custo elevado, disponibilidade limitada |
Liga de alumínio 6061 | Good mechanical properties, weldability, corrosion resistance | Menor resistência em comparação com as ligas de aço |
Cobalto-crómio (CoCr) | Resistência ao desgaste, biocompatibilidade | Difícil de maquinar, caro |
Tântalo | Elevado ponto de fusão, resistência à corrosão | High cost, limited applications |
Carboneto de tungsténio | Extremely high hardness, wear resistance | Brittle, challenging to process |
Liga de níquel 625 | High strength, fatigue resistance, thermal-fatigue resistance | Caro, difícil de maquinar |
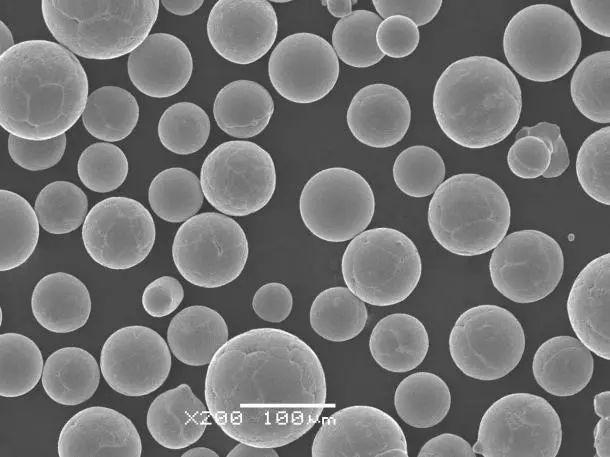
FAQs
Here are some frequently asked questions about HIP technology to provide further insights into this fascinating process.
Questão | Resposta |
---|---|
What is HIP technology? | HIP (Hot Isostatic Pressing) is a manufacturing process that improves material properties by applying high pressure and temperature. |
What materials can be processed using HIP? | Various metals and ceramics, including alloys like Inconel, titanium, and stainless steel. |
What are the benefits of HIP technology? | Enhanced density, strength, and durability of materials, elimination of internal defects. |
How is HIP different from other manufacturing processes? | HIP uses isostatic pressure and high temperature to achieve superior material properties, unlike other methods that may not offer the same level of defect elimination. |
Is HIP technology cost-effective? | While the initial investment is high, the long-term benefits in terms of reduced secondary processing and improved performance make it cost-effective. |
What industries benefit from HIP technology? | Aerospace, medical implants, automotive, energy, and tooling industries, among others. |
Are there size limitations for components processed with HIP? | Yes, the size of the HIP vessel limits the maximum size of components that can be processed. |
Can HIP technology be used for prototyping? | Yes, HIP is suitable for both prototyping and production runs, offering high-quality results for both. |
What are the common challenges with HIP technology? | High initial costs, complex process control, and energy consumption are some of the challenges. |
How does HIP improve material properties? | By applying high pressure and temperature, HIP eliminates porosity and defects, resulting in fully dense and stronger materials. |
Conclusão
HIP technology represents a transformative approach in the manufacturing sector, offering unparalleled improvements in material properties. From aerospace to medical implants, the applications are vast and varied. By understanding the specific metal powders, their properties, and the intricacies of the HIP process, manufacturers can leverage this technology to produce high-quality, durable components.
Whether you’re an engineer looking to optimize material performance or a manufacturer aiming to enhance product quality, HIP technology offers a robust solution. With advancements in this field continuing to evolve, the future of HIP technology looks promising, paving the way for innovations across numerous industries.
Sobre a 3DP mETAL
Categoria do produto
CONTACTE-NOS
Tem dúvidas ? Envie uma mensagem para nós agora mesmo! Após o recebimento de sua mensagem, nós processaremos sua solicitação com toda a equipe.