Have you ever wondered how those intricate gears in your bike or the lightweight yet sturdy frame of your phone are made? The answer might lie in a fascinating process called atomização de pó metálico. Imagine taking molten metal, the fiery lifeblood of industry, and breaking it down into a million tiny, dust-like particles. That’s the essence of atomization, and it paves the way for some incredible technological advancements.
Visão geral de Atomização de pó metálico Tecnologia
At its core, metal powder atomization is the art of transforming molten metal into a fine powder. This seemingly simple act unlocks a treasure trove of possibilities. But how exactly does it work? There are two main methods:
- Atomização de gás: Picture a scene straight out of science fiction. Molten metal is poured into a crucible, a high-temperature pot. Then, a high-pressure stream of gas, like nitrogen or argon, blasts the molten metal, shattering it into tiny droplets. These droplets rapidly solidify as they fall through a tall chamber, forming the metal powder we seek.
- Atomização de água: Here, water takes center stage. Molten metal is forced through a nozzle at high speed. A powerful jet of water then collides with the metal stream, breaking it up into fine particles. Water atomization is a more traditional method, but it’s generally used for less reactive metals like aluminum and copper.
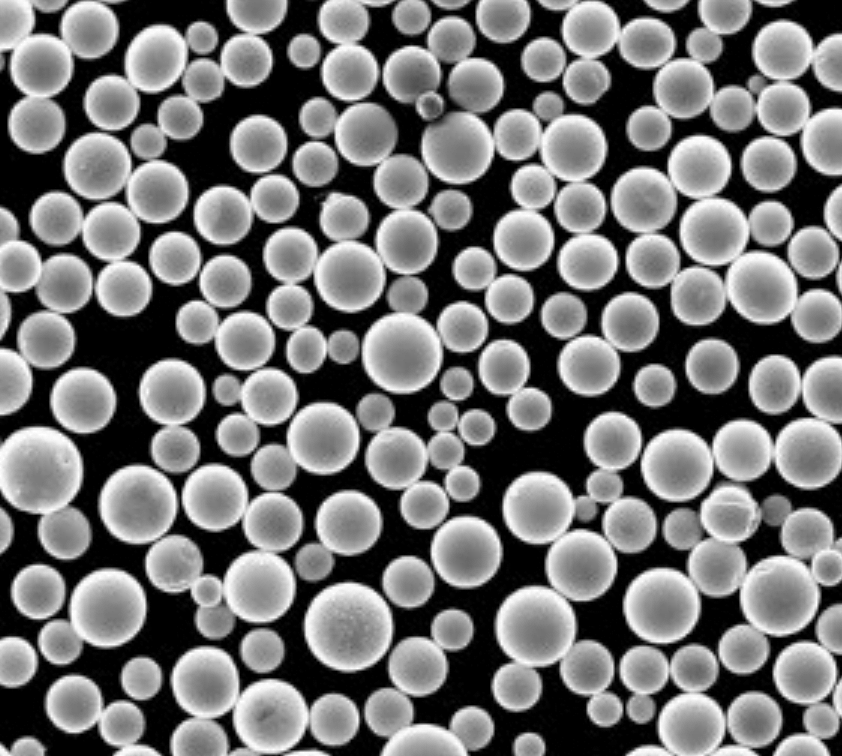
Technical Specifications for Atomização de pó metálico Tecnologia
Now, let’s delve a little deeper into the technical aspects. Both gas and water atomization involve several crucial parameters:
- Metal Properties: The type of metal being atomized plays a significant role. Highly reactive metals like titanium or tantalum might require specific gas compositions in the atomization chamber to prevent oxidation.
- Melt Temperature: Different metals have varying melting points. The atomization system needs to be able to reach and maintain the required temperature to ensure proper flow and atomization.
- Atomization Pressure: The pressure of the gas or water jet directly influences the size and distribution of the metal powder particles. Higher pressure typically results in finer powders.
- Cooling Rate: Rapid solidification is essential in atomization. The faster the droplets cool, the smaller the grain size of the resulting powder, which can impact the final properties of the material.
These factors all work together to achieve the desired powder characteristics, such as particle size, shape, and flowability – crucial for downstream applications.
Application Fields of Metal Powder Additive Manufacturing (AM)
Metal powder atomization isn’t just a party trick for scientists. It’s the foundation for a revolutionary technology: Additive Manufacturing (AM), also known as 3D printing. Here’s how it works:
Imagine a digital blueprint for a complex object. Using this blueprint, an AM machine selectively deposits layers of metal powder, building the object layer by layer until it’s complete. Metal powder atomization provides the high-quality, precisely sized powders that AM relies on.
But AM isn’t the only game in town. Metal powders find applications in various fields:
- Moldagem por injeção de metal (MIM): Here, metal powder is mixed with a binder to create a feedstock that can be molded into intricate shapes. This technique is particularly useful for mass-producing small, complex parts.
- Pulverização térmica: Metal powders are used to coat surfaces, improving wear resistance, corrosion protection, or even electrical conductivity. Imagine giving your engine components a protective metallic shield – that’s the power of thermal spraying.
- Powder Metallurgy (PM): Metal powders are pressed into desired shapes and then sintered (heated) to form a solid object. This method is often used for high-performance parts like gears and filters.
The possibilities with metal powder atomization are truly endless. From crafting lightweight components for aerospace to creating intricate medical implants, this technology is pushing the boundaries of what’s possible.
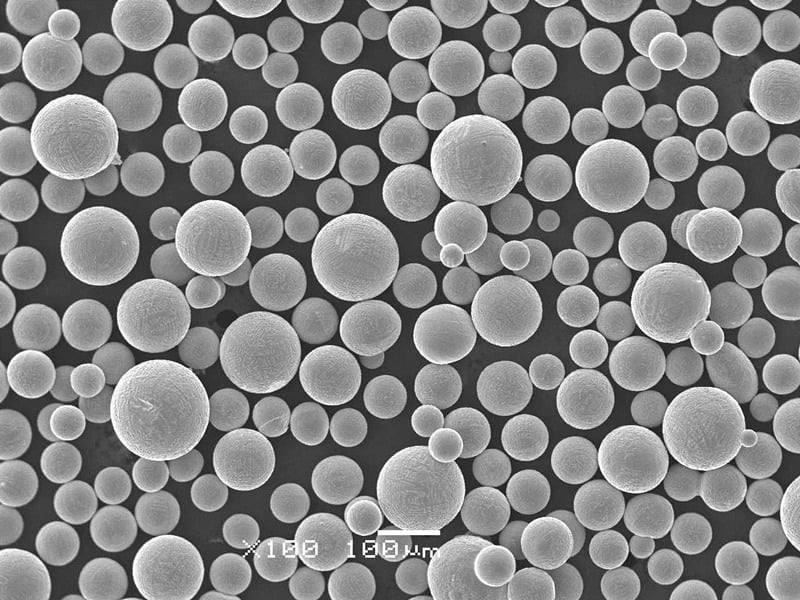
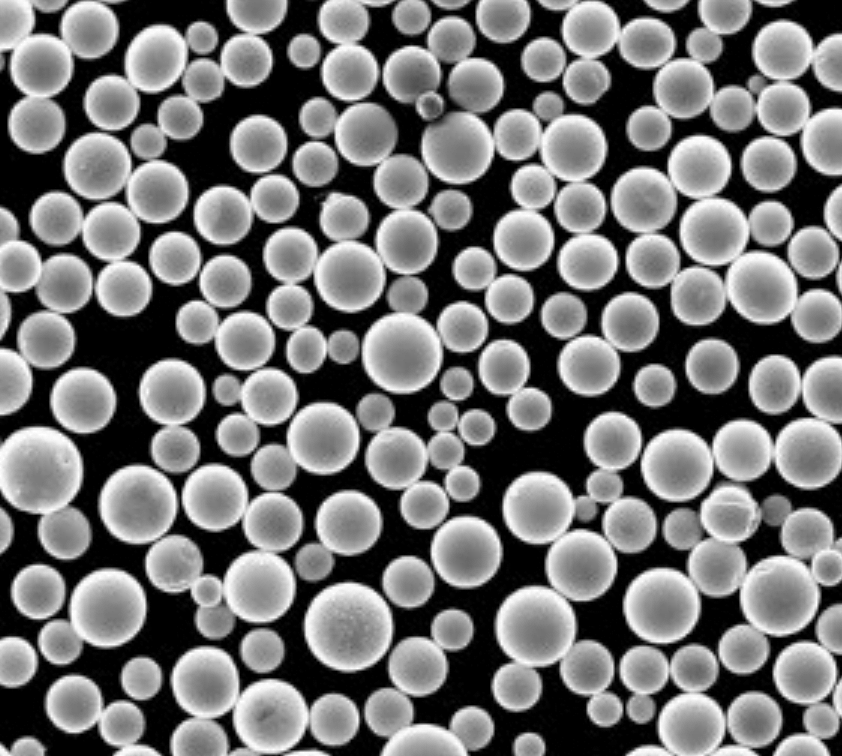
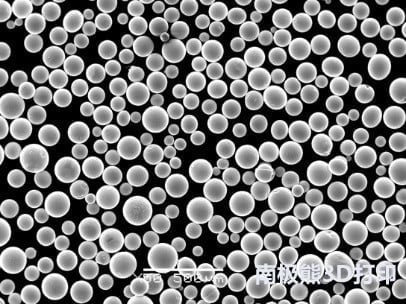
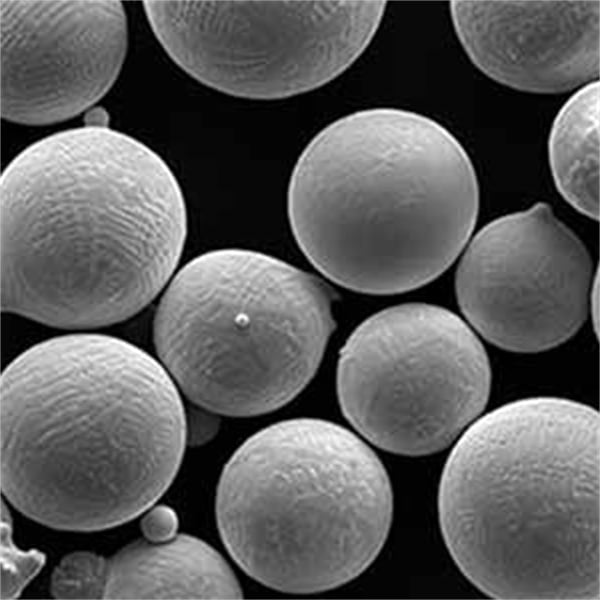
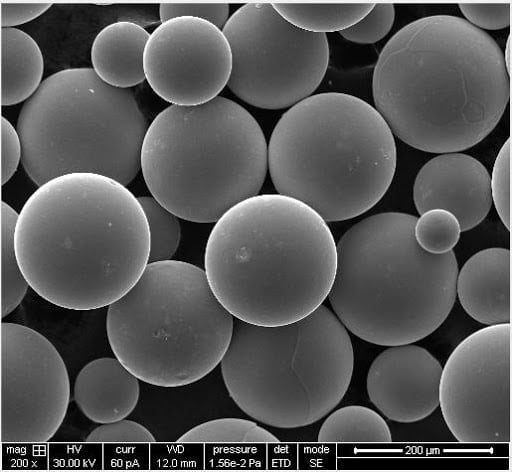
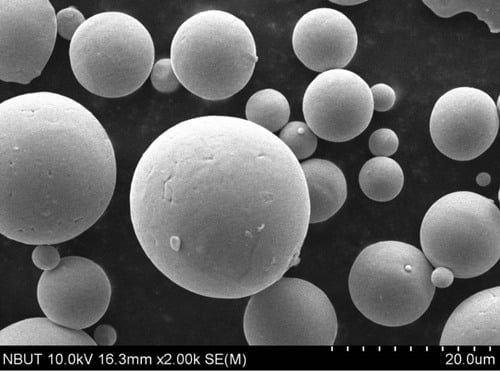
The Development Trend of Metal Powder Atomization Technology
The world of metal powder atomization is constantly evolving. Here are some exciting trends to watch:
- Multi-Material Atomization: Imagine combining different metals or even ceramics in a single powder particle. This could unlock entirely new material properties, leading to components with exceptional strength, weight, and heat resistance.
- Near-Net-Shape Atomization: This futuristic concept involves producing metal powder particles with specific near-final shapes. Think of tiny gear-shaped particles or lattice structures. This could significantly reduce the amount of post-processing needed in AM and other applications.
- Sustainable Practices: The atomization process can be energy-intensive. However, researchers are exploring ways to reduce energy consumption and minimize environmental impact. This might involve using recycled materials or developing more efficient atomization techniques.
The future of metal powder atomization is brimming with potential. As technology advances, we can expect even finer control over powder characteristics, opening doors to groundbreaking applications in various industries.
Vantagens e considerações sobre Atomização de pó metálico
While metal powder atomization offers a treasure trove of benefits, it’s essential to consider some key aspects:
Vantagens:
- Liberdade de conceção: Unlike traditional manufacturing methods, metal powder atomization allows for the creation of complex geometries. Think of intricate lattice structures or components with internal channels – these become achievable with AM, thanks to the versatility of metal powders.
- Aligeiramento: Metal powders can be used to create lightweight yet strong components. This is particularly valuable in aerospace and automotive applications, where every gram saved translates to better fuel efficiency.
- Versatilidade do material: A wide range of metals and alloys can be atomized, allowing engineers to choose the perfect material for the job. Need a component that can withstand extreme temperatures? High-temperature alloys are readily available in powder form.
- Redução de resíduos: Compared to traditional subtractive manufacturing (think machining), AM with metal powders generates significantly less waste. This translates to a more environmentally friendly production process.
Considerações:
- Custo: Metal powder atomization and AM can be expensive compared to traditional methods. The cost of the powder itself, coupled with the specialized equipment required, can be a barrier for some applications.
- Qualidade do pó: The quality of the final product heavily relies on the quality of the metal powder. Consistent particle size, shape, and flowability are crucial for successful AM and other processes.
- Controlo de processos: Metal powder atomization and AM involve a complex interplay of parameters. Fine-tuning these parameters requires expertise and experience to achieve the desired results.
Despite these considerations, the advantages of atomização de pó metálico are undeniable. As technology matures and costs come down, we can expect this technology to become even more widespread across various industries.
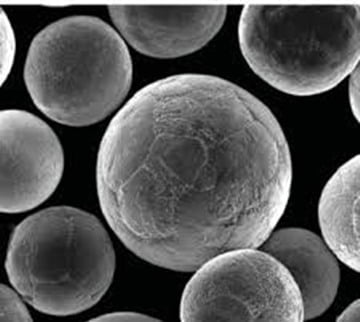
Perguntas Frequentes
Here are some frequently asked questions about metal powder atomization:
Questão | Resposta |
---|---|
What are the different types of metal powder atomization? | There are two main methods: gas atomization and water atomization. Gas atomization is generally used for reactive metals and finer powders, while water atomization is suitable for less reactive metals and larger particles. |
What are the advantages of metal powder atomization? | Metal powder atomization offers design freedom, lightweighting capabilities, material versatility, and reduced waste compared to traditional manufacturing methods. |
What are the limitations of metal powder atomization? | The cost of the process and the powder itself can be high. Consistent powder quality and process control require expertise. |
What are some applications of metal powder atomization? | Metal powders are used in Additive Manufacturing (3D printing), Metal Injection Molding (MIM), Thermal Spraying, and Powder Metallurgy (PM). |
What is the future of metal powder atomization? | The future holds promise for multi-material atomization, near-net-shape atomization, and sustainable practices in the atomization process. |
Metal powder atomization is a transformative technology that is revolutionizing the way we manufacture complex and high-performance components. As research and development continue, we can expect even more exciting advancements in this field, shaping the future of metal manufacturing.
Sobre a 3DP mETAL
Categoria do produto
CONTACTE-NOS
Tem dúvidas ? Envie uma mensagem para nós agora mesmo! Após o recebimento de sua mensagem, nós processaremos sua solicitação com toda a equipe.