Pó de Inconelum super-herói entre os pós metálicos, transforma a forma como concebemos e fabricamos componentes críticos. Mas o que é exatamente este material maravilhoso e como é que ele revoluciona várias indústrias? Apertem os cintos, porque estamos prestes a embarcar numa viagem ao fascinante mundo do pó Inconel!
O que é o Inconel em pó?
Imagine triturar uma superliga, Inconel, até obter um pó fino e metálico. Isso é essencialmente pó de Inconel! O Inconel é uma família de superligas à base de níquel conhecida pela sua força excecional, resistência a altas temperaturas e impressionante resistência à corrosão. Quando reduzido à forma de pó, o Inconel mantém estas propriedades notáveis, o que o torna um fator de mudança no fabrico aditivo (impressão 3D).
a composição: Uma mistura de força
O níquel forma a base do pó de Inconel, constituindo normalmente cerca de 70%. O crómio, outro elemento-chave, contribui para a sua resistência à oxidação e desempenho a altas temperaturas. Outros elementos de liga, como o nióbio, o molibdénio e o ferro, são estrategicamente incorporados para afinar propriedades específicas com base na aplicação pretendida. A composição exacta varia consoante o tipo específico de Inconel, como o Inconel 625 ou o Inconel 718, cada um formulado para se destacar em ambientes específicos.
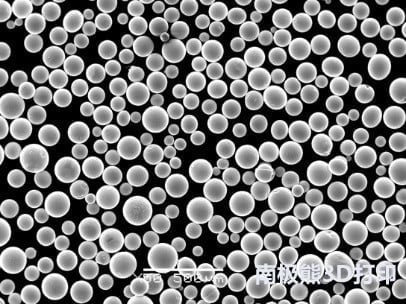
O método de fabrico de Inconel em pó
Aqui está uma espreitadela por detrás da cortina da criação do pó de Inconel:
- Atomização: O método mais comum consiste em transformar o Inconel fundido numa névoa de gotículas minúsculas através da atomização a gás ou água a alta pressão. Estas gotículas solidificam rapidamente num pó fino com uma forma esférica, ideal para processos de impressão 3D.
- Técnica de eléctrodos rotativos de plasma (PERC): Esta técnica utiliza um elétrodo rotativo parcialmente submerso em Inconel fundido. Uma tocha de plasma a alta temperatura funde o elétrodo e a força centrífuga ejecta pequenas gotículas que se solidificam num pó com uma morfologia mais irregular.
- Deposição química de vapor (CVD): Este método envolve a decomposição de precursores gasosos num substrato aquecido, permitindo que o Inconel se acumule camada por camada em forma de pó. O pó de Inconel produzido por CVD oferece uma pureza excecional e controlo sobre o tamanho das partículas.
Vantagens e considerações sobre as diferentes técnicas:
Técnica | Vantagens | Considerações |
---|---|---|
Atomização | Estabelecido, económico, boa fluidez | Pode ser necessário um pós-processamento para obter o tamanho e a morfologia desejados das partículas |
PERC | Alta pureza, tamanho e morfologia das partículas adaptáveis | Relativamente complexo e dispendioso |
DCV | Pureza excecional, controlo preciso do tamanho e da morfologia das partículas | Capacidade de produção limitada, custo elevado |
Aplicações comuns do pó de Inconel
A mistura única de propriedades do pó de Inconel abre possibilidades em vários sectores:
- Aeroespacial: O pó de Inconel encontra a sua vocação em componentes de motores a jato, como lâminas de turbina e combustores. A sua capacidade de resistir a temperaturas extremas e a ambientes adversos torna-os insubstituíveis na busca incessante de aeronaves eficientes e potentes.
- Processamento Químico: A excecional resistência do pó de Inconel à corrosão torna-o ideal para equipamento de fabrico que lida com produtos químicos agressivos e temperaturas elevadas, garantindo a segurança e a longevidade do processo.
- Produção de energia: Desde componentes em reactores nucleares a peças em turbinas de gás avançadas, o pó Inconel desempenha um papel crucial na produção fiável e eficiente de energia.
- Dispositivos médicos: Quando a biocompatibilidade é primordial, o pó de Inconel está à altura. Alguns graus podem ser utilizados para implantes médicos que requerem uma força e resistência à corrosão excepcionais, melhorando potencialmente os resultados dos pacientes.
Para além destas aplicações principais, o potencial do pó de Inconel estende-se a vários outros campos, incluindo
- Automóvel: Componentes de motores de elevado desempenho e peças expostas a temperaturas extremas.
- Engenharia marítima: Veios, hélices e outros componentes que têm de resistir ao ambiente agressivo da água salgada.
- Defesa e segurança: Componentes que requerem uma combinação de força, resistência ao calor e resistência à corrosão.
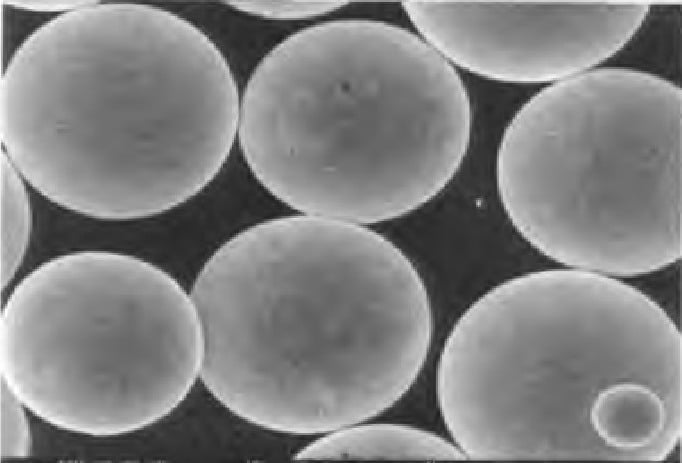
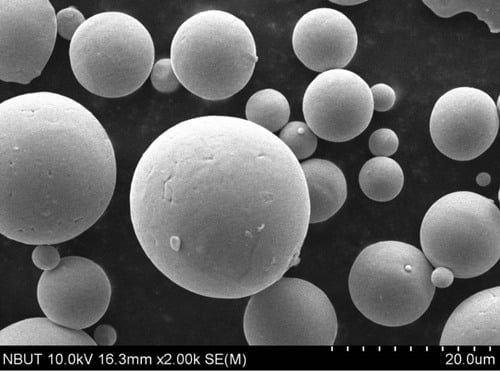
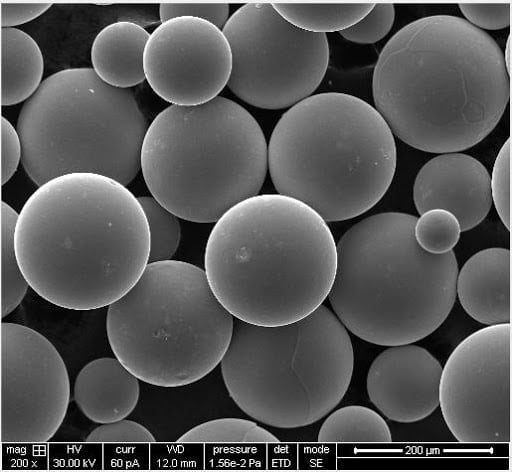
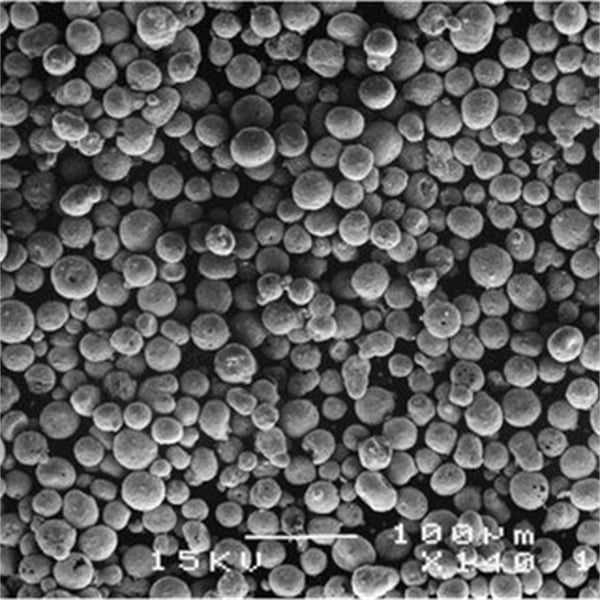
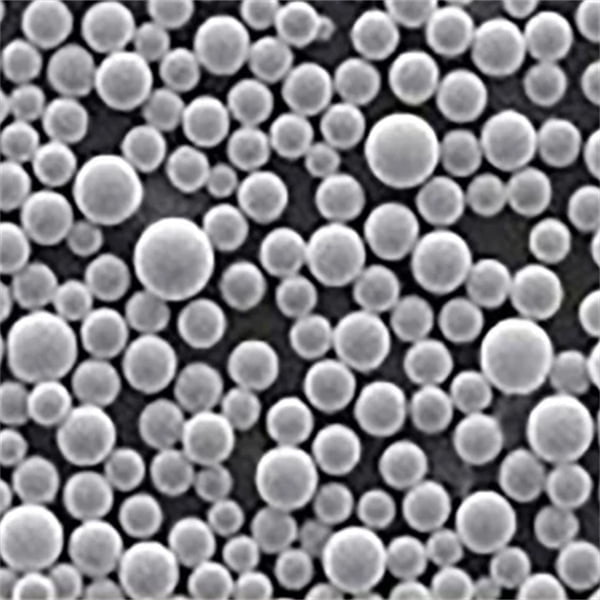
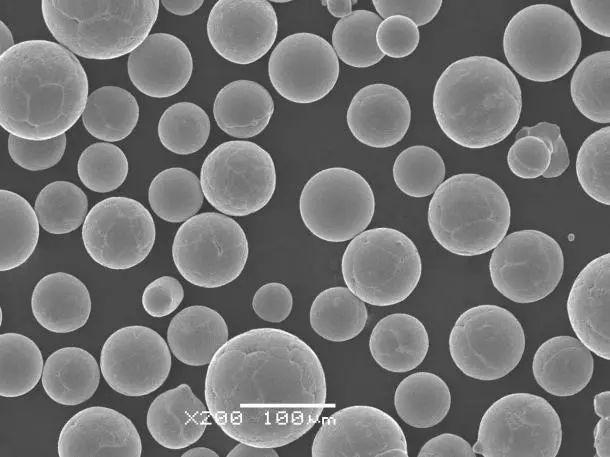
Como Inconel em pó é transformado no produto final
Uma vez concluída a magia do pó de Inconel, este é transformado numa maravilha funcional através de várias técnicas:
- Fabrico de aditivos (impressão 3D): Esta tecnologia revolucionária permite a criação de componentes complexos, quase em forma de rede, camada a camada, utilizando pó de Inconel. Isto minimiza o desperdício de material e permite a conceção de geometrias complexas, impossíveis com as técnicas de fabrico tradicionais.
- Fusão por feixe de laser (LBM): Um feixe de laser de alta potência funde seletivamente as partículas de pó de Inconel, fundindo-as camada por camada para construir a estrutura 3D desejada. O LBM oferece uma precisão e um controlo excepcionais sobre as propriedades do produto final.
- Fusão por feixe de electrões (EBM): Semelhante ao LBM, o EBM utiliza um feixe de electrões num ambiente de vácuo para fundir partículas de pó de Inconel. Este método é particularmente adequado para aplicações que requerem um controlo rigoroso do teor de oxigénio e a minimização dos efeitos de oxidação.
- Jato de ligante: Esta técnica envolve a impressão a jato de tinta de um aglutinante sobre um leito de pó de Inconel, criando seletivamente a forma 3D desejada. A peça é depois tratada termicamente para solidificar as partículas de metal e remover o aglutinante.
Escolher a técnica correcta:
A seleção da técnica de processamento mais adequada depende de vários factores, incluindo:
- Complexidade da geometria da peça: O fabrico aditivo é excelente na criação de formas complexas.
- Precisão dimensional e acabamento superficial: O LBM e o EBM oferecem uma precisão superior em comparação com o jato de aglutinante.
- Volume de produção: O jato de aglutinante pode ser mais adequado para lotes maiores, enquanto o LBM e o EBM são ideais para protótipos e produção de baixo volume.
- Propriedades do material: Técnicas específicas podem ser mais adequadas para preservar as propriedades desejadas no produto final.
Vantagens da utilização de pó de Inconel no fabrico aditivo:
- Liberdade de conceção: Liberte a criatividade com a capacidade de conceber geometrias complexas com as quais o fabrico tradicional tem dificuldades.
- Aligeiramento: Criar componentes com estruturas internas complexas, reduzindo o peso sem comprometer a resistência.
- Eficiência do material: Minimizar o desperdício de material em comparação com as técnicas tradicionais de fabrico subtrativo.
- Prototipagem rápida: Acelera o processo de criação de protótipos, permitindo iterações de design mais rápidas e ciclos de desenvolvimento de produtos mais rápidos.
Considerações sobre a utilização de Inconel em pó:
- Custo: O próprio pó de Inconel e os processos de fabrico aditivo podem ser dispendiosos em comparação com as técnicas tradicionais.
- Acabamento da superfície: Embora algumas técnicas ofereçam bons acabamentos de superfície, o pós-processamento pode ser necessário para aplicações específicas.
- Estruturas de apoio: Certas geometrias podem exigir estruturas de suporte temporárias durante o processo de impressão, que têm de ser removidas posteriormente e podem deixar marcas.
Considerações sobre o custo do pó de Inconel
O pó de Inconel, um material de primeira qualidade, tem um preço que reflecte as suas propriedades excepcionais. Segue-se uma análise dos factores de custo:
- Custo do material: O preço base do pó de Inconel é mais elevado do que o de muitos outros pós metálicos, devido à complexidade dos elementos de liga e dos processos de produção envolvidos.
- Características do pó: Factores como a dimensão das partículas, a morfologia e a pureza podem influenciar o custo. Por exemplo, os pós mais finos ou com uma distribuição de tamanho mais apertada podem ter um preço mais elevado.
- Técnica de fabrico: A técnica de fabrico aditivo escolhida também desempenha um papel importante. Técnicas como a EBM, com os seus requisitos de maior precisão e ambiente de vácuo, podem ser mais dispendiosas do que o jato de aglutinante.
Apesar das considerações de custo inicial, os benefícios da utilização do pó Inconel podem superar o investimento inicial. Eis a razão:
- Redução do desperdício de materiais: O fabrico aditivo minimiza o desperdício de material em comparação com as técnicas tradicionais, conduzindo potencialmente a poupanças de custos significativas a longo prazo.
- Potencial de redução de peso: A capacidade de criar componentes leves com estruturas complexas pode traduzir-se em benefícios em termos de eficiência de combustível em sectores como o aeroespacial, conduzindo, em última análise, a poupanças de custos.
- Vantagens de desempenho: A força excecional, a resistência a altas temperaturas e a resistência à corrosão dos componentes Inconel podem levar a uma vida útil prolongada e a custos de manutenção reduzidos.
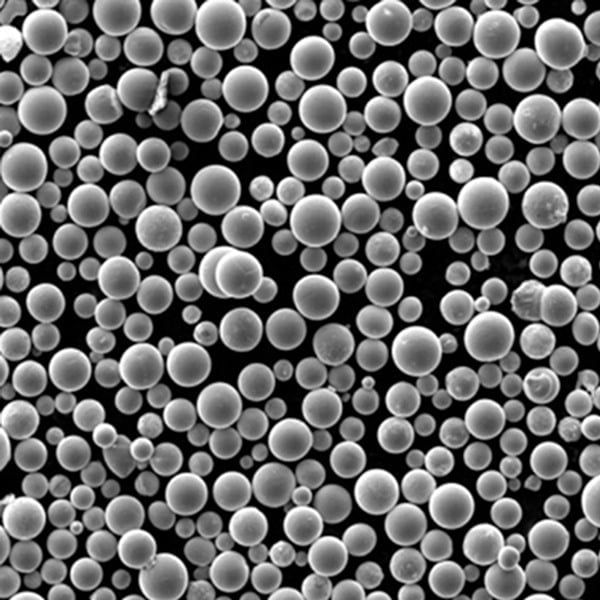
Perspectivas para o futuro: O potencial inexplorado de Inconel em pó
O futuro do pó de Inconel é brilhante. Aqui estão algumas tendências interessantes a observar:
- Avanços na produção de pós: Os esforços de investigação centram-se no desenvolvimento de métodos mais rentáveis e eficientes para a produção de pó de Inconel com um controlo ainda melhor do tamanho das partículas, da morfologia e da pureza.
- Técnicas emergentes de fabrico de aditivos: As novas tecnologias de impressão 3D estão em constante evolução, oferecendo velocidades de impressão mais rápidas, melhor resolução e a capacidade de combinar vários materiais numa única impressão, potencialmente desbloqueando possibilidades de design sem precedentes para os componentes Inconel.
- Exploração de novas aplicações: À medida que a tecnologia amadurece e os custos se tornam mais competitivos, podemos esperar ver Pó de Inconel integrado numa gama mais vasta de indústrias, revolucionando ainda mais os processos de fabrico e a conceção de produtos.
Perguntas Frequentes
Questão | Resposta |
---|---|
P: Qual é a resistência do pó de Inconel em comparação com outros pós metálicos? | R: O pó de Inconel possui uma resistência excecional, ultrapassando muitos outros pós metálicos normalmente utilizados, como o aço inoxidável ou o alumínio. A resistência específica depende do tipo de Inconel escolhido e da técnica de processamento utilizada. |
P: O pó de Inconel é seguro de manusear? | R: O pó de Inconel, tal como a maioria dos pós metálicos, pode representar um risco de inalação se não for manuseado corretamente. É fundamental seguir as precauções de segurança recomendadas, incluindo a utilização de equipamento de proteção individual (EPI) adequado, como respiradores e luvas, ao manusear o pó. |
P: O pó de Inconel pode ser reciclado? | R: Sim, o pó de Inconel pode ser reciclado até um certo ponto. O processo de reciclagem específico depende do nível de contaminação do pó usado. Geralmente, o pó Inconel não contaminado pode ser reintroduzido no processo de fabrico, promovendo a sustentabilidade. |
P: Quais são as limitações da utilização do pó de Inconel? | R: Apesar das suas propriedades notáveis, o pó de Inconel tem algumas limitações a considerar. Como mencionado anteriormente, o custo do material e dos processos de fabrico aditivo pode ser mais elevado em comparação com as técnicas tradicionais. Além disso, o acabamento da superfície pode exigir pós-processamento para determinadas aplicações e as estruturas de suporte utilizadas durante a impressão podem deixar marcas no produto final. |
P: Onde posso encontrar mais informações sobre o pó de Inconel? | R: Vários recursos oferecem informações detalhadas sobre o pó de Inconel. Os fornecedores de pó de Inconel fornecem frequentemente fichas técnicas que detalham as propriedades e especificações dos seus produtos. Além disso, as associações industriais e as instituições de investigação publicam artigos informativos e relatórios sobre o pó de Inconel e as tecnologias de fabrico de aditivos. |
Sobre a 3DP mETAL
Categoria do produto
CONTACTE-NOS
Tem dúvidas ? Envie uma mensagem para nós agora mesmo! Após o recebimento de sua mensagem, nós processaremos sua solicitação com toda a equipe.