Have you ever stopped to appreciate the intricate details of a jet engine turbine blade, the lightweight strength of a 3D-printed prosthetic limb, or the shimmering brilliance of metallic automotive paint? These marvels of modern engineering all share a common thread: they likely began their life as tiny metallic particles produced through a fascinating process called powder atomization.
In essence, powder atomization equipment takes molten metal and breaks it down into a fine mist of microscopic droplets that solidify into a free-flowing powder. Imagine a high-pressure garden hose turned up to eleven, blasting molten metal apart to create a metallic rain shower that cools and solidifies into individual particles. That’s the basic idea behind powder atomization.
The Two Main Types of Powder Atomization Equipment
There are two main types of powder atomization equipment, each with its own advantages and applications:
- Atomização de gás: This workhorse method utilizes a high-velocity gas stream, typically inert gases like nitrogen or argon, to shatter the molten metal stream into tiny droplets. Imagine a skilled sculptor using a high-powered chisel to break down a large block of metal into smaller fragments. Gas atomization offers high production rates, good powder shape control, and is suitable for a wide range of metals and alloys.
- Atomização de água: This technique employs a high-pressure water jet to fragment the molten metal. It’s like using a powerful water cannon to break apart a molten metal stream. Water atomization is particularly well-suited for reactive metals like titanium and tantalum that can react with nitrogen or argon in a gas atomization process. However, water atomization can introduce oxygen contamination and may result in slightly less spherical powder shapes compared to gas atomization.
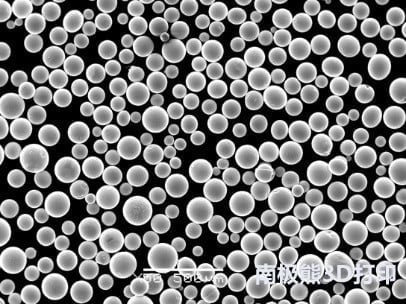
Equipamento de atomização de pó for Various Applications
The applications for powder atomization are as diverse as the materials themselves. Here are just a few examples:
- Fabrico de aditivos (impressão 3D): Metal powders are a vital ingredient in 3D printing processes, allowing for the creation of complex, near-net-shape components for aerospace, automotive, and medical applications.
- Pulverização térmica: This technique uses a high-temperature flame or plasma arc to melt and propel powder particles onto a substrate, creating wear-resistant coatings, corrosion protection, or even building up worn-out surfaces. Think of it like painting with metal instead of paint, using powder instead of a liquid.
- Moldagem por injeção de metal (MIM): Powders are mixed with a binder to create a feedstock that can be injection molded into complex shapes. After debinding and sintering, the final metal parts emerge. Imagine using a specialized mold to press metallic Play-Doh into intricate shapes, then removing the binder and heat-treating the remaining metal for a finished product.
- Production of High-Performance Alloys: Powder atomization allows for the creation of unique and high-performance alloys with improved properties like strength, weight reduction, and high-temperature resistance. It’s like having a special recipe for a metallic cake, and powder atomization is the tool that helps you create the perfect ingredients.
Key Components of Powder Atomization Equipment
A typical powder atomization system comprises several key components:
- Melting Unit: This is the heart of the system, where the metal feedstock is melted using various techniques like induction furnaces, plasma torches, or electron beam melting. Imagine a high-powered forge that heats the metal to a molten state.
- Atomization Chamber: Here, the molten metal is forced through a nozzle and broken up into droplets by the high-velocity gas or water stream. This is the chamber where the metallic rain shower is created.
- Quenching System: The atomized droplets rapidly cool and solidify in a quenching tower or chamber. This rapid solidification helps to control the final microstructure and properties of the powder particles. Think of it as a giant metal rain collector that cools down the metallic droplets before they clump together.
- Powder Collection System: The cooled powder is separated from the gas or water stream using cyclones and filters. This is like having a special net to catch all the metallic rain.
- Powder Handling System: The collected powder is carefully handled, packaged, and stored to maintain its quality and prevent contamination.
Transforming Molten Metal into Microscopic Marvels
Have you ever stopped to appreciate the intricate details of a jet engine turbine blade, the lightweight strength of a 3D-printed prosthetic limb, or the shimmering brilliance of metallic automotive paint? These marvels of modern engineering all share a common thread: they likely began their life as tiny metallic particles produced through a fascinating process called powder atomization.
In essence, powder atomization equipment takes molten metal and breaks it down into a fine mist of microscopic droplets that solidify into a free-flowing powder. Imagine a high-pressure garden hose turned up to eleven, blasting molten metal apart to create a metallic rain shower that cools and solidifies into individual particles. That’s the basic idea behind powder atomization.
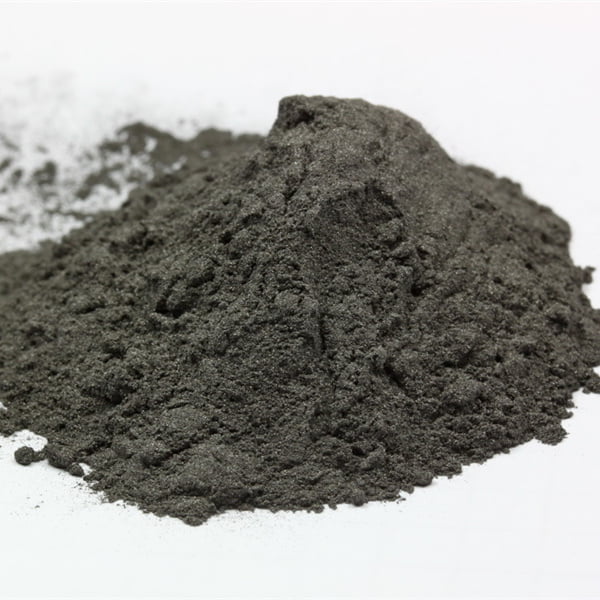
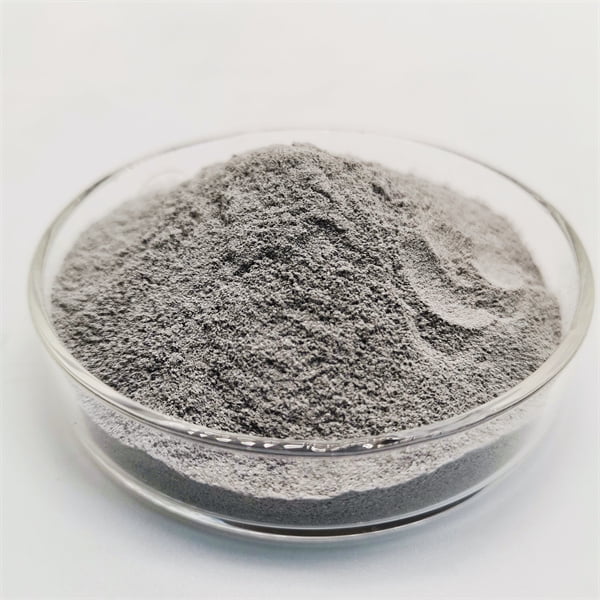
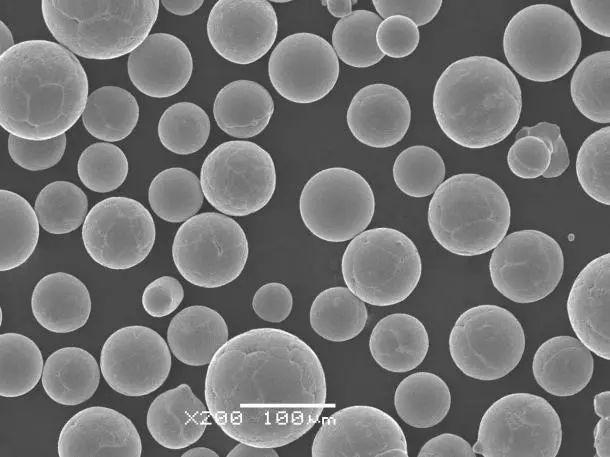
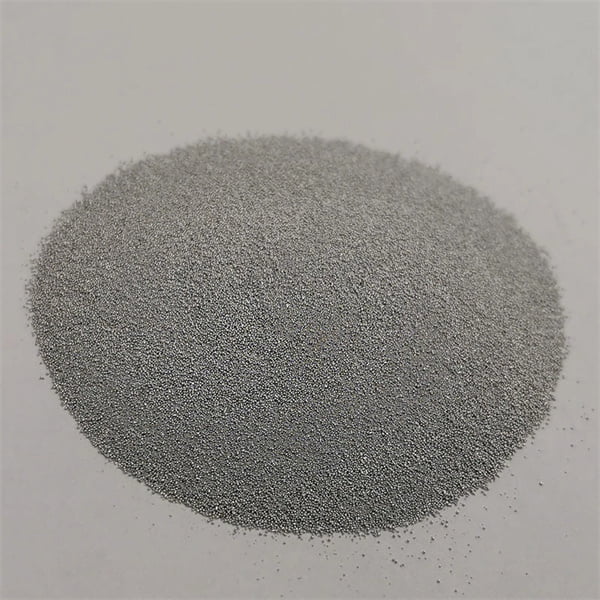
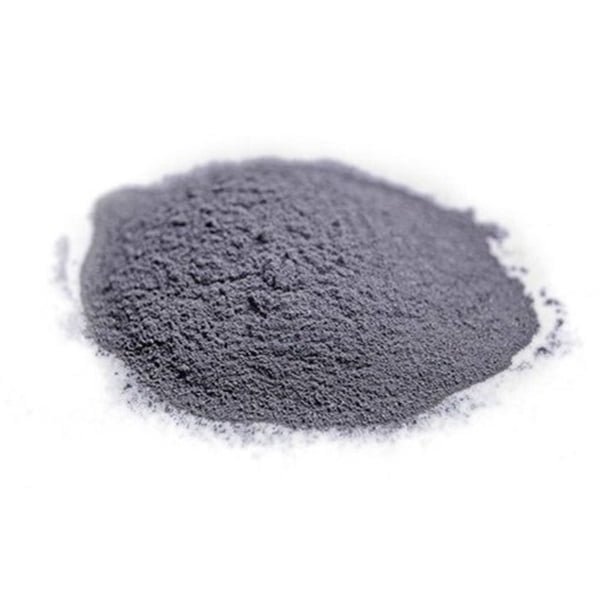
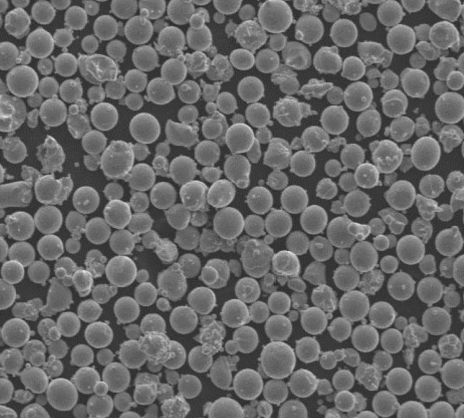
The Two Main Types of Equipamento de atomização de pó
There are two main types of powder atomization equipment, each with its own advantages and applications:
- Atomização de gás: This workhorse method utilizes a high-velocity gas stream, typically inert gases like nitrogen or argon, to shatter the molten metal stream into tiny droplets. Imagine a skilled sculptor using a high-powered chisel to break down a large block of metal into smaller fragments. Gas atomization offers high production rates, good powder shape control, and is suitable for a wide range of metals and alloys.
- Atomização de água: This technique employs a high-pressure water jet to fragment the molten metal. It’s like using a powerful water cannon to break apart a molten metal stream. Water atomization is particularly well-suited for reactive metals like titanium and tantalum that can react with nitrogen or argon in a gas atomization process. However, water atomization can introduce oxygen contamination and may result in slightly less spherical powder shapes compared to gas atomization.
Powder Atomization Equipment for Various Applications
The applications for powder atomization are as diverse as the materials themselves. Here are just a few examples:
- Fabrico de aditivos (impressão 3D): Metal powders are a vital ingredient in 3D printing processes, allowing for the creation of complex, near-net-shape components for aerospace, automotive, and medical applications.
- Pulverização térmica: This technique uses a high-temperature flame or plasma arc to melt and propel powder particles onto a substrate, creating wear-resistant coatings, corrosion protection, or even building up worn-out surfaces. Think of it like painting with metal instead of paint, using powder instead of a liquid.
- Moldagem por injeção de metal (MIM): Powders are mixed with a binder to create a feedstock that can be injection molded into complex shapes. After debinding and sintering, the final metal parts emerge. Imagine using a specialized mold to press metallic Play-Doh into intricate shapes, then removing the binder and heat-treating the remaining metal for a finished product.
- Production of High-Performance Alloys: Powder atomization allows for the creation of unique and high-performance alloys with improved properties like strength, weight reduction, and high-temperature resistance. It’s like having a special recipe for a metallic cake, and powder atomization is the tool that helps you create the perfect ingredients.
Key Components of Equipamento de atomização de pó
A typical powder atomization system comprises several key components:
- Melting Unit: This is the heart of the system, where the metal feedstock is melted using various techniques like induction furnaces, plasma torches, or electron beam melting. Imagine a high-powered forge that heats the metal to a molten state.
- Atomization Chamber: Here, the molten metal is forced through a nozzle and broken up into droplets by the high-velocity gas or water stream. This is the chamber where the metallic rain shower is created.
- Quenching System: The atomized droplets rapidly cool and solidify in a quenching tower or chamber. This rapid solidification helps to control the final microstructure and properties of the powder particles. Think of it as a giant metal rain collector that cools down the metallic droplets before they clump together.
- Powder Collection System: The cooled powder is separated from the gas or water stream using cyclones and filters. This is like having a special net to catch all the metallic rain.
- Powder Handling System: The collected powder is carefully handled, packaged, and stored to maintain its quality and prevent contamination.
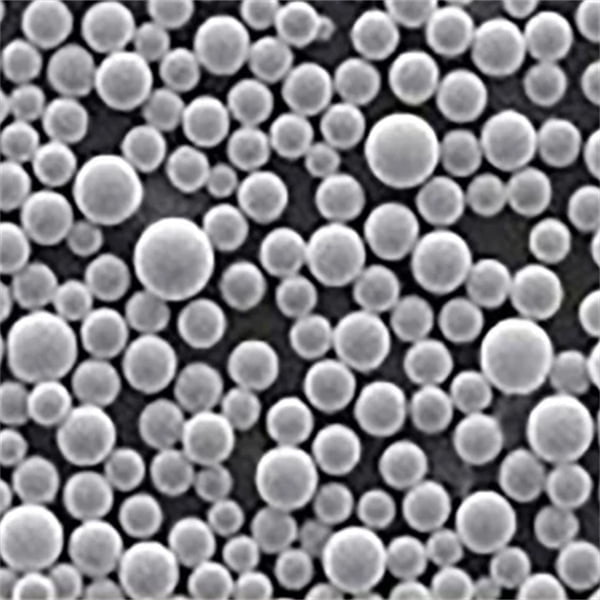
FAQs
Here are some frequently asked questions (FAQs) about powder atomization equipment:
Questão | Resposta |
---|---|
What are the typical production rates for powder atomization? | Production rates can vary significantly depending on the equipment size, material being atomized, and desired powder characteristics. Gas atomization systems typically achieve higher production rates (hundreds of kilograms per hour) compared to water atomization (tens of kilograms per hour). |
Can powder atomization be used for any type of metal? | While a wide range of metals and alloys can be atomized, some limitations exist. Highly reactive metals like lithium or sodium might require specialized techniques due to their extreme reactivity. |
What safety precautions are necessary for powder atomization equipment? | Safety is paramount. Strict protocols are required to manage the hazards associated with molten metal, high-pressure gases or water, and potential dust explosions. Proper training for operators on safe handling procedures and personal protective equipment (PPE) usage is essential. |
How is the quality of the atomized powder controlled? | A comprehensive quality control program is crucial. Powder samples are analyzed for particle size distribution, shape, chemical composition, flowability, and other critical properties. In-process monitoring and adjustments to the atomization parameters help ensure consistent powder quality. |
What are the environmental considerations for powder atomization? | Environmental regulations regarding emissions and wastewater treatment need to be followed. Gas atomization systems might require capturing and recycling inert gases. Water atomization wastewater might need treatment to remove contaminants before disposal. |
Conclusão
Powder atomization equipment stands as a remarkable testament to human ingenuity. It transforms molten metal into a microscopic marvel, unlocking a world of possibilities in various industries. As technology continues to evolve, powder atomization equipment will undoubtedly play a pivotal role in shaping the future of advanced materials and manufacturing processes. Imagine a world where complex components are built layer-by-layer using customized metal powders, or worn-out surfaces are revitalized with a metallic spray paint. The possibilities are truly endless.
Sobre a 3DP mETAL
Categoria do produto
CONTACTE-NOS
Tem dúvidas ? Envie uma mensagem para nós agora mesmo! Após o recebimento de sua mensagem, nós processaremos sua solicitação com toda a equipe.