Imagine building a component that can withstand the scorching heat of a jet engine or the corrosive bite of harsh chemicals. Imagine crafting intricate shapes that traditional manufacturing struggles to achieve, all while maintaining exceptional strength and durability. This is the transformative power of Impressão 3D em Inconel.
What is Inconel?
Inconel 3D Printing isn’t your average metal. It’s a superalloy, a champion in the material science arena. Nickle forms its base, bolstered by chromium, molybdenum, and other elements to create a material with a unique blend of properties:
- Resistência a altas temperaturas: Inconel shrugs off extreme heat, making it ideal for applications like jet engine components, gas turbines, and heat exchangers. Think of it as a metal that thrives where others melt.
- Resistência à corrosão: Highly resistant to rust, acid attack, and other forms of corrosion, Inconel finds its place in chemical processing equipment, marine environments, and applications exposed to harsh chemicals.
- Excellent Mechanical Properties: This superalloy boasts impressive tensile strength, meaning it can bear significant pulling forces without breaking. It also demonstrates good fatigue strength, resisting wear and tear under repeated stress.
These properties make Inconel a highly sought-after material for demanding applications. But traditionally, working with Inconel presented a challenge. Its work-hardening nature makes machining complex shapes difficult and expensive.
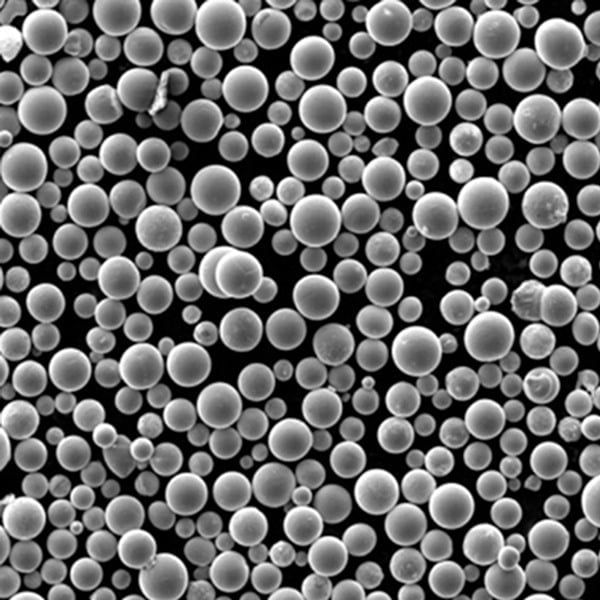
Enter 3D Printing: A Revolution in Manufacturing
3D printing, also known as additive manufacturing, has become a game-changer for many industries. It allows for the creation of complex objects layer by layer, directly from a digital model. This technology unlocks exciting possibilities for Inconel:
- Geometrias complexas: Unlike traditional methods limited by subtractive processes (removing material), 3D printing allows for the creation of intricate shapes with internal channels and intricate details. Imagine a lightweight heat exchanger with internal pathways optimized for heat transfer, only achievable through 3D printing.
- Liberdade de conceção: Gone are the constraints of conventional manufacturing. With 3D printing, engineers can unleash their creativity, designing parts with unique features that enhance performance. This opens doors to innovation and optimization in various fields.
- Redução de resíduos: Traditional machining often results in significant scrap metal. 3D printing builds parts layer by layer, minimizing waste and making the process more environmentally friendly.
As vantagens de Impressão 3D em Inconel
The marriage of Inconel and 3D printing brings a powerful combination of benefits to the table:
- Desempenho melhorado: 3D printing allows for the creation of lightweight, complex Inconel parts with optimized internal structures. This translates to improved efficiency, weight reduction, and better performance in demanding applications.
- Custos reduzidos: While the material itself might be expensive, 3D printing can minimize waste and reduce machining time compared to traditional methods. For complex geometries, 3D printing can be a more cost-effective solution.
- Faster Prototyping: The ability to create functional prototypes rapidly using 3D printing allows for faster design iterations and quicker time to market for new products. This agility gives companies a competitive edge.
- Broader Applications: 3D printing unlocks the potential of Inconel for applications where complex shapes were previously a hurdle. This opens doors to innovation in industries like aerospace, energy, and chemical processing.
The Applications of Inconel 3D Printing
With its unique combination of properties and the freedom of 3D printing, Inconel finds itself in various high-performance applications:
- Aeroespacial: Jet engine components, combustors, afterburners, and heat exchangers all benefit from Inconel’s ability to withstand extreme temperatures and harsh environments. 3D printing allows for lightweight designs that improve fuel efficiency and performance.
- Setor da energia: Gas turbines, heat exchangers, and components in nuclear power plants require materials that can handle high temperatures and resist corrosion. Inconel 3D printing offers a solution for these demanding applications.
- Processamento Químico: Inconel’s resistance to various chemicals makes it ideal for equipment used in harsh environments. 3D printing allows for the creation of complex parts with optimized flow channels, improving efficiency and safety.
- Dispositivos médicos: Certain medical implants require biocompatible materials with high strength and corrosion resistance. Inconel can be a viable option for specific applications, and 3D printing allows for customized designs.
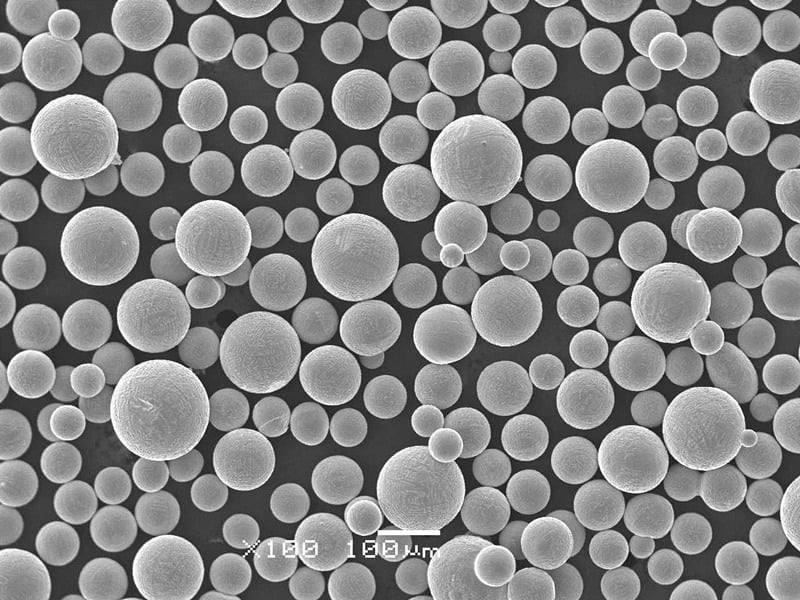
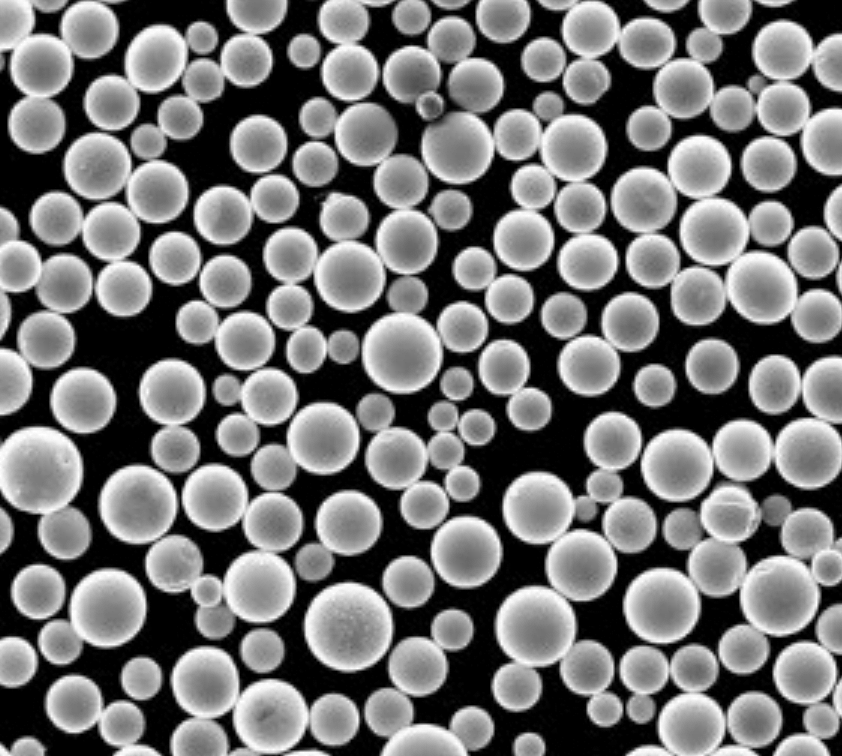
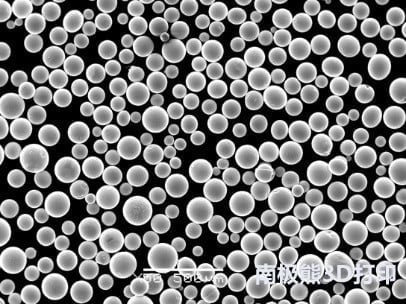
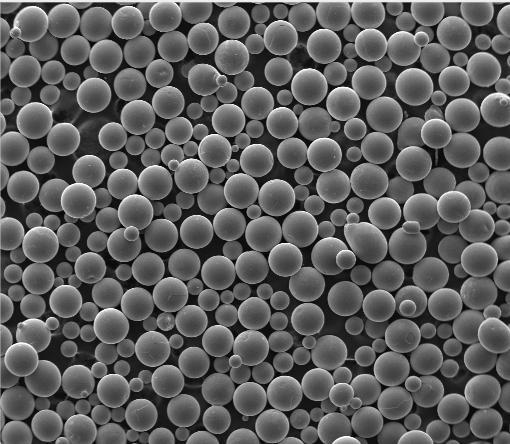
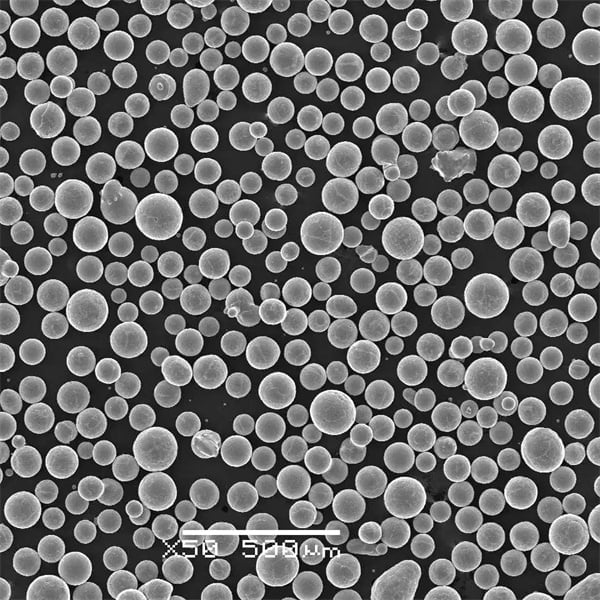
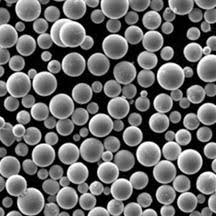
As características de Impressão 3D em Inconel
While the advantages are compelling, it’s important to understand the characteristics of Inconel 3D printing:
- Material Options: Different grades of Inconel exist, each with slightly varying properties. Inconel 625 is a popular choice for its excellent corrosion resistance, while Inconel 718 offers superior strength at high temperatures.
- 3D Printing Processes: Several 3D printing techniques can be used with Inconel, each with its own advantages and limitations. Selective Laser Melting (SLM) and Electron Beam Melting (EBM) are the most common methods for Inconel due to their ability to achieve high density and good mechanical properties. However, these processes require specialized equipment and expertise, making them more expensive compared to other techniques.
- Acabamento da superfície: 3D printed Inconel parts may require post-processing for a smooth surface finish. Depending on the application, additional machining, polishing, or heat treatment might be necessary.
Desafios e considerações
While powerful, Inconel 3D printing isn’t without its challenges:
- Custo do material: Inconel itself is a relatively expensive material compared to other metals used in 3D printing. This can be a significant cost factor, especially for larger parts.
- Complexidade do processo: Compared to printing with plastics or even some other metals, 3D printing Inconel requires specialized equipment and expertise. This can limit the accessibility of the technology for smaller companies or those without experience in additive manufacturing.
- Pós-processamento: As mentioned earlier, 3D printed Inconel parts might require additional steps like machining or heat treatment to achieve the desired surface finish and mechanical properties. This adds time and cost to the process.
Making the Most of Inconel 3D Printing
Despite the challenges, several strategies can help you maximize the benefits of Inconel 3D printing:
- Conceção para fabrico aditivo (DfAM): Approaching design with 3D printing’s capabilities in mind is crucial. Consider lightweighting opportunities, internal channels, and complex geometries that wouldn’t be feasible with traditional methods.
- Partnering with Experienced Service Providers: Working with a reputable 3D printing service provider with expertise in Inconel can ensure optimal results. They can advise on material selection, process parameters, and post-processing techniques.
- Cost-Benefit Analysis: Carefully evaluate the cost of Inconel 3D printing compared to alternative materials and manufacturing methods. Consider the potential performance benefits, weight savings, and design freedom that 3D printing offers.
O futuro da Impressão 3D em Inconel
The future of Inconel 3D printing is bright. As technology advances, we can expect:
- Custos reduzidos: As the technology matures and adoption increases, the cost of Inconel 3D printing is expected to decrease, making it more accessible to a wider range of applications.
- Material Development: Research and development efforts are ongoing to create new Inconel alloys specifically optimized for 3D printing. These alloys might offer improved printability, better mechanical properties, or even lower costs.
- Advanced Techniques: New 3D printing techniques are emerging that could further revolutionize Inconel printing. Techniques like binder jetting or cold spray could potentially offer faster printing speeds and wider printability for specific applications.
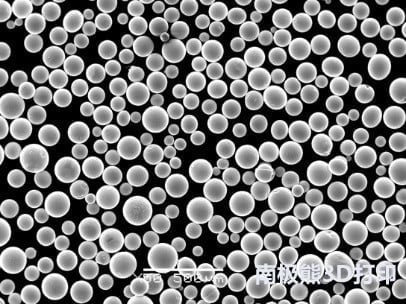
Perguntas Frequentes
Eis algumas perguntas frequentes sobre Impressão 3D em Inconel:
Questão | Resposta |
---|---|
What are the different grades of Inconel used in 3D printing? | Inconel 625 and Inconel 718 are the most common grades. Inconel 625 offers excellent corrosion resistance, while Inconel 718 boasts superior strength at high temperatures. |
What 3D printing processes can be used with Inconel? | Selective Laser Melting (SLM) and Electron Beam Melting (EBM) are the dominant methods due to their ability to achieve high density and good mechanical properties. However, other techniques like binder jetting or cold spray might play a role in the future. |
Is Inconel 3D printing expensive? | Yes, Inconel itself is a costly material, and the specialized equipment and expertise required for printing add to the cost. However, for complex geometries or applications requiring high performance, 3D printing can be a cost-effective solution compared to traditional methods. |
What are the benefits of using Inconel 3D printing? | The key benefits include enhanced performance through lightweight designs, reduced waste compared to traditional machining, faster prototyping for quicker product development, and the ability to create complex shapes that wouldn’t be possible with other methods. |
What are the limitations of Inconel 3D printing? | The main limitations are the relatively high cost of the material and the process itself, along with the need for post-processing in some cases. Additionally, the technology requires specialized expertise compared to other 3D printing methods. |
Sobre a 3DP mETAL
Categoria do produto
CONTACTE-NOS
Tem dúvidas ? Envie uma mensagem para nós agora mesmo! Após o recebimento de sua mensagem, nós processaremos sua solicitação com toda a equipe.