Deposição de metais por laser (LMD) é uma tecnologia de ponta que está a revolucionar as indústrias de fabrico e reparação. Imagine ser capaz de construir ou reparar peças metálicas com uma precisão exacta, camada a camada, utilizando um laser. Parece futurista, certo? Bem, não é apenas o futuro; está a acontecer agora mesmo. Vamos aprofundar esta tecnologia fascinante.
Visão geral da deposição de metal a laser (LMD)
A deposição de metal a laser (LMD), também conhecida como deposição direta de metal (DMD), é um processo de fabrico aditivo que utiliza um laser de alta potência para fundir pó ou fio metálico à medida que este é depositado num substrato. Esta tecnologia é fundamental na criação de geometrias complexas, na reparação de componentes de elevado valor e na adição de características a peças existentes.
Detalhes principais:
- Processo: Um feixe de laser cria uma poça de fusão no substrato onde o pó metálico ou o fio é alimentado, formando uma camada à medida que solidifica.
- APLICAÇÕES: Indústrias aeroespacial, automóvel, de implantes médicos e de ferramentas e moldes.
- Materiais: Vários metais, incluindo o titânio, o aço inoxidável, o cromo-cobalto e o Inconel.
- Vantagens: Alta precisão, desperdício mínimo e capacidade de reparar componentes dispendiosos.
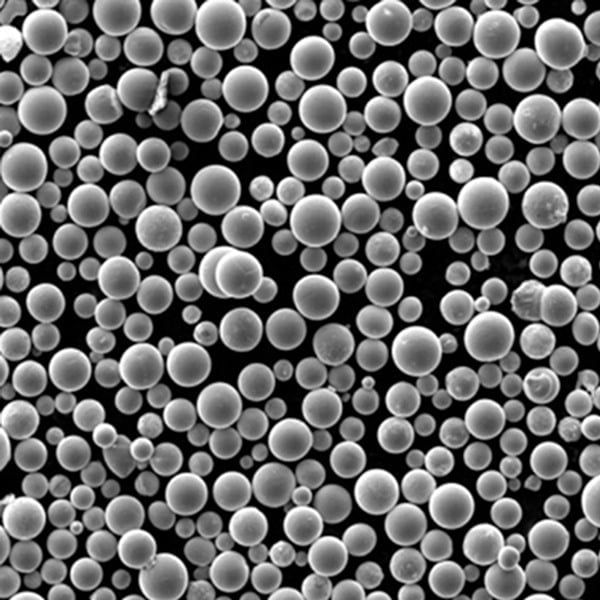
Tipos de pós metálicos para deposição de metais a laser
Pós metálicos comuns utilizados em LMD
Pó metálico | Composição | Propriedades | Características |
---|---|---|---|
Inconel 625 | Níquel-crómio | Elevada resistência, resistência à corrosão e à oxidação | Excelente soldabilidade, utilizado em ambientes agressivos |
Titânio 6Al-4V | Titânio-Alumínio-Vanádio | Elevada relação força/peso, resistência à corrosão | Leve, biocompatível, utilizado no sector aeroespacial |
Aço inoxidável 316L | Ferro-Crómio-Níquel | Elevada resistência à corrosão, boa formabilidade | Utilizado em implantes médicos, aplicações marítimas |
Cobalto-crómio | Cobalto-Crómio-Molibdénio | Elevada resistência ao desgaste e à corrosão | Utilizado em implantes dentários e ortopédicos |
Alumínio AlSi10Mg | Alumínio-Silício-Magnésio | Leve, boas propriedades térmicas | Utilizado no sector automóvel, aeroespacial |
Cobre | Cobre Puro | Excelente condutividade térmica e elétrica | Utilizado em componentes eléctricos, permutadores de calor |
Níquel 718 | Níquel-crómio-ferro | Elevada resistência, excelente resistência à fadiga e à fluência | Utilizado em turbinas de gás, no sector aeroespacial |
Aço para ferramentas H13 | Ferro-Carvão-Crómio | Elevada tenacidade, resistência ao desgaste | Utilizado no fabrico de ferramentas e moldes |
Aço Maraging | Ferro-Níquel-Cobalto-Molibdénio | Alta resistência, boa tenacidade | Utilizado no sector aeroespacial, ferramentas |
Bronze CuSn10 | Cobre-Estanho | Boa resistência ao desgaste e à corrosão | Utilizado em aplicações artísticas, rolamentos de máquinas |
Descrições pormenorizadas
- Inconel 625: Esta superliga à base de níquel-crómio é conhecida pelas suas excelentes propriedades de fadiga e de fadiga térmica, de oxidação e de resistência à corrosão. É normalmente utilizada em aplicações aeroespaciais e marítimas devido à sua robustez em ambientes extremos.
- Titânio 6Al-4V: Com uma composição de titânio, alumínio e vanádio, esta liga oferece uma relação força/peso e uma resistência à corrosão superiores, o que a torna um elemento básico na indústria aeroespacial e nos implantes médicos.
- Aço inoxidável 316L: Esta liga de ferro-crómio-níquel é favorecida pela sua resistência à corrosão e boa formabilidade, tornando-a ideal para aplicações marítimas e médicas onde a durabilidade é crucial.
- Cobalto-crómio: Conhecido pela sua elevada resistência ao desgaste e à corrosão, o cobalto-crómio é amplamente utilizado em implantes dentários e ortopédicos devido à sua biocompatibilidade e resistência.
- Alumínio AlSi10Mg: Esta liga leve oferece boas propriedades térmicas e é utilizada nos sectores automóvel e aeroespacial, onde a redução de peso sem comprometer a resistência é essencial.
- Cobre: O cobre puro é utilizado em aplicações que requerem uma excelente condutividade térmica e eléctrica, tais como componentes eléctricos e permutadores de calor.
- Níquel 718: Com a sua força excecional e a sua resistência à fadiga e à fluência, esta liga de níquel-crómio-ferro é normalmente utilizada em turbinas a gás e em aplicações aeroespaciais.
- Aço para ferramentas H13: Reconhecido pela sua elevada dureza e resistência ao desgaste, o aço para ferramentas H13 é um material de eleição para o fabrico de ferramentas e moldes.
- Aço Maraging: Esta liga de alta resistência e tenacidade é utilizada nas indústrias aeroespacial e de ferramentas. A sua composição inclui ferro, níquel, cobalto e molibdénio.
- Bronze CuSn10: Conhecida pela sua resistência ao desgaste e à corrosão, esta liga de cobre-estanho é utilizada em aplicações artísticas e em rolamentos de máquinas.
Composição de Deposição de metais por laser (LMD)
A composição dos materiais utilizados na LMD é crucial para alcançar as propriedades desejadas no produto acabado. Aqui está um olhar detalhado:
Composição de pós metálicos comuns de LMD
Pó metálico | Elementos primários | Elementos adicionais | Utilizações típicas |
---|---|---|---|
Inconel 625 | Níquel, crómio | Molibdénio, Nióbio | Aeroespacial, marítimo, processamento químico |
Titânio 6Al-4V | Titânio, alumínio | Vanádio | Aeroespacial, implantes médicos |
Aço inoxidável 316L | Ferro, crómio | Níquel, Molibdénio | Dispositivos médicos, aplicações marítimas |
Cobalto-crómio | Cobalto, Crómio | Molibdênio | Implantes dentários e ortopédicos |
Alumínio AlSi10Mg | Alumínio, Silício | Magnésio | Indústria automóvel, aeroespacial |
Cobre | Cobre | Oxigênio | Componentes eléctricos, permutadores de calor |
Níquel 718 | Níquel, crómio | Ferro, Molibdénio, Nióbio | Turbinas a gás, sector aeroespacial |
Aço para ferramentas H13 | Ferro, carbono | Crómio, Molibdénio | Ferramentaria, fabrico de moldes |
Aço Maraging | Ferro, Níquel | Cobalto, Molibdénio | Aeroespacial, ferramentas |
Bronze CuSn10 | Cobre, estanho | Zinco | Aplicações artísticas, rolamentos de máquinas |
Propriedades e características da deposição de metal por laser (LMD)
Propriedades principais
- Precisão: A LMD permite um controlo preciso do processo de deposição, o que resulta numa elevada precisão na construção ou reparação de peças.
- Eficiência dos materiais: A produção de resíduos é mínima, uma vez que o processo utiliza apenas a quantidade necessária de material.
- Versatilidade: Pode ser utilizada uma vasta gama de metais, incluindo superligas e materiais biocompatíveis.
- Resistência mecânica: Os componentes produzidos por LMD têm frequentemente propriedades mecânicas que igualam ou excedem as das peças fabricadas tradicionalmente.
Características pormenorizadas
Propriedade | Descrição |
---|---|
Precisão dimensional | Alta precisão na criação de geometrias complexas |
Acabamento da superfície | Pode variar de suave a rugoso, dependendo dos parâmetros e do pós-processamento |
Microestrutura | Tipicamente de grão fino devido à rápida solidificação |
Densidade | É possível obter uma densidade quase total com parâmetros optimizados |
Porosidade | É possível obter uma baixa porosidade, essencial para as propriedades mecânicas |
Resistência da ligação | Fortes ligações metalúrgicas entre as camadas e o substrato |
Resistência à corrosão | Depende do material; elevado para ligas como o aço inoxidável e o Inconel |
Propriedades térmicas | Boa condutividade térmica para metais como o cobre; essencial para permutadores de calor |
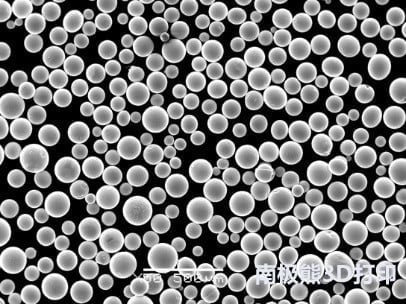
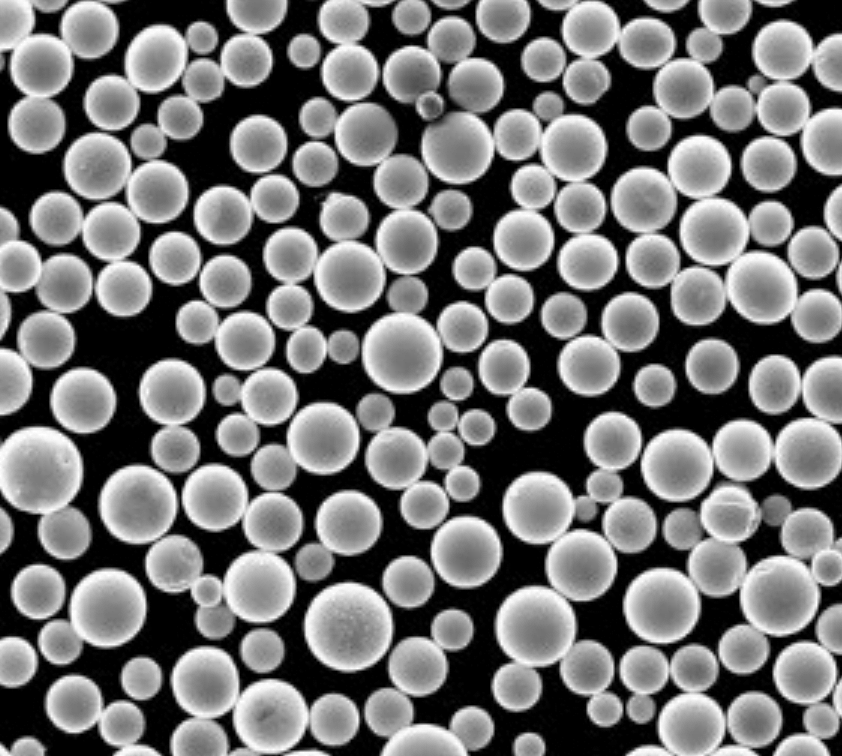
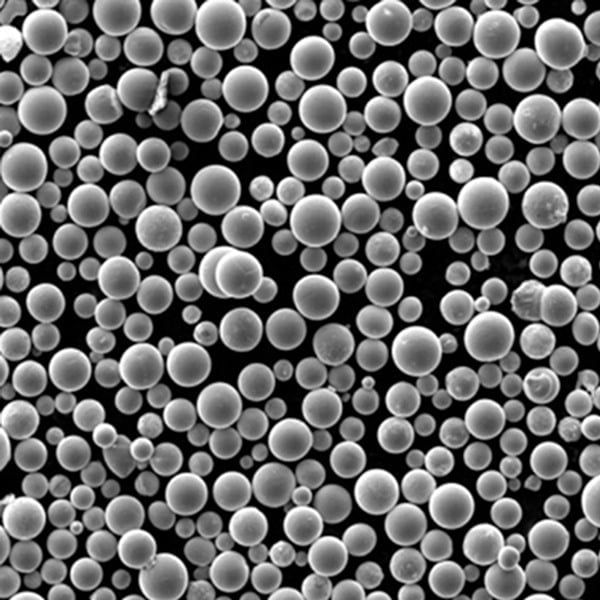
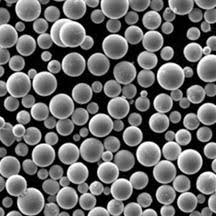
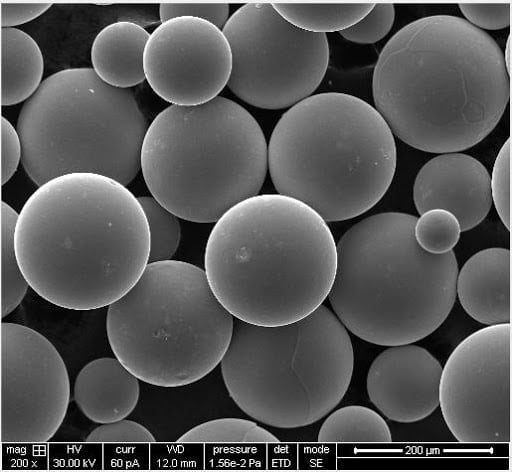
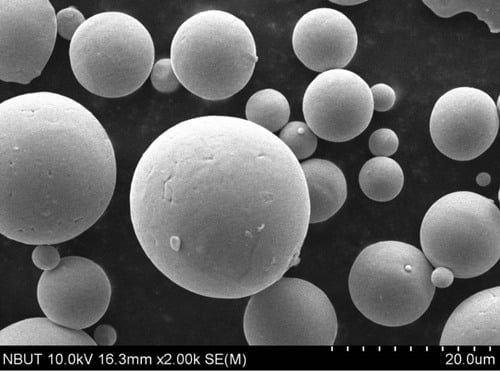
Aplicações de Deposição de metais por laser (LMD)
A tecnologia LMD é versátil e encontra aplicações em várias indústrias devido à sua capacidade de produzir peças complexas e de alta qualidade e de reparar componentes dispendiosos.
Aplicações industriais
Indústria | APLICAÇÕES |
---|---|
Aeroespacial | Componentes de motores, peças estruturais, reparação de pás de turbinas |
Automotivo | Componentes leves, protótipos, reparação de ferramentas |
Médico | Implantes personalizados, restaurações dentárias, dispositivos ortopédicos |
Ferramentas e matrizes | Reparação de moldes e matrizes, fabrico de ferramentas de corte |
Energia | Reparação de turbinas, permutadores de calor, componentes de reactores nucleares |
Defesa | Componentes de armas, reparação e manutenção de peças críticas |
Casos de utilização
- Aeroespacial: A capacidade de reparar e fabricar componentes complexos de motores torna a LMD inestimável. Por exemplo, as pás de turbina, que funcionam em condições extremas, podem ser reparadas com um tempo de paragem mínimo.
- Automotivo: A LMD é utilizada para produzir componentes leves e de alta resistência que melhoram a eficiência e o desempenho do combustível. É também excelente para a criação de protótipos e reparação de ferramentas.
- Médico: Os implantes e as restaurações dentárias personalizadas são fabricados com precisão, garantindo a biocompatibilidade e soluções específicas para cada paciente.
- Ferramentas e matrizes: A reparação de moldes e matrizes por LMD prolonga a sua vida útil e reduz os custos de fabrico. As ferramentas de corte de alta precisão também são fabricadas com esta tecnologia.
Especificações, tamanhos, graus e normas
Especificações e normas para pós metálicos de LMD
Pó metálico | Especificações | Tamanhos (µm) | Notas | Padrões |
---|---|---|---|---|
Inconel 625 | ASTM B443, AMS 5599 | 15-45, 45-106 | UNS N06625 | ASTM, AMS, ISO |
Titânio 6Al-4V | ASTM F1472, AMS 4928 | 15-45, 45-106 | 5ª Série | ASTM, AMS, ISO |
Aço inoxidável 316L | ASTM A240, AMS 5507 | 15-45, 45-106 | UNS S31603 | ASTM, AMS, ISO |
Cobalto-crómio | ASTM F75, ISO 5832-4 | 15-45, 45-106 | Liga de CoCrMo | ASTM, ISO |
Alumínio AlSi10Mg | ASTM B209 | 15-45, 45-106 | AlSi10Mg | ASTM, ISO |
Cobre | ASTM B152 | 15-45, 45-106 | C11000 | ASTM, ISO |
Níquel 718 | ASTM B637, AMS 5663 | 15-45, 45-106 | UNS N07718 | ASTM, AMS, ISO |
Aço para ferramentas H13 | ASTM A681, DIN 1.2344 | 15-45, 45-106 | H13 | ASTM, DIN |
Aço Maraging | ASTM A538 | 15-45, 45-106 | 18Ni(300) | ASTM, ISO |
Bronze CuSn10 | ASTM B505 | 15-45, 45-106 | UNS C90500 | ASTM, ISO |
Fornecedores e informações sobre preços
Fornecedor | Pós metálicos | Preço (por kg) | Local | Contacto |
---|---|---|---|---|
Höganäs | Inconel 625, Titânio 6Al-4V, Aço inoxidável 316L | $200 – $400 | Suécia | www.hoganas.com |
Tecnologia LPW | Inconel 625, Níquel 718, Aço Maraging | $250 – $450 | Reino Unido | www.lpwtechnology.com |
Tecnologia Carpinteiro | Aço para ferramentas H13, aço inoxidável 316L | $220 – $380 | EUA | www.carpentertechnology.com |
EOS GmbH | Cobalto-crómio, alumínio AlSi10Mg | $300 – $500 | Alemanha | www.eos.info |
AP&C | Titânio 6Al-4V, Inconel 625 | $270 – $460 | Canadá | www.advancedpowders.com |
Oerlikon Metco | Cobalto-crómio, Níquel 718 | $280 – $470 | Suíça | www.oerlikon.com/metco |
Sandvik | Aço inoxidável 316L, aço para ferramentas H13 | $240 – $420 | Suécia | www.materials.sandvik |
Renishaw | Aço Maraging, Alumínio AlSi10Mg | $260 – $440 | Reino Unido | www.renishaw.com |
Arcam AB | Titânio 6Al-4V, crómio-cobalto | $280 – $460 | Suécia | www.arcam.com |
GKN Hoeganaes | Inconel 625, aço inoxidável 316L | $230 – $410 | EUA | www.gknpm.com |
Comparação de vantagens e limitações
Vantagens e limitações dos pós metálicos LMD
Pó metálico | Vantagens | Limitações |
---|---|---|
Inconel 625 | Excelente resistência à corrosão e à oxidação, elevada resistência | Caro, difícil de maquinar |
Titânio 6Al-4V | Elevada relação resistência/peso, biocompatível | Custo elevado, difícil de trabalhar |
Aço inoxidável 316L | Elevada resistência à corrosão, boa formabilidade | Resistência inferior à de algumas outras ligas |
Cobalto-crómio | Elevada resistência ao desgaste e à corrosão, biocompatível | Fragilizado, caro |
Alumínio AlSi10Mg | Leve, boas propriedades térmicas | Menor resistência em comparação com as ligas de aço |
Cobre | Excelente condutividade térmica e elétrica | Custo elevado, tendência para a oxidação |
Níquel 718 | Elevada resistência, excelente resistência à fadiga e à fluência | Caro, difícil de maquinar |
Aço para ferramentas H13 | Elevada dureza e resistência ao desgaste | Requer tratamento térmico, caro |
Aço Maraging | Alta resistência, boa tenacidade | Caro, requer tratamento de envelhecimento |
Bronze CuSn10 | Boa resistência ao desgaste e à corrosão | Menor resistência em comparação com o aço, propenso à deszincificação |
Parâmetros e limiares
Parâmetros | Limiar/intervalo | Descrição |
---|---|---|
Potência do Laser | 200 - 1000 W | Determina a energia necessária para fundir o pó |
Velocidade da digitalização | 200 - 1000 mm/s | Afecta a taxa de deposição e a qualidade da camada |
Taxa de alimentação de pó | 1 - 10 g/min | Controla a quantidade de pó fornecido à poça de fusão |
Espessura da Camada | 20 - 100 µm | Afecta a resolução e o acabamento da superfície da peça |
Gás de proteção | Árgon, Nitrogénio | Protege a poça de fusão da oxidação |
Temperatura do substrato | Temperatura ambiente até 200°C | Pode influenciar a qualidade da ligação e as tensões residuais |
Espaçamento das Chocadeiras | 0,1 - 0,5 mm | Distância entre traços laser adjacentes |
Percentagem de sobreposição | 50 – 90% | Garante a cobertura completa e a ligação entre camadas |
Taxa de arrefecimento | 10^2 - 10^6 °C/s | Afecta a microestrutura e as propriedades mecânicas |
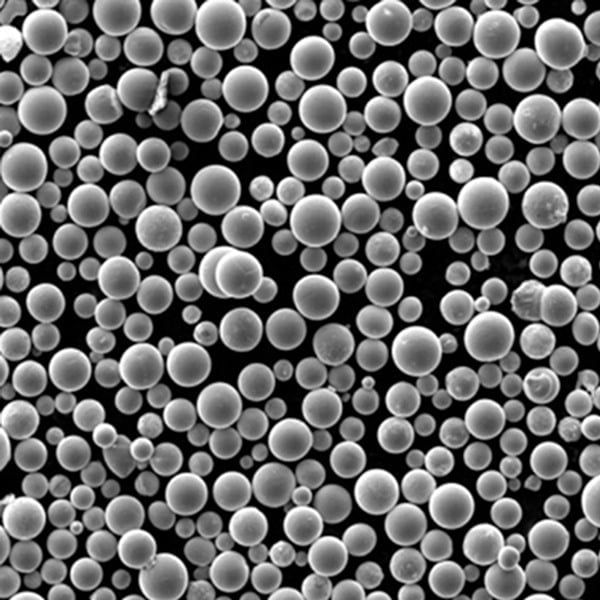
Perguntas Frequentes
Questão | Resposta |
---|---|
O que é a deposição de metal a laser (LMD)? | A LMD é um processo de fabrico aditivo que utiliza um laser para fundir pó ou fio metálico à medida que este é depositado num substrato. |
Que materiais podem ser utilizados em LMD? | Vários metais, incluindo Inconel, ligas de titânio, aço inoxidável, cromo-cobalto, alumínio, cobre e muito mais. |
Que indústrias utilizam o LMD? | Indústrias aeroespacial, automóvel, médica, de ferramentas e moldes, energia e defesa. |
Quais são as vantagens do LMD? | Alta precisão, desperdício mínimo, capacidade de reparar componentes dispendiosos e versatilidade nos materiais. |
Como é que a LMD se compara ao fabrico tradicional? | A LMD oferece maior precisão, menos desperdício e a capacidade de criar geometrias complexas em comparação com os métodos tradicionais. |
Quais são as limitações do LMD? | Custo inicial elevado, taxas de construção mais lentas em comparação com alguns métodos tradicionais e limitadas pela dimensão da área de construção. |
Qual é a espessura típica da camada em LMD? | A espessura típica da camada varia entre 20 e 100 micrómetros. |
A LMD pode ser utilizada para a reparação de peças? | Sim, a LMD é altamente eficaz na reparação de componentes de elevado valor, prolongando a sua vida útil e reduzindo os custos. |
Quais são os parâmetros-chave no processo de LMD? | Os principais parâmetros incluem a potência do laser, a velocidade de varrimento, a velocidade de alimentação do pó, a espessura da camada e o gás de proteção. |
Como é garantida a qualidade das peças de LMD? | A qualidade é assegurada através do controlo preciso dos parâmetros do processo, da seleção adequada dos materiais e das técnicas de pós-processamento. |
Sobre a 3DP mETAL
Categoria do produto
CONTACTE-NOS
Tem dúvidas ? Envie uma mensagem para nós agora mesmo! Após o recebimento de sua mensagem, nós processaremos sua solicitação com toda a equipe.